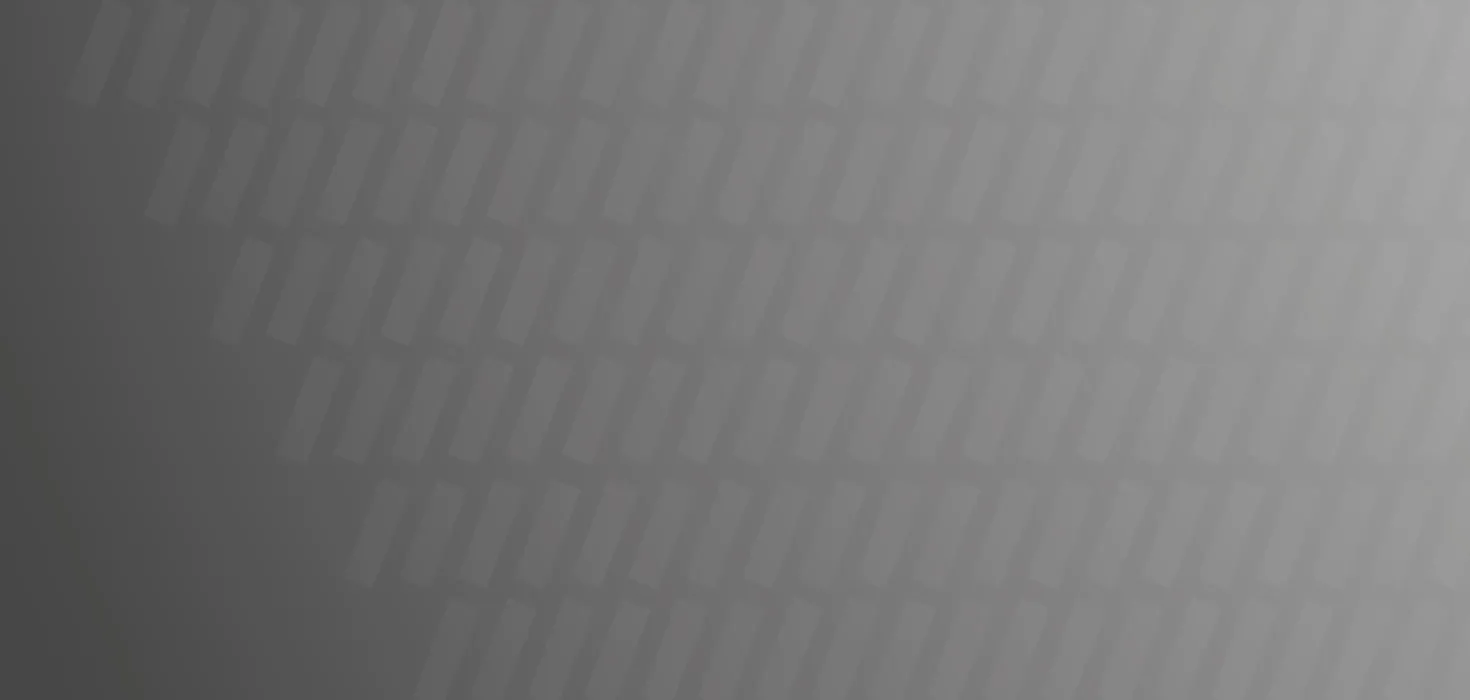
Innovative Trockenabscheidung für Spritzlacke
Einsatz eines neuen Abscheideverfahrens in der Lackverarbeitung
Energieeinsparung (elektrisch)
Erdgaseinsparung
CO2-Einsparung
Wassereinsparung
Sondermüllvermeidung
Die Daimler AG produziert am Standort Gaggenau vor allem Getriebe, Blechumformteile und Nutzfahrzeug-Achsen. Das Unternehmen hat eine neue Lackieranlage angeschafft, mit der die produzierten Teile beschichtet werden. Diese Anlage soll dafür sorgen, dass zukünftige Umweltvorschriften eingehalten werden können und Lackabfälle reduziert werden können.
