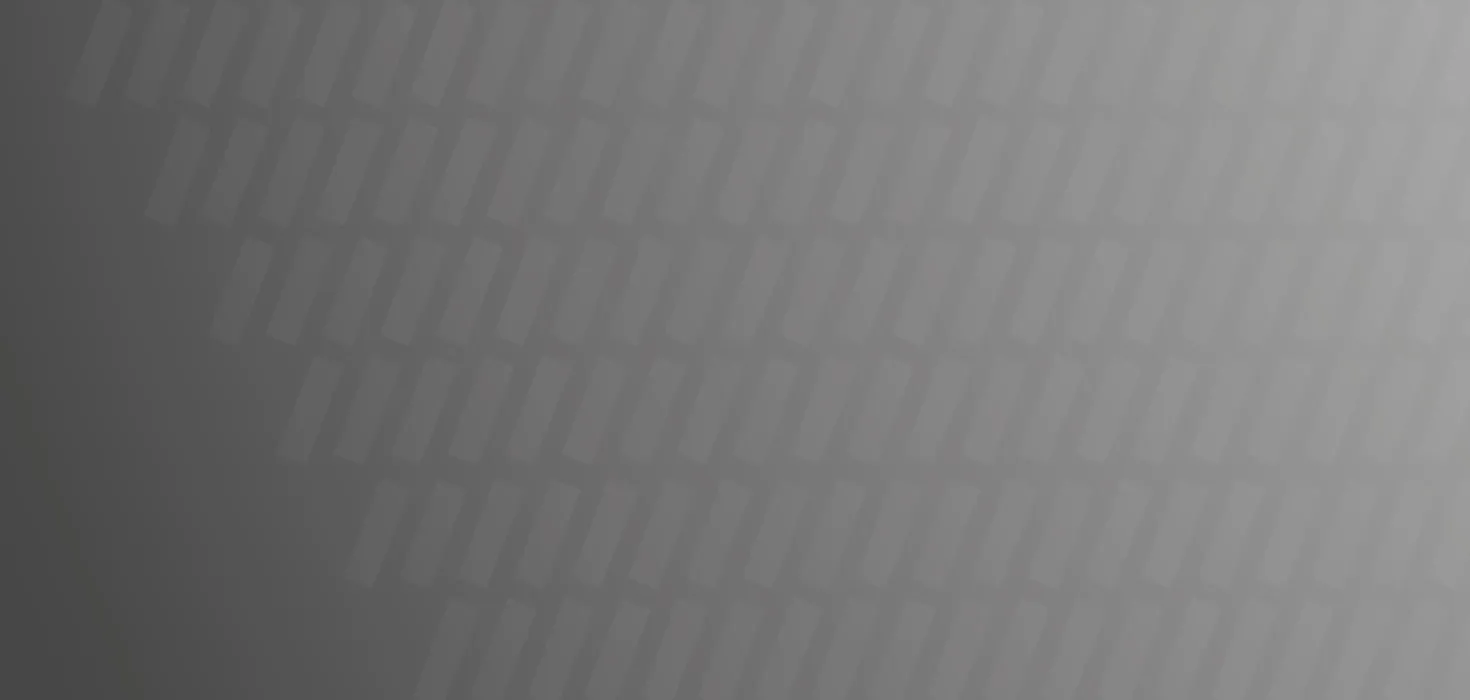
Von der Faser direkt zum Formteil
Entwicklung des neuen effizienten Herstellverfahrens FIM (Fiber Injection Molding)
Materialeinsparung
Die Fiber Engineering GmbH hat sich darauf spezialisiert, mit der Fiber Injection Molding Technologie Faserformteile materialeffizient herzustellen. Das Verfahren wurde so entwickelt, dass ein breites Anwendungsspektrum abgedeckt wird, damit langfristig möglichst viele Märkte damit erschlossen werden können. Auch für die Zukunft besteht ein hohes Potenzial, den Prozess noch weiterzuentwickeln.
