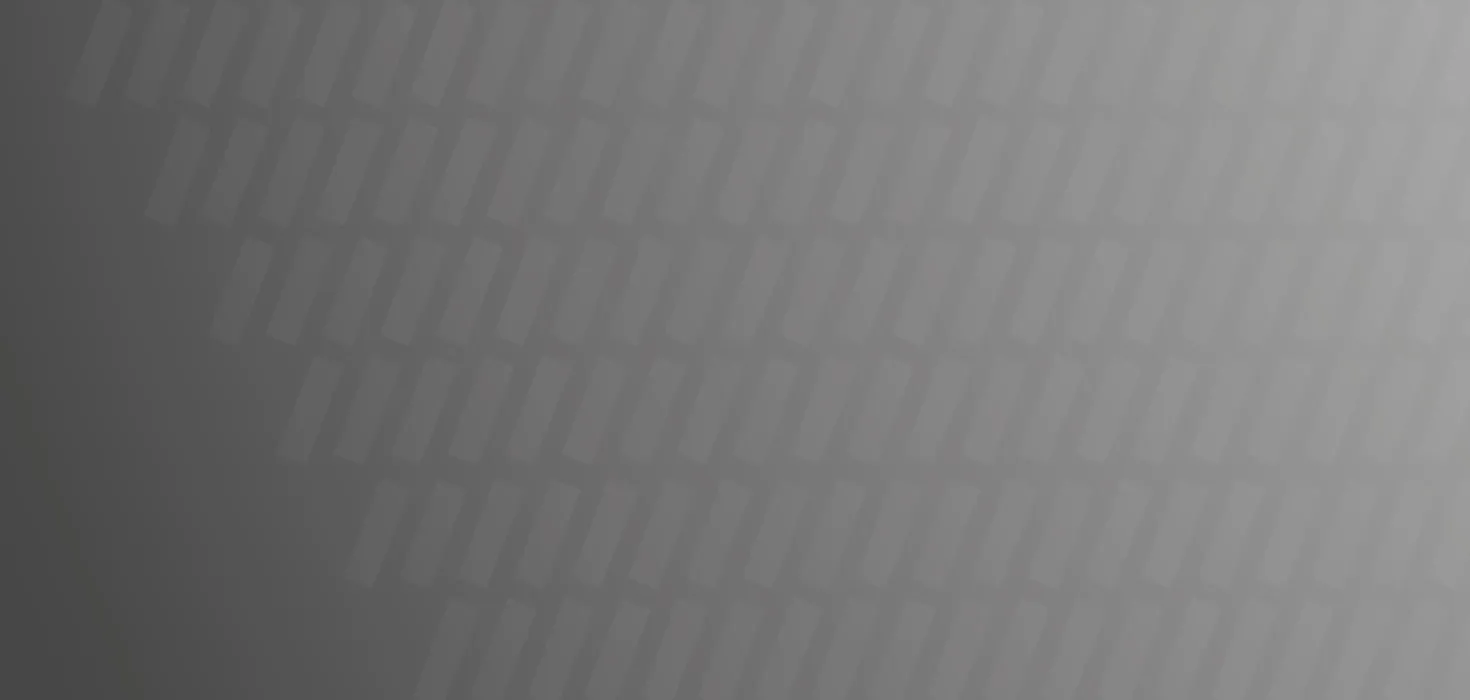
Reduzierung des Hartmetallverbrauchs durch Echtzeitregelung
Verschleißreduzierung des Fräsers bei der zerspanenden Bearbeitung
Werkzeugverschleißreduktion
Hartmetalleinsparung
ulrich medical ist unter anderem auf die Entwicklung und Produktion von Implantaten spezialisiert. Dabei wird der Werkstoff Titan in einem Prozessschritt im Fräser bearbeitet. Dadurch kann ein hoher Werkzeugverschleiß auftreten. Das Ziel war es, die Lebensdauer des Fräsers zu verlängern. Dies gelang durch die Einrichtung einer Vorsimulation und einer anschließenden Regelung des Vorschubs.
