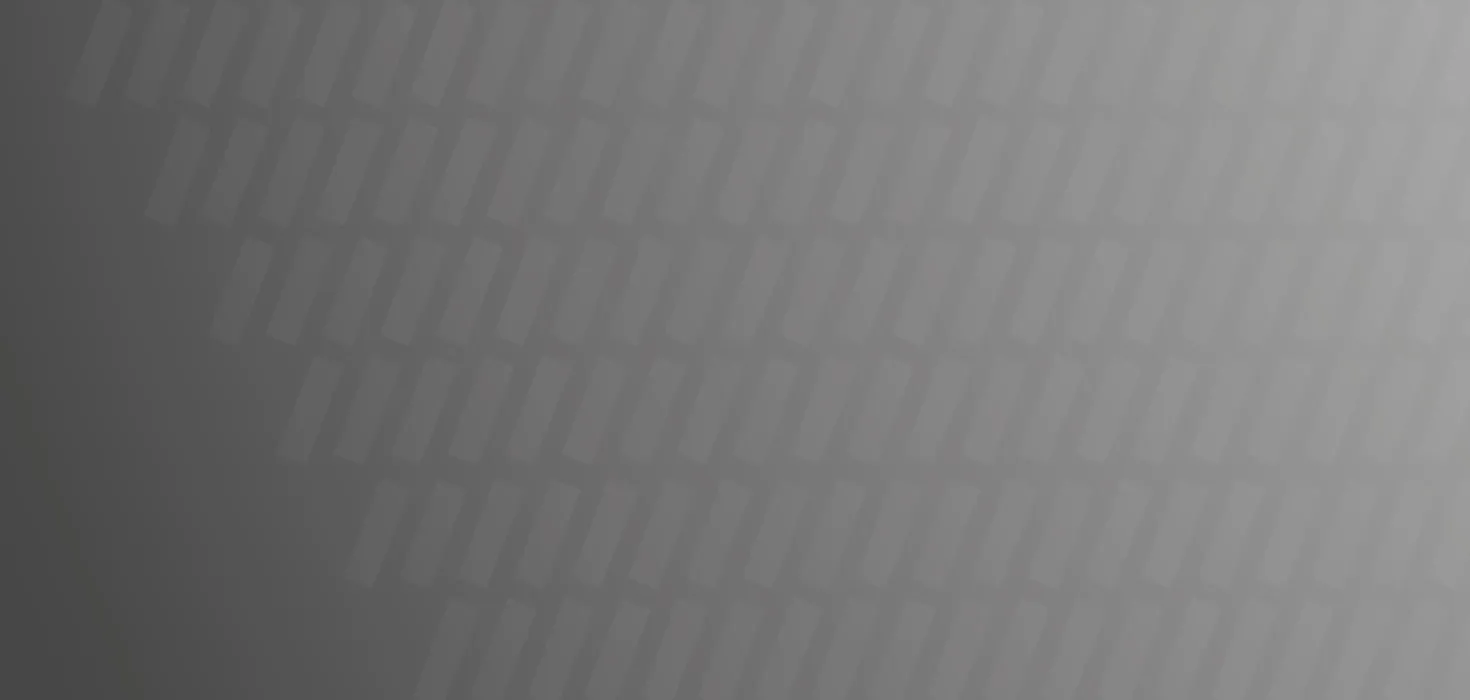
Die perfekte Welle – Flachsfasern und Unternehmensprozesse in Form gebracht
Substitution von Rohmaterialien, Einführung innovativer Produktionsprozesse, Energieeinsparung und Organisationsumbau
Gewichtseinsparung
Vollholz- und Verbundmaterialeinsparung
Abfalleinsparung
Energieeinsparung
Die GETA mbH stellt Innenausbauelemente für Schienenfahrzeuge, Flugzeuge, Busse und Schiffe her. Durch die Substitution von Rohmaterialien, die Einführung innovativer Produktionsprozesse, die Reorganisation einzelner Bereiche und die Energieeinsparung in der Produktion konnte das Unternehmen seine Ressourceneffizienz erhöhen. Es konnte einiges an Energie, Kosten und Abfällen eingespart werden.
Kostenvorteile
- 0,4Mio Materialkosten durch Materialsubstitution
- 1,5 Mio. Euro für den Lagerbestand zuzüglich der entsprechenden Lagerzinsen
Das Unternehmen GETA Interieur mbH stellt Innenausbauelemente für Schienenfahrzeuge, Flugzeuge, Busse und Schiffe her. Am Unternehmenssitz in Wangen werden ca. 800 verschiedene Tischmodelle für ICEs sowie unterschiedliche Decken- und Fußbodenverkleidungen entwickelt und produziert. Dabei geht GETA auf komplexe und umfangreiche Kundenanforderungen ein.
