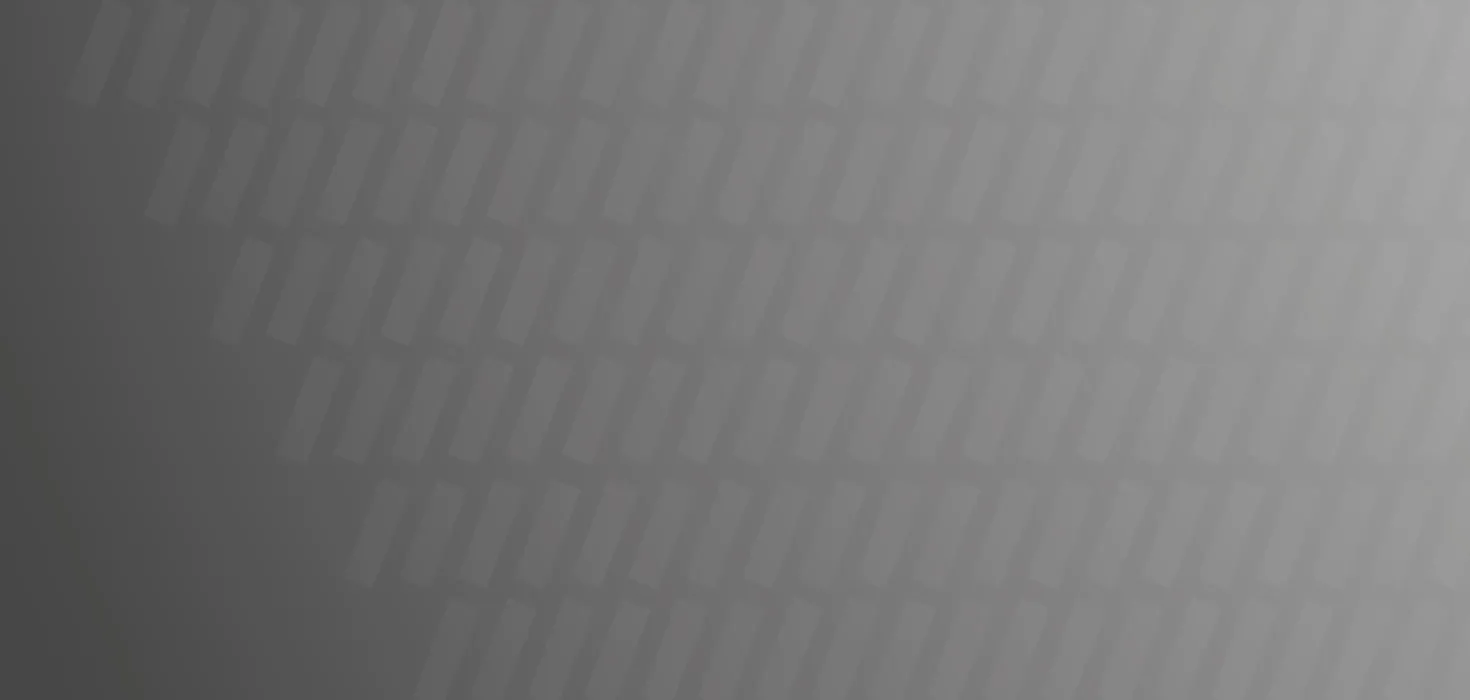
Ein effizienterer, umwelt- und mitarbeiterfreundlicherer Fertigungsprozess
Ganzheitliche Optimierung eines Prozessschritts
Energieeinsparung
Ersatz von Alkohol-Ethylsilikat durch Wasser
tsf ist ein Verfahrensspezialist im Stahlfeinguss und stellt Präzisionsbauteile für unterschiedliche Anwendungen her. Das Unternehmen hat den Prozessschritt Tauchraum bei der Produktion optimiert. Dazu wurde der Prozessschritt automatisiert, die Art des eingesetzten Schlickers wurde geändert und die Temperatur und Luftfeuchtigkeit werden nun durch Sensoren überprüft und gesteuert.
Die tsf Tübinger Stahlfeinguss Franz Stadtler GmbH & Co. KG ist ein führender Verfahrensspezialist im Stahlfeingussverfahren und stellt Präzisionsbauteile für die Medizintechnik, die Automobilindustrie, die Lebensmitteltechnik und den Maschinenbau her. Das Ziel von tsf ist es, die Anforderungen seiner Kunden zu erfüllen, um die Basis für ein wettbewerbsfähiges Kundenprodukt zu schaffen. Dazu begleitet tsf, als Partner seiner Kunden, jedes Projekt von der Entwicklung über den Prototyp bis zur Umsetzung in der Serienfertigung. tsf hinterfragt jeden Prozess und arbeitet kontinuierlich an effizienten Prozessen, um wettbewerbsfähige Lösungen anbieten zu können. Insbesondere bei energie- und rohstoffintensiven Prozessen steht die Steigerung der Energie-und Rohstoffeffizienz im Fokus.
