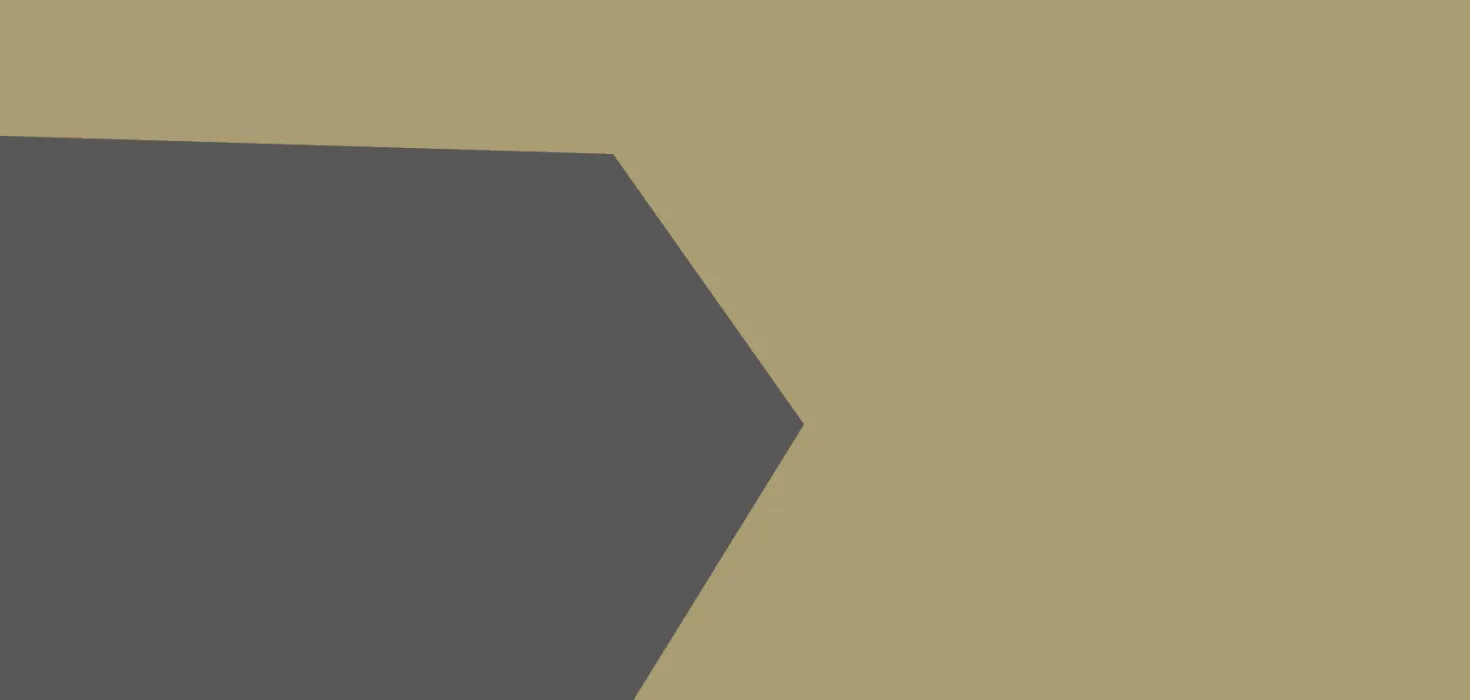
Reduzierung von Material- und Energieeinsatz beim Zylinderschweißen
Ausschussreduktion
Durch Optimierung der Maschinenkonstruktion und der Prozessparameter steigt die technische Fähigkeit eines Zuschnitt- und Schweißprozesses.
Kostenvorteile
Ca. 45.000 EUR/a
Investition
100.000 EUR
Rohrzylinder sind das Ausgangsmaterial zur Herstellung von Metallbälgen, die überwiegend durch einen hydraulischen Umformprozess hergestellt werden. Die Zylinderherstellung erfolgt in Eigenfertigung aus Bandstahl durch Runden und Verschweißen. Dabei muss die Schweißnaht bezüglich ihrer geometrischen und metallurgischen Ausprägung so beschaffen sein, dass sie sowohl statische als auch dynamische Lasten in gleicher Weise wie der Grundwerkstoff ertragen kann. Die größte statische Belastung tritt in der Regel durch hohe Drücke während der Balgumformung auf. Eine Längsnaht mit zu geringer statischer Festigkeit versagt in diesem Verfahrensschritt und führt zu Ausschuss. Dynamische Lasten werden im Betrieb des Balges durch wiederkehrende Bewegungen, Schwingungen und/oder Druckschwankungen hervorgerufen. Dabei werden produkt- und lastabhängig Lastspielzahlen zwischen wenigen 1.000 bis zu mehreren 100 Milliarden Zyklen gefordert. Längsnähte mit unzureichender Ermüdungsfestigkeit würden zu vorzeitigen Ausfällen im Einsatz führen.