Am Standort Gaggenau fertigt die Daimler AG u. a. Getriebe und Achsen für Nutzfahrzeuge, überwiegend im mittleren bis schweren Geländeeinsatz. Für diesen Einsatz sind hohe Korrosionsschutzanforderungen notwendig, um die Aggregate für die gesamte Lebensdauer zu schützen. Den wichtigsten Bestandteil zur Erfüllung dieser Anforderungen stellt die Beschichtung dar. Um diese Anforderungen auch in Zukunft nachhaltig erfüllen zu können und um aktuelle und zukünftige Umweltvorschriften einzuhalten, wurde eine Ersatzbeschaffung der Lackieranlage erforderlich.
In dieser Lackieranlage werden unterschiedlichste Bauteile beschichtet, die von kleinen Getrieben bis zu großen Achsen reichen und in Serien- und Sondereinsätzen von Lkws sowie in Unimogs verwendet werden. Aufgrund der unterschiedlichen Bauteilgeometrien ist ein manueller Lackierprozess notwendig. Zusätzlich wird ein großer Anteil an Bauteilen bereits nach Kundenwusch lackiert. Die Aggregate werden dabei bereits in dem Farbton bzw. mit dem Lack beschichtet, den der Endkunde wünscht. Hierzu sind Lösemittellacke erforderlich.
Die neue Anlage sollte nicht nur dem aktuellen Stand der Technik entsprechen, sondern nach Möglichkeit auch noch neue, innovative Technologien zum Einsatz bringen.
Im Rahmen des Beschaffungsvorgangs wurden verschiedene alternative Abscheideverfahren betrachtet. In den Fokus rückten Trockenabscheideverfahren, da sich durch diese die genannten Ziele realisieren lassen.
Zusammen mit dem Anlagenhersteller wurden die Verfahren der Trockenabscheidung beurteilt. Für die Kombination von manuellem Lackierverfahren und vieler unterschiedlicher Lacke eignen sich jedoch wirtschaftlich nur sehr wenige Verfahren.
Als Favorit stellte sich das vom Anlagenlieferanten vorgestellte und entwickelte Verfahren heraus. Bei diesem Verfahren wird der Luftstrom, welcher am Aggregat vorbeigeführt wird und das Overspray aufnimmt, auf ein Abscheidesystem zugeführt. Dieses besteht aus versetzt angeordneten Kunststoff-Halbschalen, an denen der Luftstrom mehrfach umgelenkt wird. Durch die Trägheit der Lackpartikel schlagen sich diese auf den Kunststofflamellen nieder. Nach Trocknung des Lacks können diese Lamellen ausgebaut und in einer eigens konzipierten Bürstmaschine gereinigt werden. Der entstehende Lackstaub wird gesammelt und kann mit dem Hausmüll entsorgt werden. Die Lamellen werden nach der Reinigung wieder eingebaut und können somit mehrfach verwendet werden. Hinter diesen Lamellen befindet sich ein Vliesfilter, welcher in einem festgelegten Zyklus getauscht werden muss. Weitere Zusatz- oder Hilfsstoffe werden nicht benötigt.
Da sich die Technologie noch im Versuchsstadium befand und noch keine Erfahrungen in einem Serieneinsatz vorlagen, musste sie vor der Umsetzung in der neuen Anlage unter realen Bedingungen getestet werden. Hierfür wurde ein bestehender Handspritzstand in einer Lackieranlage für andere Aggregate zu Testzwecken mit dem bevorzugten physikalischen Abscheideverfahren ausgestattet. Nach mehreren Wochen im Serieneinsatz unter Realbedingungen wurden die Ergebnisse von der Projektgruppe unter der Leitung der Produktionsplanung und der Mitwirkung von Produktion, Instandhaltung, Umweltschutz und Technischem Service gemeinsam mit dem Lieferanten bilanziert. Hierbei wurden die gesetzten Ziele zum Teil noch übertroffen, so dass die Entscheidung zu Gunsten der neuen Technologie getroffen wurde. Im Rahmen der Anlagenbeschaffung wurde die neue Technologie berücksichtigt und umgesetzt.
