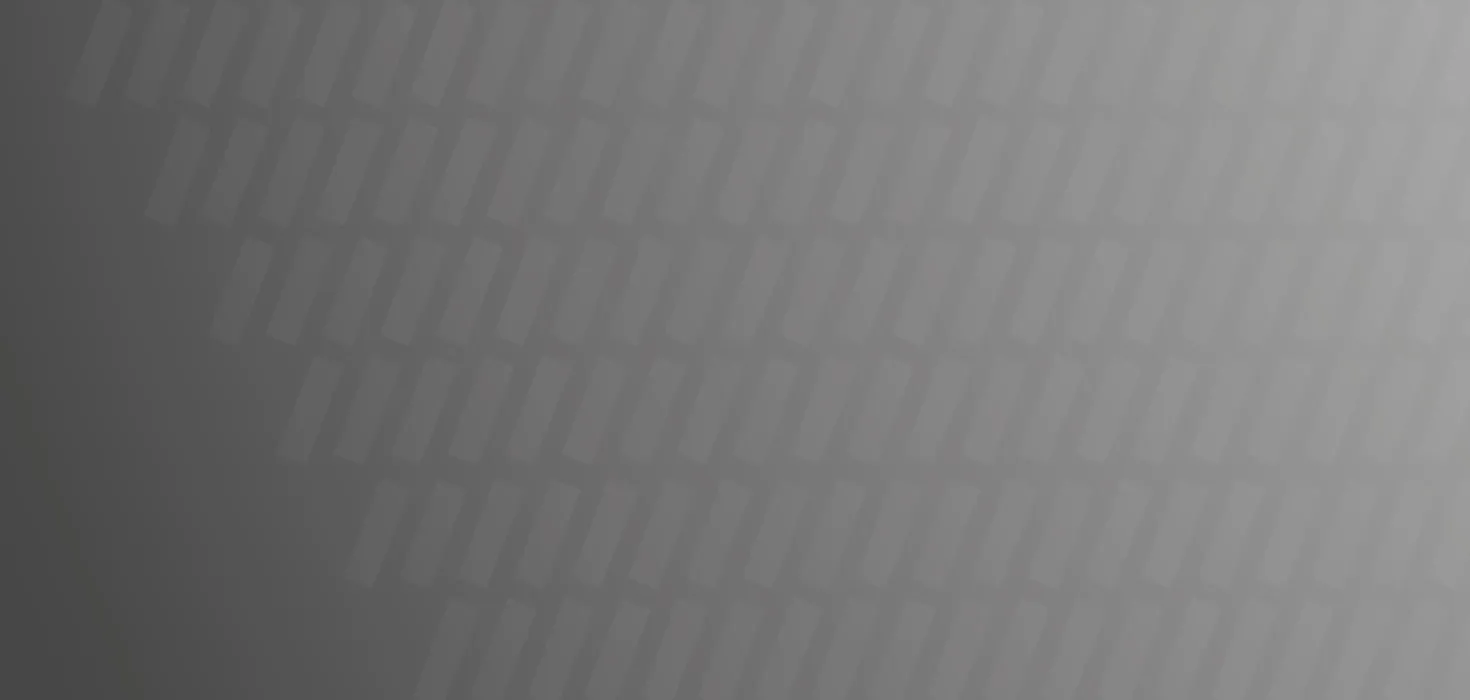
Hochtemperatur- Wärmerückgewinnung aus Härteöfen
Nutzung der Abwärme von Härteöfen zum Beheizen einer Lösemittel-Reinigungsanlage
Stromeinsparung
CO2-Einsparung
IMS Gear ist Spezialist für die Herstellung von Zahnrädern und Getrieben. Diese werden in Härteöfen gehärtet. Bisher wurde die in den Härteöfen entstehende Abwärme kaum genutzt. Das Unternehmen hat es allerdings geschafft, diese Abwärme zurückzugewinnen und nun für das Beheizen seiner Reinigungsanlagen zu nutzen. Somit wird ein großer Anteil an Strom und CO2-Emissionen eingespart.
Der Zahnrad- und Getriebespezialist IMS Gear betreibt an seinem Standort in Donaueschingen eine der weltweit modernsten Härtereien. Dort werden die unterschiedlichen Bauteile in Härteöfen Wärmebehandlungen unterzogen, um die Werkstoffeigenschaften zu optimieren. Bisher wurde die an den Härteöfen entstehende Abwärme ungenutzt an die Raumluft abgegeben und ging somit verloren. In der Härterei werden neben den Öfen vier Reinigungsanlagen zum Reinigen der Teile betrieben, die elektrisch beheizt werden müssen. Der hierfür nötige Strombedarf beläuft sich jährlich auf rund 1.000 MWh. Da es IMS Gear wichtig ist, sowohl Maßstäbe bei der Qualität seiner Prozesse und Produkte als auch in punkto Nachhaltigkeit und Effizienz zu setzen, widmete sich das Unternehmen der Frage, ob und wie sich die Abwärme der Öfen für das Beheizen der Reinigungsanlagen nutzen lässt. Das Ziel des Projekts war es, die Lösemittel-Reinigungsanlagen ohne eine zusätzliche elektrische Beheizung mit der vorhandenen Prozessabwärme betreiben zu können.
