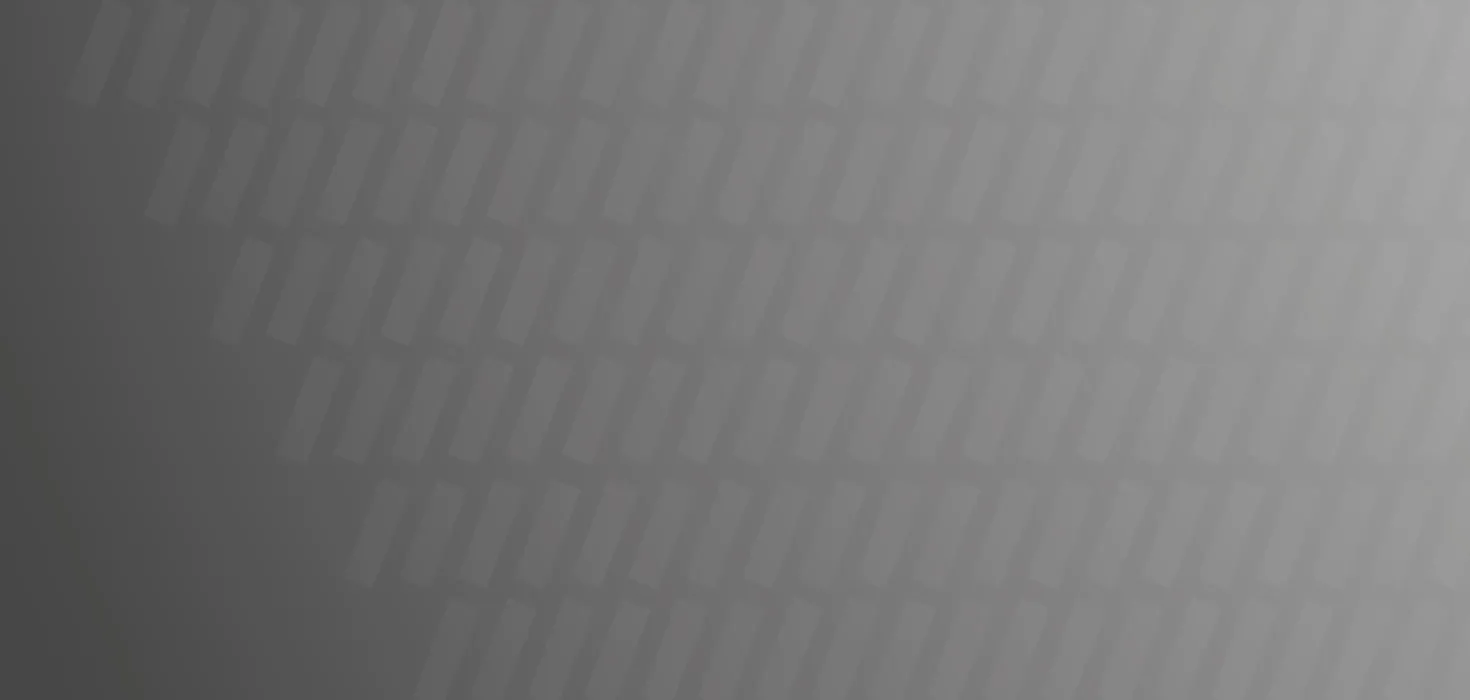
Energie- und Ressourceneffizienz durch Mehrfachnutzung von Rohstoffen
Entwicklung einer Methode zur ressourcenschonenden Mehrfachnutzung hochwertiger Polyurethan-Hartschäume
Die puren GmbH zählt zu den Pionieren der Polyurethan-(PUR)-Hartschaumtechnologie. Da bei der Verarbeitung von PUR einige Reststoffe anfallen, die nicht einschmelzbar sind, war es das Ziel des Unternehmens, neue Produkte und Produktionsverfahren zu entwickeln, damit diese Reststoffe nicht entsorgt werden müssen, sondern für neue Produkte eingesetzt werden können. So entstand das Produkt purenit®.
Die puren gmbh aus Überlingen zählt zu den Pionieren der Polyurethan-(PUR)-Hartschaumtechnologie. Das Unternehmen produziert für unterschiedliche Branchen und Anwendungsbereiche Konstruktionsdämmstoffe und Funktionswerkstoffe aus PUR-Hartschaum und Polyisocyanurat-Hartschaum (PIR).
