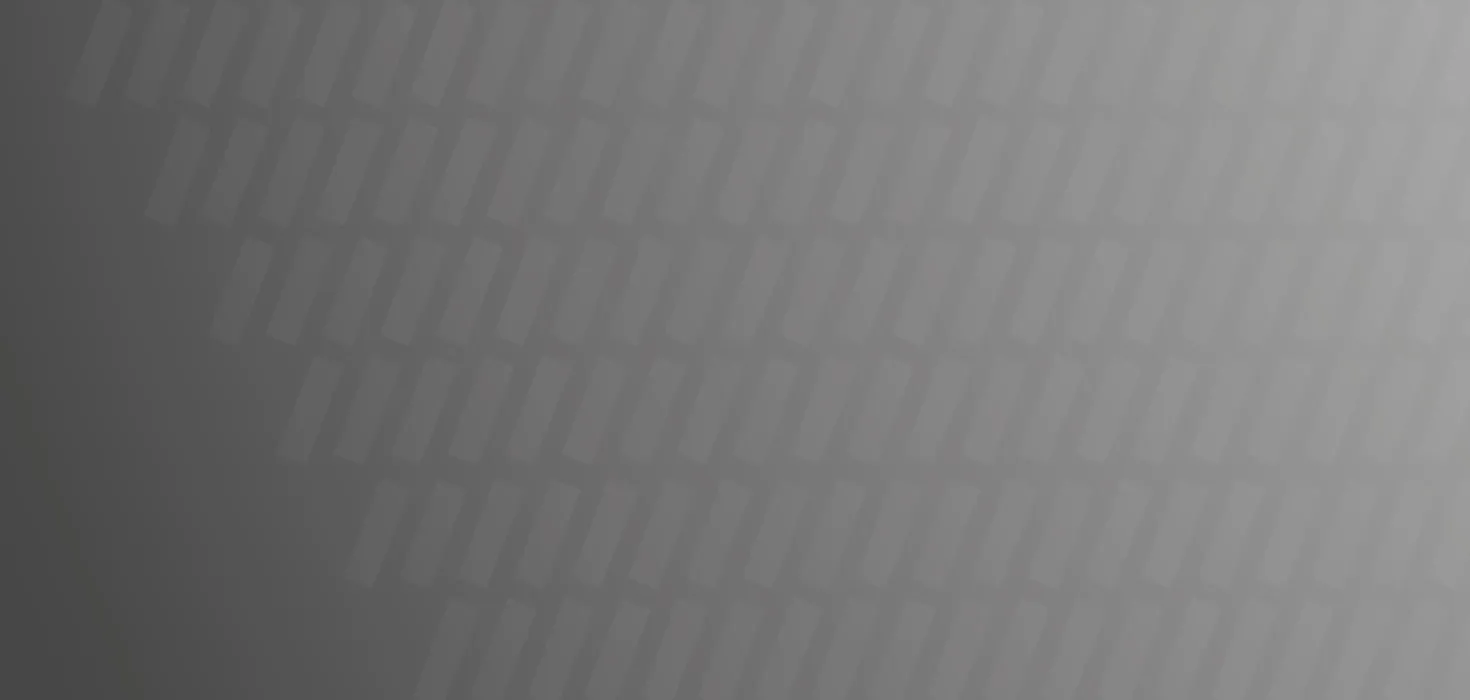
Abfallfreie Herstellung von hochtemperaturfesten Formdichtringen
Neuentwicklung eines Verfahrens zur Herstellung von metallischen Formdichtringen
Nickelbasislegierungseinsparung
Die ElringKlinger AG beschäftigt sich unter anderem mit der Herstellung von metallischen Dichtelementen für die Automobilindustrie. Dabei blieb bislang ein sehr hoher prozentualer Anteil des Materials als Stanzabfall übrig und das Verfahren war sehr aufwendig und teuer. Um das zu ändern, hat das Unternehmen ein komplett neues ressourceneffizientes Verfahren entwickelt.