ulrich medical ist unter anderem auf die Entwicklung und Herstellung von Implantaten spezialisiert. Die Implantate werden mittels zerspanender Bearbeitung aus dem Werkstoff Titan, andere Bauteile aus diversen nichtrostenden Stählen hergestellt. Dabei unterliegt das Belastungsprofil des Fräsers während der Bearbeitung oftmals Schwankungen und der Verschleiß ist hoch. Folglich mussten die Fräser bislang häufig gewechselt werden. Zudem kam es aufgrund von Fräserbrüchen oft zu Produktionsunterbrechungen. Da die Fräser aus teurem Hartmetall bestehen, ist ein hoher Tauschrhythmus ein beachtlicher Kostenfaktor. Hinzu kommt, dass Hartmetallrückstände in Form von Spänen für die Kreislaufwirtschaft ein großes Problem darstellen. Sie führen zu Hartmetalleinschlüssen im neuen, recycelten Rohmaterial, was wiederum zu erneuten Fräserbrüchen und Hartmetallrückständen führt. Deshalb wurde eine längere Nutzungsdauer der Fräser als Ziel gesetzt. Gleichzeitig sollte die Herstellung pro Implantat nicht länger als bisher dauern.
Während des Landesentscheids von Jugend Forscht im März 2015 in Stuttgart wurde zwischen Schülern und Betreuern des Schülerforschungszentrum Südwürttemberg (SFZ) gemeinsam mit dem Produktionsleiter von ulrich medical eine Idee geboren: Man nimmt mit Industrie 4.0 ein aktuelles Thema, leitet daraus eine konkrete Problemstellung (wie z. B. cyber-physische Systeme) ab und macht daraus ein großes Gesamtprojekt unter der Überschrift: Zerspanung im Zeitalter von Industrie 4.0. In diesem Gesamtprojekt sollten Schüler des SFZ gemeinsam mit Auszubildenden von ulrich medical systematisch nach Lösungen suchen. Im Juni 2015 nahm das Projekt mit fünf Schülern und vier Auszubildenden dann Fahrt auf. Ziel waren die Entwicklung eines cyber-physischen Systems, mit dessen Daten man den Bediener unterstützen kann, und die Teilnahme am Wettbewerb Jugend Forscht 2016.
Die ersten Monate waren ernüchternd. Messaufbauten funktionierten nicht wie geplant, die Aufbereitung der Daten war problematisch und die Maschinen reagierten auf Manipulationsversuche nur sehr verzögert. Erst der von Marc Engelhardt, Lukas Bohnacker und Jannik Münz zum Patent angemeldete Messaufbau brachte den Durchbruch und bildete die Basis für das Jugend Forscht-Projekt sowie die jetzt umgesetzte Maschinenregelung.
Ziel war ab diesem Zeitpunkt die Entwicklung einer Regelung, mit der sich nicht nur schneller, sondern auch qualitativ hochwertiger und dazu mit deutlich geringerem Fräserverschleiß produzieren lässt. Diese sollte mittels eines cyber-physischen Systems erfolgen, welches die Kräfte misst, die während der Bearbeitung auf den Fräser wirken und die Prozessparameter der Werkzeugmaschine dann entsprechend optimal anpasst.
Mit ausführlichen Messreihen und einer mathematischen Simulation gelang es dem Projektteam, die zu erwartenden Kräfte für den Fräser zu ermitteln. Auf Grundlage dieser Daten konnten die jeweils optimalen Werte für den Vorschub definiert werden. Diese werden als Richtwerte an die Maschinenregelung übergeben. Die Maschinenregelung vergleicht permanent die gemessenen Werte mit den mathematisch vorsimulierten Werten für jeden Prozesspunkt und gleicht über einen programmierten PID-Regler (Proportional– Integral–Derivative Controller) den Vorschub insoweit an, dass die definierten Maximalkräfte nie überschritten werden.
Neben ulrich medical und dem Schülerforschungszentrum Südwürttemberg (SFZ) war auch die Dr. Johannes Heidenhain GmbH beteiligt, da die neue Regelung explizit für Bearbeitungszentren mit Heidenhain iTNC 530 und Heidenhain TNC 640-Steuerungen konzipiert wurde.
Es gelang erstmals, ein echtzeitfähiges System zu entwickeln, das ein Bearbeitungszentrum hochdynamisch ausregeln kann. Gemäß dem Industrie 4.0 Grundgedanken erzeugt ein cyber-physisches System eine große Menge an Daten – in diesem Fall Messsignale von Kräften mit einer Frequenz von 1.500 Hz. Ein sehr schnelles Netzwerk überträgt die Daten an einen Zentralrechner. Dieser macht annähernd in Echtzeit Auswertungen und gibt Regelsignale an die Maschinensteuerung zurück. Bei Maschinen mit drei Achsen erfolgt die Datenübertragung mittels Direktverkabelung, bei Maschinen mit fünf Achsen dagegen mittels Funkübertragung, was die Übertragungszeit minimiert. Dem Bediener der Maschine bietet das System überdies nützliche Zusatzinformationen. So wird er über den Verschleißzustand des Werkzeugs sowie über eventuelle Unregelmäßigkeiten im Werkstoff (z. B. Einschlüsse bei Gussteilen) informiert.
