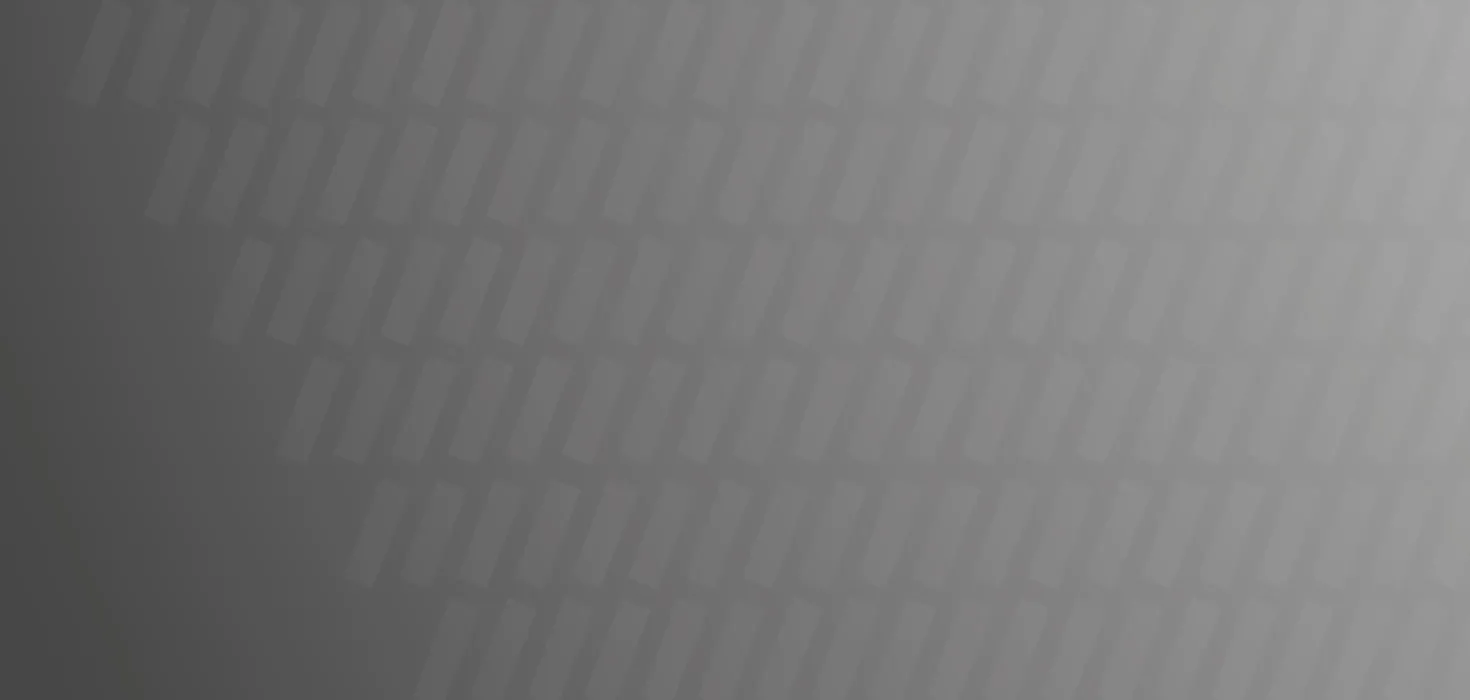
Roboterunterstützte Automatisierung erhöht Flexibilität
Entwicklung und Implementierung einer flexiblen robotergestützten Automatisierung aus Standardkomponenten
Edelstahleinsparung
Aluminiumeinsparung
Stahleinsparung
Stromeinsparung
Die SFA GmbH & Co. KG ist vor allem auf den Sondermaschinenbau spezialisiert. Um die Produktion mehrerer Einzelteile mit möglichst kurzen Umrüstzeiten umzusetzen, wurde eine innovative Fertigungszelle aus Standardkomponenten entwickelt. Besonders wichtig ist es, dass die Fertigungszelle jederzeit an die sich wandelnden Anforderungen angepasst werden kann und Umrüstverluste vermieden werden.
Die SFA GmbH & Co. KG aus Aichstetten ist auf die CNC-Fräs-/Drehbearbeitung und den Sondermaschinenbau spezialisiert. Die Sondermaschinen werden komplett von der Konstruktion über die Mechanik und Elektrik von SFA entwickelt und aufgebaut. Die entsprechende Softwareentwicklung und der Service werden ebenfalls angeboten.