Zu den Kernkompetenzen der ElringKlinger AG zählt unter anderem die Herstellung von metallischen Dichtelementen für die Automobilindustrie. Hierbei wird als Standardverfahren ein Stanz-/Biegeprozess angewandt. Dieser ist auch Stand der Technik bei der Produktion von Formdichtringen, die in erster Linie das Gehäuse von Abgasturboladern abdichten. Die Formdichtringe sind dabei höchsten thermischen und wechselthermischen Belastungen ausgesetzt. Um eine Abdichtung auch bei Abgastemperaturen oberhalb von 1.050 °C zu gewährleisten, ist der Einsatz von Nickelbasislegierungen unumgänglich. Mit Einkaufspreisen von 50 bis 500 Euro/kg zählen diese Legierungen mit zu den teuersten industriell verwendeten metallischen Werkstoffen.
Aufgrund der Geometrie eines solchen Formdichtrings – mit vergleichsweise geringem Rand und großem Gaskanal in der Mitte – fällt bei einem konventionellen Stanzprozess bis zu 90 % Stanzabfall an. Zudem ist die Herstellung eines entsprechenden Werkzeugs aufgrund vieler einzelner Folgeverbundschritte äußerst aufwändig und daher mit sehr hohen Kosten verbunden.
Diese unbefriedigende Ausgangslage gab dem Geschäftsbereich Spezialdichtungen der ElringKlinger AG den Anstoß, ein neuartiges Fertigungsverfahren zu entwickeln. Dabei ging es primär um zwei Zielsetzungen: Zum einen sollte möglichst wenig Stanzabfall anfallen, zum anderen wollte man einfache und kostengünstige Werkzeuge verwenden.
Der neue Prozess sollte folgendermaßen ablaufen: Zunächst wird der Anlage ein schmaler Endlosstreifen zugeführt und dort auf das gewünschte Maß gekürzt. Anschließend wird dieser Zuschnitt zu einem Ringband geformt und in der Anlage verschweißt. Über spezielle Rollierwerkzeuge erhält das entstandene Ringband seine charakteristische Form, so dass sich ein fertig fallendes Werkstück vollautomatisch produzieren lässt.
Des Weiteren muss die Fertigungsanlage über umfassende Prozesskontrolleinrichtungen verfügen, damit ein potenziell fehlerhaftes Teil umgehend aussortiert wird. Dies verhindert unnötige weitere Prozessschritte und spart Ressourcen ein. Ebenso können Fehler schnellstmöglich erkannt und abgestellt werden. Dadurch lassen sich die Ausschussraten stetig effektiv reduzieren. In einem konventionellen Folgeverbundwerkzeug, wie es bei einem Stanzprozess zum Einsatz kommt, ist dies nicht möglich, da eine Kontrolle zwischen den einzelnen Hüben der Presse aus technischen Gründen nicht machbar ist. In diesem Fall sind sowohl unnötige Hübe der Presse und somit ein erhöhter Werkzeugverschleiß als auch ein größerer Energiebedarf je Gutteil die Folge.
Gemeinsam mit der Otto Bihler Maschinenfabrik ist es gelungen, in einer nahezu fünfjährigen Entwicklungszeit das neu konzipierte Fertigungsverfahren umzusetzen. Hierfür wurde der komplette Prozess von der Materialzuführung über den Zuschnitt und die Umformung bis hin zum Schweißverfahren präzise überarbeitet. Zudem wurde eine komplett neue Werkzeugtechnik entwickelt und zum Serienstand etabliert. Darüber hinaus galt es, prozessbegleitende Kontrolleinrichtungen zu implementieren. Diese überprüfen das Bauteil bereits in der Anlage auf Maßhaltigkeit, Qualität der Schweißnaht sowie Dichtheit. So lassen sich bereits frühzeitig Schlechtteile aussortieren, ohne dass sie weitere, unnötige Prozessschritte durchlaufen.
Die quantifizierbaren Einsparungen betreffen hauptsächlich den Materialeinsatz. Bezogen auf den jetzigen Auslastungsgrad ergibt sich jährlich eine Gesamteinsparung von 21 t Nickelbasislegierung gegenüber dem konventionellen Stanz-/Biegeprozess. Neben der direkt sichtbaren Vermeidung von Stanzabfall werden durch wegfallende Abfalltransportwege und nicht mehr erforderliche zusätzliche Einschmelzungen ebenfalls Ressourcen in großem, wenn auch schwer zu bezifferndem Umfang eingespart.
