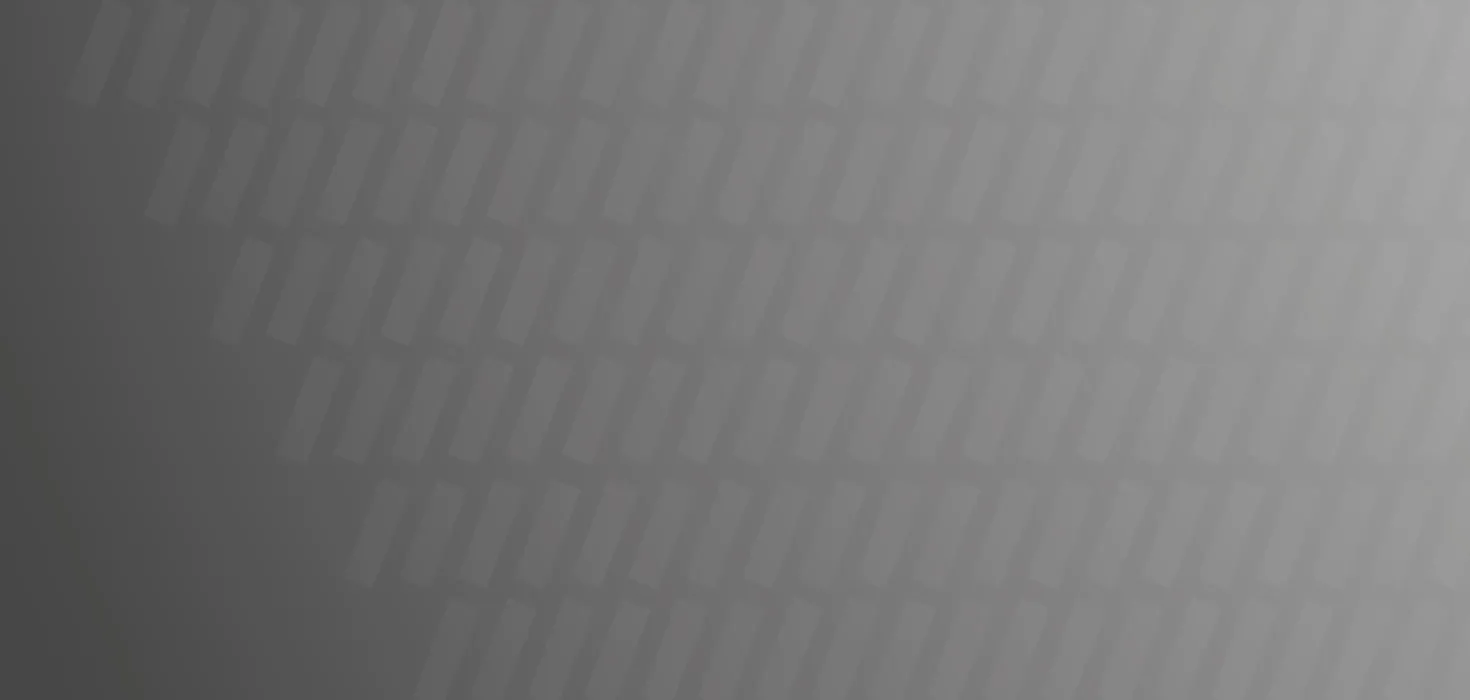
Alternativer Brennstoff für die Zementindustrie
Aufbereitung verschiedener hochkalorischer Abfälle zu Brennstoffen für die Zementindustrie
Steinkohlestaubreduktion
CO2-äquivalente Reduktion
ELM Recycling gehört zu den führenden Unternehmen der Recyclingwirtschaft Europas. Die Kunden der Zementindustrie gehören zu den energieintensivsten Branchen, weswegen ELM sich das Ziel gesetzt hat, eine möglichst hohe Einsparung an fossilem Brennstoff zu ermöglichen. Dazu wurde ein Aufbereitungsverfahren entwickelt, mit dem Ersatz-Brennstoffe mit hohen Substitutionsraten eingesetzt werden können.
Die Zementindustrie gehört zu den energieintensivsten Branchen. Die notwendige Energie wird bei der Zementherstellung im Wesentlichen für das Sintern des Zementklinkers aufgewendet. Dazu werden traditionell fossile Brennstoffe, wie Steinkohle, Braunkohle, Petrolkoks und in geringem Umfang auch schweres Heizöl, als Primärenergieträger verwendet. Geänderte rechtliche und wirtschaftliche Rahmenbedingungen haben jedoch dazu geführt, dass zunehmend alternative Brennstoffe eingesetzt werden. Der Einsatz von Ersatzbrennstoffen (EBS) gewährleistet vor diesem Hintergrund die Wettbewerbsfähigkeit der deutschen Zementherstellung und verringert die starke Abhängigkeit von fossilen Brennstoffen. Die ELM Recycling GmbH & Co. KG (ELM) hat ein mechanisches Aufbereitungsverfahren entwickelt, das die Voraussetzung schafft, alternative Brennstoffe beim Klinkerbrennprozess direkt am Brenner und mit hohen Substitutionsraten einzusetzen. In Heidenheim-Mergelstetten versorgt die ELM seit dem Jahr 2007 exklusiv ein Zementwerk mit alternativem Brennstoff. Der Produktionsstandort zur EBS-Herstellung befindet sich direkt angrenzend zum Zementwerk auf einem etwa 12.000 m2 großen Betriebsgelände der ELM. Anfangs lag die Quote des eingesetzten Ersatzbrennstoffs noch bei ca. 50 %. Diese Substitutionsquote sollte jedoch immer weiter erhöht werden, um eine möglichst hohe Einsparung an fossilem Brennstoff zu erreichen. Das Ziel ist es, in den nächsten Jahren möglichst eine 100-prozentige Substitutionsrate zu erreichen.
