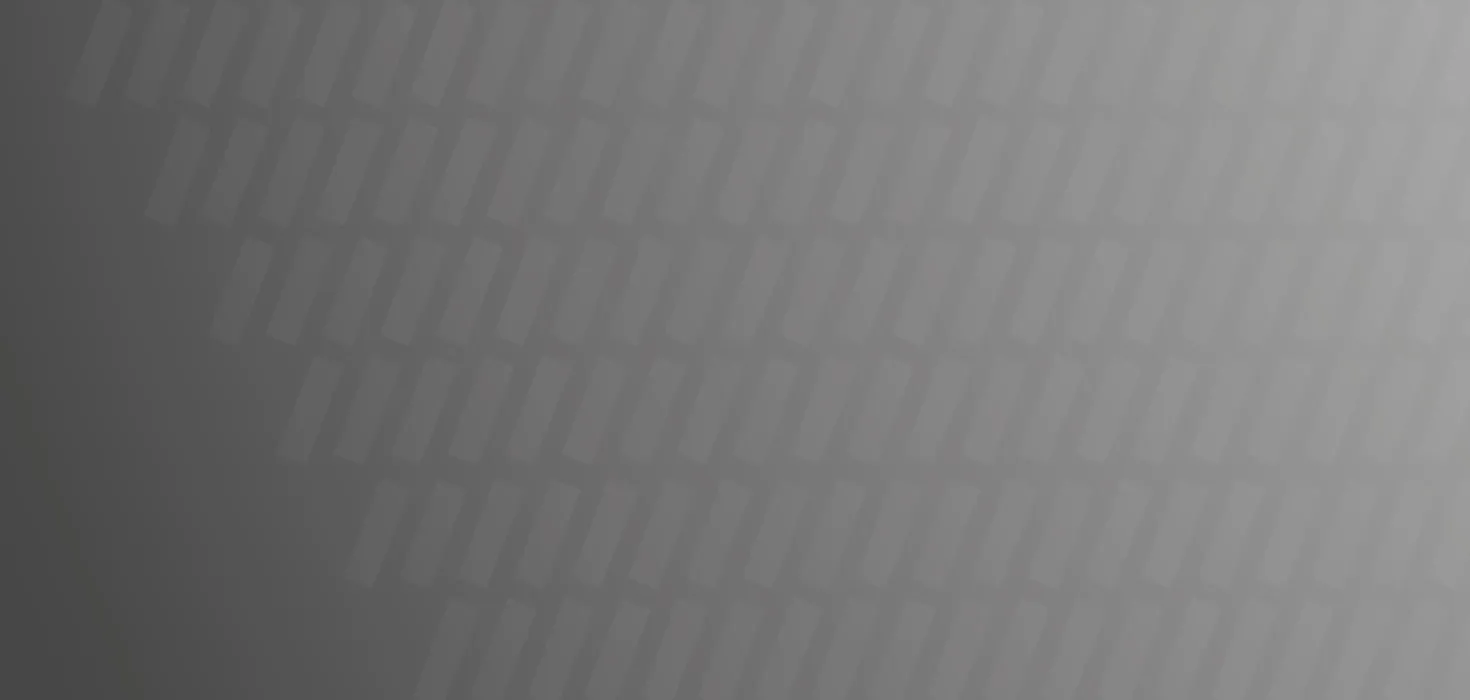
Ganzheitliche Produktionssteuerung zur Material- und Energieeinsparung
Optimierte Prozesssteuerung, Zuschnittoptimierung, Ausschussvermeidung
Materialeinsparungspotential
Verschnittverringerung
Edelstahleinsparung
Stromeinsparung
Erdgaseinsparung
Die Rieber GmbH & Co. KG gehört zu den führenden Anbietern von Küchentechnik für die professionelle Gastronomie und den privaten Haushalt. Während die Materialkosten ein wesentlicher Kostentreiber des Unternehmens sind, fällt trotzdem ein Drittel des eingesetzten Edelstahls als Schrott an. Das Ziel des Unternehmens war es daher, den Materialeinsatz zu reduzieren und damit Kosten zu sparen.