Seit über 50 Jahren werden Faserformteile aus vorgefertigten Matten gepresst und geschnitten. Diese Formteile werden als akustische und/oder thermische Isolationen beispielsweise in der Medizin-, Möbel-, Textil-, und Luftfahrtbranche verwendet. Dabei haben Faserformteile vielfältige und flexible Anwendungsmöglichen, beispielsweise als Dämmkissen, Sitzkissen, Bodenisolierungen in Fahrzeugen, Pads in BHs und als geformte feste Trägerteile aus Holzfasern.
Die Fertigung der Matten und die Endfertigung von Formteilen sind oft räumlich sehr weit voneinander entfernt. Die voluminösen Matten müssen daher erst per Lkw zum Endverarbeitungsort transportiert werden. Bei der Verarbeitung selbst fallen dann meistens große Mengen an Verschnitt an, die entweder wieder zurück zur Mattenfertigung gelangen, oder entsorgt werden. Neben Fasern aus Textilrecycling werden immer mehr Fasern aus nachwachsenden Rohstoffen verarbeitet, wodurch die CO2-Bilanz verbessert wird. Flachs und Hanf werden bevorzugt für feste Trägerteile genutzt und Schafwolle für akustische Dämmplatten im Deckenbereich.
In den letzten Jahren wurden verstärkt Polyurethane (PUR) Schaumstoffe als Ersatz von Faserformteilen eingesetzt. Die bei der Herstellung eingesetzten Chemikalien sind toxisch und daher unter Umwelt- und Arbeitsschutzaspekten als problematisch anzusehen.
Zudem ist bei PUR-Schaumstoffen kein sinnvolles Recycling möglich. Die Basisstoffe des PUR sind Isocyanat und Polyol und bestehen zu über 95 % aus Rohöl.
Ein Faserballen wird geöffnet und mit einer Bindefaser homogen gemischt. Dieses Fasergemisch wird in einen Spalt zwischen fast geschlossenem Ober- und Unterwerkzeug über einen gelenkten Faserstrom eingeblasen. Die Werkzeuge bestehen aus Lochblech, durch das die Luft entweichen kann, aber die Fasern in der Form zurückhält. Nach dem kompletten Füllen der Kavität wird durch das Lochblech von außen ein heißer Luftstrom in das eingeblasene Fasermaterial gelenkt, wodurch die Bindefaser schmilzt und sich mit der Matrixfaser verbindet. Nach dem kurzzeitigen Heizen wird Umgebungsluft zum Abkühlen ebenfalls durch das Lochblech gezogen.
Die Lochblechwerkzeuge haben eine geringe Masse, die sich nur unwesentlich erwärmt. Somit kann fast die gesamte Heizenergie zur Aktivierung des Fasermaterials verwendet werden.
Eine Weiterentwicklung entstand mit einer speziellen Einblasoberform als dritte Werkzeugform. Nur damit können reproduzierbar sehr genaue Dichtevariationen innerhalb eines 3D Formteils erzeugt werden. Dadurch wird es möglich, nur so viel Material gezielt lokal einzusetzen, wie gerade nötig ist. Daraus resultiert das Kernpatent der Fasereinblastechnik, das mittlerweile in über 30 Ländern patentiert ist.
Erste Versuche an einer einfachen Form zeigten, dass der Faserstrom über spezielle Düsen in den Spalt gelenkt werden muss. Dadurch kann fast jede Geometrie von außen über den Rand komplett gefüllt werden. Die Bewegungen der Schwenk- und Lineardüsen werden über ein einfaches Füllprogramm mit einer speicherprogrammierbaren Steuerung (SPS) genau vorgegeben, so dass ein vollautomatisches Füllen möglich ist. Die Steuerungssoftware wurde ebenfalls neu entwickelt und bietet eine einfache Plattform, die es auch Personen ohne Programmierkenntnisse erlaubt, schnell und einfach entsprechende Füllprogramme zu entwickeln oder bestehende zu modifizieren.
Um die Serienreife zu demonstrieren, wurde im Technikum eine entsprechende seriennahe Anlage aufgebaut. Dazu sind weitere nötige Komponenten wie Dosierschächte und Blasmaschinen zu einem System entwickelt worden. Auf der Technikumsanlage können gemeinsam mit Kunden nach deren Spezifikationen vorgegebene Formteile entwickelt und bis zu einer Kleinserie auch gefertigt werden. Damit können die Einsparziele an realen Bauteilen leicht überprüft werden, sowie erste Markterkenntnisse durch Prototypenserien gewonnen werden. Für größere Stückzahlen werden Serienwerkzeuge zusammen mit einer Großserienanlage an unsere Kunden verkauft.
