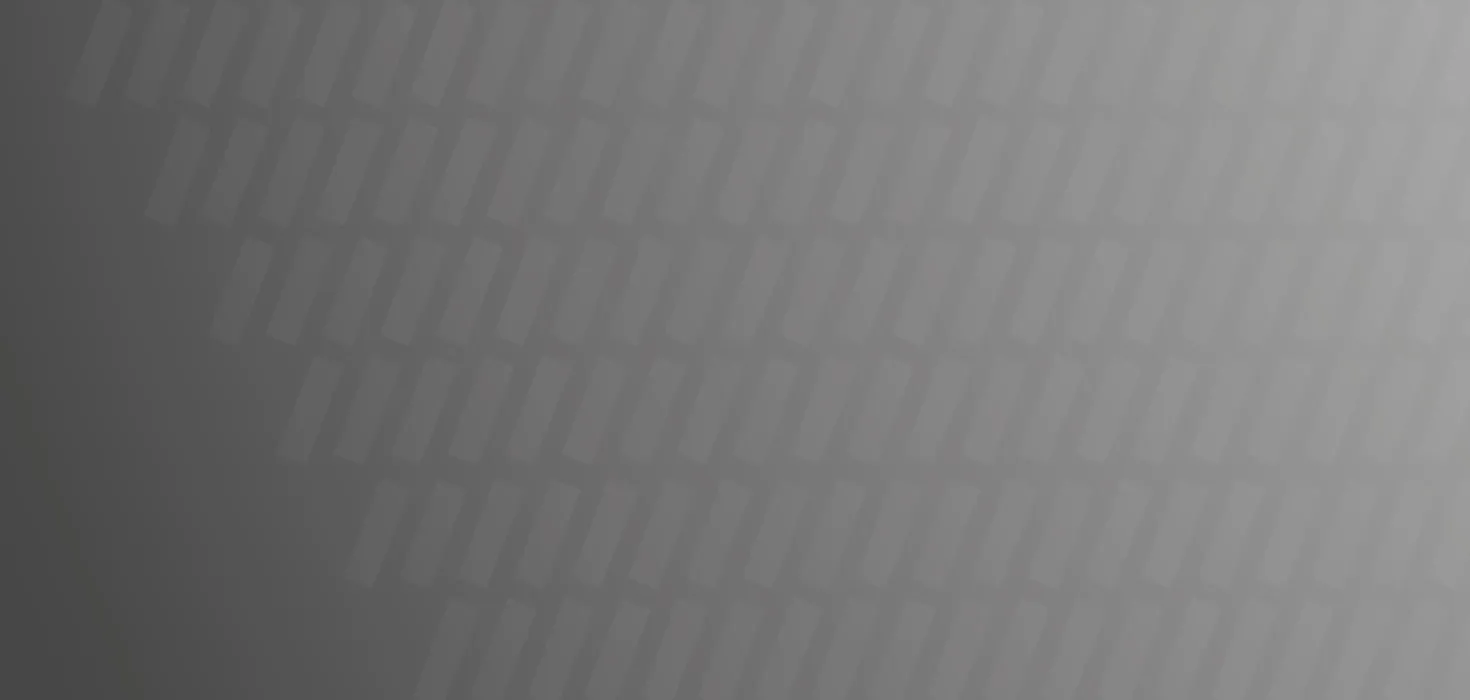
Neue sensorbasierte Steuerung von Spülbäder-Kaskaden in der Lackiertechnik
Automatisierte Überwachung der Qualität von Spülbädern
Wassereinsparung
Die John Deere gilt als Deutschlands größter Landtechnikhersteller. Das Unternehmen hat das Ziel verfolgt, im Bereich der kathodischen Tauchlackierung eine automatisierte Überwachung der Qualität der Spülbäder einzuführen und dadurch dafür zu sorgen, dass diesen nur eine bedarfsgerechte Menge an Frischwasser hinzugefügt wird. Dadurch kann eine erhebliche Menge an Wasser eingespart werden.
