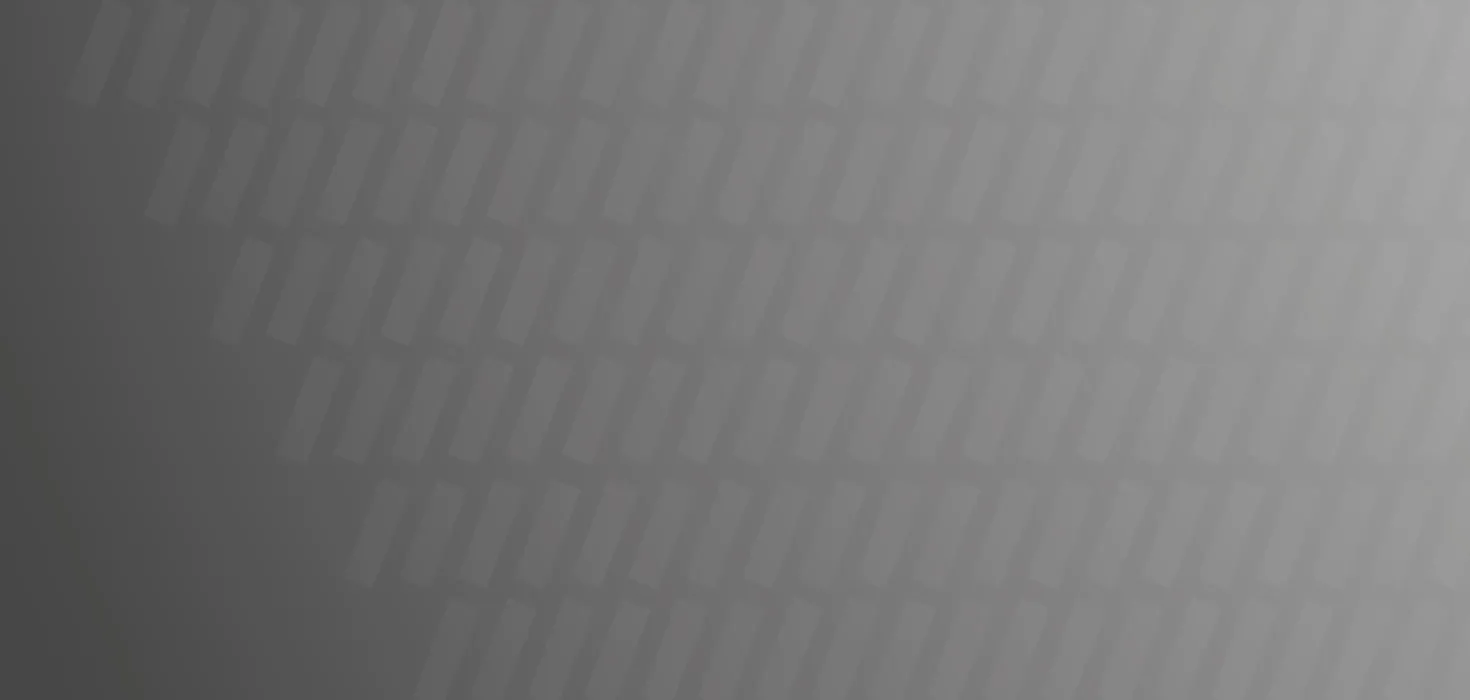
Nachhaltige Investition in Shuttle-Technologie
Shuttle-Lager und weitere Maßnahmen zur Reduktion von Energie- und Materialeinsatz in der Logistik
Reklamationsquotensenkung (intern)
Reklamationsquotensenkung (extern)
Reduktion der Durchlaufzeit
Die Unternehmensgruppe fischer hat einen zentralen Auslieferstandort in Waldachtal, den sogenannten Global Distribution Center (GDC). An diesem Standort wurde ein Shuttle-Lager eingerichtet. Dieses Lager wurde speziell auf die Bedürfnisse des Unternehmens zugeschnitten. Auch weitere Maßnehmen, die zur Reduktion des Energie- und Materialeinsatzes in der Logistik geführt haben, wurden eingerichtet.
Schon Ende der 1970er Jahre hatte sich die Unternehmensgruppe fischer entschieden, mit dem Global Distribution Center (GDC) einen zentralen Auslieferstandort in Waldachtal zu errichten. Das GDC dient als Nachschublager für alle fischer Landesgesellschaften und Importeure in über 100 Ländern sowie als Auslieferungslager für Kunden in Deutschland und Frankreich. Seit seiner Gründung haben sich die Anforderungen an das GDC stetig verändert. So lässt sich bei den Kundenaufträgen ein Trend hin zu kleineren Losgrößen und variablerem Orderverhalten erkennen. Die höhere Frequenz in der Logistik erfordert ein hohes Maß an Agilität, um alle Kundenwünsche in entsprechender Qualität und Zeit erfüllen zu können.
