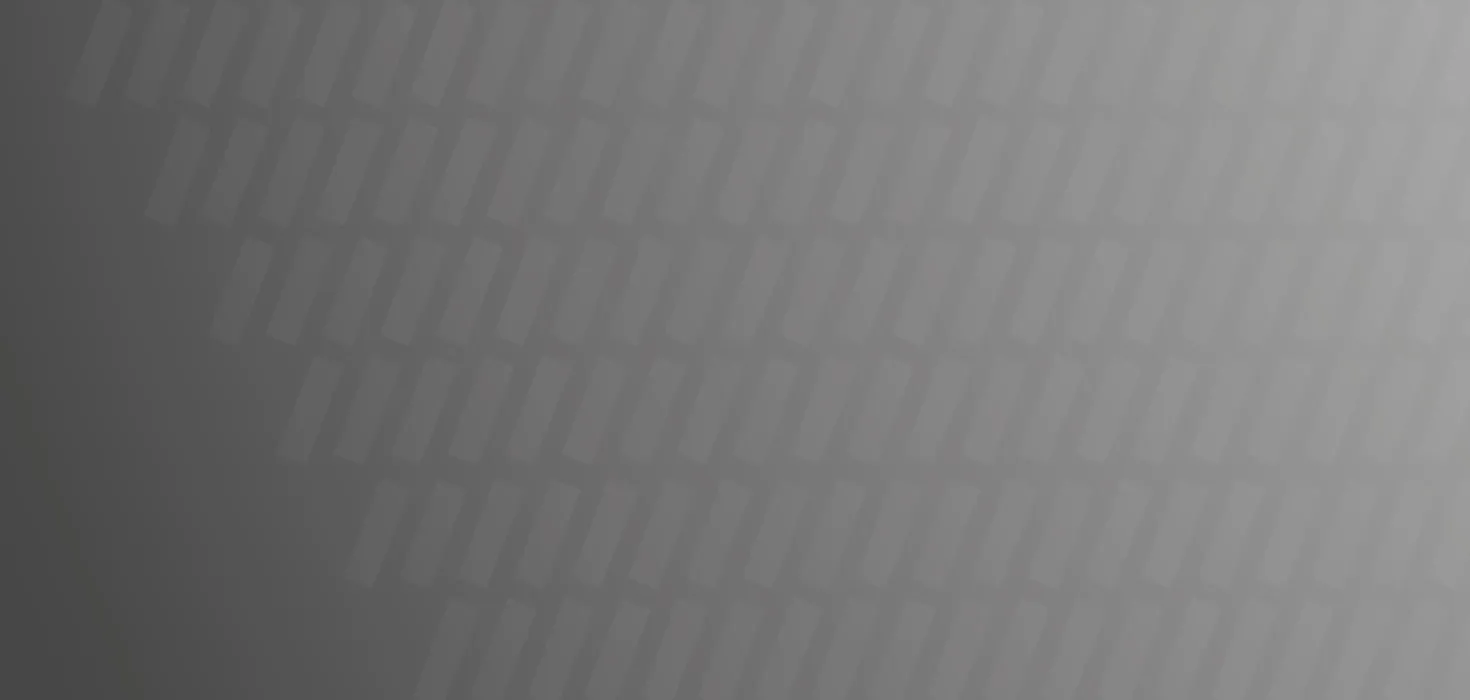
Energetische, stoffliche und nachhaltige Verwendung von Abfall-Kondensat
Prüffeldneubau unter Berücksichtigung vorhandener Abfallströme
Energieeinsparung
CO2-äquivalente Reduktion
Bedarfsreduktion von aufbereitetem Wasser
Die FUCHS SCHMIERSTOFFE GMBH stellt Schmierstoffe her. Am Standort Mannheim sollte nun ein neues Prüffeldgebäude gebaut werden. Dabei ergab es Sinn, sich mit der zukünftigen Energieeffizienz des Gebäudes auseinanderzusetzen. Das Unternehmen kann nach einer ausführlichen Analyse das Heißkondensat eines benachbarten Werkteils für den Betrieb des Kühlturms des neuen Gebäudes weiterverwenden.
Die FUCHS SCHMIERSTOFFE GMBH stellt Schmierstoffe und verwandte Spezialitäten in vier deutschen Werken her. Am Standort Mannheim sollte ein neues Prüffeldgebäude mit 1.200 m² Nutzfläche für 10 bis 15 zusätzliche Prüfstände zur mechanischen Erprobung von Schmierstoffen erbaut werden. Dabei sollte auch ein besonderes Augenmerk auf den zukünftigen nachhaltigen Betrieb des Gebäudes gelegt werden. Maßnahmen wie Gebäudedämmung, LED-Beleuchtung und Lüftungsanlagen mit maximaler Wärmerückgewinnung waren eingeplant.
