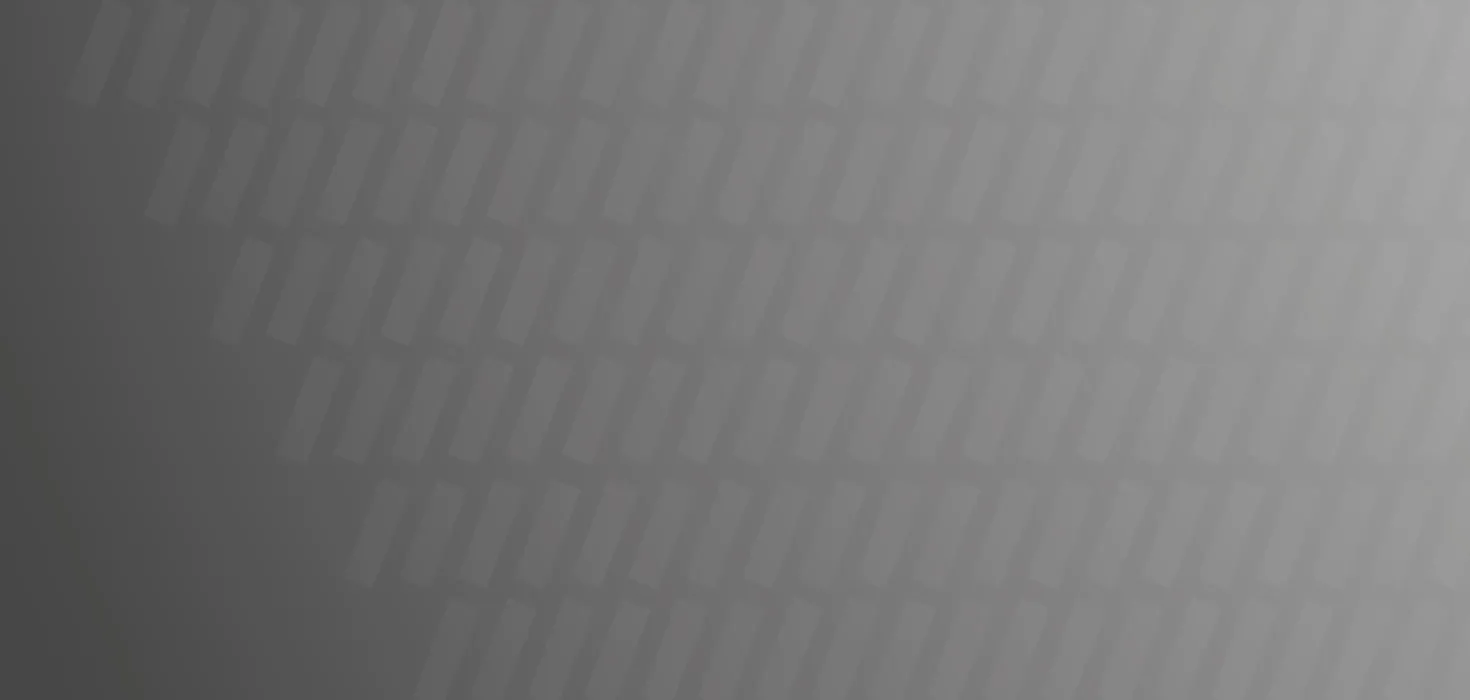
Prozesskette NANOSLIDE®
Gezielte Optimierung eines Prozessschrittes in einem bestehenden Prozess
Energieeinsparung
Die Daimler AG ist der weltweit größte Hersteller von Nutzfahrzeugen. In Zusammenarbeit mit der Heller Maschinenfabrik GmbH hat das Unternehmen NANOSLIDE® entwickelt, wodurch die Motoren deutlich kompakter und leichter gebaut werden können. So kam ein effizientes und wirtschaftliches Fertigungsverfahren zustande, durch das auch der Einsatz von Ressourcen deutlich reduziert wurde.
Die Daimler AG ist Vorreiter auf dem Gebiet der emissionsfreien Antriebe. Sie setzt dabei konsequent auf Effizienzsteigerung durch Hybridisierung und auf die stetige Optimierung von Verbrennungsmotoren. Die konsequente Effizienzsteigerung von Verbrennungsmotoren stellt dabei aktuell den größten Hebel zur Senkung von Verbrauch und Emissionen dar.