Die bisherige Strategie bei der Kommissionierung „Person-zur-Ware“ erwies sich bei mittlerweile über 10.000 Artikeln im Sortiment zunehmend als limitierend. Der hohe Wegeanteil, ergonomische Einschränkungen und die begrenzte Fördertechnik führten zu einer geringeren Wertschöpfung. Um das Logistikzentrum für den Umschlag der Befestigungssysteme auf zukünftige Herausforderungen auszurichten, sollte ein hochleistungsfähiges Shuttle-Lager mit einer für das Unternehmen neuen Kommissionierstrategie „Ware-zur-Person“ installiert werden.
Ziel war es, die Wegezeiten in der Kommissionierung und den Aufwand in der Vor- und Nachbereitung deutlich zu reduzieren und so die Wertschöpfung signifikant zu erhöhen. Zusätzlich hat sich das Unternehmen in seiner Strategie 2020 das Ziel gesetzt, die Energieeffizienz jährlich (Basisjahr 2012) um 1,5% zu steigern.
Eine zukunftsfähige Logistik, die Faktoren wie kleine Losgrößen, kurze Durchlaufzeiten, ergonomische und somit auch altersgerechte Arbeitsplätze, E-Business, kundenspezifische Lösungen, Zusammenfassung von Transporten sowie Nachhaltigkeit berücksichtigt, kann nur durch ein Paket an Maßnahmen erreicht werden. Die einzelnen Ansatzpunkte wie Transport, Packmittel und Kommissionierung müssen ganzheitlich betrachtet und optimiert werden. Neben dem Shuttle-Lager wurden daher weitere Maßnahmen umgesetzt. Um die Mitarbeiter bestmöglich bei den Neuerungen zu begleiten und wirksame Konzepte für den Veränderungsprozess zu entwickeln, entschied man sich, ein Kooperationsprojekt zum Thema „Change Management“ mit der Hochschule Pforzheim durchzuführen.
Das neue Shuttle-Lager wurde zusammen mit der österreichischen Firma KNAPP speziell auf die Bedürfnisse von fischer angepasst. Bereits in der Konzeption wurde das Zusammenspiel der Systembestandteile simuliert. Das neue Shuttle-Lager sorgt dafür, dass Kommissionierungen jetzt noch effizienter ablaufen.
Rund 75 % aller Lieferscheinpositionen werden über den neuen Lagertyp kommissioniert, der nur 20 % der Fläche in Anspruch nimmt. Die Shuttle-Anlage ist mit einer Energierückgewinnung ausgestattet und die verwendeten Kleinladungsträger (KLT) bestehen aus Recyclingkunststoff, der die Geräuschentwicklung beim Transport der Behälter auf der Fördertechnik im Vergleich zu herkömmlichen Standardbehältern deutlich minimiert. Dadurch hat sich auch die Arbeitsumgebung für die Mitarbeiter verbessert. Die KLT werden möglichst an allen deutschen und einigen europäischen Produktionsstandorten verwendet, um die fertigen Produkte ins GDC zu transportieren. Damit entfällt das Depalettieren im GDC. Wenn bei internen Transporten keine KLT zum Einsatz kommen, nutzt fischer im Bereich der Packmittel eine andere Möglichkeit: Dann werden die Umverpackungen mit einem speziellen Kleber aufeinander befestigt und nicht, wie früher, mit Schrumpffolie umwickelt. Hierdurch spart das Unternehmen große Mengen an Stretchfolie ein, die vor der Einlagerung im GDC ohnehin wieder entfernt werden müsste.
Die Verfahrwege der einzelnen Shuttles werden durch die Anordnung der Artikel gemäß ABC- bzw. XYZ-Analyse optimiert und gering gehalten. Durch die Implementierung von Kontrollpunkten, wie beispielsweise Gewichtskontrollen, werden Fehler minimiert und vermieden. Des Weiteren investierte fischer in ein neues Arbeitsplatzkonzept in der Kommissionierung. Die automatisch aus dem Shuttle-Lager ausgelagerten Behälter werden an Pick-it-Easy-Arbeitsplätzen im „Ware-zur-Person“- Prinzip zur Verfügung gestellt. Die zu befüllenden Versandkartons werden den Kartongrößen entsprechend angehoben – so hat der Kommissionierer optimalen Einblick in den Karton. Der gesamte Arbeitsbereich ist höhenverstellbar und kann auf individuelle körperliche Anforderungen angepasst werden. Displays und LED-Anzeigen unterstützen die Mitarbeiter bei ihrer Tätigkeit. So entsteht ein Arbeitsumfeld, das Ergonomie, Leistung und Qualität vereint.