Zur Kühlung der Prüfstände, die Spitzenleistungen bis 1,5 MW erbringen, wurde ein möglichst energieeffizientes Kühl- und Kaltwassernetz mit geregelten energieeffizienten Pumpen und zwei Temperaturniveaus mit Kühlturm und Kältemaschinen projektiert. Das Gebäude sollte ursprünglich – wie am Standort üblich – mit Ferndampf beheizt werden. In der Planungsphase fiel jedoch auf, dass in der benachbarten Produktion große Mengen an Heißkondensat anfallen, die bis dato ungenutzt blieben und lediglich gekühlt und ins Abwasser eingeleitet wurden. Dieses Kondensat entsteht bei der bestehenden Nutzung von Sattdampf als Prozesswärme für Produktion und Liegenschaften.
Das Kondensat bringt jedoch zwei für das neue Prüffeldgebäude relevante Eigenschaften mit: Es enthält aufgrund der hohen Temperatur noch eine große Menge nutzbarer Energie und ist als Kondensat vollentsalzt, so dass es ideal für den Betrieb des Kühlturms und einer adiabatischen Luftkühlung verwendet werden kann.
Maßnahmen zur nachhaltigen Verbesserung der Energiebilanz eines technischen Gebäudes lassen sich am effizientesten realisieren, wenn sie bereits in der Planungsphase berücksichtigt werden. Daher wurde die Nutzung des Abfallkondensats explizit in einer zusätzlichen Planungsrunde in das Bauvorhaben eingebunden. Dadurch sollte es gelingen, den maximalen Wärmeinhalt des Heißkondensats zu entnehmen und gleichzeitig möglichst viel des dann abgekühlten Kondensats als Speisewasser einzusetzen. Im Rahmen einer Gesamtplanung des Werksteils sollten weitere Abnehmer von Wärme auf niedrigerem Temperaturniveau identifiziert werden, sowie ein sicherer Sommerbetrieb gewährleistet werden.
Das Heißkondensat wird aus der Bestandsleitung in zwei Sammeltanks mit je 30 m³ Volumen gepumpt. Von dort wird es dem Prüffeldgebäude zugeleitet und versorgt dort über Wärmetauscher sowohl die Lüftungsanlagen, als auch die Heizkörper und Deckenluftheizer. Dabei wird das Kondensat auf minimal 50 °C abgekühlt und im Anschluss teilweise als Warmkondensat zur Heizung eines kleinen Nebengebäudes und zur Frostfreihaltung, sowohl des Kühlturms, als auch eines benachbarten Lagergebäudes mit 900 m² Fläche, genutzt.
Nach dieser zweiten energetischen Nutzung strömt das Kondensat mit ca. 30 bis 40 °C über einen Kühler in einen Kaltkondensattank mit 5 m³ Volumen. Aus dem Kaltkondensattank wird das vollentsalzte Wasser bei Bedarf zur Nachspeisung des Kühlturms (max. 4 m³/h) entnommen. Das Kaltkondensat dient zusätzlich noch für den Betrieb einer adiabatischen Abluftkühlung, die mittels Kreuzstromwärmetauscher dafür sorgt, dass die Zuluft für das Prüffeldgebäude im Sommer vorgekühlt ist und damit den Kältebedarf signifikant reduziert. Überschüssiges Kondensat wird ins Abwasser eingeleitet.
Um den jahreszeitlich unterschiedlichen Kalt- und Heißkondensatbedarf zu berücksichtigen, kann einer der beiden Heißkondensattanks auch als Warmkondensatspeicher dienen. Das Heißkondensat wird überdies stofflich und thermisch bei Bedarf zur Befeuchtung eines Gebäudeteils genutzt, bei dem aus Prozessgründen die Luftfeuchte geregelt werden muss. Die gesamte Anlage wird mit einem modernen Mess-, Steuer- und Regelsystem (MSR) überwacht und gesteuert, das auch detaillierte Analysen der Stoff- und Energieströme erlaubt. Damit soll die Effizienz des Systems bei wechselnden Randbedingungen (Witterung, Kühlbedarf der Prüfstände, Heißkondensatanfall, etc.) sichergestellt werden.