Um mehrere verschiedene Teile mit möglichst kurzen Umrüstzeiten nahezu zeitgleich produzieren zu können und bestmögliche Kundenzufriedenheit zu erzielen, entstand bei SFA der Wunsch nach einer hochflexiblen, automatisierten Fertigungszelle.
Diese sollte gleichzeitig auch als Lagerplatz für Mess- und Prüfvorrichtungen sowie Sondergrößen von Werkstückpaletten dienen. Sie sollte sowohl für die Einzelteilfertigung als auch für einen Vollautomatikbetrieb ausgelegt sein. Darüber hinaus wollte man die Option haben, die Zelle jederzeit mit wenig Aufwand erweitern oder umbauen zu können.
Zum Zeitpunkt der Planung und Realisierung gab es auf dem Markt jedoch keine hochflexible Fertigungszelle, welche die gewünschten Anforderungen der Betriebsführung vereinte. Daher entschied man sich bei SFA, die Fertigungszelle selbst zu entwickeln und aufzubauen.
Für die hochflexible Fertigungszelle sollten Serienmaschinen und -komponenten wie Roboter und Regalanlagen mit mehreren Rüstplätzen vereint werden. Jederzeit sollte die Möglichkeit zur Erweiterung bestehen. Geplant war eine Inhouselösung mit kurzen Wegen, wodurch für die Mitarbeiter während der Einarbeitungszeit nach der Inbetriebnahme nur ein Ansprechpartner benötigt wird. Dementsprechend müssen nicht verschiedene Vertragsparteien koordiniert werden.
Nach der Konzeption der Anlage wurde die Fräsmaschine bestellt und die Automation nach einer gewissen Anlaufzeit angebaut. Die Fräsmaschine und die Automatisierung wurden zeitversetzt installiert, um die Produktion möglichst schnell wiederaufzunehmen und die Möglichkeit zu haben, die Automation schrittweise anzubauen sowie die Funktionen zu testen. Bereits während der Umsetzung wurden Optimierungen zusammen mit den Mitarbeitern, welche die Anlage später bedienen, erarbeitet und im Vorfeld eingearbeitet und umgesetzt. Die Rüstplätze und der Greifer wurden selbst konstruiert und gebaut.
Die unterschiedlichen Paletten werden nun mittels des selbst entwickelten Greiferwechselsystems im Falle der Grundpalette mit einer Palettengabel und im Falle der Werkstückpaletten mit einer Greifergrundstation gehandhabt.
Die Paletten werden in einem handelsüblichen Schwerlastpalettenregal als eigener Parkplatz definiert und abgelegt. Das Greiferwechselsystem ist an einem 6-Achs-Roboter montiert, der wiederum auf einer Linearachse befestigt ist. Dadurch entsteht ein kombinierter Arbeitsraum mit Rund- und Längsverfahrwegen.
Bestückt werden die Werkstückpaletten auf zwei Rüstplätzen, die unabhängig voneinander beladen und gerüstet werden können. Weitere Plätze können ohne großen Aufwand integriert werden. Ist ein Rüstplatz belegt, steht der andere uneingeschränkt zur Verfügung. Diese Ausführung mit zwei Rüstplätzen ist in einem kleineren Palettensystem wie bei SFA bisher noch nicht am Markt verfügbar.
Die Automatisierung versetzt SFA in die Lage, bis zu 30 verschiedene Bauteile parallel zu bearbeiten. Die Fertigung erfolgt so wie die Teile vom Kunden abgerufen werden. Durch Kombination der unterschiedlichen Teile in der Planung kann nun mit sortenreinen Rohmaterialien gearbeitet werden. Alle Aluminiumteile, alle Stahlteile und alle Kunststoffteile werden zusammengefasst bearbeitet und die Späne können sortenrein dem Recycling zugeführt werden. Dies war früher aufgrund von Rüstvorgängen nicht möglich.
Durch die gesunkenen Rüstzeiten von einem Produkt auf ein anderes kommt es zu weniger Maschinenstillstandzeiten. Aufgrund der Materialbündelung werden weniger unter - schiedliche Materialabmessungen gleicher Materialgüte benötigt, wodurch die Lagerhaltung für die unterschiedlichsten Abmessungen weitgehend entfällt. Durch die Verwendung von einheitlichen Materialabmessungen werden pro Jahr pro Jahr 1 t Edelstahl, 3 t Aluminium und 5 t Stahl eingespart. Durch größere Abnahmemengen und Rahmenverträge mit den Lieferanten können auch bessere Einkaufskonditionen erzielt werden. Aufgrund der sortenreinen Material- und Teileplanung stieg der Recyclingfaktor des zerspanten Abfallmaterials. Mit der neuen Anlage konnte zudem der Stromverbrauch um 12 % gesenkt werden, was 50 MWh pro Jahr entspricht.
