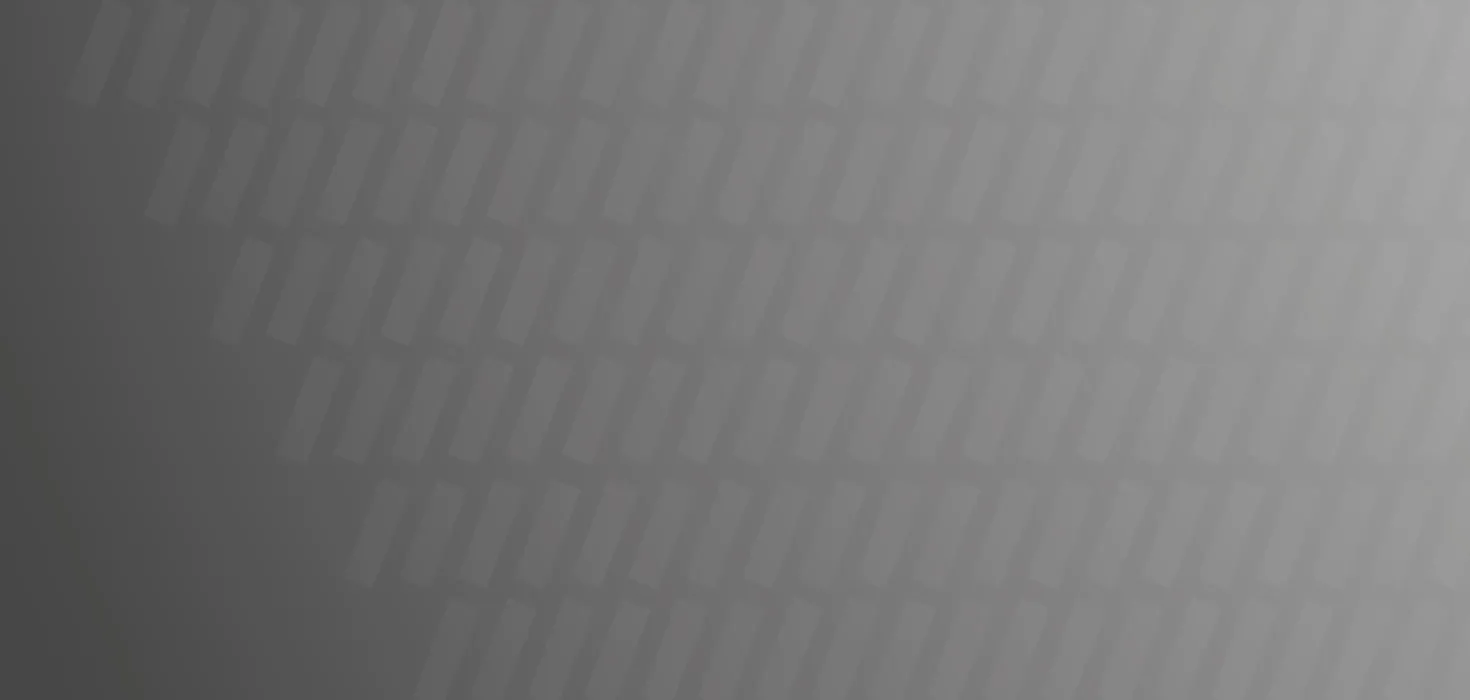
Eine selbstlernende Organisation senkt Materialverluste
Aufbau einer selbstlernenden Organisation sowie Umsetzung konkreter Maßnahmen zur Steigerung der Ressourceneffizienz
Reduktion der Teilebestellung für den Prototypenbau
Die Wiedenmann GmbH zählt zu den führenden Herstellern hochwertiger Maschinen für Rasenpflege, Schmutzbeseitigung und Winterdienst. Die Firma hat eine selbstlernende Organisation aufgebaut, um Materialverluste durch Kommunikations- oder Abstimmungsfehler zu vermeiden. Durch Workshops konnten die Mitarbeiter Kompetenzen für Ressourceneffizienz entwickeln und gemeinsam die Produktion optimieren.
