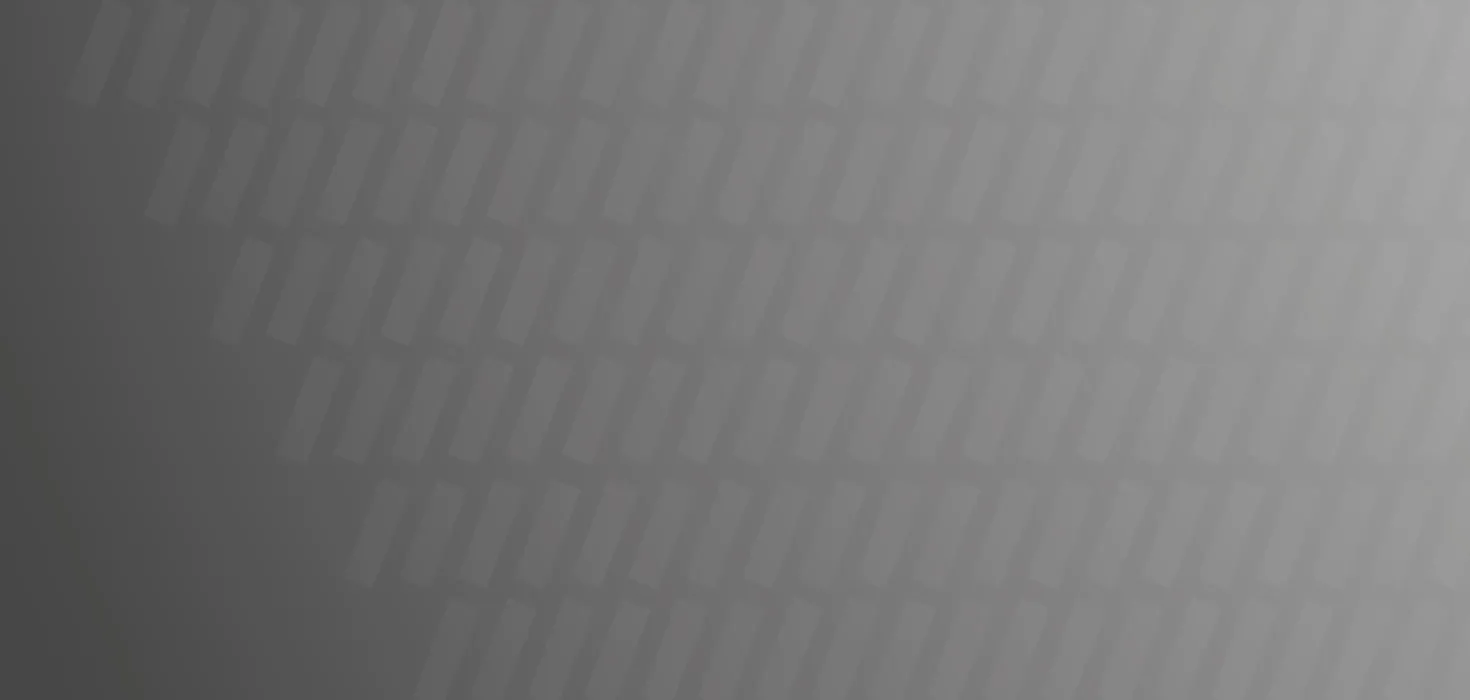
Continuous Manufacturing Technology – Optimierung der Arzneimittelproduktion
Kontinuierliche Förderung von Wirk- und Hilfsstoffen mit in-line Mischung und vollautomatischem Transport zur Tablettierung und Verkapselung
CO2-Reduktion (durch Änderung der Logistikkette)
CO2-Reduktion (durch den Einsatz erneuerbarer Energien)
Um sein Nachhaltigkeitsziel zu erreichen, optimiert das Unternehmen Pfizer stetig seine Prozesse. Bei diesem Projekt wurde die kontinuierliche Fertigung angegangen. Ziel sollten reduzierte Herstellungskosten, robuste Herstellprozesse mit Online-Monitoring, sowie ein hinsichtlich CO2-Emissionen und Abfall optimierter Fertigungsprozess sein. Dieses Ziel konnte durch das Projekt erreicht werden.
Pfizer, einer der weltweit größten Pharmakonzerne, hat im Jahr 2009 einen global gültigen Nachhaltigkeitsplan verabschiedet. Dieser enthält u. a. auch eine verbindliche Zielsetzung bezüglich CO2-Emissionen, Wasserverbrauch und Abfallvermeidung. Das Freiburger Werk nimmt innerhalb des Pfizer-Konzerns eine Vorreiterrolle ein. Einer langfristig angelegten Strategie folgend wurden seit Ende der 1990er Jahre konsequent nachhaltige Technologien implementiert. Dazu gehören geothermische Heizung und Kühlung von Gebäuden, Photovoltaik, die Verwendung von Biomasse zur Energieerzeugung und zahlreiche innovative Techniken wie die adiabate Kühlung von Laborbereichen und eine Pilotanlage zur Trocknung von Prozessluft mittels Sonnenenergie. Vervollständigt wird das Gesamtkonzept durch eine entsprechende Gebäudetechnik mit einem Online-Monitoring der Energieströme.
