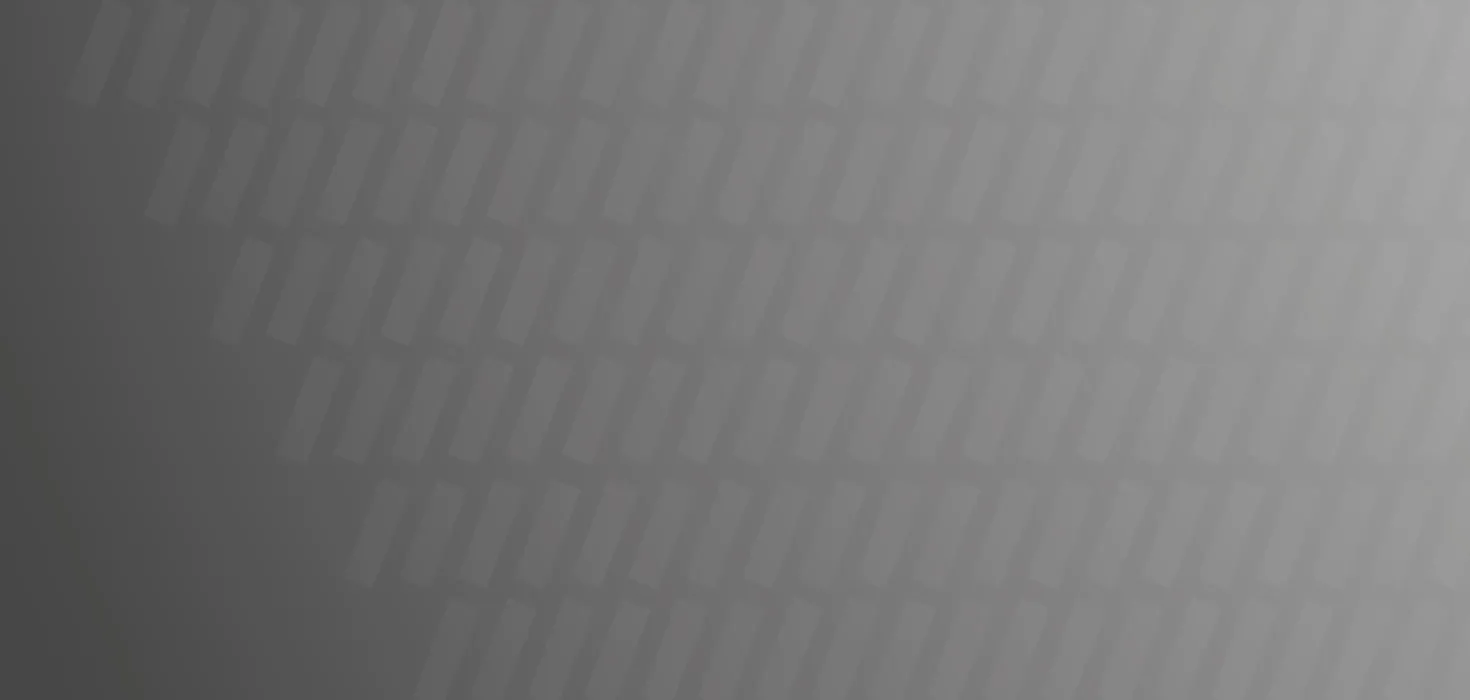
MIA – Material- und Informationsflussanalyse
Durchführung einer unternehmensweiten Material- und Informationsflussanalyse
Reduktion des ungenutzten Stangenmaterials
Rohmaterialeinsparung
Energieeinsparung (elektrisch)
Grieshaber ist auf die Produktion von Präzisionsteilen aus Nichteisenmetallen und rostfreiem Stahl spezialisiert. Um Potenziale zur Steigerung der Ressourceneffizienz aufzudecken, führte das Unternehmen eine Analyse des Material- und Informationsflusses durch. Darauf basierend wurden viele Optimierungen durchgeführt, die zu einer höheren Ressourceneffizienz und großen Kosteneinsparungen führten.
Kostenvorteile
- 62.000 Euro/Jahr durch die Reduktion des ungenutzten Stangenmaterials
- 270.000 Euro/Jahr durch Rohmaterialeinsparung
- 15.000 Euro/Jahr durch Packmitteleinsparung
- 30.000 Euro/Jahr durch Energieeinsparung (elektrisch)
- 30.000 Euro/Jahr durch die Systematisierung der Werkzeuglagerung, der Werkzeugausgabe und des Werkzeugstandmanagements
Die Kernkompetenz der mittelständischen Grieshaber GmbH & Co. KG sind spanend hergestellte Präzisionsteile aus Nichteisenmetallen und rostfreien Stählen.
