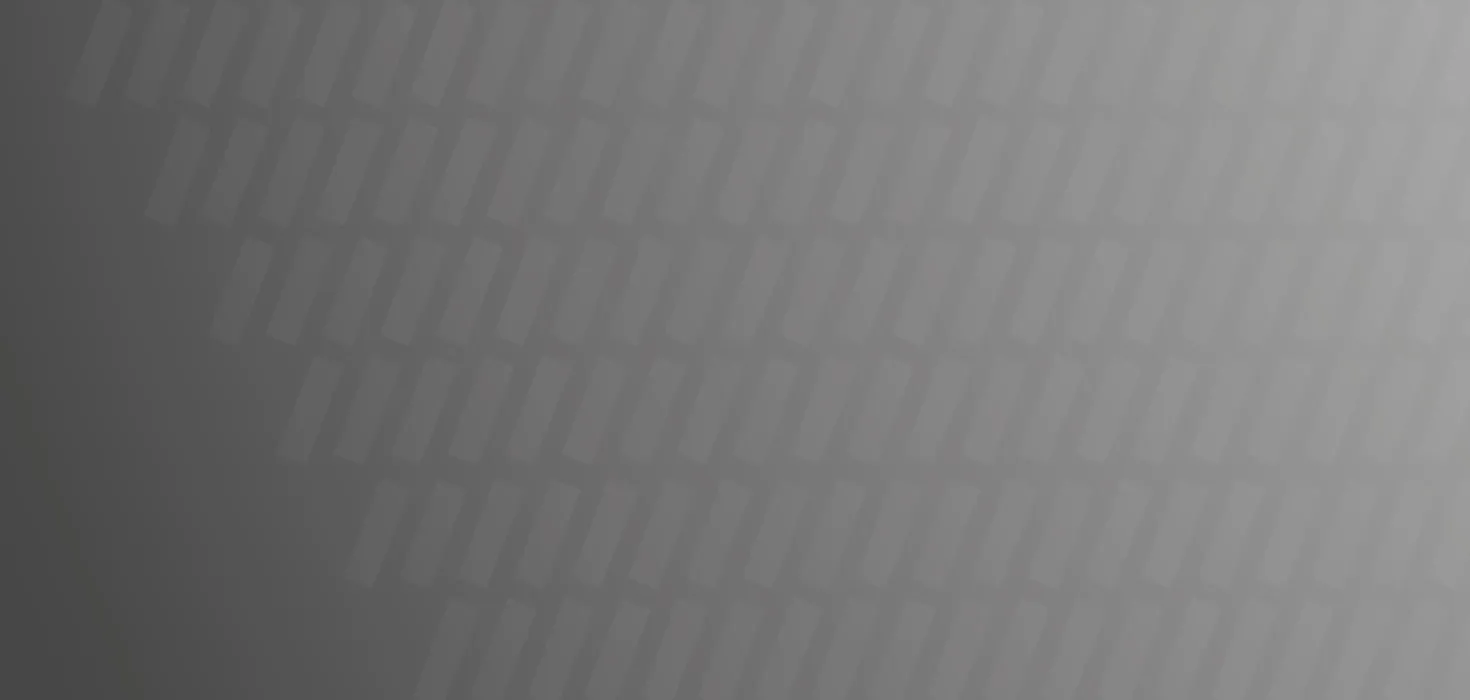
Regranulator für Kunststoffabfälle
Einsatz eines Regranulators zur Reduzierung von Kunststoffabfällen
Abfallreduktion (Kunststoff)
Die Brugger GmbH ist bekannt für die Herstellung verschiedener Magnetsysteme. Durch einen neuen Regranulator für Kunststoffabfälle konnte die Menge an Kunststoffabfall signifikant reduziert und die Menge an wiederverwendbarem Kunststoff erhöht werden. Hierbei war es wichtig, dass auch die Werte des Unternehmens „Werte schaffen Zukunft“ und nachhaltiges Wirtschaften im Fokus standen.
Die Brugger GmbH mit Firmensitz im Schwarzwald hat sich auf die Herstellung von Magnetsystemen spezialisiert. Das Produktportfolio beinhaltet Stabgreifer-, Flachgreifer-, Organisations- und Dekorationsmagnete.