Kostenvorteile
- 400.000 Euro durch Edelstahleinsparungen
- davon 85.000 Euro/Jahr durch Verschnittverringerung
Die Firma Rieber fertigt Gastronorm-Behälter, Großküchenkomponenten, Speisentransport- und -verteilgeräte, Flugzeugwasser- und -abwassertanks, Kühlschränke, Spülen, etc. Die Kernkompetenzen des Unternehmens liegen beim Tiefziehen, Glühen und Schweißen von Edelstahl. Die Materialkosten bilden mit ca. 50 % einen entscheidenden Anteil an den Gesamtkosten des Unternehmens.
Gleichzeitig fallen ca. 35 % des eingesetzten Edelstahls, bedingt durch Ausschuss und Verschnitt, als Schrott an. Daraus leitet sich die Zielsetzung des hier präsentierten Projektes ab: Es wird ein systematischer Ansatz zur ganzheitlichen Reduktion des Materialeinsatzes entwickelt. Es gilt, eine Einzeloptimierung, die an anderer Stelle überkompensiert wird, zu vermeiden. Es werden bisher verborgene Potenziale im Betriebsablauf entlang der gesamten Wertschöpfungskette sichtbar gemacht, um diese anschließend systematisch heben zu können. Dazu werden drei methodische Schritte vollzogen: Visualisierung der Materialströme, Visualisierung der dazugehörigen Informationsflüsse und abschließend die Implementierung von Mess- und Steuerungsgrößen zur Quantifizierung von Potenzialen. Um diese Ziele erreichen zu können, wird in ein neues Datenerfassungstool in der Produktion investiert.
Der gesamte Material- und Energieverbrauch des Unternehmens ist bekannt. Dieser lässt sich jedoch nicht den konkreten verursachenden Produkten und Prozessen zuordnen. Zur Identifikation und Analyse der Material- und Energieeffizienzpotenziale wird das Projekt in drei Stufen unterteilt. Material- und Energieflüsse der Produktionsmengen werden zunächst in einem Materialflussmodell aufgenommen. Hierfür ist die Erfassung von belastbaren, konsistenten und kontinuierlichen Daten unerlässlich, die durch das neue automatisierte Datenerfassungssystem sichergestellt wird. Das Materialflussmodell bildet die Grundlage für die Gegenüberstellung der Planungs- und Dispositionsprozesse im Unternehmen. Jeder Produktionsprozess lässt sich als das Ergebnis von Kommunikation und Information verstehen. Unternehmen erkennen zwar oft ihre Einsparmöglichkeiten auf Materialebene, sind aber nicht in der Lage, das volle Potenzial zu heben, da gegenläufige Planungsprozesse dies verhindern und zum Anstieg von Kosten und Materialverbrauch an anderer Stelle führen können. Aus diesem Grund werden den Material- und Energieflüssen in einem zweiten Schritt die entsprechenden Informationsflüsse gegenübergestellt.
Dies ermöglicht die Nachvollziehbarkeit des Status quo und lässt Rückschlüsse auf die beteiligten Interessengruppen zu. Der große Vorteil dieser ganzheitlichen Betrachtungsweise liegt in der umfassenden Darstellung der Verschwendungsursachen und -hintergründe. So werden reale Potenziale ausgewiesen und Verschwendungen greifbar gemacht. Die Validierung, Kontrolle und Steuerung zukünftiger Effizienzprojekte wird im letzten Schritt über ein neu entwickeltes Kennzahlensystem sichergestellt. Dieses System ist in der Lage, auch komplexe Zusammenhänge zwischen den einzelnen Fertigungsbereichen abzubilden.