Der Schwerpunkt liegt hierbei auf der Verarbeitung von Aluminiumlegierungen in mittlerer und großer Serie sowie im Kleinserienbereich bei den rostfreien Stählen. Bei der Herstellung von Präzisionsteilen sind eine fehlerfreie Qualität und die zuverlässige Erfüllung von Kundenanforderungen unabdingbar. Es ist daher notwendig, die eigenen Prozessabläufe fortlaufend zu analysieren und zu optimieren. In langjährig gewachsenen Prozessen entstehen oftmals Material- und Ressourcenverluste, die als gegeben hingenommen werden und deren Kosten inklusive verlorengegangener Wertschöpfung nicht bekannt sind respektive nicht untersucht werden. Um Potenziale zur Steigerung der Ressourceneffizienz aufzudecken, führte Grieshaber daher eine Analyse des Material- und Informationsflusses durch. Die Ziele waren dabei die Schaffung von Transparenz innerhalb des Material- und Informationsflusses, die Abstimmung des ERP-Systems mit den betrieblichen Material- und Informationsflüssen, eine Prozessgestaltung auf Basis von Material- und Informationsflüssen sowie die Reduktion von Missverständnissen und Reibungspunkten in der Organisation und letztlich eine Leistungssteigerung durch Innovationskraft und Kosteneinsparungen durch Effizienzverbesserungen.
Von einem bereichsübergreifenden Team sollte eine mehrstufige Analyse des Material- und Informationsflusses durchgeführt werden. Als Projektteam wurden alle Abteilungsleiter und die Geschäftsführung ausgewählt. Durch die gemeinsame Analyse sollten die verschiedenen Sichten auf die Material- und Informationsflüsse in einem Bild zusammen gebracht und gleichzeitig Optimierungspotenziale erarbeitet werden. Die Beteiligung der gesamten Führungsebene wurde zum einen als Teamentwicklungsprozess angesetzt, zum anderen sollte dies zu einer verbindlichen Umsetzung der erarbeiteten Möglichkeiten für Kostensenkungen, Umweltentlastungen und Leistungssteigerungen sorgen.
Zu Beginn des Projekts wurde das bereichsübergreifende Team aus Abteilungsleitern und der Geschäftsführung gebildet, das die Materialflüsse visualisierte. Daraus ergaben sich erste Ansatzpunkte zur Verringerung der Materialverluste sowie Effizienzpotenziale entlang der Logistikkette. Analog wurden wesentliche Informationsflüsse prozessbezogen visualisiert, um Prozess, Organisation und Kommunikation gemeinschaftlich neu zu bewerten und entsprechend zu gestalten. Das Projektteam kombinierte die verschiedenen Sichten auf Material- und Informationsflüsse und erarbeitete gemeinschaftlich Verbesserungsaktivitäten auf allen Ebenen. Parallel hierzu fand ein Teamentwicklungsprozess statt, der den Weg zu einer gelebten Kooperations- und Kommunikationskultur im gesamten Unternehmen ermöglichte.
Im Bereich der Materialflüsse erfolgte eine besondere Unterscheidung von Flüssen des Produktionsmaterials, von Werkzeugen und von Packmitteln. Die Informationsflüsse werden entsprechend der betrieblichen Prozesse visualisiert, wobei eine weitere Unterscheidung in Wiederholteile und Neuanläufe getroffen wurde.
Anhand der Ergebnisse wurden verschiedene Maßnahmen identifiziert und umgesetzt. So wurde die Ausnutzung des Stangenmaterials im Rohwarenbereich weiter optimiert, um die bisher als technisch gegeben gesehenen Materialverluste zu vermeiden. Hierfür wurden die Stückzahl pro Stange bzw. pro Stangenladung sowie eindeutige Vorgaben der Abstich- und Ablängewerte als Grundlage für das Einrichten und Betreiben der Maschine definiert. Außerdem wurde das Ladesystem bzw. der Werkstoffanschlag optimiert.
Die Material- und Informationsflussanalyse deckte auch ungeplante Stillstandszeiten auf. Während der Stillstandzeiten, die oft mehrere Stunden oder ganze Schichten umfassten, liefen die Maschinen zur Beibehaltung der Betriebstemperatur mit vollem Bewegungsablauf, d. h. mit Ölversorgung, Kühlung und bei ca. 70 % Leistungsaufnahme, ohne zu produzieren. Rein durch organisatorische Maßnahmen, z. B. in der Logistik, im Rüstablauf und im Auftragsdurchlauf, konnten ein Drittel der Stillstandzeiten reduziert werden.
Durch die Implementierung einer automatischen Filteranlage ist es gelungen, die Standzeit des Schneidöls zu erhöhen, wodurch 3 % der Entsorgungs- sowie Materialkosten reduziert werden und der Ressourcenverbrauch im Verhältnis zur Ausbringungsmenge sinkt.
Mittels Abwärmenutzung von Maschinen und Kompressoren wurde es möglich, die Heizkosten und den Verbrauch von Heizöl und Gas zu senken.