Kostenvorteile
Reduktion der Aufbereitungskosten um ca. 30 % durch die Reduzierung des Wasserverbrauchs
John Deere setzte sich im Jahr 2013 das ehrgeizige Ziel, bis zum Jahr 2018 den Energie- und Wasserverbrauch sowie die Emissionen von Treibhausgasen um 15 % zu reduzieren. So entstand am Campus Bruchsal z. B. ein Energiekonzept basierend auf einer eigenen Heizzentrale in Verbindung mit einer Photovoltaikanlage, wodurch der jährliche CO2- Ausstoß um über 7.000 Tonnen reduziert werden konnte. Ein weiterer grundlegender Ansatz zur Erreichung der Ziele war es, sämtliche Produktionsprozesse systematisch zu analysieren und zu optimieren.
So wurde für die Farbgebung Bruchsal ein mehrstufiger Optimierungsplan erstellt und akribisch abgearbeitet. Eine Maßnahme dieses Plans war z. B. die Erarbeitung eines geschlossenen Wassermanagements in der Farbgebung. Dieses gewährleistet durch konsequente Kreislaufführung die vollkommene Abwasserfreiheit des Lackierprozesses. Dazu wird das eingesetzte Prozesswasser mittels einer Vakuumdestillationsanlage vollständig aufbereitet und dem Farbgebungsprozess zurückgeführt. Diese systematischen Optimierungen und konsequente Investitionen in moderne und ressourcenschonende Systeme wurde mit dem Green Award 2014 der Fachzeitung „besser lackieren“ ausgezeichnet.
Im Bereich der kathodischen Tauchlackierung ergab die Prozessanalyse und die Implementierung des Wassermanagements ein erhebliches Einsparpotenzial hinsichtlich des Prozesswassereinsatzes in der Tauchvorbehandlung. Bei der kathodischen Tauchlackierung werden die zu beschichtenden Bauteile oftmals mittels einer Tauchvorbehandlung auf die Lackierung vorbereitet. Klassische Prozessschritte der Vorbehandlung sind hierbei das Entfetten, Beizen und Zinkphosphatieren. Diese Prozessschritte werden auch als Aktivbäder bezeichnet. In den Entfettungsbädern werden Verunreinigungen wie Öle und Fette von den Bauteilen gewaschen, in der Beize werden Oxidschichten entfernt und die Zinkphosphatierung dient als haftvermittelnde Schicht zwischen der Lackierung und dem metallischem Untergrund. Zwischen den Aktivbädern sind Spülzonen integriert. Die Spülzonen sind wässrige Bäder, die die Übertragung chemischer Bestandteile zwischen den einzelnen Aktivbädern verhindern sollen. Den Spülbädern muss im laufenden Betrieb eine ausreichende Menge an Frischwasser zudosiert werden, um eine hinreichende Verdünnung zu garantieren.
Es wurde festgestellt, dass zur Sicherstellung der Wasserqualität, den Spülbädern in der Praxis oftmals eine zu große Menge an Frischwasser kontinuierlich zudosiert wird. Der Grund dafür ist, dass nach dem Stand der Technik für die Wassernachdosierung kein Regelkreis existiert. Stattdessen wird die hinzuzufügende Wassermenge auf Basis der maximalen Anlagenauslastung einmalig eingestellt. Die tatsächlichen Qualitätszustände der Spülbäder werden nicht berücksichtigt, so dass im Spülprozess Wasser verschwendet wird. Das Ziel war es, kontinuierlich den tatsächlichen Qualitätszustand der Spülbäder automatisiert zu überwachen und, basierend auf den zuvor gemessenen Werten, eine bedarfsgerecht dosierte Wassermenge hinzuzufügen. Dadurch sollte erreicht werden, dass in der Vorbehandlung nur so viel Wasser verbraucht wird, wie für den Spülprozess notwendig ist, und dass kein Wasser verschwendet wird.
Die Bestimmung des Qualitätszustandes bzw. des Kontaminationswertes der Spülbäder sollte mittels Leitwertmessung erfolgen. Leitwertsensoren zeichnen sich durch Robustheit und Zuverlässigkeit aus. Gleichzeitig sind sie kostengünstig und nicht wartungsintensiv. Daher finden sie in zahlreichen industriellen Bereichen Anwendung. Ein Beispiel ist u. a. die Erzeugung von voll entsalztem Wasser. Die Daten des Leitwertsensors sollten in einer Steuerung aufbereitet und die Nachdosierung der bedarfsgerechten Frischwassermenge automatisiert ausgeführt werden.