Bei den jährlich zu lackierenden Aggregaten (Nfz-Achsen, Getriebe) können im Vergleich zur Nassabscheidung ca. 18 MWh elektrische Energie und ca. 60.000 m³ Erdgas pro Jahr eingespart werden. Dies entspricht ca. 160 t CO2 pro Jahr.
Durch die Vermeidung von Wasser in der Anlage (4.000 l/Jahr) entsteht kein Lackschlamm, wodurch Sondermüll in der Höhe von 9 t/Jahr vermieden werden kann. Stattdessen muss nur noch der trockene, abgebürstete Lack entsorgt werden, der als Hausmüll gilt. Daneben sind Tanks, Leitungen und Pumpen obsolet, womit das Risiko von Leckagen entfällt.
Zudem ist eine aufwendige Abwasserbehandlung nicht mehr notwendig. Durch die Reduzierung von Lärm- und Aerosolbelastungen kommt es zu einer weiteren Optimierung der Arbeitsbedingungen.
Erreichen die Kunststofflamellen die Verschleißgrenze, können sie vollständig recycelt und bei der Herstellung neuer Lamellen wiederverwendet werden.
In der Zusammenarbeit der interdisziplinären Arbeitsgruppe gemeinsam mit dem Anlagenhersteller der neuen Lackieranlage wurde in der Konzeptphase ein Screening der möglichen Verfahren zur Lackabscheidung durchgeführt. Für die angestrebte Technologie der Trockenabscheidung gab es allerdings einige Risiken. Zum einen wurde diese noch nie in einer Serienanlage einer solchen Größe eingesetzt. Zum anderen sind eine Ausrüstung der Lackieranlage mit einer Nassauswaschung und eine spätere Umrüstung auf Trockenabscheidung aufgrund der komplexen Technik bzw. der deutlich höheren Investitionskosten nicht wirtschaftlich. Durch eine konsequente Chancen-Risiken-Abschätzung und insbesondere durch den Test der Technik in einer bestehenden Anlage konnte die Anwendbarkeit nachgewiesen werden.
Die Anlage ist mit der neuen Technik seit etwa sechs Monaten im Einsatz und hat sich bis heute bewährt. Die ausgewiesenen Einsparungen konnten nahezu vollständig nachgewiesen werden, während die Kosten der Beschaffung der Anlage im Gegensatz zur konventionellen Abscheidetechnik niedriger sind.
Die Daimler AG produziert an ihrem Standort in Gaggenau Getriebe, Wandler für Automatikgetriebe, Blechumformteile und Nutzfahrzeug-Achsen. Mit seinen rund 6.500 Mitarbeiterinnen und Mitarbeitern stellt das Werk Gaggenau damit einen der wichtigsten Produktionsstandorte für Aggregate und Komponenten im Daimler-Konzern dar. Die gefertigten Produkte sind weltweit in Pkws und Lkws im Einsatz.
Das Werk wurde 1894 gegründet und ist damit das älteste Automobilwerk der Welt. Nachdem von Beginn an Nutzfahrzeuge wie Lkws und Unimogs produziert wurden, begann in den 1970er Jahren die Produktion von Aggregaten. Nach der sukzessiven Verlagerung der Fahrzeugumfänge ins Werk nach Wörth ist Gaggenau seit Anfang des neuen Jahrtausends ein reines Aggregate-Werk. Das Werk Gaggenau mit seinen vier verschiedenen Werkteilen steht für unzählige Komponenten, technische Zuverlässigkeit, fachliche Kompetenz, höchste Qualität und innovative Technologien.

- Großserienfertigung
- Unterstützungsprozesse / Gebäudemanagement
- Prozessinnovation
- Energie ,
- Material ,
- Chemieprodukte ,
- Abfälle ,
- Abgas
- taktisch (1 bis 5 Jahre)