Bei der Herstellung und Weiterverarbeitung von PUR-Dämm- und Konstruktionswerkstoffen fallen PUR-Reststoffe an, die weder einschmelzbar sind, wie beispielsweise auch Holz, noch in den Produktionskreislauf der ursprünglichen PUR-PIR-Hartschäume rückführbar sind. Die anfallenden Reststoffe mussten und müssen teilweise bei einigen Unternehmen heute noch aufwendig entsorgt, d. h. verbrannt werden. Die Problematik der PUR-Reststoffe ist bei puren nahezu seit der Unternehmensgründung vor 48 Jahren bekannt. Seit jener Zeit wurde von puren nach Alternativen im Umgang mit den PUR-Reststoffen geforscht und neue Produkte entwickelt, die andere Eigenschaften haben als die von PUR-PIR-Hartschäumen.
Das Ziel des Unternehmens bestand daher darin, neue, umweltschonende und nachhaltige Produkte und Produktionsverfahren zu entwickeln, um die hochwertigen PUR-Reststoffe dem Produktionskreislauf neuer Produkte für neue Anwendungen zuzuführen.
Durch eine Mehrfachnutzung der hochwertigen PUR-Hartschäume aus unterschiedlichen Funktionsbereichen sollte die Ressourceneffizienz gesteigert werden. Neben den anfallenden Produktionsresten sollten auch Reststoffe aus dem Rückbau in den Kreislauf eingehen. Von zentraler Bedeutung war der Aufbau eines praxistauglichen Konzeptes welches von Dipl.-Kfm. Hans Bommer, Unternehmensgründer der puren gmbh, entwickelt und mit Richard Stehle realisiert wurde.
Das von Hans Bommer entwickelte Verfahren soll am Beispiel typischer Tiefkühlkoffer-Aufbauten von Nutzfahrzeugen dargestellt werden. Diese Aufbauten bestehen aus Verbundelementen aus PUR und Polyester. Für einen Tiefkühlkoffer-Aufbau werden rund 13 m³ PUR benötigt. Die durchschnittliche Nutzungsdauer beträgt 15 Jahre.
Nach dem Gebrauchszyklus des Tiefkühlkoffer-Aufbaus kann der Tiefkühlkoffer mit der entwickelten purenit®-Technologie einer Mehrfachnutzung zugeführt werden, wodurch eine Verbesserung der Ressourceneffizienz erzielt wird. Der Kunststoff-Aufbau (PUR/ Polyester) wird geschreddert, aufbereitet und anschließend der Herstellung des Funktionswerkstoffs purenit® zugeführt. Dabei werden nur ca. 10 bis 12 % neue Rohstoffe verwendet, so dass die Ressourcenschonung bei ca. 88 bis 90 % liegt.
Der neue Funktionswerkstoff kann im Bauwesen eingesetzt werden. Für die Produktion von purenit® hat puren ein Produktionswerk mit zwei großen Fertigungsstraßen errichtet, auf denen PUR-Reststoffe aus der eigenen PUR-/PIR-Hartschaum-Produktion, aus Kundenverarbeitung und von Dritten aus dem In- und Ausland verarbeitet werden. Das Verfahren beinhaltet eine Homogenisierung, so dass sich keine Probleme infolge unterschiedlicher Herkunft der PUR-Reststoffe ergeben.
Aus dem beschriebenen Tiefkühlkoffer-Aufbau werden ca. 1,2 m3 Funktionswerkstoff purenit® hergestellt. Bei der Verwendung des neuen Funktionswerkstoffs purenit® im Bauwesen beträgt die durchschnittliche Nutzung 50 Jahre. Die dabei zu erzielende Energieeinsparung beträgt für 1,2 m³ neuen Funktionswerkstoff ca. 24,5 MWh. Selbst nach 50 Jahren sind keine nennenswerten Änderungen der technischen Daten zu erwarten. Der Funktionswerkstoff kann nach der Nutzungsphase von 50 Jahren und mehr weitere zwei- bis dreimal aufbereitet werden. Aufgrund der Rohdichte des Funktionswerkstoffs beträgt die Dämmleistung ca. ein Drittel des PUR-Hochleistungsdämmstoffs, d. h. ca. 0,44 MWh/m3 pro Jahr.
Am Ende des Lebenszyklus des ersten purenit® wird purenit® in gleicher Weise aufbereitet und mit einem geringfügig höheren Rohstoffanteil (Bindemittel) von ca. 1,2 % gegenüber dem ersten Rohstoffinput (Bindermittel) von ca. 10 % gefertigt. In dieser zweiten Nutzungsphase kann für die 1,2 m³ purenit® eine Energieeinsparung von ca. 24,5 MWh erreicht werden. Ähnlich verhält es sich für die dritte Nutzungsphase. Am Ende des zweiten Lebenszyklus wird das zweite purenit® in gleicherweise aufbereitet und mit einem geringfügig höheren Rohstoffanteil (Bindemittel) von ca. 1,2 % gegenüber dem zweiten gefertigt. Die in der dritten Nutzungsphase erzielte Energieeinsparung liegt dann bei etwa 24,4 MWh.