Das Projekt wurde in enger Zusammenarbeit mit der Firma Henkel, dem Chemikalienlieferant im Bereich Tauchvorbehandlung des Werks Bruchsals, realisiert. Es wurde ein interdisziplinäres Projektteam aus Fachleuten der Gebiete Steuerungs- und Regelungstechnik, Chemie und Beschichtungstechnik zusammengestellt. Neben der Projektierung lag der Fokus der Tätigkeiten vor allem auf den projektbegleitenden Qualitätsanalysen der verschiedenen Spülkaskaden. Denn es musste über die gesamte Testphase von mehreren Monaten nachgewiesen werden, dass der Leitwert den tatsächlichen Qualitätszustand der Spülbäder zuverlässig widerspiegelt.

Der Wasserverbrauch wurde durch die Einführung der sensorbasierten Wassernachdosierung um 30 % reduziert. Das Abwasser in der Farbgebung des John Deere Werks Bruchsal wird vollständig mittels Vakuumdestillationstechnologie aufbereitet und der Vorbehandlung wieder zugeführt. Durch die Reduzierung des Wasserverbrauchs reduzierten sich ebenfalls die Aufbereitungskosten um ca. 30 %. Diese gliedern sich primär in Aufwand für elektrische Energie und in Abfallkosten für das anfallende Konzentrat. Die Investitionskosten amortisierten sich dadurch schon im ersten Betriebsjahr.
Während der ersten Testwochen hatte sich auf Basis der kontinuierlichen Leitwertmessung herausgestellt, dass die verschiedenen Spülkaskaden noch weiteres Einsparpotenzial aufwiesen. Durch den Einsatz zusätzlicher Filtertechnik zum kontinuierlichen Partikelaustrag konnte der Wassereinsatz in den Spülkaskaden weiter reduziert werden. Dieser Synergieeffekt konnte nur durch die Umstellung auf die sensorbasierte Steuerung ausgenutzt werden. Ähnliche Erfahrungen konnten ebenfalls bei anderen Optimierungsmaßnahmen gemacht werden. Mit jeder realisierten Veränderung gingen Qualitätsverbesserungen einher. Zudem hatten die Aktionen positive Auswirkungen auf benachbarte Produktionsprozesse. Schließlich konnten durch die ergriffenen Maßnahmen weitere Verbesserungspotenziale offengelegt werden, die nun kontinuierlich gehoben werden können.
Deere & Company ist eine weltweit angesehene Firma, deren Mitarbeiter jeden Tag daran arbeiten, die Grundwerte der Gründer zu wahren. So sind Integrität, Qualität, Engagement und Innovation auch heute noch die gelebten Ideale von Deere & Company. Als Deutschlands größter Landtechnikhersteller beschäftigt die John Deere GmbH & Co. KG rund 7.000 Mitarbeiter an sechs Standorten in der Bundesrepublik. Neben dem Mannheimer Werk, das etwa 60 % der in Deutschland produzierten Traktoren herstellt sowie den Standorten in Zweibrücken (Mähdrescher, Feldhäcksler), Bruchsal (Fahrerkabinen, Europäisches Ersatzteilzentrum, Vertrieb) und Kaiserslautern (Forschung und Entwicklung) verfügt John Deere auch über zwei Standorte in Nordrhein-Westfalen. Dabei handelt es sich um die Fabriken in Gummersbach (Rasenmäher der Marke SABO und John Deere) und Stadtlohn (Erntevorsätze der Marke KEMPER).
- Großserienfertigung
- Unterstützungsprozesse / Gebäudemanagement
- GreenTech BW ,
- Prozessoptimierung ,
- Industrie 4.0 / Digitalisierung
- Energie ,
- Material ,
- Trinkwasser ,
- Abwasser ,
- Abgas
- operativ (kleiner 1 Jahr)