Das neue System führt zu einer deutlichen Produktivitätssteigerung der Prozesse. Bei gesunkenem Gesamtenergiebedarf wurde der Output um 20 % gesteigert und die Wertschöpfung deutlich erhöht. Auf Grundlage von vorhandenen Daten optimiert die Software das Shuttle-Lager laufend: So werden zum Beispiel Behälter mit häufig benötigten Waren weiter vorne in der Regalgasse eingelagert, um die Fahrwege der Shuttles zu verkürzen. Dadurch ist künftig mit weiteren Effizienzsteigerungen zu rechnen. Die Logistiksoftware schafft somit Transparenz in den Lagerprozessen, verkürzt Transportwege, reduziert den Emissionsausstoß, verringert die Fehlerquote und erhöht die Auslieferqualität. Durch das neue System konnte die interne Reklamationsquote um 13 % und die externe Reklamationsquote um 71 % gesenkt werden, so dass entsprechende Rücktransporte vermieden werden.
Zudem werden durch die neue Art der Kommissionierung die Setzmuster in den Paketen optimiert, wodurch mehr Gewicht pro Volumen transportiert wird. Dies führt bei der meistverwendeten Paketgröße zu einer Steigerung des Gewichts pro Volumen um rund 50 %. Hierdurch werden Transporte und die damit verbundenen Emissionen eingespart. Weiterhin konnte die Durchlaufzeit durch diese Maßnahmen um 69 % reduziert werden. Wollte man die gleiche Menge an Artikeln mit dem früheren Lagersystem kommissionieren, wäre unter Berücksichtigung der notwendigen Verfahrwege und optimalen Bedingungen das Dreifache an Fläche nötig. Schließlich konnte auf der bestehenden Logistikfläche ein ausgegliedertes 3.000 m2 großes Auslieferungslager integriert werden, wobei die entsprechenden Umweltwirkungen aus dem Betrieb dieses Lagers zukünftig entfallen.
Konzeption und Durchführung des Projekts realisierte fischer federführend mit einem Generalunternehmer. So war sichergestellt, dass eine individuelle, auf die Anforderungen von fischer angepasste Lösung umgesetzt wird. Auch dass die Mitarbeiter in die einzelnen Prozessschritte eingebunden waren und im Rahmen des kontinuierlichen Verbesserungsprozesses die Möglichkeit hatten, Bedenken, Kritik und Ideen einzubringen, hat sich bewährt. Hilfreich war außerdem der Besuch eines Unternehmens, das bereits mit einer ähnlichen Shuttle-Anlage arbeitete. Diese konnte vor Ort besichtigt werden und es ergab sich die Gelegenheit, damit zu arbeiten.
Die Unternehmensgruppe fischer mit Sitz in Waldachtal, Nordschwarzwald, hat 2016 mit weltweit rund 4.600 Mitarbeiterinnen und Mitarbeitern einen Umsatz von 755 Mio. Euro erzielt. Das Familienunternehmen ist mit 46 Gesellschaften in 34 Ländern vertreten und exportiert in über 100 Länder. Es umfasst die fünf Unternehmensbereiche fischer Befestigungssysteme, fischer automotive systems, fischertechnik, fischer Consulting und LNT Automation.
fischer Befestigungssysteme besitzt die technologische Marktführerschaft in wichtigen Feldern der Befestigungstechnik. Für ein breites Spektrum an Kunden, vom Heimwerker über den Handwerker bis zum Key-AccountPartner, bietet fischer Produkte in technischer Perfektion. fischer automotive systems fertigt hochwertige Innenraumkomponenten für Fahrzeuge. Das Unternehmen besitzt eine hohe Kompetenz in der Kunststoffverarbeitung und ist ein wichtiger Partner der Automobilindustrie. Das Produktspektrum umfasst Luftausströmer, Getränkehalter, Ablagefächer und Multifunktionskomponenten.
fischertechnik ist mit seinen Konstruktionsbaukästen sowohl im Spielwaren- als auch im Bildungsbereich aktiv. Als einer der letzten Spielwarenanbieter entwickelt und fertigt fischertechnik ausschließlich in Deutschland. fischer Consulting entstand aus den im eigenen Unternehmen entwickelten Kompetenzen. Dort angesiedelt ist das fischer ProzessSystem, dessen zentraler Inhalt die permanente Verbesserung ist. Dabei orientiert sich das fischer ProzessSystem immer am Nutzen für den Kunden. fischer Consulting berät mittelständische Unternehmen, Behörden und Großkonzerne auf dem Weg zu schlanken und effizienten Prozessen. LNT Automation entwickelt und fertigt kundenspezifische Elektroniklösungen.
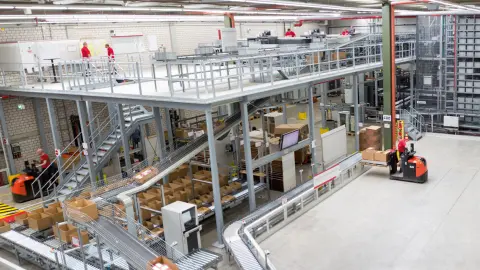
- Großserienfertigung
- Unterstützungsprozesse / Gebäudemanagement
- Prozessinnovation
- Material ,
- Metalle ,
- Chemieprodukte
- operativ (kleiner 1 Jahr)