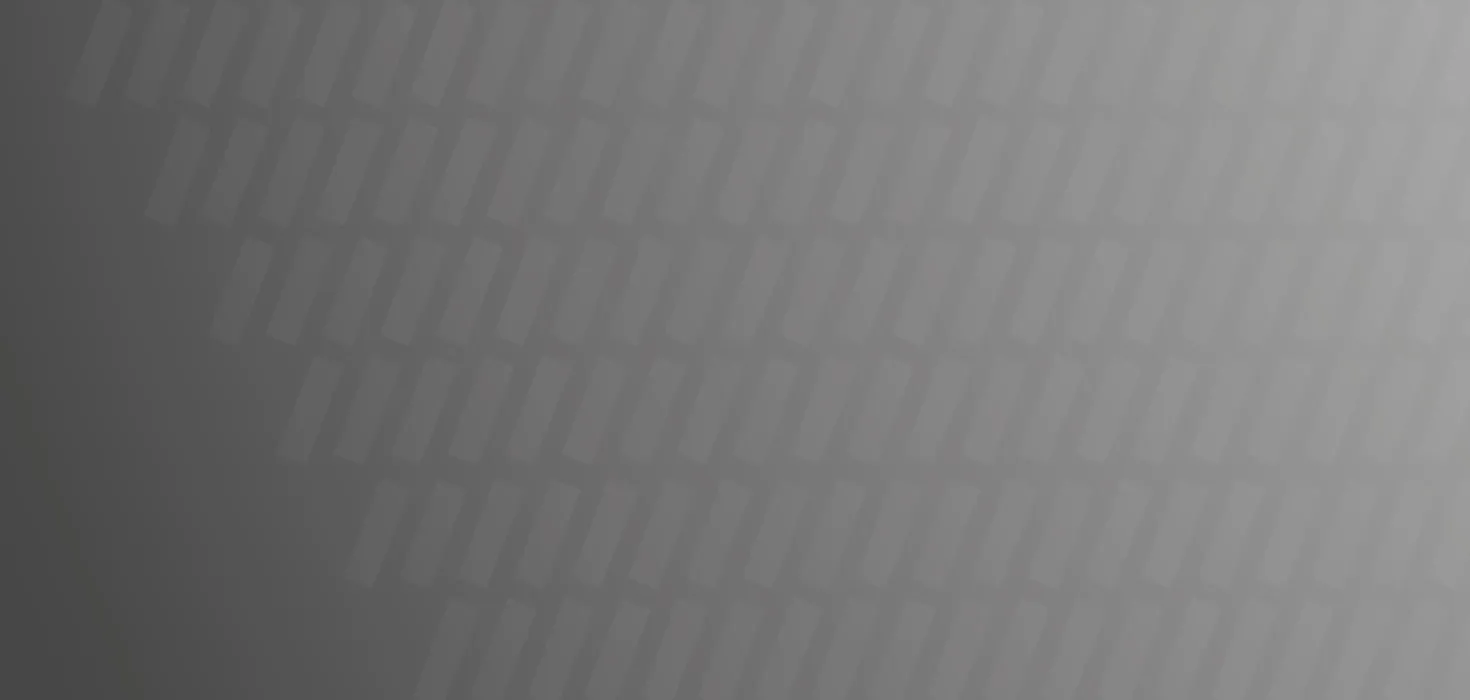
Analyse von Optimierungsmaßnahmen mittels Materialflusskostenrechnung
Reduzierung von Kreislaufmaterial und Optimierung der Prozesseffizienz
Die C. & C. Bark GmbH konzentriert sich auf die Herstellung von Magnesiumdruckgussteilen für die unterschiedlichsten Anwendungen. Das Ziel dieses Projekts war es, mithilfe der Materialflusskostenrechnung die Materialverluste und Ineffizienzen innerhalb des Produktionsprozesses zu erfassen, um anschließend Optimierungsmaßnahmen aufstellen zu können. Dabei wurde das Tool bw!MFCA genutzt.