Insbesondere die Minimierung von Reibungsverlusten im Antrieb ist eine ebenso effiziente wie wirtschaftliche Möglichkeit zur nachhaltigen CO2-Reduktion. Für den größten Verlustanteil im Motor, nahezu 50 %, ist die Bewegung der Kolben in den Zylindern verantwortlich. Aus diesem Grund fokussiert MercedesBenz seine Entwicklungsarbeiten seit Jahren auf die Entwicklung innovativer Zylinderlaufbahnen in idealer Kombination mit optimierten Kolben und Kolbenringen.
Mit NANOSLIDE® hat die Daimler AG eine neuartige, extrem glatte und verschleißbeständige ultrafeine bis nanokristalline Zylinderlaufbahnbeschichtung auf Eisen-Kohlenstoffbasis für Aluminium-Kurbelgehäuse entwickelt. Der Einsatz von NANOSLIDE® macht die bisher verwendeten schweren eingegossenen Grauguss-Laufbuchsen überflüssig. Die Motoren können dadurch deutlich kompakter und leichter gebaut werden. Darüber hinaus verringert NANOSLIDE® die Reibungsverluste im Kolben-/Zylinderlaufbahnsystem um bis zu 50 %. Allein dies reduziert den Kraftstoffverbrauch bei Pkw mit Otto- und Dieselmotoren um ca. 3 %.
Die fertigungstechnische Basis von NANOSLIDE® beruht auf dem Lichtbogen-Draht-Spritzen (LDS), das von Anfang an auf höchste Ressourcen- und Kosteneffizienz hin entwickelt wurde, und gegenüber allen anderen thermischen Spritzverfahren deutliche Vorteile im Bereich Prozessstabilität, Großserienfähigkeit und Ressourceneinsatz aufweist. Mittels LDS wird dabei eine 0,1 bis 0,15 mm dünne, mikroporöse Gleitschicht auf die zuvor aktivierte Zylinderinnenwand aufgebracht und bei der Endbearbeitung extrem geglättet.
Eine „Aktivierung“ der Zylinderinnenwand vor der eigentlichen Beschichtung ist für die mechanische Verklammerung der aufgespritzten Schicht auf dem Aluminium-Substrat notwendig. Dies erfolgt bei thermischen Spritzverfahren u. a. mittels Hochdruckwasserstrahlen (HDWS). Allerdings ist der Betrieb von HDWSAnlagen mit einem Arbeitsdruck von 3.000 bar zum einen mit hohen Investitionskosten und entsprechendem Raumbedarf verbunden und erfordert andererseits einen verhältnismäßig hohen Energie- und Wasserbedarf. Zusätzlich wird eine relativ aufwendige Technik zur Prozesswasseraufbereitung benötigt.
Für eine breite Industrialisierung der NANOSLIDE®-Technologie als innovatives, wirtschaftliches und ökonomisches Verfahren zur Reduktion von Kraftstoffverbrauch und damit CO2- Emissionen sollte neben weiteren Optimierungsmaßnahmen insbesondere eine ressourceneffiziente Alternative für den Prozessschritt „Aktivieren“ entwickelt und umgesetzt werden.
Für die gute Anbindung der Spritzschicht an das Aluminium-Zylinderkurbelgehäuse sollte als Vorbehandlungsprozess „Aktivieren“ eine speziell entwickelte mechanische Aufrauhung zum Einsatz kommen. Die Aufrauhung sollte Mikro- und Makrostrukturen erzeugen, die eine ideale Schichthaftung ermöglichen. Das Ganze sollte mittels eines, in Bearbeitungszentren integrierbaren innovativen Schneidwerkzeuges umgesetzt werden. Der Fokus lag auf einem platzsparenden, fabrikoptimalen und zukünftig kühlschmiermittelfreien Fertigungsansatz.
