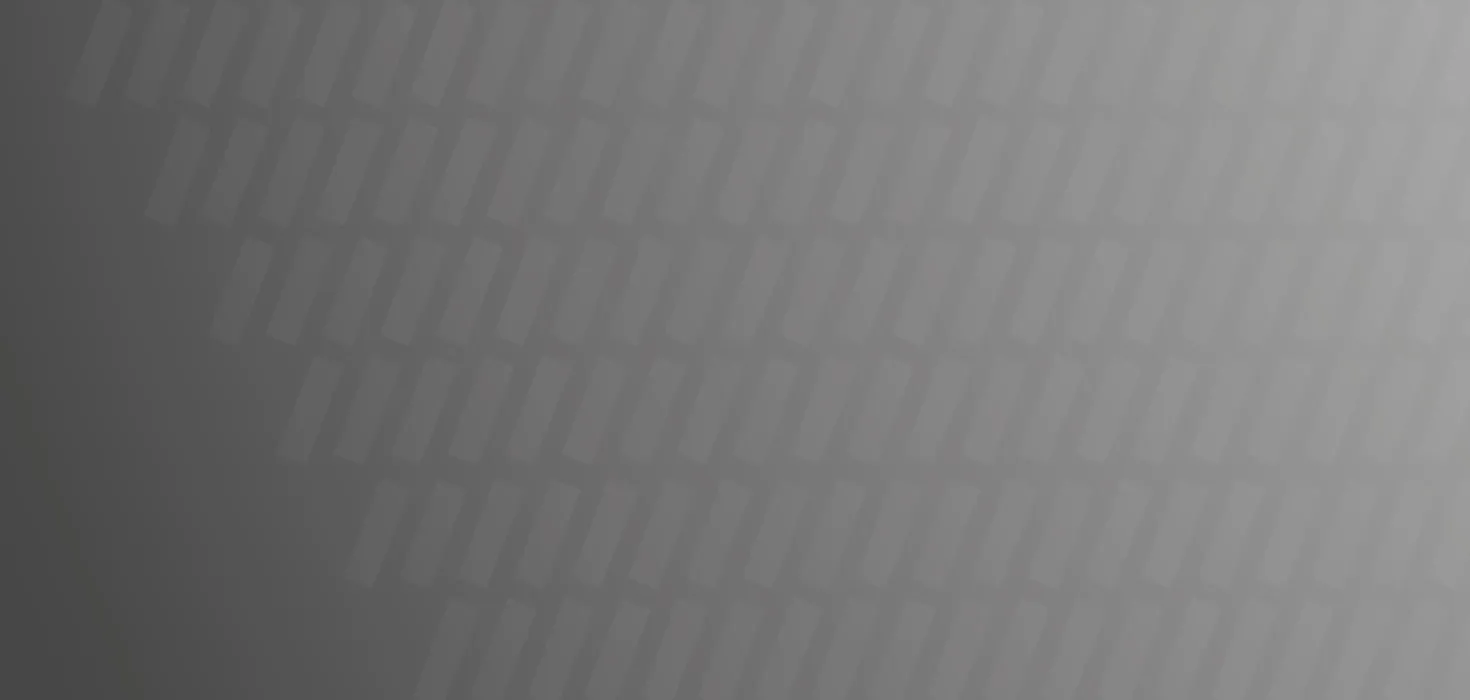
REProMag – Ressourceneffiziente Produktion von Magneten
Energieeinsparung
OBE Ohnmacht & Baumgärtner gehört zu den führenden Herstellern komplexer, im Metallpulverspritzgussverfahren gefertigter Bauteile. Um Material einzusparen und unabhängig vom asiatischen Markt zu sein, hat das Unternehmen ein Verfahren mitentwickelt, mit dem es Magnete aus ausgedienten Gebrauchsgütern wiederverwenden kann und hat so einen geschlossenen Materialkreislauf geschaffen.
Die 1904 gegründete Firma OBE Ohnmacht & Baumgärtner GmbH & Co. KG mit Hauptsitz in Ispringen im Nordschwarzwald gehört zu den führenden Herstellern komplexer, im Metallpulverspritzgussverfahren gefertigter Bauteile. Seit dem Jahr 1996 werden für die Branchen Automotive, Luftfahrt, Telekommunikation und Feinmechanik kleinste, hochkomplexe Metallbauteile in Serie hergestellt, die herkömmlich nicht oder nur unwirtschaftlich herstellbar wären. OBE setzt mit dieser Technologie stetig neue Maßstäbe, z. B. mit der Entwicklung spezieller Materialien für die Technologie des Metallpulverspritzgusses (Metal Injection Moulding, MIM).