Kostenvorteile
- 46 % weniger Produktionskosten im theoretischen Zielzustand
- 61 % weniger kreislaufbedingter Aufwand
Investition
Veränderte Arbeitsorganisation und Produktionssteuerung
Die international normierte Methode der Materialflusskostenrechnung bzw. Material Flow Cost Accounting (MFCA) kann als Analyse- und Bewertungsmethode für Ineffizienzen und zur Identifizierung von Effizienzpotenzialen im Produktionsprozess dienen. Mit Materialverlusten geht immer eine Verringerung der Wertschöpfung einher, da hierfür neben den Rohstoffen auch Energie und Personal eingesetzt wurden. Darüber hinaus kommt noch eine mögliche (Zusatz-) Beanspruchung von Produktionskapazitäten hinzu.
Der Unterschied zur konventionellen Kostenrechnung besteht in der Behandlung der Kosten der Materialverluste. Im Gegensatz zur konventionellen Kostenrechnung, in der die Kosten für Materialverluste nicht gesondert aufgeführt werden, sondern dem Produkt zugeordnet werden, lassen sich mit Hilfe der MFCA mögliche Einsparungspotenziale und Effizienzgewinne ableiten. Dies wird durch die Behandlung der Materialverluste als eigenständiger Kostenträger ermöglicht, verbunden mit allen verfahrensbedingten Kosten.
Das Ziel des Projekts war es, mit Hilfe der MFCA die Materialverluste und Ineffizienzen im Produktionsprozess zu erfassen und monetär zu bewerten. Der Aspekt der Anlagenverfügbarkeit sollte dabei ebenfalls berücksichtigt werden. Aus den Ergebnissen wurden anschließend entsprechende Einsparpotenziale und Optimierungsmaßnahmen abgeleitet und bewertet.
Der Produktionsprozess sollte mit allen Inund Outputs transparent in einem Energieund Stoffstrommodell veranschaulicht werden. Durch eine vollständige Parametrisierung der In- und Outputs innerhalb des Modells lassen sich monetäre Auswirkungen von Maßnahmen sowie Änderungen der Prozessparameter schnell auswerten und visuell darstellen. Das Modell kann demnach als Vorschau von geplanten Optimierungsmaßnahmen oder für die Nachkalkulation eingesetzt werden. Ändert sich beispielsweise das Schichtmodell, dann passen sich andere Parameter, etwa der Energieverbrauch des Schmelzofens, entsprechend an.
Für die Erstellung des Energie- und Stoffstrommodells wurde auf die Modellierungssoftware bw!MFCA zurückgegriffen, die vom Land Baden-Württemberg über die Umwelttechnik BW GmbH kostenlos bereitgestellt wird. Die automatisierte Kaltkammer-Gießzelle spielt im gesamten Produktionsprozess die wichtigste Rolle. Durch den prozessbedingten Anguss wird relativ viel Material im Kreislauf geführt. Der Schwerpunkt der Untersuchung lag deshalb auf der Optimierung von Ausschuss- und Nachbearbeitungsquoten, der Reduzierung von ungeplanten Stillständen an der Gießzelle und der Einführung eines internen Recyclings.
Werden alle ausgewählten Optimierungsmaßnahmen mit ihrer maximal möglichen Ausprägung in das Modell integriert, lässt sich ein maßnahmenübergreifender Zielzustand definieren. Dieser Zielzustand dient sozusagen als Richtwert und gibt Auskunft darüber, welche Kosten- und Materialsituation theoretisch möglich wäre. Demnach dient das Projekt in zweierlei Hinsicht als ein „Leuchtturmprojekt“.
Die Gesamtkosten im theoretischen Zielzustand lassen sich mit den gewählten Maßnahmen um 46 % reduzieren. Darüber hinaus verringert sich der kreislaufbedingte Aufwand um 61 % gegenüber der aktuellen Situation.
Zu den monetären Einsparungen, die auf die gesteigerte Prozessstabilität zurückzuführen sind, kommen vor allem durch das interne Recycling ökologische Einsparungen hinzu. Dadurch, dass weniger Material die energieintensive Aufbereitung durchläuft, leistet das interne Recycling einen wichtigen Beitrag zur Reduzierung der CO2-Emissionen.
Die Materialflusskostenrechnung ist der Start für eine Abbildung der gesamten Wertschöpfungskette der wichtigsten Produkte im Unternehmen. Dadurch lässt sich der transparente Einblick in die Produktion einer Produktlinie auf das gesamte Produktportfolio erweitern.