Durch die neue, gezielte Vorsimulation des Zerspanungsprozesses mit anschließender Regelung des Vorschubs konnte der Werkzeugverschleiß um über 80 % reduziert werden. Bei einer Prozessfähigkeitsuntersuchung (MFU) der Titanlegierung TiAl6V4 konnten Standzeiten von 20 Stunden Spaneingriffszeit je Zahn erreicht werden, ohne Auswirkungen auf statistische Werte wie Cm und Cmk des Prozesses. Ohne diese Regelung wird mit den gleichen Zerspanparametern nach ein bis zwei Stunden Spaneingriffszeit ein deutlicher Verschleiß sichtbar, der sich auch in den Cm- und Cmk-Werten des Prozesses widerspiegelt.
Zum Verständnis der monetären Bedeutung lässt sich sagen, dass sintermetallurgisches Hartmetall, das primär aus Wolframcarbid und Cobalt besteht, rund 400 Euro/kg kostet. Zudem ist es in der Herstellung sehr energieintensiv. Je nach Einsatzgebiet, Teilespektrum und Rohmaterialart lassen sich je Bearbeitungszentrum bis zu 40 kg Hartmetall pro Jahr einsparen.
Ein weiterer positiver Aspekt ist die bessere Qualität der Bauteiloberfläche. Durch die Ausregelung lässt sich beim repräsentativen Musterteil die durchschnittliche Rauhtiefe Rz trotz des deutlich längeren Einsatzes des Werkzeuges von Rz4 auf Rz3 reduzieren.
Hinzu kommt eine Einsparung bei der Herstellzeit, die allerdings je nach Verschleiß des Fräsers pro Implantat unterschiedlich hoch ausfällt. Beim repräsentativen Musterteil veränderte sich die Herstellzeit trotz längerer Werkzeugstandzeit und besserer Oberflächengüte von 74 auf durchschnittlich 67 Sekunden.
Das Projekt ermöglichte detaillierte Einblicke in die Steuerung und Regelung von Werkzeugmaschinen und vertiefte das Verständnis für Mess-Sensorik. Die anfänglichen Schwierigkeiten bei der Messung der Krafteinwirkung auf den Fräser konnten durch den neuen patentierten Messaufbau erfolgreich behoben werden. Das entwickelte Verfahren wird nun nach und nach an allen Produktionsmaschinen implementiert. Mittelfristig soll das System derart weiterentwickelt werden, dass es von allen zerspanenden Bearbeitungszentren genutzt werden kann. Da das System ohne Kontrollschnitt auskommt, wird es in anderen Branchen wie z. B. dem Formenbau noch zu viel größeren Einsparungen führen.
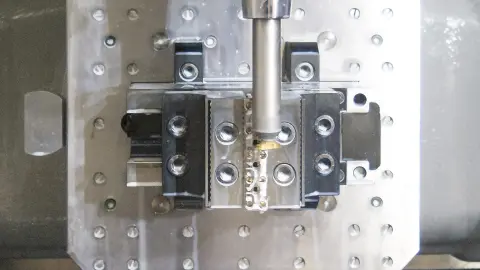
Als international agierendes, mittelständisches Familienunternehmen blickt ulrich medical auf über 100 Jahre erfolgreicher Unternehmensgeschichte zurück. Mit den Produktbereichen Wirbelsäulenimplantate, Kontrastmittelinjektoren sowie Chirurgische Instrumente, Fußchirurgie und Blutsperregeräte bietet der Medizintechnikhersteller ein umfassendes Portfolio innovativer Produkte. Als einer der wenigen in der Branche entwickelt und produziert das Unternehmen in Deutschland und setzt dabei auf modernste Fertigungstechnologien. Am Hauptsitz in Ulm arbeiten über 300 Mitarbeiter. Als inhabergeführtes Unternehmen legt ulrich medical besonderen Wert auf eine langfristige, nachhaltige Unternehmensentwicklung und ist daher stolz auf sein kontinuierliches, gesundes Wachstum.
- Kleinserienfertigung
- Entwicklung / Konstruktion
- Prozessoptimierung
- Material ,
- Metalle
- taktisch (1 bis 5 Jahre)