Die Herstellung von Magneten auf Basis von Neodym und anderen geeigneten Metallen, den so genannten Seltenen Erden, ist ein höchst ressourcenintensiver Prozess. Zum Abbau und Aufschluss der Erze werden eine Reihe giftiger Chemikalien eingesetzt, bevor der nutzbare Rohstoff, ein metallisches Pulver, für die weitere Verarbeitung zur Verfügung steht. Außerdem steigt die weltweite Nachfrage nach diesen Materialen mit der weiter fortschreitenden Nutzung von Sensoren, Generatoren und Elektromotoren in Elektrogeräten, zur Energiegewinnung und in Mobilitätsanwendungen. Aus wirtschaftlicher Sicht ist besonders bedeutend, dass über 90 % der Seltenen Erden in China abgebaut werden, wobei eine restriktive Exportpolitik und volatile Preisgestaltung europäischen und deutschen Firmen den Zugang zu den Seltenen Erden erschweren.
Ziel des Projekts ist es, Neodym-Eisen-BorMagnete (NdFeB-Magnete) aus ausgedienten Gebrauchsgütern wiederzuverwerten. Dies geschieht durch Herstellung und Aufbereitung eines rezyklierten NdFeB-Pulvers, das zu neuen magnetischen Komponenten verarbeitet werden kann. Damit wird ein geschlossener Materialkreislauf geschaffen und eine Unabhängigkeit vom asiatischen Markt erreicht.
Die Herausforderung besteht in der Auslegung der Prozesskette, d. h., der Abstimmung der Prozessschritte Pulverherstellung, Aufbereitung der spritzgieß- bzw. druckfähigen Formmasse, Entbindern und Sintern. Dabei wird das Ziel verfolgt, aus dem rezyklierten Pulver einen in seinen Eigenschaften mit Neumaterial vergleichbaren Magneten zu erhalten. Im Gegensatz zu vielen gängigen Werkstoffen neigt NdFeB im Pulverzustand schon bei Raumtemperatur stark zur Aufnahme von Sauerstoff aus der Atmosphäre. Dies kann einerseits die Magneteigenschaften stark verschlechtern, andererseits auch zu sicherheitstechnischen Schwierigkeiten aufgrund einer erhöhten Brandgefahr führen.
Eine weitere prozesstechnische Herausforderung besteht in der Kontrolle des Kohlenstoffgehalts des Werkstoffs, der die magnetischen Eigenschaften ebenfalls negativ beeinflusst. Eine Kontaminationsquelle für das Pulver besteht im organischen Bindersystem, das sich beim Entbinderungsprozess (bei etwa 500 bis 600 °C) thermisch zersetzt und Kohlenstoff an das Metall abgeben kann. Schon eine Erhöhung des Kohlenstoffanteils im Bereich von einem Zehntelprozent kann dazu führen, dass die Magneteigenschaften des Materials verlorengehen.
Im ersten Schritt der Prozesskette wird das Pulver hergestellt. Grundlage für das Recycling von Magnetkomponenten zu Pulver ist die hohe Reaktivität von Neodym mit Wasserstoff (H2), welche den Prozess sehr stark erleichtert. Setzt man z. B. eine Computerfestplatte in einem geschlossenen Reaktor einer Wasserstoffatmosphäre aus und bewegt diese dabei in einer sich drehenden Trommel, so kann nach kurzer Zeit das NdFeB-Pulver in hydrierter Form am Reaktorboden aufgefangen und – nach Abpumpen des Wasserstoffs – entnommen werden. Nachdem etwaige Korrosionsbeschichtungen, wie z. B. galvanisch aufgebrachte Nickelschichten, mechanisch abgesiebt wurden, kann das gewonnene Pulver direkt für den Druck- oder MIM-Prozess verwendet werden.
Der zweite Schritt, die Herstellung des Feedstocks, erfolgt in einem vorgeheizten Knetmischer, in dem die Binderkomponenten aufgeschmolzen werden, bevor das recycelte NdFeB-Pulver zugeführt wird. Im Gegensatz zur konventionellen Feedstockherstellung für den Metallpulverspritzguss müssen hierbei die Komponenten in einem mehrstufigen Prozess unter Schutzgasatmosphäre gemischt werden, um eine Kontamination des hydrierten Pulvers an der Luft zu vermeiden und die Pulverpartikel so im Feedstock einzubetten, dass beim nachfolgenden Spritzgießen eine Bildung von Nd-Oxiden prozesssicher vermieden werden kann.
Der dritte Schritt, die Formgebung der Bauteile, erfolgt durch das 3D-Drucken oder das MIM-Verfahren, wobei in beiden Fällen der oben beschriebene Feedstock als Ausgangsmaterial verwendet wird.
Im letzten Schritt in der Prozesskette wurde die Prozesstechnik des Entbinderns und Sinterns darauf ausgelegt, die Aufnahme von Kohlenstoff aus dem Bindersystem möglichst vollständig zu verhindern. Durch geeignete Wahl der Heizparameter und Gasatmosphären bzw. deren Umschaltpunkte konnten die Kohlenstoffgehalte in den Endprodukten von 0,2 % auf <0,1 % reduziert und damit eine Aufnahme aus Binderbestandteilen vollständig unterdrückt werden.