Für eine ansprechende Optik und zum Schutz vor Korrosion und mechanischen Beschädigungen ist ein Großteil der Permanentmagnete mit einem passenden Kunststoffmantel aus thermoplastischen Elastomeren (TPE) umhüllt. Die Kunststoffmäntel werden in der hauseigenen Kunststoffspritzgießerei produziert. Beim Spritzgießen von Kunststoffteilen bleiben Angüsse übrig, die entsorgt werden müssen.
Während des ersten Audits zum Thema Abfallentsorgung und -recycling fiel der Geschäftsleitung die signifikante Abfallmenge an Kunststoff auf, die monatlich abgeholt und entsorgt werden musste. Dabei handelte es sich um mindestens einen Container mit einem Volumen von 5 m³. Dieser Abfall ist vermeidbar, da TPE-Kunststoffe zu 100 % recycelbar sind. Deshalb setzte sich Brugger das Ziel, die Verschwendung zu reduzieren und eine umweltgerechte und ressourcenschonende Lösung zu finden und umzusetzen.
Um die Wiederaufbereitung der Angüsse möglichst effizient, materialschonend und zeitlich autonom gestalten zu können, musste eine passende Anlage gefunden und ausgewählt werden, die diese drei Kriterien erfüllt. Hierbei stand eine adäquate und ressourcenschonende Lösung im Vordergrund, in der sich auch das Unternehmensleitbild „Werte schaffen Zukunft“ und nachhaltiges Wirtschaften widerspiegeln.
Nach Absprache und Überprüfung des Anforderungsprofils durch den Bereichsleiter der Spritzgießerei und der Anpassung der internen Abläufe durch den Fertigungsleiter, fiel die Wahl der Investition auf den Regranulator TRS 7000 der hw.tech GmbH. Die Maschine wird zunächst ca. 45 Minuten vorgeheizt, bevor sie über einen Trichter mit den zuvor gesammelten Angüssen befüllt wird. Das Material wird dann mit Hilfe von Schnecken transportiert und durch ein Heizelement zu einer homogenen Masse verschmolzen. Anschließend wird das zähflüssige Material extrudiert und über Spulen durch ein Wasserbad geleitet und abgekühlt. Im letzten Schritt wird der abgekühlte Kunststoffstrang zu kleinem, gleichförmigen Granulat zerkleinert. Das Bedienen der Maschine erfolgt hierbei parallel zu anderen Tätigkeiten, wie dem Mahlen von anderen Kunststoffen. Somit wird gewährleistet, dass der notwendige Zeitaufwand zur Bedienung der Maschine minimiert wird.
Zudem werden die Angüsse nicht unmittelbar nach ihrem Anfallen verarbeitet, sondern zunächst gelagert, bis sich eine ausreichend große Menge angesammelt hat. Diese Maßnahme dient der Optimierung des Verhältnisses von Heiz- zu Regranulierzeit. Die verbesserte Losgröße verringert Energieverluste durch einen unnötigen Heizaufwand für Mindermengen. Das Granulat wird in handliche Säcke á 13 kg verpackt und produktionsnah gelagert, um kurze Wege sicherzustellen. Das Granulat wird dann bei Bedarf beigemischt oder bei bestimmten Produkten zu 100 % wiederverwendet. Der Einsatz des recycelten Granulats erfolgt flexibel nach Bedarf und Verfügbarkeit, um die Losgrößen der zu granulierenden Angüsse nicht negativ zu beeinflussen und zu unterschreiten. Zusätzlich wurde die Maschine als Stromspitzenwertmaschine deklariert, die erst nach zwölf Uhr benutzt wird, um Stromspitzen zu mindern und das Energienetz zu entlasten.
