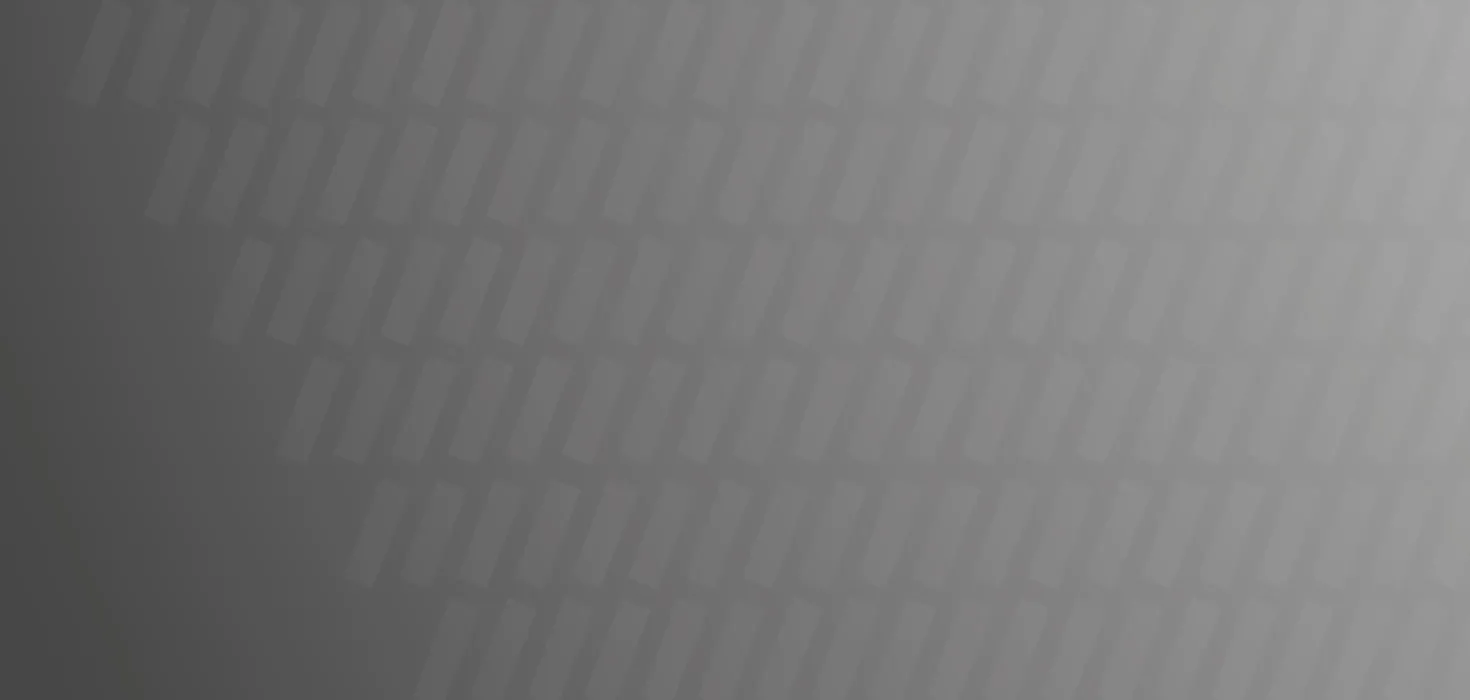
Gummimatten aus Altreifenrecyclat
Verwendung eines neuen, innovativen Verfahrens
CO2-Einsparung
Die matteco GmbH nutzt ein innovatives Verfahren, um Gummimatten herzustellen. Hierbei werden Altreifen granuliert und können so zu 100 % wiederverwendet werden. Dieses Herstellungsverfahren ist spart Ressourcen und Energie ein. Dabei ist die Qualität der Produkte durch den kontrollierten Prozess sichergestellt. Es erfüllt die Anforderungen eines neuen Produktes und kann diese substituieren.
Die matteco GmbH wurde gegründet, um ein in der Schweiz entwickeltes Verfahren zur Produktion von Gummimatten aus Altreifenmehl erstmalig großtechnisch für den deutschen Markt umzusetzen. Durch das Verfahren sollen einerseits die Herstellung und der Vertrieb von hochwertigen Gummimatten zu wirtschaftlichen Marktpreisen vorangetrieben werden, sowie andererseits die steigenden ökologischen und umweltspezifischen Ansprüche in diesem Marktsegment erfüllt werden.
