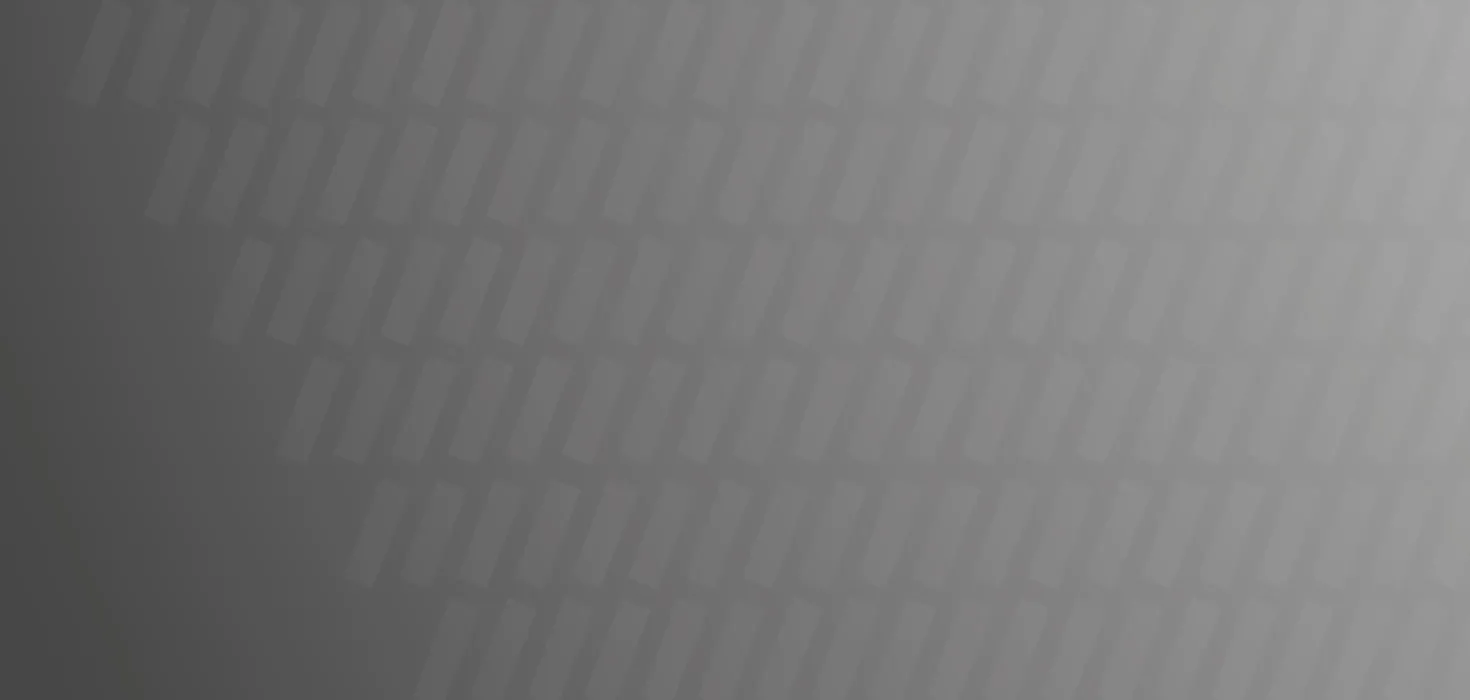
Ganzheitliche Ressourceneffizienz in Fabrikplanung und -betrieb
Konsequente Integration von Ressourceneffizienz in Planungs- und Betriebsstrategien
Die Festo AG hat sich auf die Entwicklung von Automatisierungstechnik spezialisiert. Das Unternehmen will langfristig Ressourceneffizienz in seine Planungs- und Betreibstrategien einbauen. Dabei wurde sowohl ein Konzept für Ressourceneffizienz des Gebäudes als auch für den späteren Produktionsbetreib erarbeitet. In den nächsten Jahren soll so rund ein Viertel der CO2-Emissionen eingespart werden.