Weiterhin befindet sich durch die verlängerten Maschinenlaufzeiten der verwendete Kühlschmierstoff länger im Umlauf und seine Standzeit wird erheblich verlängert. Seit Inbetriebnahme der Anlage im Jahr 2016 musste die Kühlemulsion nicht gewechselt werden und die teure Entsorgung und Neubefüllung des Kühlmittelsystems konnte eingespart werden.
Außerdem sinkt durch ein ergonomischeres Bestücken der Werkstücke auf die Werkstückpaletten die Belastung für die Mitarbeiter. So wurden mit der neuen Anlage keine krankheitsbedingten Stillstandzeiten mehr verzeichnet. In der Vergangenheit kam es bei einer typähnlichen Maschine ein- bis zweimal jährlich zu Ausfallzeiten durch muskuläre Probleme der Mitarbeiter.
Das umgesetzte Projekt zeigt, dass mit Standardbearbeitungsmaschinen und -komponenten eine hochflexible Automatisierung realisiert werden kann, die den Grundsätzen des Lean Managements entspricht. Der erweiterte Nutzen für die Anwender besteht in der Möglichkeit, dass die Bearbeitungen an die sich wandelnden Marktanforderungen angepasst werden können. Darüber hinaus können auch eine weitere Bearbeitungsmaschine oder weitere Folgebearbeitungen eingebunden werden. Hier können z. B. Kundenforderungen wie Kanbanlieferungen, Abrufrahmenverträge oder Einzelfertigung mit wenig Aufwand vereint werden. Allerdings ist festzustellen, dass sich die Flexibilität oft nicht mit dem Ziel der sortenreinen Abfallmaterialverwendung vereinbaren lässt. Schließlich ist geplant, das Automationssystem durch die eigene Sondermaschinenabteilung zu vermarkten.
Die SFA mechanische Fertigung / Sondermaschinenbau GmbH & Co. KG mit Sitz in Aichstetten im württembergischen Allgäu ist ein junges innovatives Unternehmen, welches in den Bereichen CNC-Fräs-/Drehbearbeitung und Sondermaschinenbau tätig ist.
Gegründet wurde das Unternehmen im Jahr 1994. In den Jahren 1997, 2005, 2012 und 2017 expandierte der Betrieb und beschäftigt mittlerweile 75 Mitarbeiterinnen und Mitarbeiter, die auf ca. 4.700 m² Produktions- und Lagerfläche Fertigungsaufträge bearbeiten und Automationsanlagen sowie Sondermaschinen bauen.
Das eigene Qualitätsverständnis und -bewusstsein sowie die Einstellung aller Mitarbeiter zur Qualität sind wichtige Voraussetzungen für die Zufriedenheit der Kunden und den Unternehmenserfolg. Daher wurde im Jahr 2005 ein QS-Managementsystem nach DIN EN 9001:2000 eingeführt und fortlaufend rezertifiziert. Auf diese Weise werden eine möglichst störungsfreie Organisation, kontinuierliche Verbesserungen sowie fortschrittlichste Methoden in der Produktion sichergestellt.
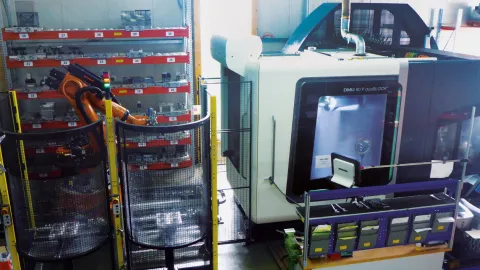
- Kleinserienfertigung
- Produktionsplanung / -steuerung ,
- Produktionslogistik ,
- Verarbeitungsprozess
- Werkzeuginnovation ,
- Prozessoptimierung ,
- Stoffkreislauf / Recycling ,
- Industrie 4.0 / Digitalisierung
- Energie ,
- Material ,
- Metalle ,
- Abwasser ,
- Abgas
- strategisch (größer 5 Jahre)