Es sollte ein Konzept entwickelt werden, das die Abwärme direkt an der Ofenflamme abgreift. Die zurückgewonnene Wärme sollte dann für das Beheizen der Reinigungsanlagen genutzt werden.
Die konkrete technische Lösung wurde von IMS Gear in enger Zusammenarbeit mit EMO Oberflächentechnik im Zuge eines Pilotprojekts konzipiert, entwickelt, umgesetzt und validiert.
In der Pilotphase wurde die Abwärme von zwei Härteöfen für die Wärmerückgewinnung genutzt. Dabei passiert die Abwärme der Öfen mit etwa 360 °C einen Rohrbündelwärmetauscher, in dem Wasser erhitzt wird und im nachgeschalteten Dampferzeuger in dampfförmigen Zustand übergeht. Der rund 130 °C heiße Wasserdampf versorgt die Heizregister der Teilereinigungsanlage. Die komplette Anlage, von der Verrohrung über die Auslegung und den Eigenbau eines hocheffizienten Rohrbündelwärmetauschers bis hin zur Software, wurde in Zusammenarbeit mit EMO Oberflächentechnik in Eigenregie entwickelt und gebaut.
Die technischen Herausforderungen waren vielfältig. So musste aus Gründen der Prozesssicherheit die ursprüngliche Idee, die Abwärme direkt an der Ofenflamme abzugreifen, verworfen werden und der Wärmetauscher musste schließlich dezentral anlegt werden. Um eine Explosions- beziehungsweise Brandgefahr auszuschließen, musste sichergestellt werden, dass Wasser unter keinen Umständen zurück in einen der Öfen gelangen kann, selbst für den Fall, dass der Wärmetauscher Undichtigkeiten aufweisen sollte.
Aus dem gleichen Grund musste ebenfalls verhindert werden, dass brennbare Gase aus den Öfen in das Rohrleitungssystem der Wärmerückgewinnung gelangen können. Zudem durfte das neue System zur Wärmegewinnung keinen negativen Einfluss auf die regulären Produktionsprozesse haben oder Wartungsarbeiten behindern.

Mit der in Eigenregie entwickelten und in den regulären Betrieb überführten Pilotanlage zur lösemittelbasierten Teilereinigung mit Wärmerückgewinnung können Einsparungen in Höhe von über 150 MWh/Jahr an elektrischem Strom erzielt werden.
Nachdem bereits zwei der derzeit neun Härteöfen in das neue System der Wärmerückgewinnung eingebunden sind, wird in einem nächsten Schritt ein dritter Ofen integriert. Diese Maßnahme geht mit einer zusätzlichen jährlichen Stromeinsparung von weiteren 80 MWh einher.
In einem weiteren Schritt werden neben den Sicherheitsflammen der drei Öfen auch die Abgase der jeweils sechs Gasbrenner pro Ofen an das System zur Wärmerückgewinnung angebunden und so weitere Stromeinsparungen von 30 MWh/Jahr realisiert werden können.
Der vorläufig letzte Schritt wird die Duplizierung des Wärmerückgewinnungssystems an weiteren Reinigungsanlagen und Öfen sein.
Insgesamt soll damit eine Stromeinsparung von rund 966 MWh/Jahr erreicht werden. Das entspricht einer jährlichen CO2-Einsparung von 273,4 t.
Die bei IMS Gear im Regelbetrieb eingesetzte Sonderanlage zeigt, dass die Idee, Abwärme aus Härteöfen zum Beheizen von Teilereinigungsanlagen nicht nur technisch umsetzbar ist, sondern sich auch unter Nachhaltigkeits- und Effizienzaspekten rechnet.
IMS Gear begann 1863 als feinwerktechnischer Zulieferer und ist heute eines der führenden Unternehmen im Bereich der Zahnrad- und Getriebetechnik. Mit seinen technischen Lösungen für Komponenten, Baugruppen und Getriebe ist es eine feste Größe im Automobilsektor. Tiefes Entwicklungs-Know-how, eine große Fertigungsbreite, Prozesskompetenz und Internationalisierung sind wesentliche Faktoren des Erfolgs. Das Unternehmen produziert kundennah an Standorten in Deutschland, den USA, Mexiko sowie China und beschäftigt weltweit rund 3.000 Mitarbeiterinnen und Mitarbeiter. In der Härterei werden über 6.000 verschiedene Bauteile, vor allem für die Bereiche Automobil- und Maschinenbau bearbeitet. Langjährige Erfahrung und metallografisches Spezialwissen kombiniert mit fortschrittlichen Verfahrenstechniken machen IMS Gear zu einer der modernsten Härtereien weltweit.
- Großserienfertigung
- Unterstützungsprozesse / Gebäudemanagement
- Energiekonzept ,
- Stoffkreislauf / Recycling
- Energie ,
- Abgas
- taktisch (1 bis 5 Jahre)