Seit mehr als 60 Jahren setzt Festo Impulse für die Automatisierungstechnik. Mit weniger Aufwand und Ressourcen zu produzieren ist dabei eine grundlegende Zielsetzung, die auch einer nachhaltigen Entwicklung Rechnung trägt. Langfristiges Denken und verantwortungsbewusstes Handeln sind dabei wichtige Grundsätze im ganzheitlichen unternehmerischen Denken des Familienunternehmens. Das Werk, in dem Ventile, Ventilinseln und Elektronik produziert werden, konnte von Grund auf neu geplant werden.
Bei der Fabrikplanung wurde die ökologische Zielsetzung und damit das Teilprojekt „Energie und Umwelt“ von Anfang gleichberechtigt mit anderen Zielsetzungen wie intelligente Automation und schlanke Produktion gestellt. In einer interdisziplinären Arbeitsgruppe arbeiteten interne Experten aus den Bereichen Produktion, Gebäudemanagement, Energie und Umweltmanagement sowie Forschung zusammen. Die Spezialisten aus den unterschiedlichsten Bereichen haben das Konzept für die ganzheitliche Ressourceneffizienz des Gebäudes und des späteren Produktionsbetriebs erarbeitet.
Gemeinsam mit Wissenschaftlern des Instituts für Werkzeugmaschinen und Fertigungstechnik (IWF) der Technischen Universität Braunschweig wurde das systematische Planungsvorgehen und die zentralen Methoden und Werkzeuge festgelegt. Die gebäude- und produktionstechnischen Aspekte sowie unterschiedlichste Maßnahmen wurden nach ökologischen und ökonomischen Kriterien sowie in ihrer ganzheitlichen Wirkung in der Fabrik bewertet. Ein Sankey-Diagramm für Gebäude und Produktionsprozesse sowie ein Bewertungstool zur Berechnung der Fabriklebenszykluskosten waren zentrale Instrumente der Planung.
Aus den detaillierten Voruntersuchungen wurden drei unterschiedliche Investitionspakete entwickelt. Das Projektteam bezifferte diese in verschiedenen Zukunftsszenarien hinsichtlich Effizienz und Amortisation des gesamten Werkes und verglich sie mit einem Planungsreferenzstandard. Dabei wurden Energiepreisentwicklungsszenarien berücksichtigt. Weil die Amortisation des gesamten Investitionspaketes bewertet wurde, konnten Ideen realisiert werden, deren Amortisation deutlich über dem üblichen Zeitrahmen lag.
Festo legt Wert darauf, in nationalen und europäischen Forschungsprojekten an der Automatisierung der Zukunft mit zu forschen. Bei der Planung der Technologiefabrik wurden die Forschungsergebnisse aus den EU-/BMBFForschungsprojekten „Energieeffizienz in der Produktion im Bereich Antriebs- und Handhabungstechnik (EnEffAH)“, „Eco Manufactured Transportation Means from Clean and Competitive Factory (EMC2 Factory)“ und „Metamorphose zur intelligenten und vernetzten Fabrik (MetamoFAB)“ eingebracht und angewendet. 2015 wurde die Technologiefabrik in Ostfildern–Scharnhausen, in der 1.200 Mitarbeiter auf vier Ebenen mit insgesamt 66.000 m² produzieren, eingeweiht.
Bei der Gebäudeinfrastruktur sind folgende Maßnahmen beispielhaft zu nennen:
- Eigenenergieerzeugung durch Blockheizkraftwerke, die aus Gas elektrische Energie und Wärme für Produktionsprozesse und Klimatisierung erzeugen
- Betonkernaktivierung, die mit Produktionsabwärme gespeist wird
- konsequente Nutzung von Regenwasser für Ressourceneffizienz.
Umweltfreundliche Maßnahmen in der Produktion sind eine hocheffiziente Drucklufterzeugung und die umweltfreundliche Gestaltung des üblicherweise kritischen Prozesses der Galvanisierung. Weiterhin wurde – wo anwendbar – Minimalmengenschmierung statt konventioneller Kühlschmierstoffe verwendet bzw. der Verbrauch durch eine bedarfsgerechte Dosierung reduziert. Der Strom- und Druckluftverbrauch auf Produktionsprozessebene wird kontinuierlich erfasst und überwacht (Monitoring).