Die erste Großserienanlage wurde gemeinsam mit dem Maschinenbauer Robert Bürkle GmbH aus Freudenstadt realisiert. Der Kunde war ein Automobilzulieferer aus den USA, der mit der Anlage Dämmteile für den VW Passat fertigte.

Die Einsparungen sind von der Komplexität und Größe des Faserformteils abhängig. Allen gemeinsam ist die Einsparung der Halbzeugfertigung in Form von Matten, da die Fasern ohne Umweg direkt in die Werkzeugformen eingeblasen werden.
An einem Bauteil soll das Einsparpotenzial, das sich mit der Einblastechnologie FIM bietet, exemplarisch aufgezeigt werden. Hierbei wurde ein bestehendes PUR-Schaumteil durch ein komplexes Faserformteil ersetzt. Das Faserformteil wurde konturgenau gefertigt, d. h., ohne den zusätzlichen Schritt des Stanzens. Es entsteht kein Abfall, damit wird eine hundertprozentige Verwertung des ein - gesetzten Materials erreicht.
Durch die Festlegung einer höheren Dichte in den Außenbereichen wird eine sichere Befestigung ermöglicht. Im Innenbereich konnte die Dichte wesentlich reduziert werden, wodurch das Gesamtgewicht von 200 g auf 100 g gesenkt werden konnte. Neben der Materialeinsparung von 50 % können durch den vollautomatischen Prozess die Personalkosten gesenkt werden.
Durch die Substitution des PUR-Schaums mit Polyesterfasern wird i. d. R. ein um 30 % geringeres Teilegewicht erreicht. Erste Anwendungen als Polsterersatz im Automobil sind in der Testphase. Für Kindertrageschalen wurden bereits mehrere Modelle entwickelt, die sich derzeit in der Übergangsphase zur Serienfertigung befinden.
Durch die Vielzahl an Anwendungsmöglichkeiten in den unterschiedlichen Branchen ergeben sich jedes Mal neue Herausforderungen und tiefe Einblicke in völlig andere Fertigungsprozesse. Da FIM relativ neu ist, besteht sicher noch ein großes Potenzial, diesen Prozess immer weiter zu optimieren, obwohl er bereits jetzt bestehende Technologien in der Effizienz überholt hat.
Die bestehenden Technologien sind beim Fortschritt mit der Fasereinblastechnik das größte Hemmnis, da diese großen Investitionen sich zum Teil noch nicht amortisiert haben.
Die positive Resonanz selbst aus Südkorea zeigt, dass die Fiber Engineering mit FIM die richtige Technologie zur Ressourceneffizienz geschaffen hat. Die ersten Kunden haben das Potenzial erkannt und betreiben gemeinsam mit uns die Entwicklung an entsprechenden Formteilen.
Die Fiber Engineering GmbH hat sich darauf spezialisiert, mit der FIM Technologie 3D Faserformteile effizient herzustellen. Dazu werden gemeinsam mit Kunden aus den Bereichen Automobil, Möbel, Textil, Design, Medizin u. a. zunächst Formteile entwickelt, am Markt getestet und dann in Serie gefertigt.
Darüber hinaus werden Werkzeuge und Anlagen für Großserienfertigung angeboten. Damit wird den Kunden ermöglicht, diese Teile selbst herzustellen. Außerdem verbreitet sich so das neue Fertigungsprinzip und wird zum Multiplikator bei der Ressourceneinsparung. Die Anlagen wurden hochflexibel entwickelt, so dass mit einem einfachen Werkzeugwechsel die Produktion in kurzer Zeit umgestellt werden kann.
- Kleinserienfertigung
- Entwicklung / Konstruktion ,
- Verarbeitungsprozess
- Prozessinnovation
- Material ,
- Kunststoffe ,
- Abgas
- taktisch (1 bis 5 Jahre)