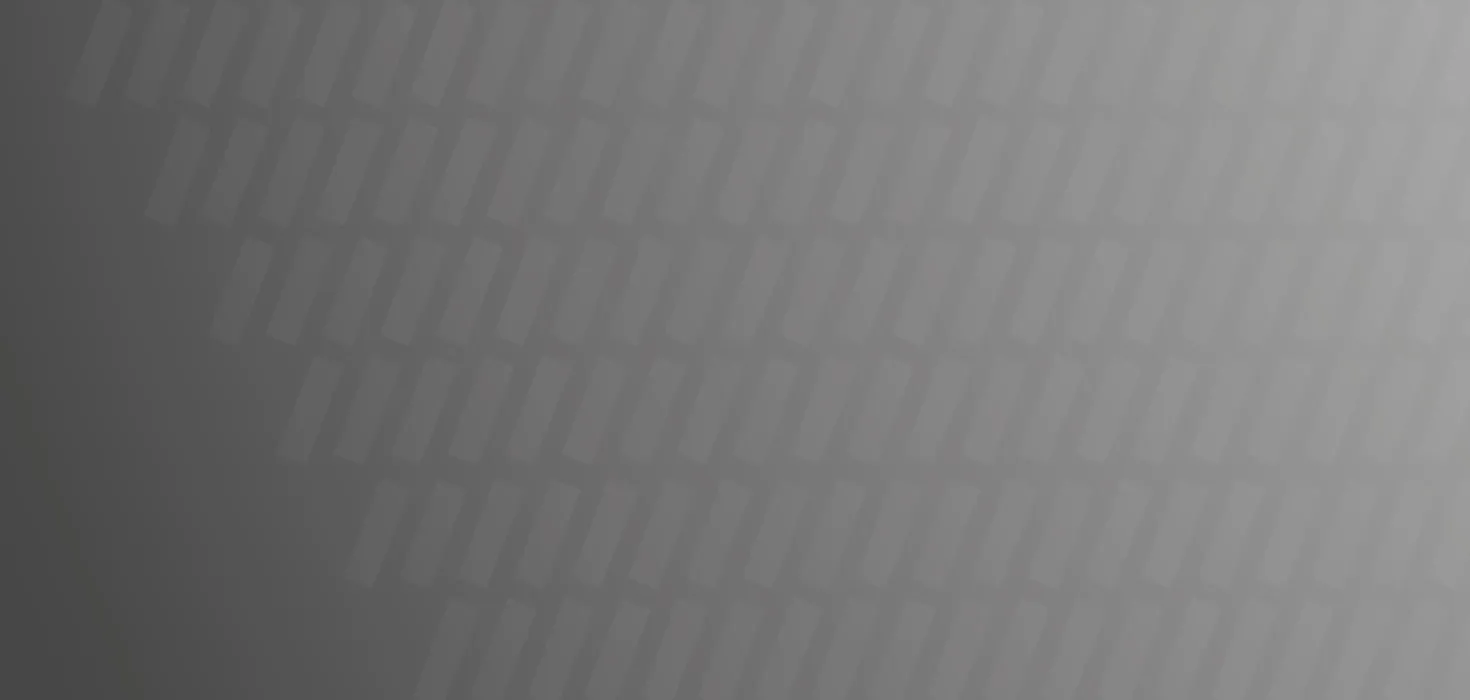
AluMotive® – Systematische Ressourceneffizienzsteigerung von Aluminiumleichtbau-Komponenten
Entwicklung einer neuen Legierung und Untersuchung alternativer Vormaterialherstellungsrouten
Aluminiumeinsparung
Stromeinsparung
Gaseinsparung
CO2-Einsparung
Die LEIBER Group GmbH & Co. KG hat den Herstellungsprozess für Hochleistungsbremstöpfe aus Aluminium ressourcenseitig optimiert. Die umgesetzten Maßnahmen wurden umfassend an der kompletten Wertschöpfungskette vorgenommen und reduzierten den Materialeinsatz und die CO2-Emissionen deutlich. So wurde ein nachhaltiger und innovativer Prozess zur ressourceneffizienten Produktfertigung entwickelt.