Die thermische Nutzung des Heißkondensats reduziert den jährlichen Bedarf an Ferndampf zur Heizung des Prüffeldgebäudes und der Nebengebäude signifikant um über 40 %. Die elektrische Frostfreihaltung eines Lagergebäudes entfällt völlig. In Summe werden ca. 130 MWh jährlich eingespart, das entspricht einem CO 2 - Äquivalent von rund 18 t/Jahr.
Auch die Nutzung als Speisewasser für den Kühlturm und die adiabatische Luftkühlung lohnt sich. Das (abgekühlte) Kondensat ist als vollentsalztes Wasser ideal geeignet, in diesen Anlagen zu verdunsten, um die Enthalpie zur Kühlung zu nutzen. Damit reduziert sich einerseits der Bedarf an aufbereitetem Wasser um rund 1.000 m³/Jahr, zum anderen reduziert sich der Abschlämmbedarf wegen reduzierter Salzanreicherung. Auch die bisherigen Abwasser- und Kühlkosten für das Abfallkondensat entfallen weitgehend.
Das neue Prüffeldgebäude wurde im Februar 2017 in Betrieb genommen. Die Ausstattung der Technischen Gebäudeausrüstung (TGA), zu der die Nutzung des Abfallkondensats gehört, befindet sich noch in der Erprobung. Zudem sind erst einige Prüfstände eingezogen, so dass bisher nur ein kleiner Teil der im Endausbau erwarteten Kühlleistung anfällt. Daher ist es zu früh, einen Vergleich zwischen Erwartungen und Erreichtem zu ziehen.
Allerdings hat sich erwiesen, dass die Gebäudeheizung mittels Abfallkondensat und Energierückgewinnung über Kreuzstromwärmetauscher seit Oktober 2016 zumindest prinzipiell funktioniert. Bei kälterer Witterung im Winter 2016/2017 musste aber zusätzliche Heizenergie in Form von Ferndampf zugeführt werden. Das hängt auch damit zusammen, dass der tatsächliche Heißkondensatanfall im Werk hinter den Planungserwartungen zurückblieb. Das verlängert zwar die Amortisationszeit des Konzepts, nicht aber die prinzipielle Eignung zur nachhaltigen Ressourcenschonung. Zukünftig wird die stoffliche Weiterverwendung des anfallenden Kondensats in einzelnen Bereichen anderer Werksteile angestrebt.
FUCHS entwickelt, produziert und vertreibt ein Vollsortiment an Schmierstoffen und verwandten Spezialitäten für nahezu alle Industrien und Anwendungsbereiche. Im Jahr 1931 als Familienunternehmen in Mannheim gegründet, firmieren heute 57 operative Gesellschaften unter dem Dach der FUCHS PETROLUB SE mit rund 5.000 Mitarbeiterinnen und Mitarbeitern in mehr als 40 Ländern. FUCHS ist der weltweit größte Anbieter unter den unabhängigen Schmierstoffherstellern.
Zu den weltweit mehr als 100.000 Kunden zählen unter anderem Automobilzulieferer und OEMs, Unternehmen aus den Bereichen Maschinenbau, Metallverarbeitung, Bergbau und Exploration, Luft- und Raumfahrt, Unternehmen des Energie-, Konstruktions- und Transportsektors, der Land- und Forstwirtschaft sowie der Stahl-, Metall-, Zement-, Guss- und Schmiedeindustrie, aber auch Lebensmittel- und Glashersteller. FUCHS-Schmierstoffe sind maßgeschneidert, stehen für Leistung und Nachhaltigkeit, Sicherheit und Zuverlässigkeit, Effizienz und Kostenersparnis und erfüllen höchste Qualitätsanforderungen.
Die FUCHS SCHMIERSTOFFE GMBH ist eine 100-prozentige Tochter des weltweit agierenden Schmierstoffherstellers FUCHS PETROLUB SE, mit Stammsitz in Mannheim. Als größte Tochtergesellschaft des FUCHS-Konzerns mit mehr als 800 Mitarbeiterinnen und Mitarbeitern entwickelt und vertreibt die FUCHS SCHMIERSTOFFE GMBH qualitativ hochwertige Schmierstoffe und benachbarte chemische Spezialitäten für den deutschen und internationalen Markt.

- Prozessindustrie
- Unterstützungsprozesse / Gebäudemanagement
- GreenTech BW ,
- Dämmung / Isolation ,
- Prozessoptimierung ,
- Stoffkreislauf / Recycling
- Energie ,
- Material ,
- Trinkwasser ,
- Abwasser ,
- Abgas
- taktisch (1 bis 5 Jahre)