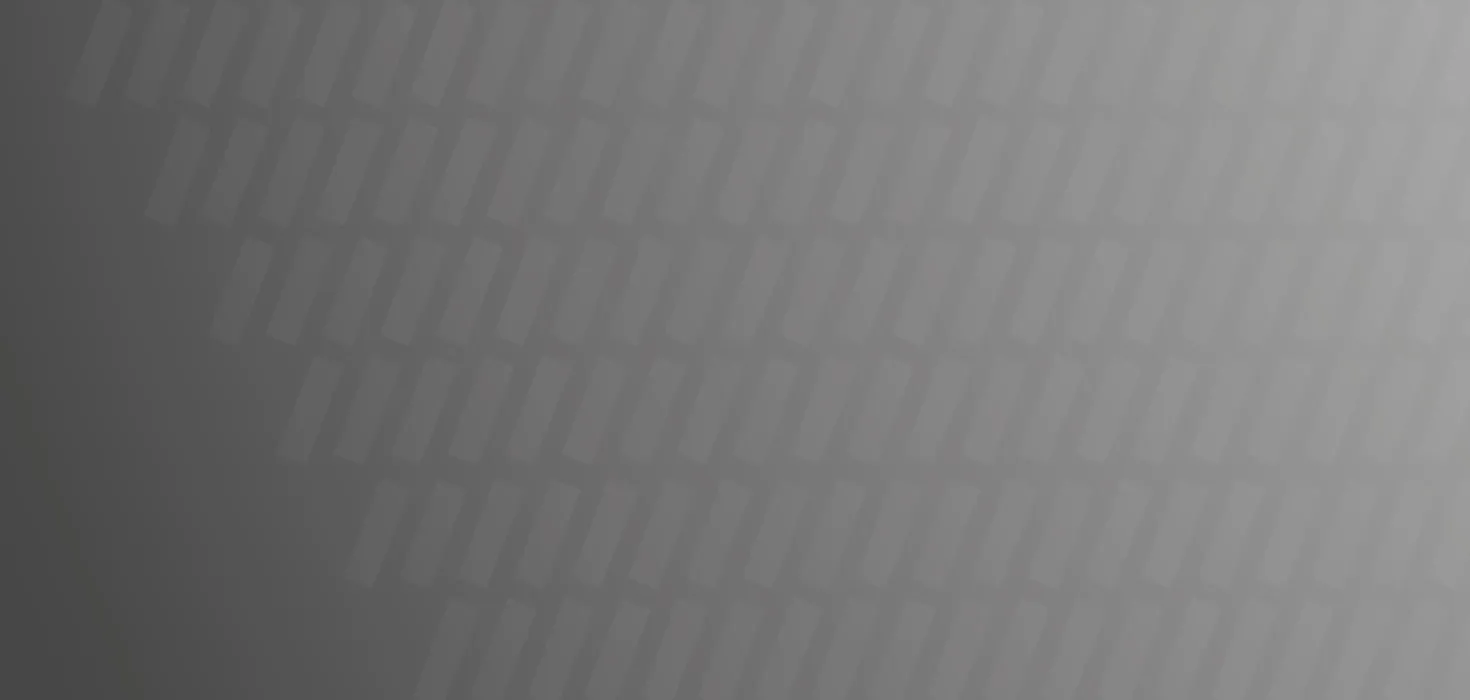
Verbesserte Materialeffizienz in der Produktion eines Drahtwälzlagers
Konstruktive Optimierung eines Drahtwälzlagers
Gewichtsreduktion (Rohlinge)
Die Franke GmbH ist weltweit Technologieführer bei der Entwicklung leichtgewichtiger Bewegungssysteme. Eines ihrer wichtigsten Produkte ist ein Drahtwälzlager für eine medizintechnische Anwendung. Bei der Produktion gibt es allerdings einen hohen Materialverlust. Deshalb hat das Unternehmen ein neues Design entwickelt, das zu einer besseren Materialeffizienz geführt hat.
Zu den Hauptprodukten der Franke GmbH zählt ein hochdynamisches Drahtwälzlager für eine medizintechnische Anwendung. Drahtwälzlagern liegt ein einfaches, aber geniales Prinzip zugrunde. Einzelne Laufringe aus Draht sind mit einer Laufbahn versehen, die exakt an den Durchmesser der Wälzkörper angepasst ist. Der Abrollvorgang erfolgt dadurch nicht unmittelbar zwischen Wälzkörper und umschließender Konstruktion, sondern reibungsarm auf den vier offenen Laufringen. Dieses Konstruktionsprinzip ermöglicht die freie Gestaltung der umschließenden Konstruktion bezüglich Geometrie und Werkstoffwahl.
Durch die starke Profilierung der einzelnen Bauteile entsteht bei der Herstellung ein Materialverlust von mehr als 40 %. Damit verbunden sind hohe Kosten für die spanende Bearbeitung. Aufgrund dieser Tatsachen setzte sich Franke das Ziel, die Herstellung des Drahtwälzlagers zu optimieren und die Materialeffizienz zu steigern.
Mit Hilfe einer ökobilanziellen und einer ökonomischen Analyse sollten die wesentlichen Umweltwirkungen und Einsparpotenziale des Drahtwälzlagers für kleine und mittlere Losgrößen innerhalb der Prozesskette identifiziert und geeignete Optimierungsempfehlungen abgegeben werden. Im Rahmen der Analyse sollten die spezifischen Umweltwirkungen der Bauteile wie das Treibhauspotenzial, das Eutrophierungspotenzial und das Versauerungspotenzial untersucht und ergänzend eine Materialflusskostenrechnung (Material Flow Cost Accounting, MFCA) durchgeführt werden.