Darüber hinaus liegt der Energiebedarf des neuen Produktionsverfahrens um ein Vielfaches niedriger als der eines konventionellen Stanzprozesses. Zudem sinkt der Bedarf an Hilfswerkstoffen, wie Stanzölen und dergleichen. Da die Energiebilanz jedoch ganzheitlich betrachtet werden muss, ist hier aufgrund des etwaigen Ausschusses bei unterschiedlichen Maschinengrößen und -ausbringungen keine quantitative Aussage zur Energieeinsparung möglich.
Durch die Kooperation mit der Otto Bihler Maschinenfabrik und dank der Bereitschaft, etablierte Herstellungsprozesse infrage zu stellen, ist es ElringKlinger gelungen, ein völlig neuartiges Fertigungsverfahren zu entwickeln. Solche Lösungen lassen sich nur mit einer ausgeprägten Innovationsbereitschaft und dem nötigen Fachwissen realisieren.
Veränderungen in gewachsenen Strukturen sind immer mit besonderen Herausforderungen verbunden. Eine Kernkompetenz des Geschäftsbereichs Spezialdichtungen der ElringKlinger AG liegt in Stanz-, Biege- und Tiefziehprozessen. Auf diesem Fachgebiet wurde über Jahrzehnte hinweg Know-how aufgebaut. Dennoch konnte ein komplett neues Produktionsverfahren für ein metallisches Formdichtelement erfolgreich implementiert werden. Dies zeugt sowohl von der Offenheit gegenüber neuen Ideen als auch dem visionären Zukunftsdenken der Mitarbeiter.
Mittlerweile wurde bereits die dritte Anlage in Betrieb genommen und eine vierte ist in Planung.
Ihren Ursprung hat die ElringKlinger-Gruppe in einem 1879 von Paul Lechler in Stuttgart gegründeten Handelshaus für technische Produkte und Dichtungen. Das Unternehmen fokussiert seine Kraft auf die Entwicklung zukunftsweisender, grüner Technologien. Diese tragen nicht nur zur CO2-Reduzierung bei, sondern helfen auch, gesundheitsschädigende Stickoxide, Kohlenwasserstoffe und Ruß zu vermindern. Egal, ob für den mittels Downsizing optimierten klassischen Verbrennungsmotor oder für das batterie- oder brennstoffzellengespeiste Elektroauto: Als einer von nur wenigen Automobilzulieferern weltweit entwickelt und produziert ElringKlinger bereits heute technologisch anspruchsvolle Komponenten für alle Antriebsarten. Mit seiner Leichtbaukompetenz trägt das Unternehmen entscheidend dazu bei, das Fahrzeuggewicht und damit den Verbrauch weiter abzusenken. Partikelfilter und komplette Abgasreinigungssysteme für Anwendungen in Schiffen, Nutzfahrzeugen, Baumaschinen und Stationärmotoren sowie in Kraftwerken runden das Angebot zur Emissionsreduzierung ab. Die ElringKlinger Kunststofftechnik ergänzt das Portfolio um Produkte aus dem Hochleistungskunststoff PTFE (Polytetrafluorethylen) – auch für Branchen außerhalb der Automobilindustrie. Seine Innovationskraft nutzt ElringKlinger gezielt für nachhaltige Mobilität und ertragsorientiertes Wachstum. Dafür engagieren sich innerhalb des ElringKlinger-Konzerns über 7.900 Mitarbeiter an 45 Standorten rund um den Globus.
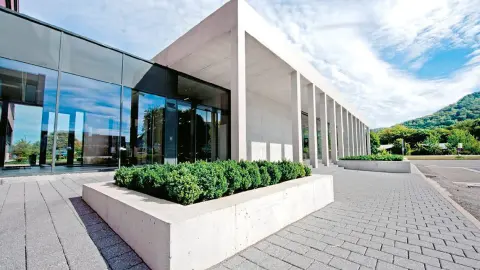
- Großserienfertigung
- Entwicklung / Konstruktion ,
- Verarbeitungsprozess
- Prozessinnovation
- Material ,
- Metalle
- taktisch (1 bis 5 Jahre)