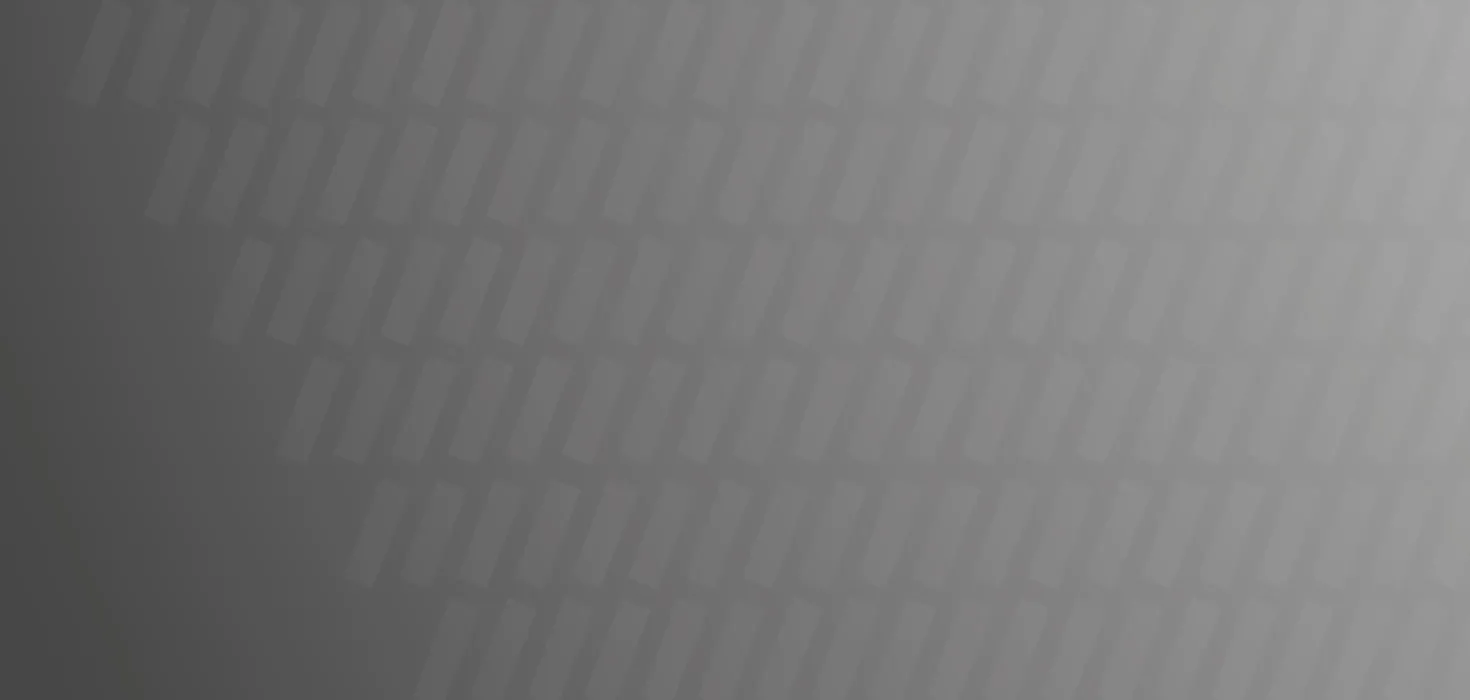
Von spanender Fertigung zur Kaltumformung
Umstellung eines Fertigungsverfahrens
Stahleinsparung
Energieeinsparung
Stromeinsparung
CO2-Reduktion
Felss ist auf ressourceneffiziente Kaltumformverfahren spezialisiert und fertigt unter anderem Komponenten für die Automobilindustrie. Das Unternehmen hat einen Fertigungsprozess, bei dem bisher große Materialverluste anfielen, vom Spanen auf Kaltumformung umgestellt. Dadurch kann in Zukunft mehr als die Hälfte des Materials eingespart werden, wodurch das Unternehmen auch Kosten sparen kann.
Kostenvorteile
- 115.500 Euro/Jahr durch Stahleinsparung
- 3.500 Euro/Jahr durch Stromeinsparung
Felss ist auf ressourceneffiziente Kaltumformverfahren spezialisiert und fertigt unter anderem Komponenten für die Automobilindustrie. Diese zeichnen sich durch große Stückzahlen und hohe Anforderungen an Maßgenauigkeit aus. Mit Kaltumformverfahren können gegenüber einer spanenden Fertigung große Materialeinsparungen erzielt und Leichtbauprinzipien realisiert werden. Damit sind beträchtliche monetäre Einsparungen möglich.