Das Materialflussmodell wird auf Grundlage der Produktionsdaten aus dem SAP-System von Rieber in Excel berechnet. Hierüber lassen sich dezidiert Fertigungsaufträge, Produktgruppen, Arbeitsplätze und Arbeitsschritte auswerten. Die Visualisierung der entsprechenden Materialflüsse wird in der Software e!sankey realisiert. Hiermit lassen sich alle Materialflüsse als Ströme zwischen den unterschiedlichen Produktionseinheiten dynamisch sowie aggregiert oder auftragsbezogen darstellen. Die Integration der Energieströme war im Zuge dieses Projekts nicht möglich, da die Datenbasis keine produktbezogene Zuordnung der Energieverbräuche zuließ. In Zukunft werden alle Verbräuche über die automatisierte Datenerfassung ermöglicht. Das Materialflussmodell ist in die Unternehmensstruktur fest integriert und bildet die Entscheidungsgrundlage für die Initiierung zukünftiger Projekte zur Steigerung der Materialeffizienz. Zuständigkeiten und Verantwortlichkeiten für die Datenpflege sowie das Kennzahlensystem wurden festgelegt und ermöglichen die Generierung von Anschlussprojekten.
Das ganzheitliche Produktionssteuerungsmodell ist zwar noch in der Umsetzungsphase, erste Einsparungen im Materialeinsatz konnten aber bereits in verschiedenen Projekten realisiert werden. Durch die ganzheitliche Betrachtung der Produktionsprozesse und die gezielte Verbesserung der Datenqualität lässt sich aus den Beispielmaßnahmen ein Materialeinsparpotenzial in der Produktion von mindestens 5 % ableiten. Dies entspricht einer Edelstahlmenge im Wert von ca. 400.000 Euro.
Beispielsweise konnte durch die Anpassung und Verschachtelung der Zuschnitte einer gängigen Spüle der Verschnitt um 10 % verringert werden, wodurch eine Materialeinsparung von 33 t Edelstahl, also ca. 85.000 Euro pro Jahr erzielt werden konnte. Durch diese Einsparungen ließen sich nicht nur die Kosten, sondern auch die entsprechende Umwelteinwirkung des Unternehmens senken.
Bereits heute wird die Abwärme des Glühofens zur Heizung der Waschmaschinen in der Produktion genutzt. Durch eine Investition von einmalig 20.000 Euro werden so jährlich 600 MWh elektrischer Strom und 10.000 m³ Erdgas eingespart. Durch die geplante Einführung eines MES-Systems lassen sich sämtliche Zustände und Auftragsdaten einzelner Maschinen auslesen und analysieren. Dies trägt dazu bei, weitere Potenziale der Material- und Energieverschwendung zu entdecken und gezielt zu heben.
Rieber sieht sich ebenfalls in der Verantwortung für die verschwendungsarme Nutzung seiner Produkte beim Endanwender. Der Unternehmensleitsatz „protecting resources“ richtet sich nach innen wie nach außen. So wurde bereits 1964 die Gastronorm durch die Firma etabliert. Auf diese Weise wird ein Mehrwegsystem für Lieferungsbehältnisse im Bereich der Gemeinschaftsverpflegung und Gastronomie ermöglicht. Die Umweltbelastung wurde mittels Life Cycle Assessment beispielhaft für einen GN-Behälter 1/1 bewertet. Dies ergab, dass das Mehrwegsystem gegenüber dem Einwegsystem für die Großküchenbelieferung mit Joghurt aus ökologischer Sicht deutlich vorteilhafter ist, da durch den Einsatz des GN-Behälters täglich ca. 90 Plastikbecher ersetzt werden können. Des Weiteren ermöglichen die Gastronorm-Behälter, die Verschwendung von Lebensmitteln so gering wie möglich zu halten. Zur sicheren Überwachung von Speisen und Lebensmitteln sowie um Prozesse transparent, sicher und rückverfolgbar zu machen, entwickelte Rieber das System °CHECK. Es dient dazu, jederzeit in „Echtzeit“ zu sehen, welche Speise sich wo, mit welcher Temperatur befindet. Diese HACCP-relevanten Daten können mit geringem Aufwand digital erfasst, dokumentiert, verwaltet und via Internet ortsunabhängig sowie jederzeit abgerufen werden. Weniger Lebensmittelabfälle sind die Konsequenz. Die eindeutige Zuordnung und Identifizierung des zu überwachenden/messenden Objektes erfolgt über einen QR-Code. °CHECK ermöglicht eine optimale Abstimmung und Organisation von Abläufen im Food-flow-Prozess, aber auch in anderen Arbeitsprozessen.