Die Nähe zum Abnehmer der Brennstoffe war eine entscheidende Voraussetzung für die Investition in eine mechanische Abfallaufbereitungsanlage. Dadurch können Logistikkosten auf ein Minimum reduziert werden und es entfallen die Transportkosten des aufbereiteten Brennstoffs zum Zementwerk. Vor allem aber kann der Brennstoff speziell auf die technischen Erfordernisse des einzigen Abnehmers konzipiert und produziert werden. Der alternative Brennstoff sollte hinsichtlich seiner Handhabung und der Einbringung in den Verbrennungsprozess direkt am Brenner die gleichen Eigenschaften haben wie der Primärenergieträger, um die angestrebten Substitutionsraten zu erreichen.
Durch den Einsatz direkt am Brenner kann der zuvor verwendete Kohlestaub ohne Qualitätsverlust durch den alternativen Brennstoff ersetzt werden.
Dem Team der ELM, bestehend aus Ingenieuren und Technikern, ist es gelungen, einen mechanischen Prozess zu entwickeln, der es erlaubt, einen qualitativ hochwertigen Brennstoff zu erzeugen, der die hohen Anforderungen des Zementklinkerprozesses einhält.
Dabei schließen die Vorzerkleinerer das Material soweit auf, dass im weiteren Verarbeitungsprozess eine Abtrennung eventuell anhaftender oder eingeschlossener Störstoffe möglich ist. In den darauf folgenden Nachzerkleinerern werden die Materialien auf eine Korngröße kleiner als 30 mm zerkleinert und dabei so aufgeschlossen, dass sowohl eine gute Förderfähigkeit als auch eine große Oberfläche der Einzelpartikel erzeugt wird, mit der die erforderlichen Zündeigenschaften ermöglicht werden. Ein zusätzlich nachgeschalteter Infrarot-Scanner entfernt noch enthaltene, nicht-EBS-fähige Störstoffe, die ca. 7 % des Inputstroms ausmachen, um damit die Einhaltung der festgeschriebenen Schwermetallund Chlorgrenzwerte gewährleisten zu können. Das so produzierte (Fertig-)Produkt wird noch einer Nachreinigung in einer eigens entwickelten Abscheidetechnik im Fallstrom des fertigen EBS zur Abtrennung kleinster Metallteile unterzogen. Somit werden die im Abfall enthaltenen Metalle zu nahezu 100 % abgetrennt und einem stofflichen Recycling zugeführt. Danach wird der Brennstoff im Fertigmateriallager zwischengelagert oder direkt zum Abnehmer transportiert. Sämtliche Verfahren werden seit Inbetriebnahme in enger Abstimmung mit dem benachbarten Abnehmer immer weiter optimiert. Das so hergestellte Brennstoffprodukt besteht aus heizwertreichen organischen Materialien der Stoffgruppen Kunststoff, Papier und Textil bzw. Verbundwerkstoffen, das auch als zweidimensionales Material bezeichnet werden kann, da es ausschließlich aus dünnwandigen Stoffen besteht. Dies ist wiederum die Voraussetzung zur Herstellung eines hochwertigen blasfähigen EBS mit Verbrennungseigenschaften, die weitgehend denen von Kohlenstaub entsprechen. Da der bei der Verbrennung entstehende Ascheanteil zudem gewollt in das Produkt Zementklinker eingebunden wird, liegt hierbei zudem eine simultane energetisch-stoffliche Verwertung vor.