Derzeit kommen Vollholz, Sperrhölzer, Verbundmaterialien und Schaumkunststoffe in der Fertigung zum Einsatz. Gerade im Schienenfahrzeugbereich ist es von entscheidender Bedeutung, das Gewicht einzelner Elemente zu reduzieren. Damit trägt GETA zur Effizienzsteigerung der Fahrzeuge bei. Diese schlägt sich etwa in Treibstoffverbrauchssenkungen oder Nutzlastgewinnen nieder. Neben der Effizienzsteigerung für den Kunden, ist es jedoch ebenso wichtig, Ressourceneffizienzmaßnahmen im Herstellungsunternehmen zu initiieren.
Daher wurden zur Aufdeckung von Einsparpotenzialen die Möglichkeiten der Produkt- und Prozessgestaltung detailliert untersucht und bewertet. Das Ziel war es, den Material- und Energieeinsatz effizienter zu gestalten und zugleich marktfähige Produkte zu entwickeln. Die einzelnen Prozesse wurden über den gesamten Produktlebensweg hinweg betrachtet, um zu vermeiden, dass die Effizienzsteigerung im Unternehmen an anderer Stelle zu Mehrverbrauch führt.
Basierend auf den Ergebnissen hat GETA einige Maßnahmen und Projekte zur Erhöhung der Ressourceneffizienz geplant und umgesetzt. Davon soll beispielhaft eine kleine Auswahl vorgestellt werden. Diese reicht von der Rohmaterialsubstitution, über die Einführung innovativer Produktionsprozesse und der Energieeinsparung in der Produktion bis hin zur Reorganisation einzelner Bereiche.
Der Erfolg dieser verschiedenen Maßnahmen zeigt sich sowohl direkt als auch indirekt. So ergeben sich neben der Erhöhung der Ressourceneffizienz weitere Markt- und Wettbewerbsvorteile, wie etwa die Verringerung der Herstellungskosten, eine verminderte Abhängigkeit vom Rohstoffmarkt, eine Steigerung des Gewinnes und eine verbesserte Außenwirkung des Unternehmens.
In den langen Phasen der Entwicklungstätigkeit wurde bereits festgestellt, dass die bisher verwendeten Materialien durch Flachsfasern ersetzt werden konnten. In einem neuen Formlegeprozess sollte das Flachsgelege durch Verformung in einer Sperrholzschablone in eine wellenartige Form gebracht werden. Die Schablone wird in der Regel durch vertikalen Verbund von Sperrholzplatten und anschließender CNC-Wellenfräsung realisiert. Durch eine wellpappenähnliche Struktur sollte die für den vorgesehenen Anwendungsbereich notwendige Stabilität erreicht werden.
Im Herstellungsprozess Plattenzuschnitt sind bisher große Mengen an verfahrensbedingtem Abfall durch manuell ermittelten Verschnitt entstanden. Diese Materialverluste sollten durch eine effektive und effiziente Gestaltung der Prozesskettenabfolge programmtechnisch optimiert und damit reduziert werden. Hierfür wurde auf eine chaotische Zuschnittoptimierung, die Einführung eines Nestingverfahrens, eine intelligente Produktionsvernetzung und die Einführung eines ERP-Systems zurückgegriffen.
Zudem sollte die Auftragsbearbeitung über das neu eingeführte ERP-System erfolgen. Dieses ermöglicht die durchgängige Verfolgung des Auftrags und liefert gleichzeitig die benötigten Daten an die weiteren Unternehmensbereiche. Der technische Einkauf hatte das Ziel, seine Aktivitäten auf wenige Zulieferer mit idealen Losgrößen auszurichten und im Projektverfahren zu agieren.
Die Organisationseinheiten sollten ebenso neu definiert und jeder Stelle sollte eine genaue Aufgabenbeschreibung zugeordnet werden. Dadurch konnten Mehrfachbestellungen für einen Kunden ausgeschlossen werden. Insbesondere wurde darauf geachtet, Prozesse zu erzeugen, die eine Vereinheitlichung von Bauteilen zum Ziel haben. Durch diese Maßnahme sollte die Vielfalt der Bauteile reduziert werden. Ein wesentlicher Bestandteil der Strategie bestand darin, das Management der Materialkosten zu verbessern.
Dem Unternehmen und seinen Mitarbeitern ist es gelungen, alle Projekte erfolgreich umzusetzen. Dazu wurden einerseits eigene Forschungs- und Entwicklungsleistungen erbracht. So wurde das Flachsgelege entwickelt und innovative Technologien, wie das Nestingverfahren, wurden aus anderen Anwendungsbereichen auf die Holz- und Kunststofffertigung übertragen. Andererseits wurden Anbieter innovativer Lösungen eingebunden.