Bei der bisherigen Fertigung wurden Zylinder aus Edelstahl und Nickelbasislegierungen mit dünner Wandstärke (0,2 mm bis 0,25 mm) auf handelsüblichen Zylinderschweißmaschinen gefertigt, die nach Herstellerangaben auf Wandstärken größer 0,5 Millimeter ausgelegt sind. Bei Verwendung von dünnerem Material als vorgesehen ist die Schweißnahtqualität unzureichend. Durch zu geringe Stabilität der Schweißnaht kann es bei späteren Prozessen zu Ausschuss oder bei Verwendung der Fertigprodukte zu vorzeitigen Ausfällen im Einsatz kommen. Der Ausschussanteil betrug in der Praxis 12,5 Prozent.
Durch technische Optimierungen sollte das Verfahren so modifiziert werden, dass auch für dünne Wandstärken ein robuster und stabiler Prozess sichergestellt ist. Der Prozess gliedert sich in drei wesentliche Schritte. Das Zuschneiden der Bleche, das Runden der Bleche und zuletzt das Verschweißen zu einer Zylinderform. Mit Hauptaugenmerk auf das Verschweißen sind diese Prozessschritte gemeinsam zu betrachten. Der Rundungs- und Schweißprozess wurde durch Neuentwicklung diverser Hilfs- und Führungselemente optimiert. Durch Prozessbeobachtungen wurden bei deutlich reduzierter Schmierstoffmenge zunächst Stip-Slick-Effekte an der Bandkantenführung während des Schweißprozesses erkannt. Diese führten zu Relativbewegungen der Bandkanten zueinander, was das Schweißergebnis signifikant negativ beeinflusste. Hier wurde eine neue Auszugsachse konzipiert und steuerungstechnisch integriert, was auch bei reduzierter Schmierstoffmenge zu guten Ergebnissen führt.
Der Längs- und Querteilprozess wurde durch besseres Ausrichten, verbesserte Bandführung und geänderte Messerwerkstoffe optimiert, um die Stabilität während des folgenden Schweißprozesses zu verbessern. Ergänzend wurde der Rundungs- und Schweißprozess durch Neuentwicklung diverser Hilfs- und Führungselemente optimiert. Verbrennende Schmierstoffe können beim Schweißen zu Poren führen. Durch geänderte Messerwerkstoffe ist es gelungen, die notwendige Schmierstoffmenge drastisch zu reduzieren und so die Porenbildung zu minimieren. Durch den deutlich reduzierten Einsatz von Schmierstoffen kam es allerdings während des Schweißprozesses bei Verwendung des dünnen Materials zunächst unter anderem zu Stip-Slick-Effekten an der Bandkantenführung. Diese führten im Prozess zu Relativ-bewegungen der Bandkanten zueinander, was das Schweißergebnis signifikant negativ beeinflusste. Zur Lösung des Problems wurde eine neue Auszugsachse konzipiert und steuerungstechnisch integriert. Mit Hilfe dieser Achse können auch bei reduzierter Schmierstoffmenge Zylinder mit der angestrebten Qualität erzeugt werden.
Letztlich ist es gelungen, durch die Summe der verschiedenen Einzelmaßnahmen, die Ausschussquote von 12,5 Prozent auf 2,8 Prozent zu reduzieren – das Ziel, den Ausschuss zu halbieren wurde damit deutlich unterboten. Materialeinsatz und Energieeinsatz können entsprechend reduziert werden. Wird nur die Reduzierung der Schrottmenge unter Berücksichtigung des Schrotterlöses betrachtet, betragen die jährlichen Kosteneinsparungen über 45.000 Euro. Hinzu kommen Nebeneffekte des reduzierten Schmierstoffverbrauchs, der damit verminderten Rauchgasentwicklung durch verbrennende Schmierstoffe und ein geringerer Energieeinsatz. Diese reduzieren nicht nur die Kosten, sondern dienen auch der Entlastung der Umwelt.
Die größte Schwierigkeit bestand darin, die Ansatzpunkte zu finden, das gesteckte Ziel effizient zu erreichen. Ähnlich herausfordernd war es, den Einfluss von Verschleißerscheinungen an Maschinen- und Werkzeugkomponenten bestmöglich abzuschätzen, um vorbeugende Maßnahmen in die Wartungspläne aufnehmen zu können.
- Großserienfertigung
- Entwicklung / Konstruktion ,
- Verarbeitungsprozess
- Prozessoptimierung ,
- Six Sigma
- Material ,
- Metalle ,
- Chemieprodukte ,
- Abfälle
- taktisch (1 bis 5 Jahre)