Der Feingussprozess besteht bei tsf aus mindestens elf verknüpften Prozessen. Im ersten Prozessschritt wird das Wachsmodell hergestellt und an einen Wachsstamm zu einem Wachsbaum montiert. Der Wachsbaum wird anschließend mit einer Keramikschicht aus Alkohol-Schlicker, Ammoniak und Sand im Tauchraum beschichtet. Es folgt das Ausschmelzen des Wachses und das Brennen der Keramikform bevor die Stahllegierung in die heiße Keramikform gegossen werden kann. Danach wird die Keramik abgerüttelt und die Stahlteile werden vom Stamm getrennt. Anschließend erfolgen Angussschleifen, Sandstrahlen, Wärmebehandlung, Qualitätskontrolle und Versand. Je nach Anwendungsgebiet werden die Stahlfeingussbauteile mechanisch bearbeitet oder es wird z.B. eine Oberflächenbeschichtung aufgetragen. Einer der personal- und ressourcenintensivsten Prozesse ist die Herstellung der keramischen Schale im Tauchraum.
Die Herausforderung bestand darin, die Abläufe im Prozessschritt Tauchraum effizienter zu gestalten, sodass die Kunden von tsf von einer gesteigerten Produktqualität profitieren.
Die Optimierung des Prozessschritts Tauchraum sollte im Wesentlichen aus drei Komponenten bestehen:
- Der Prozessschritt sollte vollständig automatisiert werden.
- Wechsel von einem alkoholbasierten Schlicker auf einen wasserbasierten Schlicker.
- Sensorgesteuerte Überwachung und Steuerung der Temperatur und Luftfeuchtigkeit in klimatisierten Trockenkammern.
Die weltweit leistungsstärkste Tauch- und Trocknungsanlage konnte zum Zeitpunkt der Modernisierung des Tauchraums bei tsf nur mit einem sehr hohen Energieverbrauch betrieben werden konnte. Somit bestand eine weitere Herausforderung darin, die Anlage in Zusammenarbeit mit dem Anlagenhersteller energieeffizienter zu gestalten.
Zusammen mit dem Anlagenhersteller und dem Planer der technischen Gebäudeausrüstung, dem Ingenieurbüro Isenmann aus Haslach i. K., wurden Ansätze entwickelt, wie der Energieeinsatz in der neuen Tauchanlage reduziert werden konnte. Dank innovativer Lösungen zur Wärmerückgewinnung, Wasserkühlung und Verwendung von Prozesswärme sowie dem Einsatz von effizienteren Motoren und Elektrokomponenten konnte eine hohe Einsparung gegenüber der Standardausführung erreicht werden.
Im neuen Tauchraum erfolgt die Herstellung der keramischen Schalen vollautomatisiert und mit wasserbasiertem Schlicker. Ein Roboter übernimmt das Tauchen und Besanden sowie das Handling der Wachsstämme. Die einzelnen Schichten der keramischen Schale werden durch diesen Prozessablauf gleichmäßig und prozesssicher aufgebracht. Durch die gesteigerte Prozesssicherheit kann die interne Fehlerquote erheblich minimiert werden. Die Trocknung der Gussformen erfolgt in sensorgesteuerten, vollklimatisierten Trockenkammern, welche im Umluftbetrieb arbeiten. Die Umluft wird mittels Silicagel chemisch entfeuchtet. Die Regeneration des Silicagelrades erfolgt über die Abwärme der Kältemaschine, welche zur Kühlung der Ventilatorenabwärme notwendig ist. Dieses Verfahren gewährleistet eine sehr hohe Entfeuchtung, so dass die trockene Luft mit der feuchteren wieder vermischt werden kann. Dadurch wird ein großer Teil der Kühlleistung eingespart, die notwendig ist, um die Luft von ca. 22 °C mit einer relativen Feuchte von 50 % auf den Taupunkt abzukühlen. Weiterhin hat dieses Verfahren den großen Vorteil, dass die keramischen Feingussformen gleichmäßig austrocknen. Der Energieaufwand bei einer chemischen Entfeuchtung (Silicagelrad) ist um ein vielfaches geringer als bei der herkömmlichen mechanischen Entfeuchtung.
Durch die von tsf angeregten Änderungen an der Trocknungsanlage konnten an mehreren Punkten Einsparungen realisiert werden. So wurde eine Kühlanlage mit Propangas installiert. Diese hat gegenüber der Standardausführung geringere Klimawirkungen. Zudem werden Energieeinsparungen über einen effizienteren Motor der Kältemaschine erreicht. Die Motoren der Kältemaschine sind frequenzgeregelt und erreichen damit mindestens die Wirkungsgradklasse IE2 für Elektromotoren. Somit werden voraussichtlich 13.000 kWh pro Jahr eingespart.