Mit dem System °CHECK war Rieber für den Umwelttechnikpreis Baden-Württemberg 2015 nominiert. Darüber hinaus ist Rieber Partner der ARGE Deutscher Pavillon Expo Milano 2015, um mit dem Mehrwegsystem GN 360 4.0 zum Expo-Thema „Feeding the planet, energy for life“ beizutragen.
Ein großes Problem vieler Mittelständler in Bezug auf Materialeffizienz stellt ihre starke Spezialisierung und Anpassung an Kundenwünsche dar. Dies hat ein weit gefächertes Produktportfolio zur Folge. Durch die hohe Angebotsvielfalt laufen klassische Analysemethoden der BWL (ABC-Analyse, etc.), die hauptsächlich auf Großserienproduktion ausgerichtet sind, ins Leere. In diesem Fall bedarf es einer Prozesssicht, um von der Betrachtung der Materialflüsse Standards für eine effiziente Produktion ableiten zu können. Die kombinierte Betrachtung von Material-, Energie- und Informationsflüssen ist bisher nicht verbreitet. Die strukturierte und ganzheitliche Analyse der bestehenden Prozesse kann dabei zur neuen Standardmethodik im Unternehmen werden und beispielhaft als Entscheidungsgrundlage für produzierende mittelständische Unternehmen wirken. Eine konsequente und dynamische Erfassung von Material- und Energieflüssen ist im Mittelstand bisher neu.
Die Gegenüberstellung der Informationsflüsse legt nun die Grundlage für effektive Einsparmaßnahmen, welche im zweiten Schritt über konkrete Grenzwerte abgesichert werden konnten. Auch in Kontakt mit Zulieferern und Kunden profitiert Rieber durch diesen Ansatz. Bei der Umsetzung aller Projekte zur Effizienzsteigerung sollen nun mit Hilfe aller Mitarbeiter neue Wege beschritten werden. Bei vielen Unternehmen, nicht nur bei Rieber, ist die vollständige Durchdringung der eigenen Produktionsprozesse zur Umsetzung von Einsparungen im Energie- und Materialbereich unerlässlich. Eine umfassende Produktionsdatenerfassung ist somit die Grundlage für die Verbesserung der Prozesssteuerung. Dies ist umso wichtiger vor dem Hintergrund von Zielkonflikten bei der Optimierung. Mit dem Aufbau individueller Informationsstrukturen können Einsparpotenziale offengelegt werden, die mit den bisherigen Methoden nicht identifiziert werden konnten.
Die Rieber GmbH & Co. KG mit Sitz in Reutlingen gehört zu den führenden Anbietern von Küchentechnik für die professionelle Gastronomie und den privaten Haushalt.
Rieber beschäftigt rund 600 Mitarbeiter an vier Fertigungsstandorten in Reutlingen und Trebbin. Tochtergesellschaften für den Vertrieb liegen in Österreich, der Schweiz, den Benelux-Ländern und Großbritannien. In allen europäischen Ländern und in zahlreichen weiteren Exportländern ist Rieber durch Partnerschaften vertreten.
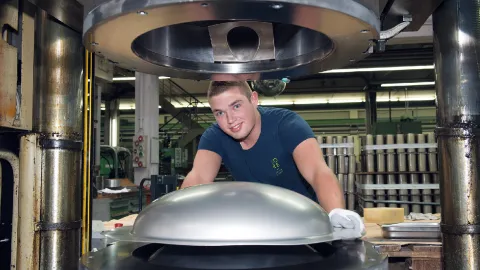
- Kleinserienfertigung ,
- Großserienfertigung
- Produktionsplanung / -steuerung ,
- Produktionslogistik ,
- Verarbeitungsprozess
- Prozessinnovation ,
- Industrie 4.0 / Digitalisierung
- Energie ,
- Material ,
- Metalle ,
- Abgas
- operativ (kleiner 1 Jahr)