Die LEIBER Group GmbH & Co. KG mit Sitz in Emmingen-Liptingen ist Spezialist für Leichtbauteile aus Aluminium. Das Leistungsspektrum umfasst die gesamte Prozesskette von der Forschung und Entwicklung bis hin zur Serienfertigung und Montage kompletter Baugruppen. Eines der Produkte von LEIBER sind Bremsscheibentöpfe. Diese sind für die Übertragung der Bremsmomente verantwortlich und damit ein elementarer Bestandteil des
Bremssystems. Der Reibring kann fest (aus einem Guss) oder durch zusätzliche Verbindungselemente mit dem Bremsscheibentopf verbunden sein. In Hochleistungsbremsanlagen kommen aufgrund der geringen Dichte bei gleichzeitig hohen statischen und dynamischen Festigkeiten geschmiedete Bremsscheibentöpfe aus Aluminium zum Einsatz. Neben den technischen Anforderungen müssen die Bremsscheibentöpfe höchsten optischen
Anforderungen entsprechen. Gefordert wird ein Oberflächenbild, das frei von Gefügeunterschieden ist. Diese werden durch Rekristallisation auf der Oberfläche sichtbar und müssen zerspanend entfernt werden, was zur Folge hat, dass sich der Materialbedarf verdreifacht.
Daraus entstand die Zielsetzung, systematisch die komplette Prozesskette zu analysieren und die aus der Hotspotanalyse entstandenen Ergebnisse in zielgerichtete Maßnahmen umzuwandeln. Vor diesem Hintergrund entwickelte LEIBER ein neues Fertigungskonzept, mittels alternativer Vormaterialherstellrouten, um von Anfang bis Ende des Herstellungsprozesses Ressourcen einzusparen. Ziel des Projekts war die Reduzierung des Materialeinsatzes und die damit einhergehende Reduzierung des Bearbeitungsaufwands.
Im Jahr 2020 sollten im Rahmen einer internen Forschungs- und Entwicklungsmaßnahme ein neues Legierungskonzept sowie alternative Vormaterialherstellungsrouten untersucht und deren Eignung anhand von Prototypen überprüft werden. Die internen Forschungsmaßnahmen beinhalteten Grundlagenuntersuchungen hinsichtlich der Eignung des Legierungskonzepts als Schmiedevormaterial. Des Weiteren wurde untersucht, ob die technologischen sowie optischen Anforderungen erfüllt werden können. Darüber hinaus wurden Lieferanten aufgebaut, um eine Verfügbarkeit des Materials für künftige Produkte sicherzustellen. Bei Erfolg der internen Maßnahmen sollte das neue Konzept an Kunden herangetragen und diese überzeugt werden.
Durch die internen Bemühungen konnte die LEIBER Group unter der Eigenmarke AluMotive® eine neue Legierungsvariante hervorbringen. Hierzu wurde ein Projektteam gegründet, welches aus den Abteilungen Industrial Engineering, Innovation und dem Werkstoffprüflabor bestand. Durch die Teamkombination konnten Maßnahmen analysiert und umgesetzt, sowie die Eignung dieser in Abhängigkeit der Anforderung untersucht werden. Durch AluMotive® lässt sich die Rekristallisation und damit die erforderliche Bearbeitungszugabe (Aufmaß) für die Zerspanung deutlich reduzieren. Zusätzlich hat AluMotive® durch seine hervorragende Umformbarkeit das weitere Potenzial, an verschiedenen Stellen in der Wertschöpfungskette ressourcenschonend Leichtbauprodukte herzustellen.
Durch die Verwendung der neuen Legierungsvariante kann durch den Wegfall eines kompletten Prozessschrittes, welcher eine Erwärmung, Umformung und nachfolgende Bearbeitungen (Recken, Trennen etc.) beinhaltet, das Schmiedevormaterial ressourcensparender erzeugt werden. Des Weiteren werden für den Einsatz von AluMotive® nur ausgewählte Lieferanten herangezogen, welche einen CO2-Footprint von weniger als 4 kg CO2e pro kg Aluminium aufweisen. Laut European Aluminium liegt der globale Durchschnitt bei 16 kg CO2e.
Bisher kam beim Schmieden der Bremsscheibentöpfe ausschließlich stranggepresstes Vormaterial zum Einsatz, um die hohen statischen und dynamischen Anforderungen zu erfüllen. Seit Kurzem sind jedoch qualitativ höherwertige Stranggussverfahren in der Branche vorhanden, welche die erforderlichen Reinheitsgrade sicherstellen. Üblicherweise wird das Stranggussverfahren verwendet, um Bolzen für den Strangpressprozess zu gießen. Diese Bolzen haben typischerweise Durchmesser von 200 - 400 mm und sind als Schmiedevormaterial ungeeignet. Durch den Einsatz modernster Kokillentechnologie im
Durchmesserbereich von 60 - 200 mm wird es nun in Kombination mit hohen Reinheitsgraden möglich, stranggegossenes Aluminium direkt als Schmiedevormaterial zu nutzen.