Ein Kunde, der Lenkungen produziert, betraute Felss mit der Entwicklung eines Fertigungsverfahrens für Lenkspindeln. Bisher wurden die Lenkspindeln spanend gefertigt. Hierbei wurde das Bauteil aus Stangenmaterial aus Stahl mittels Bohren, Fräsen und Drehen gefertigt. Bei diesem Verfahren fällt eine große Menge an Materialverlust in Form von Spänen an.
Die spanende Fertigung der Lenkspindel wurde von einer Kaltumformung abgelöst. Hierfür wurde eigens eine Rundknetanlage konzipiert. Rundkneten ist ein Verfahren zur Herstellung von rotationssymmetrischen Bauteilen mit ausgeprägter Längsachse. Werkzeugsegmente rotieren um das Werkstück und formen es um. Neben der Bearbeitung der Außenkontur ist es ebenso möglich die Innenkontur zu bearbeiten. Hierfür werden Dorne eingesetzt, die die Negativform für die Innengeometrie darstellen.
Die Komponentenfertiger und Maschinenbauer von Felss, sowie der Kunde haben für die Entwicklung des Prozesses eng zusammengearbeitet. Nach der Optimierung des Bauteils wurden auch die Prozesskette und die Maschinentechnik optimiert. Durch diesen ganzheitlichen Ansatz, konnten die Effizienzpotenziale optimal ausgeschöpft werden.
Die Lenkspindel wird nun in sieben Bearbeitungsschritten hergestellt. Begonnen wird mit einem Rohrabschnitt. Dieser wird in den ersten drei Schritten über den Dorn gehämmert, anschließend gedreht und spanend bearbeitet. Im vorletzten Schritt wird durch Axialformen die benötigte Außenverzahnung spanlos aufgepresst.
Ebenso wurde die Maschinentechnik energetisch optimiert. Alle Antriebsachsen wurden elektrifiziert, sodass auf die Hydraulik gänzlich verzichtet werden kann. Damit konnte eine Steigerung der Vorschubgeschwindigkeit der Antriebsachsen um 25 % realisiert werden.
Durch den Wechsel zur Kaltumformung sowie die Optimierung des Bauteils können bei einem jährlichen Produktionsvolumen von 160.000 Stück rund 136 t Stahl eingespart werden. Dies entspricht einer Ersparnis von ca. 115.500 Euro und einer Senkung des Materialverbrauchs um 59 %. Das fertige Bauteil ist zudem um fast 200 g leichter als das Bauteil aus der spanenden Fertigung.
Bei Vergleichsmessungen konnte durch die Elektrifizierung der Maschine eine Energieeinsparung von 60 % zur hydraulischen Vorgängermaschine erzielt werden. Der Energieverbrauch pro Rundknetarbeitsschritt sank durch die Elektrifizierung von 89 Wh auf 37 Wh. So können je Arbeitsschritt 52 Wh eingespart werden. Pro Jahr summiert sich die Energieeinsparung bezogen auf 160.000 Teile mit je fünf Rundknetarbeitsschritten auf 41.600 kWh Strom mit einem Gegenwert von etwa 3.500 Euro.
Auch der CO2-Ausstoß wird durch die Stromersparnis gemindert: So fallen pro Jahr rund 25 t weniger CO2 an.
Durch die Entwicklungspartnerschaft mit den Kunden kam es zu einer Interaktion, die es ermöglichte Hand in Hand die ideale Lösung für das Produkt zu finden. Die gewonnenen Erkenntnisse können für zukünftige Projekte hinsichtlich Ressourceneffizienz als Vorbild dienen.
Die Hemmnisse der Kunden, den eigenen Entwicklungsprozess offen zu legen, konnten durch das Erreichen eines Vertrauensverhältnisses abgebaut werden. Je früher im Entwicklungsprozess der Kunde an uns herantritt, desto größer sind die Potenziale, Materialeinsparungen zu realisieren.
Die Felss Gruppe produziert unter dem Markennamen Felss Shortcut Technologies für diverse Branchen, wie zum Beispiel die Automobilindustrie, sowohl Maschinen zur Metallbearbeitung als auch Komponenten. Technisch stehen die Kaltumformverfahren Rundkneten, Axialformen, Biegen, Autofrettage und Endenbearbeitung im Mittelpunkt.
Die Felss Gruppe ist eine global aktive Unternehmensgruppe mit Hauptsitz in Königsbach-Stein. Neben zwei weiteren deutschen Standorten in Bretten-Gölshausen und Nesselwang ist das Unternehmen in Wujiang (China), New Berlin (USA) und Triengen (Schweiz) ansässig. Der Umsatz lag 2015 bei über 100 Mio. Euro. Weltweit beschäftigt Felss über 590 Mitarbeiter, 370 davon in Deutschland.
- Großserienfertigung
- Entwicklung / Konstruktion ,
- Verarbeitungsprozess
- Prozessinnovation
- Energie ,
- Material ,
- Metalle ,
- Abgas
- taktisch (1 bis 5 Jahre)