Aufgrund der identifizierten Materialverluste sollten Optimierungen ausgearbeitet werden, um die Materialeffizienz zu steigern. Die einzelnen Bauteile sollten konstruktiv so verändert werden, dass lediglich ein geringer Materialanteil durch spanende Bearbeitung abgetragen werden muss. Außerdem sollte untersucht werden, ob die verwendeten Warmwalzverfahren für die Rohteile eventuell durch Gießverfahren ersetzt werden können, um noch weitere spanende Bearbeitungsschritte einzusparen.
In Abstimmung mit dem Kunden wurde das neue Design von Franke in mehreren Schritten realisiert. Die Rahmenbedingungen des Kunden wie Abmessungen der Anschlusskonstruktion, Schnittstellen und Leistungsanforderungen mussten bei der Festlegung des neuen Designs berücksichtigt werden. Hierbei arbeiteten die Technikabteilungen des Kunden und von Franke eng zusammen. Mit Hilfe der 3DSoftware Solidworks wurden die möglichen konstruktiven Maßnahmen simuliert, analysiert und beurteilt.
Da für die Fertigung der Lagerbauteile gewalzte Rohlinge verwendet werden, wurde der Querschnitt der Einzelteile soweit wie möglich rechteckig ausgelegt, um den Zerspanungsprozess auf ein Minimum zu reduzieren. Beispielsweise wurde der Ring-AB (blau) in zwei Teile aufgeteilt, um das Zerspanvolumen weiter zu verringern und Maschinenzeiten zu sparen.
Beim ursprünglichen Drahtwälzlager entstand im Fertigungsprozess der vier Laufringe ein durchschnittlicher Materialverlust von rund 40 % was knapp 170 kg entspricht. Bei der Herstellung der einzelnen Laufringe betrug der Materialverlust teilweise mehr als 70 %. Zur Herstellung der Laufringe wird warmgewalzter Standardstahl (C45N) verwendet. Die Ursache des enormen Materialverlusts lag in der starken Profilierung der einzelnen Bauteile, die durch eine umfassende spanende Bearbeitung entsteht. Diese spanende Bearbeitung bildet nicht nur einen großen Kostenanteil, sondern trägt auch noch einen großen Teil zur Umweltwirkung des gesamten Lagers bei. Wesentlich ist hier der hohe Stromverbrauch durch die lange Bearbeitungszeit. Durch die Optimierung des Lagers reduziert sich einerseits das Gesamtgewicht der Rohlinge um ca. 30 %. Außerdem beträgt der Materialverlust beim Nachfolgemodell nun nur noch etwa 22 %, was ca. 62 kg entspricht.
Durch eine vorrausschauende Vorgehensweise bei Neukonstruktionen können beachtliche Materialeinsparungen erreicht werden. Das größte Potenzial kann dann ausgeschöpft werden, wenn das Unternehmen vom Kunden von Anfang an in Neuentwicklungen eingebunden wird, da hierbei teilweise Einfluss auf das Design angrenzender Bauteile genommen werden kann.
Das Projekt zeigt außerdem, dass es möglich ist, ökologische Gesichtspunkte und Kundeninteressen in Einklang zu bringen. Darüber hinaus lassen sich durch die Materialeinsparung, die verkürzten Maschinenzeiten, sowie die Einsparung von Hilfsstoffen, wie z. B. Kühlschmiermittel, Kosten sparen.
Die Franke GmbH ist Erfinder des Drahtwälzlagers und weltweit Technologieführer bei der Entwicklung und Herstellung leichtgewichtiger Bewegungssysteme. Auf der Suche nach einer raumsparenden Lagerung für ein optisches Gerät entwickelte der Ingenieur Erich Franke 1936 das Drahtwälzlager.
Die Kernkompetenz des Unternehmens ist die Entwicklung innovativer Lösungen gemeinsam mit Kunden. Die Vielseitigkeit hinsichtlich Auslegung und Gestaltung von Drahtwälzlagern führt stets zu optimalen Lösungen für die jeweilige Anwendung. Das Produktprogramm umfasst heute sowohl rotative als auch lineare Komponenten mit und ohne Antrieb.
Drahtwälzlager und Linearsysteme von Franke sind weltweit erhältlich. Vertretungen und Partner in zahlreichen Ländern beraten Kunden und stehen diesen mit Produkten und Serviceangeboten zur Seite. Kooperationen mit starken Partnern in Nordamerika und Asien ermöglichen die Produktion vor Ort und tragen dazu bei, Kunden schnell und kostengünstig zu beliefern.
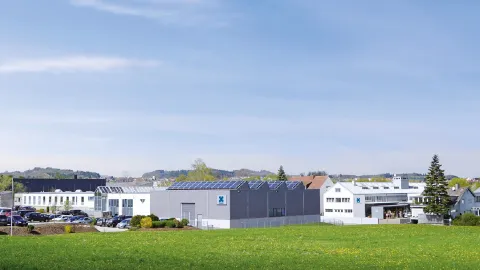
- Kleinserienfertigung
- Verarbeitungsprozess
- Produktinnovation ,
- Prozessinnovation
- Material ,
- Metalle
- operativ (kleiner 1 Jahr)