Darüber hinaus konnten in den letzten Jahren durch grundlegende interne Untersuchungen beim Schmieden von gegossenem Vormaterial Umformgrade und Prozessgrenzen für das Schmieden definiert werden, die sicherstellen, dass vergleichbare mechanische Kennwerte wie bei der Verwendung von stranggepresstem Halbzeug erreicht werden.
Weiteres Potenzial zeigt sich bei der Prozessauslegung mit diesen neu definierten Prozessgrenzen. Für das Schmieden ist es möglich, den Vormaterialdurchmesser zu minimieren, was eine Einsparung beim Sägeverschnitt zur Folge hat.
Die Verwendung von AluMotive® ermöglicht es ebenfalls, den Schmiedeprozess dahingehend zu optimieren, dass durch die Verwendung bauteilspezifischer Rohteilgeometrien (near net shape) das Einsatzgewicht bei den Bremsscheibentöpfen um 18 % reduziert werden konnte. Die Optimierung im Schmiedeprozess führte zudem zu Einsparungen in den nachgelagerten Bearbeitungsprozessen, welche sich in einem verringerten Zerspanvolumen und kürzeren Bearbeitungszeiten äußern.
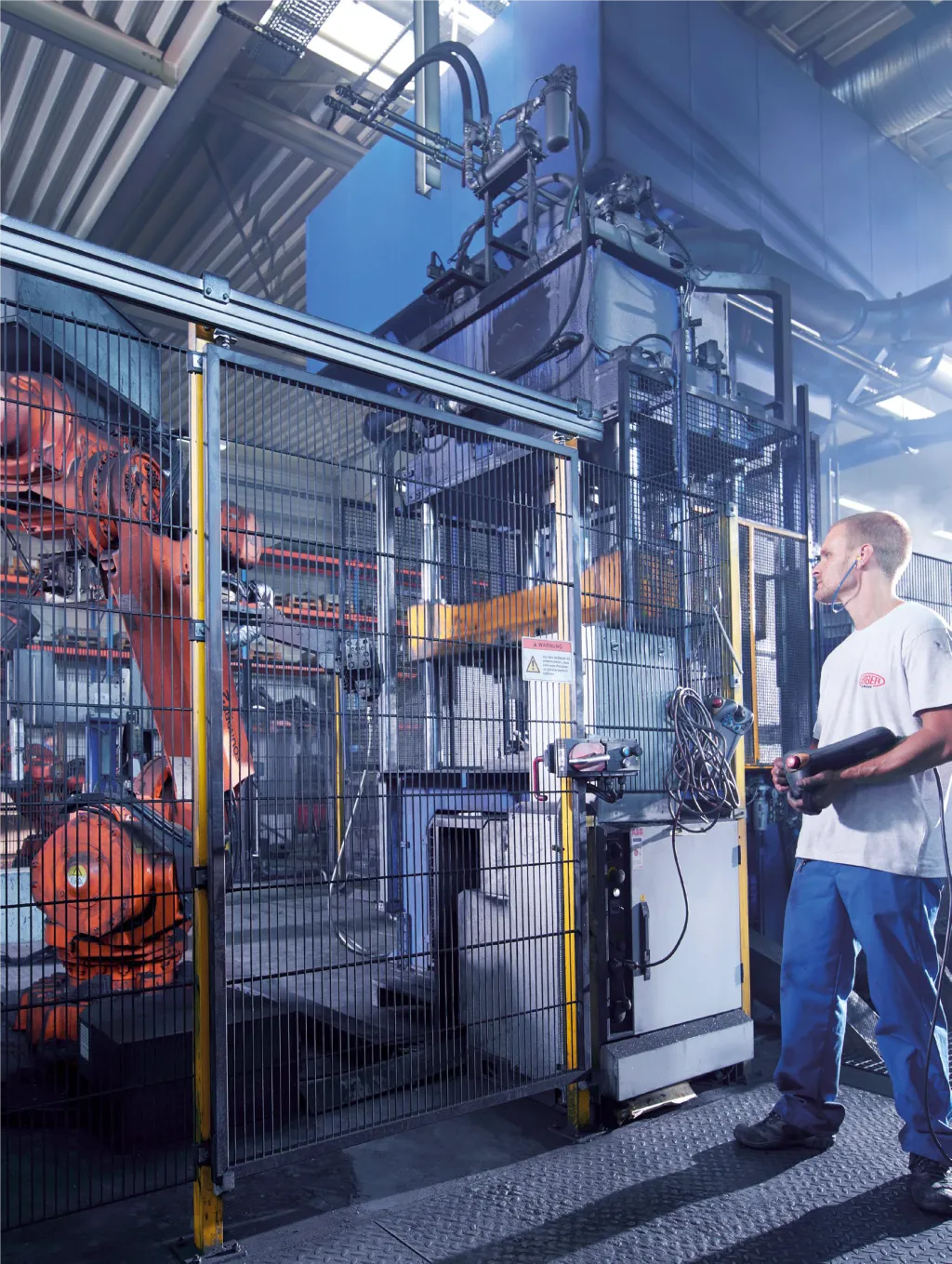
Durch die umgesetzten Maßnahmen konnte der Aluminiumeinsatz für die Bremsscheibentöpfe um 18 % und der Sägeverschnitt aufgrund des geringen Stangendurchmessers um 36 % reduziert werden. Durch die Reduzierung des Einsatzgewichts muss eine geringere Tonnage an Aluminiumknetlegierung für den Warmumformungsprozess erwärmt werden, wodurch sich der Verbrauch von Strom und Erdgas reduziert. Des Weiteren konnten durch die Reduzierung des Einsatzgewichts und die damit verbundenen geringeren Dimensionen des Schmiedehalbzeugs die Bearbeitungszeiten und das Spanvolumen während der mechanischen Bearbeitung gesenkt werden.