Kostenvorteile
- 31.000 Euro die an Materialwert 2012 und 2013 eingespart wurden
- 79.000 Euro eingesparte Wertschöpfungskosten bei den Nullserien
- 36.000 Euro durch Vermeidung jährlicher Verschrottungen von veraltetem Lagerbeständen
- ca. 200.000 Euro durch Materialverlustvermeidung in der zweijährigen Umsetzungsphase der Maßnahmen
- 300.000 Euro im organisatorischen Bereich
Die in Rammingen beheimatete Wiedenmann GmbH zählt zu den führenden Herstellern hochwertiger Maschinen für Rasenpflege, Schmutzbeseitigung und Winterdienst. Das Unternehmen kauft jährlich Stahl sowie Kauf- und Normteile im Wert von rund 6,5 Mio. Euro ein, von diesem eingekauften Material gingen bislang ca. 5 % als Produktionsabfall verloren.
Da die vielfältigen Gründe für die Entsorgung und damit auch den Wertschöpfungsverlust bisher nicht systematisch erfasst wurden, konnten sie nur schwer beeinflusst und verändert werden. Gerade bei geringen Stückzahlen für Kleinserien und Sonderaufträge kam es durch fehlerhafte Zeichnungen und Stücklisten sowie Fehlern in der Arbeitsvorbereitung immer wieder zu fehlerhaften Teilen.
In der Serienproduktion waren fehlende Informationen bei den Mitarbeitern in den einzelnen Fertigungs- und Montagebereichen, Teileverwechslungen aufgrund unvollständiger Teilekennzeichnung, Lagervernichtung durch Überalterung und fehlendes Auslaufmanagement für Bauteile Materialverlustgründe. Auch Qualitätsabweichungen bei Neuanläufen aufgrund von Abstimmungsfehlern zwischen den Abteilungen, selbstverursachte Hektik durch zu spät angestoßene oder kurzfristig verschobene Fertigungs- und Montageaufträge, höherer Rüstverlust durch Fehlteile aufgrund nicht abgestimmter Materialbestellung oder zu spät bestelltes Material sowie keine konsequente Werkerselbstkontrolle waren weitere Gründe.
Um die Ressourceneffizienz ganzheitlich und konsequent zu verbessern, mussten den Mitarbeitern Kompetenzen und Fähigkeiten vermittelt werden. Diese sollten sie dabei unterstützen, die Verlustgründe zu erkennen und die Möglichkeiten zur systematischen Änderung selbstständig auszuschöpfen. Die Erfolge in der Verbesserung der Ressourceneffizienz sollen die Mitarbeiter motivieren, sich weiter in Richtung selbstlernende Organisation zu entwickeln.
Durch eine ganzheitliche Material- und Informationsflussanalyse, die Implementierung systematischer KVP-Workshops und die dauerhafte Installation eines abteilungsübergreifenden KVP-Teams zur Steigerung der Materialeffizienz sollten vor allem abteilungsübergreifende Themen durch die beteiligten Mitarbeiter selbst angegangen und erfolgreich verändert werden. Im Produktentwicklungsprozess sollen durch agile, abteilungsübergreifende Teams Kommunikationsbarrieren überwunden und Folgefehler vermieden werden. Der systematische Kompetenzaufbau bei den Mitarbeitern auf allen Hierarchieebenen soll auch in Zukunft dafür sorgen, dass auftretende Herausforderungen zur Steigerung der Materialeffizienz erkannt und selbstständig umgesetzt werden können. Die eigens dafür ausgebildeten internen Wiedenmann Coaches begleiten die Teams in ihrer Arbeit.