Der Abnehmer von ELM erreicht mit dem gelieferten Brennstoff im Jahresdurchschnitt in der Brenn-/Sinterzone eine Substitutionsrate von 90 % der fossilen Brennstoffe und geht damit weit über die Einsatzraten anderer Unternehmen hinaus. Dies ist nach dem jetzigen Kenntnisstand die höchste Substitutionsrate europaweit, die direkt am Brenner in einem Zementwerk erreicht wird. Durch den komplexen mehrstufigen Produktionsprozess entsteht ein Brennstoff, der im Zementherstellungsprozess die gleichen Eigenschaften des sonst verwendeten Primärbrennstoffs Kohlestaub hat und diesen somit unmittelbar ersetzt. Insgesamt können so am Standort Mergelstetten durch den Einsatz von ca. 90.000 t EBS/Jahr rund 80.000 t Steinkohlestaub und rund 66.000 t C02-Äquivalente eingespart werden. Die energetische Nutzung in der MVA wurde als Vergleichsprozess nicht bilanziert. Zur Herstellung einer Tonne alternativen Brennstoffs werden ca. 40 bis 45 kWh an elektrischer Energie benötigt. Bei einem Heizwert von 23 MJ/kg entspricht dies dem Energiegehalt von ca. 7 kg Brennstoff also nur ca. 0,7 % des Brennstoffenergiegehalts.
Die Nutzung der hochkalorischen, nicht mehr stofflich nutzbaren Abfälle als EBS in der Klinkerherstellung ist auch deshalb sinnvoll, da hierbei ein Nettowirkungsgrad von durchschnittlich 70 % erreicht wird. Dieser Wert entspricht dem herkömmlich eingesetzten Primärbrennstoff Steinkohle. Dieser Nettowirkungsgrad ist allerdings deutlich größer als bei der Verbrennung in einer Müllverbrennungsanlage (MVA), der im Durchschnitt bei ca. 45 % liegt. Aufgrund des hohen Heizwerts dieser Abfälle würden dort zudem Kapazitäten verdrängt, welche zur energetischen Behandlung niederkalorischer Siedlungsabfälle derzeit dringend benötigt werden.
Ein Alleinstellungsmerkmal stellt darüber hinaus die simultane stoffliche Nutzung des Ascheanteils dar, der als anfallender Sekundärrohstoff in den Zementklinker eingebunden wird und ca. 10 % des eingesetzten EBS ausmacht. Diese Art der stofflichen Nutzung können weder MVA noch EBS-Kraftwerke erbringen. Die beim Verbrennungsprozess im Drehrohrofen entstehende Asche wird direkt in das Produkt (Zementklinker) eingebunden und spart an dieser Stelle den entsprechenden Anteil an primären Ressourcen ein.
Bei den direkt auf dem Zementwerksgelände zur Brennstoffherstellung verwendeten Abfällen handelt es sich zudem i. d. R. um heimische Ressourcen, welche den größtenteils aus nicht-europäischen Ländern stammenden Primärenergieträger Steinkohle ersetzen. Auch hierdurch werden erhebliche Logistikressourcen und -emissionen eingespart.
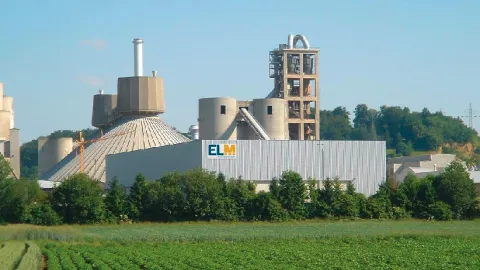
Die größte Herausforderung des Prozesses war die möglichst vollständige Ausschleusung unterschiedlichster Schad- und Störstoffe sowie die Erreichbarkeit eines Zünd- und Brennverhaltens, das dem substituierten Primärbrennstoff gleichkommt. Die hohen Anforderungen für den Einsatz im Zementklinkerherstellungsprozess mit derart hohen Substitutionsraten können nur durch die ständige Optimierung des mechanischen Aufbereitungsprozesses erreicht werden. Dies erfolgt in enger Abstimmung mit dem Zementwerk. Die kurzen Wege und eine gute Kommunikation sind unerlässlich, um flexibel auf die individuellen Bedürfnisse der Produktion am Standort eingehen zu können. Weitere Optimierungen sowie die Einbeziehung anderer Abfallströme sind geplant.
Die ELM Recycling GmbH & Co. KG, ein typisches mittelständisches eigentümergeführtes Unternehmen, wurde 1998 von den geschäftsführenden Gesellschaftern am heutigen Hauptsitz in Bissingen a. d. Teck gegründet und gehört mittlerweile, mit vier Produktionsstandorten in Baden-Württemberg und einem in Bayern, europaweit zu den führenden Unternehmen in der Ersatzbrennstoffaufbereitung. Die hohe Qualität der hergestellten Sekundärbrennstoffe wird zudem über die Auszeichnung mit dem RAL-Gütezeichen 724 dokumentiert. Die ELM Recycling GmbH & Co. KG ist heute ein Know-how-Träger auf dem Gebiet der alternativen Brennstoffherstellung aus Abfällen, mit dem Potenzial, diese Technologie auch in weitere Länder zu exportieren, da geeignete Abfälle in allen EU-Mitgliedstaaten in hohen Mengen anfallen.
- Prozessindustrie
- Entsorgung / Recycling
- GreenTech BW ,
- Produktinnovation ,
- Ausbeuteerhöhung ,
- Stoffkreislauf / Recycling
- Material ,
- Sonstige Materialien ,
- Abgas
- strategisch (größer 5 Jahre)