Bezogen auf das bereits umgesetzte Projekt mit 10.500 Bremsscheibentöpfen bedeutet das eine Einsparung von 5,8 t Aluminium, 18 MWh Strom und 5 MWh Gas. Diese Material- und Energieeinsparungen sowie die optimierte Vormaterialroute führen zu CO2-Einsparungen in Höhe von etwa 102 t CO2e pro Jahr.
Langfristig können und sollen die Maßnahmen auf die komplette Produktfamilie übertragen werden. Das Gesamtvolumen dieser Produktfamilie beträgt aktuell ca. 120.000 Bauteile pro Jahr und soll bis zum Jahr 2030 auf >200.000 Bauteile steigen, sodass die Einsparungen etwa um den Faktor 20 sukzessive erhöht werden können. Dies entspricht einer jährlichen Einsparung von etwa 115 t Aluminium, 360 MWh Strom, 103 MWh Erdgas und ca. 1.930 t CO2e.
Durch die Verknüpfung aller Faktoren von Vormaterialherstellungsprozessen bis zu optimierten Schmiede- und Zerspanprozessen ist es dem Unternehmen gelungen, einen bestehenden Prozess durch einen innovativen und ressourceneffizienten zu ersetzen, der auf eine Vielzahl von Produkten der gleichen Produktfamilie übertragen werden kann. Das stetige Hinterfragen der aktuellen etablierten Prozesse bringt oftmals bislang ungenutzte Potenziale zum Vorschein.
Durch die systematische Analyse der kompletten Wertschöpfungskette wurde ein wichtiger Stellhebel geschaffen, um den Kunden weitere Projekte dieser Art anbieten zu können.
Ein nicht zu vernachlässigender Faktor ist allerdings der zeitliche Aufwand der Beteiligten an diesem Projekt. Eine ganzheitliche Betrachtung und eine detaillierte Bewertung der Faktoren ist ein zeitaufwändiger Prozess. Aufgrund ausgiebiger Kommunikation der Analyseergebnisse und deren Maßnahmen konnte ein gemeinsames nachhaltiges Bewusstsein geschaffen werden.
Die LEIBER Group ist ein weltweit anerkannter Spezialist und Impulsgeber für Leitbauteile aus Aluminium und hat ihren Stammsitz im süddeutschen Emmingen, gelegen in der für ihre Wirtschaftsstärke bekannten Region zwischen Tuttlingen und dem Bodensee-Hegau. Darüber hinaus wurde im Jahre 1995 mit der Gründung des Produktionsstandorts in Ruda Slaska in Südpolen ein weiterer Standort für Klein- und Mittelserien sowie einzelne ausgereifte
Produktionsreihen eröffnet.
Die Kunst des Leichtmachens treibt LEIBER seit jeher an. Aber es ist das Fundament aus Werten, das das Familienunternehmen vom ersten Tag an zuverlässig trägt. Diese Werte zu leben, ist Anspruch und Ansporn zugleich.
Diese Werte haben die Mitarbeiterinnen und Mitarbeiter dazu angetrieben dieses Projekt umzusetzen, um für eine enkeltaugliche Welt einzutreten. Nachhaltigkeit bedeutet für LEIBER: wirtschaftliches Handeln unter Berücksichtigung der Menschen, Umwelt und Ressourcen.
Es ist eben so viel leichter, Großes zu erreichen, wenn die Werte stimmen.
- Kleinserienfertigung
- Verarbeitungsprozess
- Prozessinnovation ,
- Prozessoptimierung
- Energie ,
- Material ,
- Abgas