Weil Energieeffizienz nicht nur eine Sache der Hardware, sondern im Produktionsalltag vor allem auch eine Sache des Bewusstseins und Verhaltens ist, durchlaufen die Mitarbeiter in der werkseigenen Lernfabrik Schulungen zur Energieeffizienz. Am Lernstand erlernen sie Einsparmöglichkeiten bei der täglichen Verwendung von Druckluft. Den Mitarbeitern wird dadurch z. B. bewusst, wie viel Druckluft bei der Entlüftung von Schläuchen verloren geht und dass bei der Teilereinigung ein höherer Druck nicht immer zu einem besseren Reinigungsergebnis führt.
Laut den Hochrechnungen sollen in den nächsten 20 Jahren rund 7 % Energie (Strom und Gas) eingespart werden. Dies entspricht im Vergleich einer Reduktion der CO2-Emissionen um 23 % beziehungsweise um etwa 78.000 t.
Die Technologiefabrik wurde 2015 mit dem höchsten Zertifizierungsstatus „Platin“ der Deutschen Gesellschaft für Nachhaltiges Bauen (DGNB) ausgezeichnet, der die Themenfelder Ökologie, Ökonomie, soziokulturelle und funktionale Aspekte, Technik und Prozesse umfasst.
Der wahrscheinlich wichtigste Grundstein für die ressourceneffiziente Fabrik wurde mit der ökologischen Zielsetzung und der Gründung einer Arbeitsgruppe „Energie und Umwelt“ auf höchster Projektebene gelegt.
Der Schlüssel liegt darin, die Gebäudeinfrastruktur und die zukünftigen Produktionsprozesse gemeinsam zu betrachten. Wenn die Nutzungsstrategie des Gebäudes und die Auslegung der technischen Gebäudeausrüstung genau aufeinander abgestimmt sind, können Ressourcen bestmöglich genutzt werden. Dabei sollten die Spezialisten aller relevanten Bereiche eng zusammenarbeiten.
Zusätzlich ist im Festo Produktionssystem ein Energie- und Umweltteam mit der methodischen Unterstützung der Produktionsbereiche betraut. Dort werden pilothafte Maßnahmen fortlaufend entwickelt und erprobt und erfolgreiche weltweit ausgerollt. Die Technologiefabrik nimmt weltweit eine Vorreiterrolle ein. Externe Besucher können die Energiesparansätze in Gebäude und Produktion in einem Energieeffizienzrundgang vor Ort besichtigen.
Die Festo AG ist gleichzeitig Global Player und unabhängiges Familienunternehmen mit Sitz in Esslingen am Neckar. Das Unternehmen liefert pneumatische und elektrische Automatisierungstechnik für 300.000 Kunden der Fabrik- und Prozessautomatisierung in über 35 Branchen. Produkte und Services sind in 176 Ländern der Erde erhältlich. Weltweit rund 18.700 Mitarbeiter in 61 Landesgesellschaften erwirtschafteten im Jahre 2015 einen Umsatz von rund 2,64 Mrd. Euro. Davon werden jährlich rund 8 % in Forschung und Entwicklung investiert. Im Lernunternehmen beträgt der Anteil der Aus- und Weiterbildungsmaßnahmen 1,5 % vom Umsatz. Lernangebote bestehen aber nicht nur für Mitarbeiter: Mit der Festo Didactic SE bringt man Automatisierungstechnik in industriellen Aus- und Weiterbildungsprogrammen auch Kunden, Studierenden und Auszubildenden näher.

- Großserienfertigung
- Unterstützungsprozesse / Gebäudemanagement
- GreenTech BW ,
- Prozessinnovation
- Energie ,
- Material ,
- Trinkwasser ,
- Chemieprodukte ,
- Holz, Karton und Papier ,
- Abgas
- taktisch (1 bis 5 Jahre)