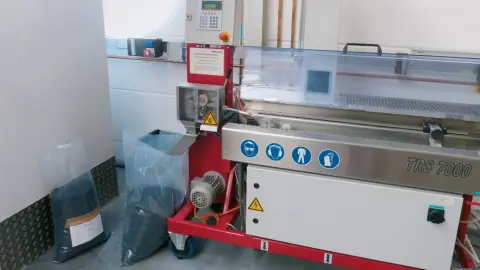
Durch die Investition und die Implementierung des Regranulators in den Produktionsablauf konnten die Kunststoffabfälle um insgesamt 7 t reduziert werden. Die entsprechende Menge konnte dementsprechend im Materialeinkauf eingespart werden. Dadurch wurde eine Nettoersparnis von ca. 6.800 Euro im Jahr 2014 und rückgerechnet bis ins Jahr 2008 eine durchschnittliche Ersparnis von ca. 4.200 Euro pro Jahr generiert, mit jährlich steigender Tendenz. Abzüglich der Anfangsinvestition von 35.000 Euro amortisiert sich die Maschine nach insgesamt acht Jahren. Bis Ende des Jahres 2017 wird eine finanzielle Einsparung von ca. 18.000 Euro erwartet. Diese wird trotz der vergleichbar geringen Menge an Kunststoff, die mit dem Regranulator wiederaufbereitet wird, erzielt.
Um Einsparungen im Produktionsprozess zu erreichen, ist es wichtig den Fokus auf die Vermeidung der Energie- und Ressourcenverbräuche zu legen. Wenn die Vermeidung aufgrund der produktionsspezifischen Gegebenheiten nicht möglich ist, dann fällt die nächste Wahl auf Verfahren der Wiederverwertung oder dem Recycling. Diese Verfahren müssen wiederum unter dem Aspekt der Vermeidung von Verschwendung, z. B. in Form von unnötigen Transportwegen, betrachtet werden. In den meisten Fällen sind Technologien zur effizienten Ressourceneinsparung bereits auf dem Markt vorhanden. Es ist jedoch die Aufgabe des Unternehmens, diese wahrzunehmen und zu nutzen. Der allgemeine betriebswirtschaftliche Konsens lautet, dass sich eine Investition nach drei, spätestens aber nach fünf Jahren amortisieren sollte, um rentabel zu sein. Das Beispiel des Regranulators mit einer Amortisationszeit von acht Jahren zeigt hingegen, dass es auf lange Sicht trotzdem von Vorteil ist eine ressourceneffiziente Investition zu tätigen, vor allem wenn man gesamtwirtschaftliche Effekte mitberücksichtigt.
Im Jahr 1963 gründete Rudolf Brugger „seine erste eigene Fabrik“ als metallverarbeitenden Betrieb. Mit den Jahren wuchs der Betrieb und erweiterte seine Produktpalette um die Herstellung von verschiedenen Magnetsystemen. Die Anwendungsbereiche der permanentmagnetischen Baugruppen erstrecken sich von der Automobilindustrie, der Licht- und Medizintechnik, dem Baugewerbe, über die Verwendung zu Dekorationszwecken, als Werbemittel bis hin zum Einsatz in Namensschildern. Am Standort in Hardt beheimatet Brugger neben der Entwicklung, Konstruktion und Herstellung eigener Werkzeuge und Produkte, die Fertigung von individuellen Kunststoffspritzgussteilen, Stanz- und Ziehteilen, sowie die Montage der Magnetsysteme. Mit einem modernen Maschinenpark, innovativen Produktkonzepten und großer Beratungskompetenz fertigt Brugger jährlich mehrere Millionen Magnetsysteme „Made in Germany“.
Die Brugger GmbH verfügt über eine Produktions- und Lagerfläche von ca. 5.400 m² und beschäftigt 96 Mitarbeiter. Heute wird das Unternehmen von den beiden Söhnen Thomas Brugger und Georg Brugger-Efinger geführt.
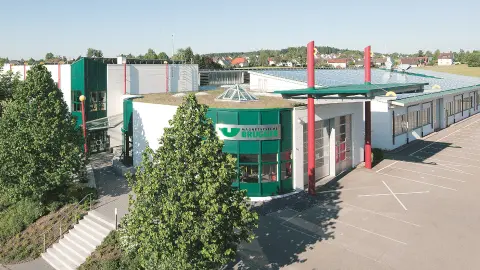
- Großserienfertigung
- Entsorgung / Recycling
- GreenTech BW ,
- Stoffkreislauf / Recycling
- Material ,
- Kunststoffe
- strategisch (größer 5 Jahre)