Der ganzheitliche Kompetenzaufbau bei den Mitarbeitern wurde durch das imu augsburg unterstützt. Zunächst wurde das Projekt im Führungskreis geplant und organisatorische Entscheidungen getroffen. In einer Art Analysephase wurden bereits erste Themenschwerpunkte eruiert sowie Handlungsschwerpunkte zur Identifikation von Materialeffizienzpotenzialen identifiziert. Um eine möglichst lückenlose Darstellung der Material- und Informationsflüsse zu gewährleisten, wurden aus allen wesentlichen Bereichen des Unternehmens Personen benannt.
Im nächsten Schritt wurde das KVP-Team als Ergänzung zur bereits bestehenden KVP-Prozesslandschaft aufgebaut. Die vordergründige Aufgabe des KVP-Teams ist die Identifizierung von Materialeffizienzpotenzialen, die dazugehörige Maßnahmengenerierung sowie die Kontrolle der Umsetzungsfortschritte. Eine weitere, aber ganz wesentliche, Aufgabe des KVP-Teams besteht in der Sensibilisierung aller Mitarbeiter hinsichtlich der Thematik der Materialeffizienz.
Über die gesamte Wertschöpfungskette hinweg wurde eine Materialflussanalyse durchgeführt, welche durch eine Informationsflussanalyse vom Kunden über Vertrieb, Entwicklung und Produktion bis hin zum Einkauf ergänzt wurde. Die Ergebnisse der Analysen wurden zusammengeführt und Handlungsfelder zusammengefasst. Weiterhin wurden Maßnahmen zur Steigerung der Materialeffizienz generiert und umgesetzt.
Die Einführung von agiler Teamarbeit im Produktentwicklungsprozess wie auch in den Bereichen Versuch und Montage führte zu passenden organisatorischen Strukturen und Entscheidungskompetenzen, um die aufgedeckten Effizienzpotenziale wiederkehrend zu heben. Die internen Wiedenmann Coaches sorgten für verbindliche und lösungsorientierte Treffen, so dass bestehende Probleme wirklich gelöst werden konnten.
Durch die Umsetzung der generierten Maßnahmen konnten in unterschiedlichen Bereichen des Unternehmens Einsparungen erzielt werden. Konkret führte die Optimierung des Produktentwicklungsprozesses im Bereich der Serienüberleitung zur Einführung einer vorgelagerten Vorserie vor der in Serienumgebung gefertigten Nullserie. Kennzeichnend für die Serienüberleitung sind erhebliche Kosten für Maschinen, die nicht reproduzierbar in erster Serie gefertigt wurden und entweder als Prototypen gekennzeichnet und entsprechend nicht verkäuflich waren oder durch umfangreiche Nacharbeit erst in Serienzustand versetzt werden mussten. Durch Einführung eines Zwischenschritts zur Prüfung der Serienfähigkeit, einer sogenannten Vorserie, kann sichergestellt werden, dass die erste Serie im Serienzustand erhalten wird und damit als verkäufliche Ware in entsprechender Qualität angeboten werden kann. Der reine Materialwert, der hierdurch in den Jahren 2012 und 2013 während des Projekts eingespart wurde, beträgt 31.000 Euro. Darüber hinausgehende, eingesparte Wertschöpfungskosten bei den Nullserien betragen 79.000 Euro. Durch den stabilisierten und standardisierten Produktentwicklungsprozess sowie durch die Einbindung von Einkauf und Arbeitsvorbereitung konnte die Teilebestellung für den Prototypenbau um 50 % reduziert werden. Die neue Zusammenarbeit in den agilen Produktentwicklungsteams führte Ende des Jahres 2016 erstmals zu einer Vorserie ohne Materialverluste, in der alle entwickelten Teile fehlerfrei im Prototypenbau genutzt werden konnten.