Die Nutzung von Pulvern, die bis zu 100 % aus Rezyklat bestehen, bildet zusammen mit der beschriebenen Optimierung der Prozessführung die Grundlage für die ressourceneffiziente Herstellung von Magneten in einem geschlossenen Materialkreislauf ohne Fertigungsabfälle. So konnten z. B. endkonturgetreue Demonstratoren für Elektromotoren gefertigt werden, bei deren bisheriger Fertigung über 90 % des NdFeB-Materials als Schleifabfall verloren gingen. Die hergestellten Recyclingmagnete zeigten dabei 95 % der Koerzitivfeldstärke des Neumaterials.
Erste Versuche zeigen, dass durch geringe Zusätze von Nd zum Recyclingmaterial die Werte des Neumaterials erreicht werden können. Die Entwicklung des REProMagFertigungsprozesses eröffnet die Möglichkeit, die umweltbelastende Erzgewinnung und -aufbereitung und damit das Anfallen toxischen Schlamms, der zum Eintrag von Schwermetallen ins Grundwasser führt, drastisch zu reduzieren. Mit der Realisierung des Verfahrens geht zudem, je nach Komplexität der Magnetgeometrie, ein hohes Einsparpotenzial in der Magnetproduktion selbst einher, da komplexe Bauteile hergestellt werden können. Diese können in der bislang üblichen Press- und Sintertechnik nicht oder nur mit hohem Nachbearbeitungsaufwand, insbesondere Schleifen, dargestellt werden. Da die Formgebung endkonturnah bzw. endkonturgetreu erfolgt und somit spanende Nachbearbeitungsschritte entfallen können, kann neben dem enormen Einsparpotenzial an Rohstoffen auch eine geschätzte Energieersparnis im Fertigungsprozess von rund 30 % erreicht werden.
Auf Seiten der Magnettechnik bedeuten die komplexen Geometrien zudem neue Möglichkeiten der Führung des Magnetflusses, die zu weiteren Einsparungen von Material, Bauraum und Gewicht bei gleicher oder höherer Leistung führen.
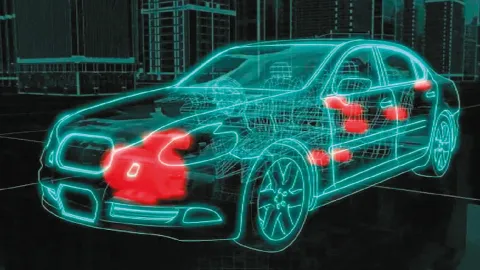
Das REProMag-Projekt zeigt die Leistungsfähigkeit des SDS-Verfahrens. Ausgehend von den im Projekt exemplarisch untersuchten Demonstratorbauteilen werden derzeit erste Serienanwendungen projektiert. Hierbei sollen Magnete aus Produkten rezykliert werden, die von Endverbrauchern an den jeweiligen Hersteller im Rahmen seiner Rücknahmeverpflichtung zurückgegeben wurden. Dieses Rezyklat soll anschließend zu neuen Magneten verarbeitet werden und in Nachfolgeprodukten zum Einsatz kommen. Um das SDS-Verfahren hersteller- und bauteilunabhängig zum Erfolg zu führen, wären allerdings die Einführung einer Kennzeichnungspflicht von Magneten und der Aufbau einer entsprechenden Recycling-Infrastruktur seitens des Gesetzgebers wünschenswert. Alle Vorteile des Prozesses werden nur unter Verwendung von Sekundärmaterial ausgeschöpft. Doch auch beim Einsatz von Primärmaterial führt der Prozess zu Material- und Energieeffizienzsteigerungen in der Herstellung.
OBE Ohnmacht & Baumgärtner GmbH & Co. KG in Ispringen führt das REProMag-Projekt im Rahmen eines Konsortiums, das aus 14 Partnern aus fünf europäischen Ländern besteht. Davon sind fünf Partner Universitäten bzw. Forschungseinrichtungen, fünf Partner kleinere und mittlere Unternehmen (KMU), drei Partner sind Großunternehmen und ein Partner ist Forschungsdienstleister.
Das Konsortium ist so zusammengestellt, dass die gesamte Prozesskette von der Gewinnung des Recyclingpulvers bis zur Herstellung von Demonstratorbauteilen abgebildet ist. Das Projekt wird im Rahmen des Calls „Factory of the Future FoF02-2014- Manufacturing processes for complex structures and geometries with efficient use of material“ der Forschungsförderung HORIZON 2020 der Europäischen Kommission unter der Grant Agreement Nummer 636881 gefördert.
- Kleinserienfertigung
- Entwicklung / Konstruktion ,
- Verarbeitungsprozess
- Stoffkreislauf / Recycling ,
- Industrie 4.0 / Digitalisierung
- Energie ,
- Material ,
- Metalle ,
- Abgas
- strategisch (größer 5 Jahre)