Die Wärmerückgewinnung in der Kühlanlage ermöglicht die Nutzung der Prozesswärme in den Trocknungsschränken. Dadurch können pro Jahr weitere 70.000 bis 80.000 kWh eingespart werden. Die Ultraschallbefeuchtung ermöglicht gegenüber der herkömmlichen elektrischen Befeuchtung voraussichtlich eine zusätzliche jährliche Einsparung von 30.000 bis 40.000 kWh. Darüber hinaus wurde durch effizientere Motoren innerhalb der Anlage die Wirkungsgradklasse von IE2 auf IE3 gesteigert. Somit können nach konservativer Schätzung pro Jahr mindestens weitere 3.000 bis 4.000 kWh an elektrischer Energie eingespart werden.
Weitere Einsparungen in Höhe von jährlich 132.000 kWh thermischer Energie, ergeben sich beim Heizen der Betriebsgebäude aus der Beschaffung von effizienteren Kompressoren inklusive Wärmerückgewinnung. Darüber hinaus können durch die Vermeidung von Leerlaufphasen in der produktionsfreien Zeit weitere Einsparungen von jährlich 10.000 kWh realisiert werden. Das Paket aller Einzelmaßnahmen zur Steigerung der Energieeffizienz ermöglicht gegenüber der Standardausführung Einsparungen von knapp 400.000 kWh pro Jahr.
Die Änderungen im Prozessschritt Tauchraum führen allerdings nicht nur zu Energieeinsparungen, sondern auch zur Einsparung von Betriebsstoffen. So kann das im bisherigen Prozessablauf verwendete Alkohol-Ethylsilikat zu 100 % durch Wasser ersetzt werden. Auf den Einsatz von Ammoniak, zum Schutz von Umwelt und Mensch, kann völlig verzichtet werden.
Mit der vollständigen Automatisierung verdoppelt sich die Produktionskapazität im Tauchraum. Darüber hinaus wird die physische Belastung im Tauchraum auf ein Minimum reduziert und die Produktivität der Mitarbeiter um 200 % gesteigert. Im alten Prozessablauf wurden ca. 50 % der Ausschussteile durch Tauchfehler verursacht. Mit dem neuen Prozessablauf im Tauchraum wird die Ausschussquote deutlich minimiert und eine Einsparung der internen Qualitätskosten im sechsstelligen Eurobereich realisierbar.
Die frühzeitige Einbindung von Energieberatern ist für den Erfolg eines solchen Projektes unabdingbar. Um hohe Einsparungen zu erreichen, bedarf es der zielorientierten Zusammenarbeit von Anlagenhersteller, Energieberater und Fachhandwerkern. Die vielen Schnittstellen und mögliche Sprachbarrieren verlangen ein konsequentes Projektmanagement. Den Ansatz, möglichst früh die betreffenden Experten mit dem Anlagenhersteller an einen Tisch zu bringen und mögliche Einsparungspotenziale zu identifizieren, wird tsf auch in Zukunft praktizieren. Dieses Projekt hat gezeigt, dass für Kunden, Mitarbeiter und für die Umwelt eine Win-Win-Situation geschaffen werden kann.

Tübinger Stahlfeinguss (tsf) fertigt mit 60 Mitarbeitern Feingussteile mit Stückgewichten von 10 g bis über 35 kg. Dabei können Bauteillängen bis ca. 500 mm realisiert werden. Dank einer breiten Palette an Werkstoffen und Legierungen geht tsf gezielt auf die spezifischen Anforderungen seiner Kunden ein. Derzeit fertigt tsf Einsatz-, Vergütungs- und Werkstähle. Darüber hinaus vergießt tsf hitze- und zunderbeständige Stähle sowie rost- und säurebeständige Stähle. Als Spezialist für Präzisionsgussteile hat tsf für seine Kunden weit über 3.000 Serien- und Prototypenprojekte realisiert. Das Fundament dafür bildet ein über Jahrzehnte gewachsenes feingussspezifisches Know-how in Verbindung mit modernsten Technologien. Dank eines eingespielten Netzwerks an Lieferanten und Produktionspartnern werden den Kunden einbaufertige, hochwertige Bauteile aus einer Hand geboten. Transparente und verlässliche Produktionsprozesse sowie ein engagierter Kundenservice stellen die Produktqualität sicher. Dafür steht das inhabergeführte Familienunternehmen mit seinem Namen.
- Einzelteilherstellung ,
- Kleinserienfertigung
- Produktionsplanung / -steuerung ,
- Verarbeitungsprozess
- Prozessinnovation
- Energie ,
- Material ,
- Chemieprodukte ,
- Abgas
- strategisch (größer 5 Jahre)