Bei den bisher bekannten Verfahren werden die Gummimatten aus Granulat und einem Polyurethan (PU)-Kleber mittels chemischer Bindung hergestellt. Mit dem neuen Verfahren lässt sich erstmals sehr feines Gummimehl aus Altreifen verarbeiten und zu Gummimatten verpressen. Diese können wiederum ohne neuerliche Zugabe von Bindemittel zu 100 % recycelt werden. Des Weiteren erlaubt das neue Verfahren, Altreifengranulat mit Textilanteil, ohne wesentlichen Einfluss auf die Qualität des Endproduktes, zu verarbeiten.
Die Herstellung der Gummimatten stellt eine Alternative zur weitverbreiteten thermischen Verwertung von Altreifen in Zementwerken dar. Die matteco GmbH hat es sich zum Ziel gesetzt, sowohl Gummimatten aus der Herstellung nach herkömmlicher Methode als auch vermehrt Neuware aus Kautschukprodukten zu ersetzen. Dies würde zu einer wesentlichen Reduzierung von CO2-Emissionen sowie zu einem verminderten Einsatz von Bindemitteln führen.
Die Innovation liegt in der Verwendung von sehr feinem Gummimehl in Verbindung mit einem geringen Anteil an Bindemittel in Form eines Schmelzklebers. Die beiden Komponenten werden gemischt und in einem Pressensystem unter hohem Druck thermisch verpresst. Hierbei entsteht ein Gummiprodukt mit einer sehr homogenen und feinen Struktur sowie Eigenschaften, die nahe an die von Kautschukprodukten heranreichen.
Die hergestellten Gummimatten sollen hervorragende, spezifische Eigenschaften hinsichtlich der Reduzierung von auftretenden Schwingungen und von Körperschall besitzen und eine Verbesserung der Trittschalldämmung sowie der Rutschhemmung zur Ladungssicherung im Transportwesen bieten. Die Zielkundensegmente sind demzufolge neben der Industrie und dem Transportwesen, wie Lkw und Bahn, auch der Hoch- und Tiefbau.
Das für die Produktion erforderliche Pressensystem wurde in enger Zusammenarbeit mit einem deutschen Pressenhersteller entwickelt und hergestellt. Die für das Produktportfolio notwendigen Parameter und Rezepte wurden nach erfolgter Inbetriebnahme der Anlage zusammen mit dem Schweizer Verfahrensentwickler erarbeitet. Hierfür wurde eine komplette Produktionsstätte im badischen Kappelrodeck aufgebaut, die es erlaubt, in der ersten Ausbaustufe bis zu 600 t Altreifenmehl pro Jahr zu verarbeiten.
Das Rohmaterial, ein Feinmehl aus Altreifengummi, wird in der Anlage mit einem Copolyester Schmelzkleber ohne Weichmacher gemischt und mittels Spezialverfahren erwärmt, gepresst und danach abgekühlt. Die hergestellten Gummimatten bleiben beim Verwenden absolut eben auf dem Boden liegen und haben nicht das Bestreben, sich wieder zusammen zu rollen. Der speziell entwickelte Schmelzkleber verbindet das Gummimehl ganzflächig. Durch die Elastizität dieses speziellen Schmelzklebers ergeben sich keine harten Soll-Bruchstellen wie bei einer Gummigranulatmatte mit PU-Bindemittel. Die komplette Vernetzung des Feinmehls mit dem Bindemittel erlaubt eine sehr hohe mechanische Beanspruchung, ohne dass es zu einer Kugelbildung, d. h. einem Herauslösen von Granulat, kommt. Durch die geschlossene Oberfläche kann kein Schmutz in die Gummiprodukte eindringen und die Funktion negativ beeinflussen.
Gebrauchte Gummimatten können von matteco zurückgenommen werden. Nach einer Überprüfung, werden diese gereinigt, zerkleinert und dem Produktionsprozess wieder zugeführt, und das ohne neuerliche Zugabe von Bindemittel. Somit hat matteco einen geschlossenen Stoffkreislauf geschaffen, bei dem keine Abfälle oder Produktionsreste auf Deponien entsorgt werden müssen.