Unter Einbindung eines Kooperationspartners, der Gebr. Heller Maschinenfabrik GmbH in Nürtingen, wurden alle Prozessschritte und die Maschinentechnik optimiert. Außer der kontinuierlichen Weiterentwicklung der Gesamtprozesskette NANOSLIDE® wurde verstärkt der Fokus auf den Prozessschritt „Aktivieren“ gelegt und mit dem „Mechanisch Aufrauen“ innerhalb von nur drei Jahren eine Alternative für das HDWS entwickelt.
Seit dem Jahr 2015 wird im Werk Untertürkheim der Daimler AG das „Mechanisch Aufrauen“ für die Aktivierung der Zylinderbohrungsoberflächen vor der eigentlichen Beschichtung eingesetzt. Die Technologie wurde mit dem Start der Serienproduktion des neuen Vier-Zylinder-Diesel-Motors, als erstem Vertreter der neuen Motorenfamilie von Mercedes-Benz, eingeführt.
Unter Berücksichtigung von Fertigungsgegebenheiten lässt sich der mechanische Aufrauprozess nun in serienüblichen Bearbeitungszentren integrieren und findet somit Einzug in verkettete Bearbeitungslinien einer flexiblen Produktion.
Die Gebr. Heller Maschinenfabrik GmbH konnte damit als weltweiter Gesamtanbieter für Turnkey-Fertigungssysteme mit einer extrem ressourceneffizienten Prozesstechnologie ihr Produktportfolio erweitern. Die Gebr. Heller Maschinenfabrik GmbH bietet das Verfahren unter dem Namen CBC (Cylinder Bore Coating) an.
Durch den neuen, innovativen Ansatz für den Prozessschritt „Aktivieren“ wird eine signifikante Einsparung an elektrischer Energie erzielt. So konnte der Verbrauch an elektrischer Energie gegenüber dem HDWS-Verfahren um 96 % reduziert werden. Auf die Ressource Wasser, inklusive der komplizierten Wasseraufbereitung (Trennung von Wasser und Aluminium-Abtrag), kann beim „Mechanisch Aufrauen“ komplett verzichtet werden. Die erzeugten Aluminiumspäne werden rezykliert und dem Gießprozess als Sekundärmaterial wieder zugeführt. So werden allerhöchste Maßstäbe einer umweltgerechten Produktion durch das „Mechanisch Aufrauen“ erfüllt.

Bei der Optimierung war es wichtig die gesamte Fertigungsprozesskette im Auge zu behalten. Änderungen eines Prozessschrittes können sich sowohl auf die Folgeprozesse, als auch auf das eigentliche Produkt auswirken.
Durch die Entwicklungspartnerschaft mit der Gebr. Heller Maschinenfabrik GmbH konnte Hand in Hand eine ideale Lösung für die Prozesskette entwickelt und zeitnah in eine großserienfähige Anlagentechnik überführt werden.
Das Ergebnis zeigt, dass Aufwände und Investitionen in die Entwicklung ressourcenschonender Technologien insbesondere bei einer konsequenten Industrialisierung wirtschaftlich sehr attraktiv und auch in kurzer Zeit amortisiert sind.
Die Daimler AG mit Sitz in Stuttgart ist ein börsennotiertes Unternehmen und gehört zu den größten Anbietern von Premium-Pkw und ist der größte weltweit aufgestellte Nutzfahrzeug-Hersteller. Die Daimler AG bietet Finanzierung, Leasing, Flottenmanagement, Versicherungen und innovative Mobilitätsdienstleistungen an.
Heller wurde im Jahr 1894 in Nürtingen als kleiner Handwerksbetrieb gegründet. Heute entwickelt und produziert die Unternehmensgruppe als einer der führenden Hersteller weltweit modernste Werkzeugmaschinen und komplette Fertigungssysteme für die spanende Bearbeitung. Das Heller Produktprogramm umfasst vier- und fünfachsige Bearbeitungszentren, Fräsdreh-Zentren, Maschinen für die Kurbel- und Nockenwellenbearbeitung, flexible Fertigungssysteme sowie ein modulares Dienstleistungsangebot.
- Großserienfertigung
- Entwicklung / Konstruktion ,
- Verarbeitungsprozess
- Prozessinnovation
- Energie ,
- Material ,
- Trinkwasser ,
- Metalle ,
- Abwasser ,
- Abfälle ,
- Abgas
- taktisch (1 bis 5 Jahre)