Darüber hinaus wurden die Materialien im Lager nach der ABC-Methode klassifiziert und beschriftet. Das Lager wurde weiterhin nach der 5S-Methode aufgeräumt und übersichtlich gestaltet. Außerdem erfolgt nun die Erfassung und Überprüfung der Ist-Daten durch vierteljährliche Inventur und Fortschreibung im ERP-System. Durch die Integration aller Projekte übertrifft die Fertigung den Stand der Technik jetzt deutlich.
Zudem sind nun alle Bereiche des Unternehmens auf die Fertigung und damit auf die Wertschöpfung im Unternehmen hin ausgerichtet. Für alle Maßnahmen gilt eine fortlaufende Optimierungs- und Anpassungsfähigkeit unter dem Gesichtspunkt wachsender Produktionskapazitäten und Produktportfolios.
Durch das neue nachwachsende Compositmaterial aus Flachs ist es gelungen, Gewichtseinsparungen von bis zu 50 % zu realisieren bei gleichzeitiger Erschließung neuer Anwendungsgebiete. Beispielweise kann durch Materialsubstitution von Flachs anstelle von Vollholz in einem Bahntischflügel mit 2 kg Eigengewicht und produktionstechnischer Optimierung ein Endgewicht von 1,2 kg realisiert werden. Durch die beschriebenen Maßnahmen konnten 28 % der Vollholz- und Verbundmaterialien sowie Materialkosten in Höhe von 0,4 Mio. Euro eingespart werden. Gleichzeitig konnten jährlich knapp 45 t an Abfall eingespart werden.
Mit kleineren Maßnahmen, wie dem Einsatz von LED-Beleuchtung, werden jährlich 40 % Energie eingespart. Der Lagerbestand konnte um 1,5 Mio. Euro zuzüglich der entsprechenden Lagerzinsen reduziert werden. Die Lagerumschlaghäufigkeit wurde auf bis zu fünf Mal pro Jahr erhöht und es konnten auch Lagerschwund und -schäden gesenkt werden. Die Investitionskosten für alle Maßnahmen betrugen fast 5 Mio. Euro.
Um effektive Einsparmaßnahmen zu etablieren, ist eine systematische und übergreifende Analyse der eigenen Prozesse unter Beachtung der Informationsflüsse und der Kostentreiber wichtig. Kostentreiber sind oft eine zu hohe Modell- und Materialvielfalt. Letztendlich war dadurch ein strategischer ziel- und kosteneffizienter technischer Einkauf nicht möglich. Gerade kleinere und mittlere Unternehmen erliegen oft dem Trugschluss, dass Maßnahmen zur Material- und Ressourceneffizienz nur im Einkauf liegen. Dieser ist aber nur ein Puzzleteil von vielen.
Es ist wichtig, das gesamte Unternehmen hinsichtlich der Material-, Energie- und Informationsflüsse zu betrachten, um damit einerseits eine konsequente Erfassung aller Material- und Energieströme sicherzustellen und andererseits eine effektive Produktionsgestaltung zu ermöglichen. Selbst kleine und mittlere Unternehmen können vom praktizierten Lean Management der Großen lernen und versuchen, dieses konsequent auf das eigene Unternehmen zu übertragen.
Der zweite entscheidende Faktor ist eine systematische Forschungs- und Entwicklungstätigkeit. Diese wird bislang oft nur durch Kundenwünsche initiiert. Die GETA betreibt seit ihrem Bestehen eine rege Forschungs- und Entwicklungstätigkeit, die bereits zu mehreren Patenten und zu Alleinstellungsmerkmalen in der Branche geführt hat. Neue Produkte, neue Materialien und neue Verfahren sichern die Wettbewerbsfähigkeit jedes Unternehmens und generieren Umsatzwachstum. Nur wer immer wieder das Portfolio und die Kundenwünsche hinterfragt sowie an Systemlösungen arbeitet, wird für die Zukunft gut gerüstet sein.
Die GETA mbH mit Sitz in Wangen im Allgäu fertigt die beschriebenen Innenausbauelemente mit rund 120 Mitarbeiterinnen und Mitarbeitern in drei Werken in Deutschland. Im Fokus ist dabei die Erfüllung der sehr hohen Qualitätsansprüche der weltweiten Auftraggeber. Weitere Produktionsstandorte befinden sich in China und Russland. Konstruktions- und Vertriebsleistungen werden über Tochtergesellschaften in Thüringen, Schweiz, Italien und China abgewickelt. Weltweite Entwicklungs- und Produktionspartnerschaften runden das Unternehmensportfolio ab.

- Kleinserienfertigung
- Einkauf ,
- Produktionsplanung / -steuerung ,
- Produktionslogistik ,
- Verarbeitungsprozess
- Energiekonzept ,
- Prozessinnovation ,
- Green Supply Chain Management ,
- Lean Management ,
- Industrie 4.0 / Digitalisierung
- Energie ,
- Material ,
- Kunststoffe ,
- Holz, Karton und Papier ,
- Abfälle ,
- Abgas
- taktisch (1 bis 5 Jahre)