Am Ende der dritten Nutzungsphase wird das purenit® der thermischen Verwertung zugeführt, wodurch rund 4,8 MWh Energie erzeugt werden.
Die Einsparung von insgesamt ca. 324,2 MWh entspricht einer CO2-Reduktion von ca. 79,1 t über den gesamten Lebenszyklus inklusive der mehrfachen Aufbereitung. Dabei werden außerdem thermische Stickoxide, Monoxide und Staub (Feinstaub) reduziert. Durch die Mehrfachnutzung bei relativ geringem Anteil an neuen Rohstoffen ergibt sich eine Ressourceneffizienz von ca. 88 bis 90 %.
Selbst wenn ein Drittel der purenit®-Produkte in Industrieanwendungen (z. B. Schienenfahrzeuge, Container usw.) statt im Bauwesen verwendet wird und der Lebenszyklus nur bei 20 Jahren liegt, ergibt sich immer noch eine beachtliche Energieeinsparung von ca. 53 MWh, eine Ressourcenschonung von ca. 88 bis 90 % und eine Nachhaltigkeit von purenit® in einer Größenordnung von 120 Jahren (20 Jahre + 2 x 50 Jahre).
Durch umfangreiche Forschungs- und Entwicklungsbemühungen sowie Investitionen ist es gelungen, eine überzeugende Technologie zur ökologischen und ökonomischen Verwertung von PUR-Hartschaum-Reststoffen zu entwickeln. Möglich wurde dies durch das umfangreiche Know-how des Unternehmens in der PUR-Hartschaumtechnologie. Die über viele Jahre konsequente Verfolgung des Entwicklungsvorhabens und die intensive Marktbearbeitung haben zu einem weiteren sicheren Standbein des Unternehmens geführt. Ausdauer, Mut und Risikobereitschaft haben sich gelohnt. Der weitere Ausbau der purenit®- Linien ist in vollem Gange.
Mit purenit® ist es gelungen, ein neues Produkt zu schaffen und einen neuen Markt zu erschließen. Mittlerweile verfügt das Unternehmen über eine breite purenit®-Produktfamilie (Produkttypen mit kundenspezifischen Eigenschaften).
Die puren gmbh ist ein mittelständisches Familienunternehmen mit ca. 300 Mitarbeiterinnen und Mitarbeitern. Das Unternehmen zählt zu den Pionieren auf dem Gebiet der Polyurethan-Technologie, besonders bezüglich Hochleistungsdämmstoffe, Konstruktions- und Funktionswerkstoffe. Das heutige Tätigkeitsfeld der puren Gruppe ist breit gefächert. Der Geschäftsbereich Bau umfasst Herstellung und Vertrieb von Wärmedämmelementen und -systemen für geneigte und flache Dächer, Böden und Decken sowie Fassaden. Im Geschäftsbereich Industrie erfordern komplexe Anwendungen immer wieder neue und kreative PUR-Lösungen. Hier fertigt puren großformatige Hartschaumblöcke mit verschiedensten spezifischen Eigenschaften, die nach Kundenwunsch noch weiter konfektioniert werden. Zu diesen beiden Kernbereichen ist im Jahr 2004 die Sparte purSonic® mit einer faszinierenden Soundtechnik hinzugekommen, die durch die Entwicklung eines besonderen PUR-Werkstoffes ermöglicht werden konnte. Mit purSonic® werden Wände und Decken zur unsichtbaren Schallquelle und bieten Designern und Innenarchitekten ganz neue Gestaltungsmöglichkeiten.
Schon immer spielten für puren auch Themen wie Umweltschutz, Energieeinsparung und Ressourcenschonung eine große Rolle. Bereits Anfang der 1970er Jahre war puren ein Pionier im Bereich Nachhaltigkeit. Mit der Rückführung der Produktionsreststoffe in den Wertstoffkreislauf und der Entwicklung des Funktionswerkstoffes purenit® sowie effizienter Öl- und Chemikalienbindemittel für Böden und Gewässer war puren bereits damals seiner Zeit voraus.

- Prozessindustrie
- Entsorgung / Recycling
- Dämmung / Isolation ,
- Produktinnovation ,
- Stoffkreislauf / Recycling
- Material ,
- Kunststoffe
- strategisch (größer 5 Jahre)