Durch die Einführung eines konsequenten und transparenten Auslauf- und Änderungsmanagements werden jährliche Verschrottungen von veraltetem Lagerbestand in Höhe von 36.000 Euro eingespart. Kern der Transparenz ist ein Durchlauf des Änderungsscheins über das Intranet, so dass alle beteiligten Abteilungen stets über den Stand von Änderungen informiert sind. Restbestände an Kauf- und Normteilen, hergestellten Baugruppen und ausgelaufenen Serienprodukten wie Kehrmaschinen oder ähnlichem, die ansonsten zu 100 % verschrottet wurden, werden mittlerweile von kaufmännischen und gewerblichen Auszubildenden eigenständig als kleine Firma in der Firma über eBay verkauft.
In der zweijährigen Umsetzungsphase der Maßnahmen konnten Materialverluste in Höhe von ca. 200.000 Euro vermieden werden. Neben diesen eingesparten Kosten durch die Vermeidung der Materialverluste werden zusätzlich damit zusammenhängende Einsparungen im organisatorischen Bereich von über 300.000 Euro erzielt. Durch ein konsequentes Verfolgen der vereinbarten Maßnahmen können die Mitarbeiter diese Kosteneinsparungen jährlich wiederkehrend erreichen.
Das Schwierige im Maschinenbau sind die komplexen Zusammenhänge von Ressourceneffizienzpotenzialen. Zumeist liegen die Potenziale in technologischen und organisationstheoretischen Gründen gleichzeitig verankert. Eine Hebung dieser Potenziale erfordert einen Blick, der mehrere Perspektiven einnimmt und vereint. Eine Einzelperson kann dies zumeist nicht leisten.
Deshalb ist das Besondere an diesem Projekt die dauerhafte Implementierung des abteilungsübergreifend besetzten KVP-Teams in der Organisation von Wiedenmann. Dieses Team trifft sich seit der Gründung in 2012 wöchentlich. Die Besetzung erfolgte nicht nach Hierarchie, sondern nach Fach- und Sozialkompetenzen. Durch deren Engagement und direkte Kommunikation, durch die internen Wiedenmann Coaches sowie durch die agile Teamarbeit in der Produktentwicklung, Montage und im Versuch entwickelt sich die Kultur von einem abteilungsorientierten Silodenken hin zu einer selbstlernenden Organisation, in der Effizienzpotenziale in allen Ebenen entdeckt und eigenständig gehoben werden.
Die Wiedenmann GmbH wurde 1964 von Gertrud und Georg Wiedenmann gegründet. Beständigkeit und Zuverlässigkeit zählen von Beginn an zur Firmenphilosophie und formten den Leitsatz „Nur das Beste“. Heute wird das Unternehmen von den Söhnen Jürgen, Horst und Uwe Wiedenmann erfolgreich geleitet. Rund 245 Mitarbeiterinnen und Mitarbeiter in Rammingen bei Ulm sowie im ungarischen Beled setzen regelmäßig neue Maßstäbe hinsichtlich innovativer Technologien und kompromissloser Qualität. Vom hohen Leistungsanspruch des Familienunternehmens zeugen mittlerweile zahlreiche Innovationspreise, Patente und Schutzrechte.
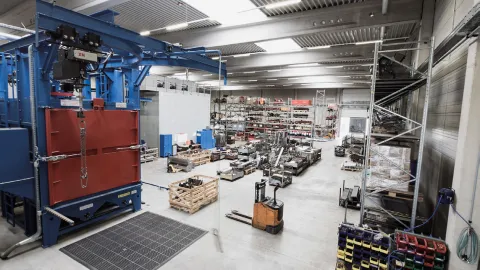
- Einzelteilherstellung ,
- Kleinserienfertigung
- Marketing / Vertrieb ,
- Einkauf ,
- Produktionsplanung / -steuerung ,
- Produktionslogistik ,
- Verarbeitungsprozess
- Prozessoptimierung ,
- Stoffkreislauf / Recycling ,
- Green Supply Chain Management ,
- Lean Management
- Material ,
- Metalle ,
- Sonstige Materialien ,
- Abwasser
- operativ (kleiner 1 Jahr)