Der Standort Freiburg hat vergleichsweise hohe Arbeitskosten im Pfizer-Netzwerk. Auch innerhalb eines multinationalen Konzerns besteht ein Wettbewerb der Standorte um Produkte. Marktchancen erhält vor allem das Werk, das weltweite Qualitätsanforderungen erfüllt, termingerecht liefern und wettbewerbsfähig herstellen kann. Um hierbei erfolgreich zu sein, werden alle Prozesse des Arzneimittelwerks in Freiburg kontinuierlich geprüft und optimiert. Dies geschieht mit Hilfe der Automation, Industrie 4.0, Lean Manufacturing und Steigerung der Energieeffizienz. Am Standort werden neue, innovative Technologien in Kooperationen mit anderen Werken und Forschungsstandorten des Pfizer Netzwerkes, mit Hochschul- und Industriepartnern entwickelt und umgesetzt.
Dem aktuellen Projekt – der kontinuierlichen Fertigung - liegen mehrjährige Forschungs- und Entwicklungsarbeiten im Pfizer Forschungszentrum Groton (USA) in Zusammenarbeit mit der Firma GEA und der Hochschule Gent zugrunde. Hier wurden neuartige pharmazeutische Herstellungsverfahren entwickelt, die die traditionellen, chargenbezogenen Herstellschritte durch einen kontinuierlichen, voll automatisierten Prozess ersetzen können.
Für die nachhaltige Produktion fester Arzneiformen sollte eine neue Fabrik entstehen. Die traditionelle, chargenbezogene Einwaage und stufenweise Fertigung sollte darin durch die kontinuierliche Förderung von Wirk- und Hilfsstoffen mit In-line-Mischung und vollautomatischem Transport zur Tablettierung und Verkapselung ersetzt werden. Die für Pharmaka erforderliche hohe Dosiergenauigkeit sollte mittels In-line-Mischung, Echtzeitanalytik und Rückkopplung zur Fördertechnik erzielt werden. Entsprechende Sensoren erfassen dabei die Prozess- und Qualitätsparameter und erstellen vollelektronisch Herstellungsdokumente. Die Chargengröße wird über die Laufzeit der Anlage definiert und kann so hochflexibel an veränderten Marktbedarf angepasst werden. Die Konzeption der Fabrik sollte einen verkürzten Materialfluss unter enger Lieferanteneinbindung ermöglichen.
Die Konzeption zur Umsetzung vom Forschungs- und Entwicklungsmaßstab in den großtechnischen Betrieb erfolgte in Kooperation des Freiburger Werks mit Experten der Hochschulen Offenburg, Freiburg und Albstadt-Sigmaringen sowie internationalen, nationalen und regionalen Industriepartnern.
Im neuen Prozessfluss werden im ersten Schritt, dem Versorgen, die Wirk- und Hilfsstoffe in sehr großen Gebinden, sogenannten Big Bags, bereitgestellt und können ohne weitere Zwischenschritte direkt in der Produktion verwendet werden. Die Big Bags wurden von Pfizer entwickelt und verfügen über ein Fenster zur Qualitätskontrolle mittels Raman-Spektroskopie. Ein manuelles Probeziehen ist damit nicht mehr erforderlich. Diese Umstellung spart z. B. 80 % der zuvor eingesetzten Holzpaletten ein.
Der zweite Prozessschritt ist das Dosieren. Dabei werden die Wirk- und Hilfsstoffe dem Produktionsprozess über ein vollautomatisches Fördersystem zugeführt und entsprechend der Medikamentenzusammensetzung genau dosiert.
Im dritten Prozessschritt, dem Mischen, vermengt eine neuentwickelte Mischeinheit die Wirk- und Hilfsstoffe zu einer homogenen Mischung, die z. B. in einem Kapselfüller weiterverarbeitet werden kann. Die Durchsetzrate des kontinuierlichen Mischers reicht von 5 bis 1.000 kg pro Stunde. Mit dieser hohen Flexibilität kann Pfizer rasch auf den Markt- und damit Patientenbedarf reagieren. Eine Kernkomponente der kontinuierlichen Fertigung ist die Online-Qualitätsmessung mit Hilfe der Prozess-Analyse-Technologie (PAT). Sie bindet die Qualitätssicherung in den laufenden Prozess ein, wodurch langwierige Laboruntersuchungen der Vergangenheit angehören.
Durch die kontinuierliche Fertigung konnte die Logistikkette verschlankt und optimiert werden. Die Umstellung von Packmitteln und Gebindegrößen führte zu einer signifikanten Reduktion des Frachtaufkommens, wobei die Lieferkette von Luft- auf Seefracht umgestellt wurde. Der auf die Logistikkette bezogene CO2-Ausstoß konnte um 33 % reduziert werden.