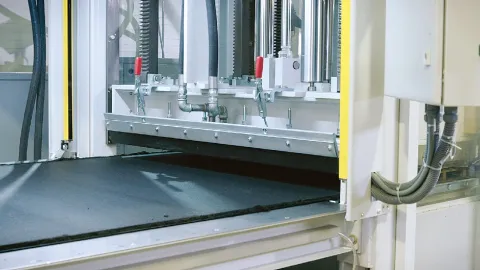
Der wesentliche ökologische Vorteil liegt in der umweltfreundlichen und energiesparenden Herstellung der Gummimatten, u. a. kein Lösemitteleinsatz und hundertprozentige Recyclingfähigkeit. Durch die hohe Qualität der matteco-Produkte ist das Unternehmen in der Lage, teilweise Produkte, die bisher aus synthetischem Gummi hergestellt werden, zu substituieren.
Bei den herkömmlichen Verfahren zur Herstellung von Gummimatten, die von Wettbewerbern eingesetzt werden, werden ausnahmslos Gummigranulate in Verbindung mit einem PU-Binder eingesetzt. Dieses Herstellungsverfahren stellt sich im Vergleich zum von der matteco GmbH geplanten, neuartigen Verfahren deutlich energieintensiver und umweltbelastender dar.
Das Produktspektrum der matteco GmbH sieht eine mögliche Substitution von 22 % Neuware aus Kautschukprodukten sowie 78 % Produkte aus PU-gebundenem Granulat vor. Bei einer geplanten Jahresproduktion von 540 t ergibt sich durch die Energieeinsparungen im Produktionsprozess sowie einem verminderten Einsatz von Bindemittel eine absolute Umweltentlastung von 2.660 t CO2-Äquivalent.
Beim Produkt der matteco GmbH, den Gummimatten aus Altreifen, handelt es sich zwar nicht um ein neues Produkt, dennoch ist es gelungen, neue Maßstäbe bei der Produktion zu setzen. Die matteco GmbH hat es durch grenzüberschreitende Zusammenarbeit mit den Schweizer Verfahrensentwicklern und dem Anlagenbauer aus Deutschland geschafft, eine neue Technologie in Deutschland zum Einsatz zu bringen und so eine Alternative zur thermischen Verwertung der Altreifen zu schaffen. Neben den Kostenvorteilen gegenüber Kautschukprodukten sind vor allem die energetischen Einsparungen bei der Herstellung sowie die hundertprozentige Verwertung der Einsatzstoffe die wesentlichen Wettbewerbsvorteile.
Die matteco GmbH wurde erst im Jahr 2015 von den beiden Ingenieuren Matthias Krieg und Frank Fuhrer sowie dem Kaufmann Bernd Krieg gegründet. Seit Anfang des Jahres 2016 werden am Standort Kappelrodeck erstmalig in Deutschland Gummimatten nach einem neuartigen Verfahren für die Anwendungsbereiche Bau, Industrie und Transport produziert.
In der eigenen Produktionsstätte ist die matteco GmbH in der Lage, schnell und unkompliziert auf Kundenbedürfnisse einzugehen. Mittels einer Schneideanlage können die matteco Gummimatten individuell konfektioniert werden. Durch eine Vielzahl von verschiedenen Rezepturen, lassen sich matteco Gummimatten mit den unterschiedlichsten Eigenschaften speziell auf Wunsch herstellen.
Die Gummimatten können nach Kundenwunsch mit einem speziellen Belag, wie z. B. einem Gewebe aus Polyester, beschichtet werden. Das Bestreben des Unternehmens Ressourcen zu schonen, spiegelt sich bereits im Namen wider, der sich aus Matte und ecological zusammensetzt.
- Kleinserienfertigung ,
- Großserienfertigung
- Verarbeitungsprozess ,
- Entsorgung / Recycling
- Stoffkreislauf / Recycling
- Energie ,
- Material ,
- Kunststoffe ,
- Abgas
- strategisch (größer 5 Jahre)