Ein großes Optimierungspotenzial bildete die Reduktion von ungeplantem Ausschuss, beispielsweise in den folgenden Bereichen:
- Werkzeugmanagement
- Materialeingangsprüfungen und Werkszeugnisse zur Materialbeschaffenheit
- Erhöhung der Mitarbeiterkompetenz im Umgang mit Material für Produkt und Werkzeug
- Auslaufmanagement für Produkte
Im Zuge dieser Maßnahmen wurde bspw. die Teilezählung am Ausgabenkanal und unmittelbar vor dem Gutteilebehälter an der Maschine mittels geeigneter Sensorik verbessert. In Kombination mit der jeweiligen Sollstückzahlvorgabe kann nun frühzeitig möglicher Schwund festgestellt werden und geeignete Gegenmaßnahmen eingeleitet werden. Für Ausschussteile wurde eine einfache Zählmöglichkeit geschaffen. Mit artikelspezifischen Messbechern können gerade bei Kleinteilen die Ausschussmengen genauer erfasst werden. In der Folge können bei Überschreitung der maximalen Vorgabe frühzeitig Gegenmaßnahmen eingeleitet werden.
Ebenso wurden die Werkzeuglagerung, die Werkzeugausgabe und das Werkzeugstandmanagement systematisiert, um einerseits eine längere Nutzungsdauer zu erreichen und andererseits Verlust, Schwund, geringen Bestand, Verwechslungen sowie Ersatznutzung von ähnlichen Werkzeugen zu vermeiden.
Durch die Optimierung der Stangenausnutzung konnte der jährliche Anteil des ungenutzten Stangenmaterials um 0,5 % reduziert werden. Dies entspricht 62.000 Euro des reinen Materialeinkaufswerts.
Im Rahmen des Projekts konnten rund 60 t pro Jahr Rohmaterial eingespart werden, die einen Wert von 270.000 Euro haben. Darüber hinaus können Packmittel mit einem Wert von 15.000 Euro eingespart werden. Außerdem werden 216,2 MWh weniger elektrische Energie verbraucht, wodurch etwa 30.000 Euro jährlich eingespart werden können. Die Systematisierung der Werkzeuglagerung, der Werkzeugausgabe und des Werkzeugstandmanagements sparen jährlich 30.000 Euro ein.
Flussmanagement kann als einmaliges Projekt zur Effizienzsteigerung genutzt werden. Seine eigentliche Leistungsfähigkeit entfaltet der Ansatz aber erst, wenn es als dauerhaftes Managementsystem eingeführt wird. Das nachhaltige Einführen und Ausrichten der Unternehmensstruktur und der Prozesse entlang der Material- und Informationsflüsse steigert einerseits die Ressourceneffizienz und reduziert andererseits Umweltbelastungen dauerhaft.
Die Umsetzung der Projektergebnisse wird durch eine hohe Motivation der beteiligten Mitarbeiter gesichert. Diese wird durch die Möglichkeiten der Mitgestaltung der eigenen Arbeitsabläufe im Rahmen des Flussmanagement-Projekts gefördert. Mittels der Durchführung einer Kampagne zur Visualisierung von Materialverbrauchskennzahlen und deren persönlicher Zuordnung zu kleinen Produktionsbereichen konnte ein Verantwortungsgefühl in der Breite unter den Mitarbeitern geschaffen werden.
Grieshaber wurde 1903 als Handwerksbetrieb gegründet. Heute produziert das Unternehmen mit 285 Mitarbeiterinnen und Mitarbeitern auf über 10.000 m² Fertigungsfläche in dem Werk in Schiltach jährlich über 100 Mio. Präzisionsteile aus Nichteisenmetallen und rostfreiem Stahl mit höchsten Qualitätsanforderungen. Die Qualität und hundertprozentige Zuverlässigkeit sind die Garanten des Unternehmenserfolgs. Zu den Kunden zählen namhafte, weltweit operierende Firmen aus der Kfz-Zulieferindustrie, der Mess- und Regeltechnik sowie der Klima-, Haus- und Gerätetechnik. Darüber hinaus ist Grieshaber ein kompetenter Partner, wenn es um individuelle Problemlösungen bzw. Mitentwicklungen neuer Produkte geht.
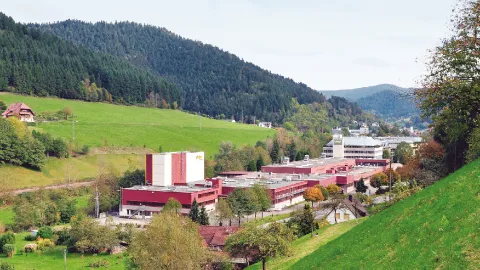
- Großserienfertigung
- Produktionsplanung / -steuerung ,
- Produktionslogistik
- Prozessinnovation ,
- Wertstromanalyse
- Energie ,
- Material ,
- Metalle ,
- Abgas
- operativ (kleiner 1 Jahr)