Das Unternehmen C. & C. Bark Metalldruckguss und Formenbau GmbH mit Sitz in Schömberg auf der Schwäbischen Alb wurde 1924 als Karl Hopt GmbH gegründet. Im Jahr 1986 erfolgte die Neugründung als C. & C. Bark Metalldruckguss und Formenbau GmbH mit der Spezialisierung auf Magnesiumdruckgussteile. Das mittelständische Unternehmen ist global aktiv und beschäftigt aktuell rund 80 Mitarbeiterinnen und Mitarbeiter. Neben der Magnesiumgießerei ist am Standort eine CNC-Fertigung eingegliedert.
Das Unternehmen ist mit der Technologie eines angussreduzierenden Verfahrens beim Warmkammerdruckguss mit einem weiteren Fallbeispiel im Projekt „100 Betriebe für Ressourceneffizienz“ vertreten. Dieses Projekt war der Ausgangspunkt verschiedener Effizienzmaßnahmen.
Der Werkstoff Magnesium mit seiner 100-prozentigen Recyclingfähigkeit und der optimalen Verwendbarkeit in allen Bereichen des Leichtbaus leistet einen deutlichen Beitrag zum Umweltschutz. Der möglichst effiziente Umgang mit diesem Werkstoff nimmt daher beim Unternehmen C. & C. Bark Metalldruckguss und Formenbau GmbH einen sehr hohen Stellenwert ein.
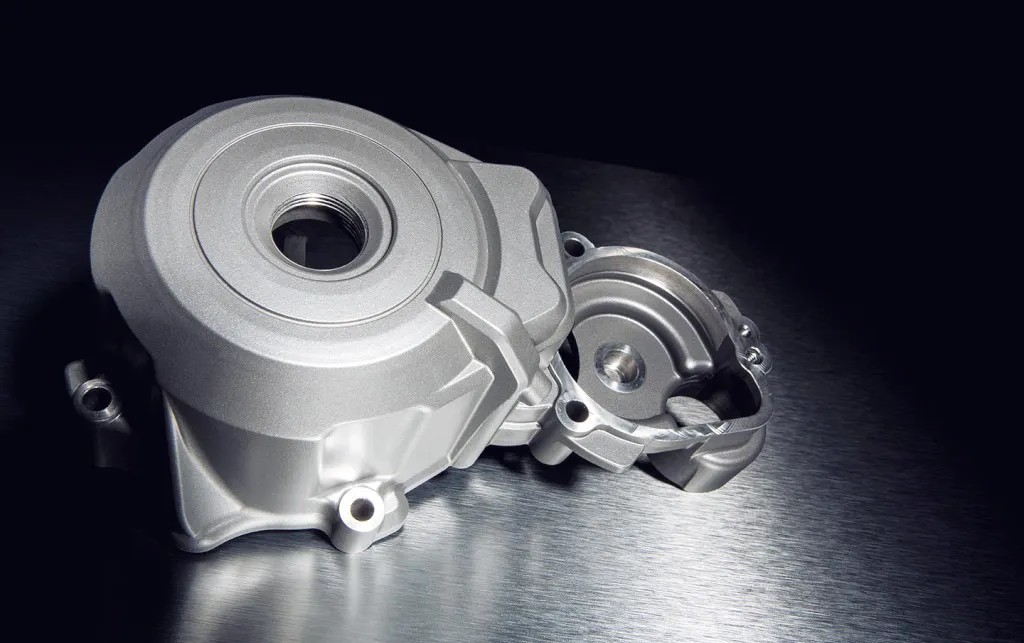
Motorradbauteil aus Magnesium – Leichtbau in Perfektion (C. & C. Bark Metalldruckguss und Formenbau GmbH)
- Kleinserienfertigung ,
- Großserienfertigung
- Produktionsplanung / -steuerung
- Prozessoptimierung ,
- Stoffkreislauf / Recycling ,
- Materialflusskostenrechnung MFCA ,
- Lean Management
- Energie ,
- Material ,
- Metalle ,
- Abgas
- operativ (kleiner 1 Jahr)