Die neue Förder- und Mischtechnik verkürzt die Durchlaufzeiten für die Bereitstellung der Rohstoffe einer Charge signifikant durch die hohe Ausbringleistung von 1.000 kg pro Stunde – eine durchschnittliche Rohstoffmischung für die Herstellung von Kapseln besteht in der Regel aus etwa 500 kg. Durch den Einsatz der neu entwickelten In-line-Messtechnik wird die Rohstoffmischung kontinuierlich auf Ihre Zusammensetzung und Qualität geprüft. Dadurch entfällt die traditionelle Kontrollanalytik und es wird das Risiko von Materialverlusten reduziert. Dementsprechend verringern sich auch Abfallmengen und die CO2-Bilanz verbessert sich.
Zudem reduziert sich durch den Einsatz erneuerbarer Energien zur Sicherstellung der pharmazeutischen Umgebungsbedingungen (Feuchte, Temperatur, Luftwechsel) der Energieverbrauch und CO2-Ausstoß um 750 t pro Jahr für die Klimatisierung der Produktionsstätte.
Weiterhin ergeben sich durch die Prozessumstellungen flexible Anpassungen der Chargengröße an den Kundenbedarf. Dies erhöht die Agilität und Skalierbarkeit bei Bedarfsveränderungen, verringert Vorratshaltung sowie Lager- und Vernichtungskosten. Schließlich werden An- und Abfahrverluste im kontinuierlichen Prozess vermieden sowie die Reinigungsprozesse optimiert.
Die Übertragung in den technischen Maßstab erforderte den Bau einer neuartigen Fabrik und revolutionär veränderte Materialfluss- und Logistikprozesse, die nur durch Zusammenarbeit entlang der Lieferkette erreicht werden konnten. Die Technologie wird nun durch weitere Investitionen im mittleren zweistelligen Millionenbereich am Standort in Freiburg im Bereich der Entwicklungsabteilung und der Produktionsstätte für Klinikmuster und Routineproduktionen weiter ausgedehnt. Damit können neue Arzneimittel deutlich schneller entwickelt und auf den Markt gebracht werden, wovon insbesondere die Patienten profitieren.
Mit dem Einstieg in die kontinuierliche Produktion ist es Pfizer gelungen, den Materialwertstrom zu optimieren und den ökologischen Fußabdruck weiter zu verringern. Es ist schon jetzt absehbar, dass die neue Technik die Produktion fester Arzneiformen revolutionieren wird.
Seit über 160 Jahren steht der Name Pfizer für die Erforschung und Entwicklung moderner Arzneimittel. Weltweit arbeiten bei Pfizer mehr als 10.000 Forscherinnen und Forscher und über 97.000 Mitarbeiterinnen und Mitarbeiter daran, Impfstoffe zur Prävention sowie Arzneimittel, die Krankheiten heilen oder lindern können, zu entwickeln und herzustellen. Zu den Forschungsschwerpunkten gehören u. a. Krebserkrankungen, Entzündungskrankheiten und Erkrankungen des zentralen Nervensystems. Bei der Entwicklung von neuen Wirkstoffen und Behandlungsmöglichkeiten erschließt die Pfizer-Forschung das große Potenzial von Biotherapeutika und setzt auch auf zielgerichtete und personalisierte Behandlungen.
In Deutschland beschäftigt Pfizer derzeit mehr als 2.000 Mitarbeiterinnen und Mitarbeiter an den Standorten: Berlin, Freiburg und Karlsruhe. Freiburg zählt international zu den modernsten Produktionsanlagen für Tabletten und andere feste Arzneimittelformen. 1.000 Mitarbeiterinnen und Mitarbeiter produzieren hier pro Jahr rund 6 Mrd. Tabletten, Kapseln und Dragees sowie rund 200 Mio. Packungen in mehr als 3.000 verschiedenen Aufmachungen für mehr als 175 Länder. Beim Umweltschutz und Nachhaltigkeit ist der Standort Vorreiter in der pharmazeutischen Industrie. Eines der Unternehmensziele von Pfizer, die Nachhaltigkeit, wird durch effiziente, ressourcen- und umweltschonende Produktionsprozesse erreicht. Dabei werden auch die Bedürfnisse der Mitarbeiterinnen und Mitarbeiter mit einbezogen.

- Großserienfertigung ,
- Prozessindustrie
- Entwicklung / Konstruktion ,
- Produktionsplanung / -steuerung ,
- Produktionslogistik ,
- Verarbeitungsprozess
- Energiekonzept ,
- Prozessinnovation ,
- Prozessoptimierung ,
- Green Supply Chain Management ,
- Lean Management ,
- Industrie 4.0 / Digitalisierung
- Energie ,
- Material ,
- Abgas
- taktisch (1 bis 5 Jahre)