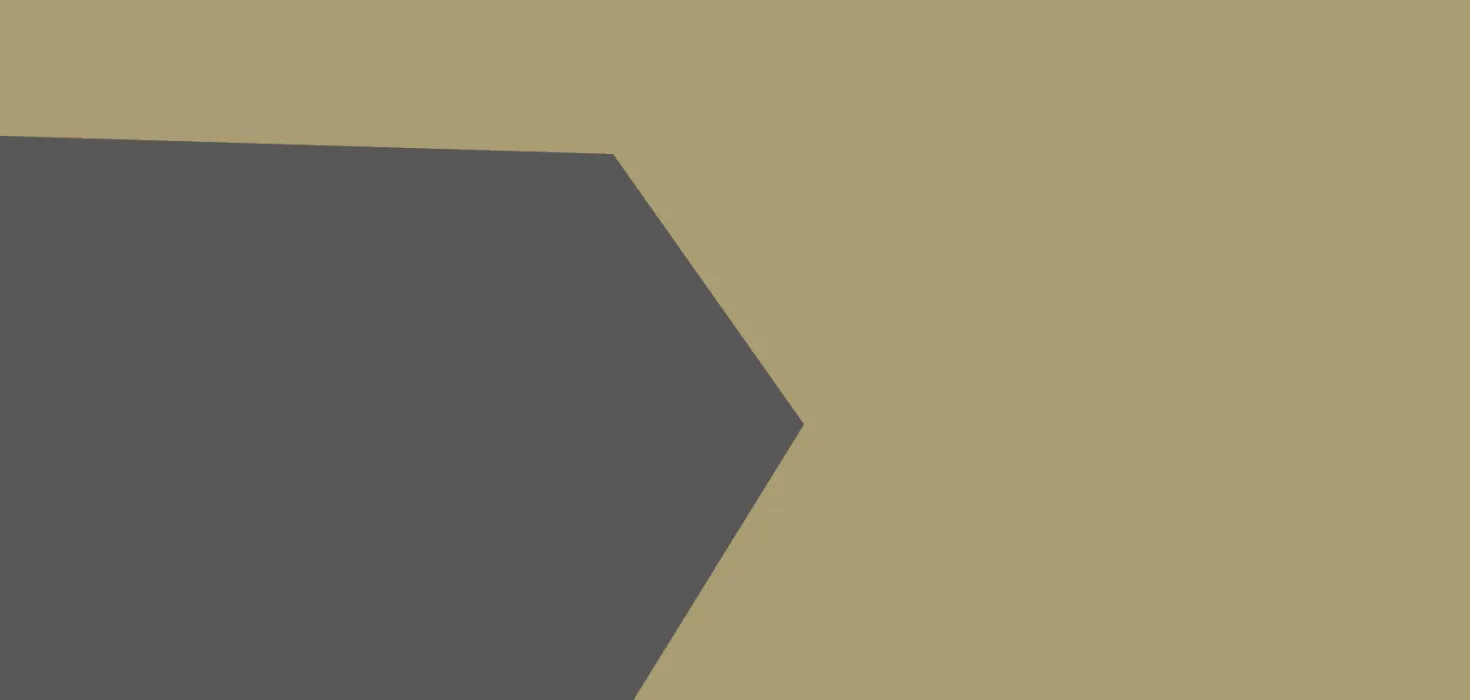
Herstellung ressourceneffizienter Ölnebelfilter aus plissiertem Mikroglasvlies
Glasfasermaterialeinsparung
Kunststoffeinsparung
Stahlblecheinsparung
CO2-Einsparung
Eine neue Plissiermaschine für Microglasvlies reduziert die benötigte Materialmenge pro Filterprodukt und erhöht dessen Filterleistung.
Kostenvorteile
22.000 EUR/a Materialkosten
5.200 EUR Energiekosten pro 3 a Nutzungsdauer einer Patrone
Investition
400.000 EUR
Die Firma Junker-Filter GmbH stellt im baden-württembergischen Sinsheim unter anderem Ölnebelfilter zur industriellen Abluftreinigung her. Die patronenförmigen Filter bestehen aus etwa 4 Kilogramm Glaswolle, 2 Kilogramm Kunststoff sowie 3,5 Kilogramm Stahl. Eine Reduktion des Materialbedarfs bei gleichzeitiger Leistungssteigerung kann durch das Plissieren (Falten) des Filtermediums erreicht werden.
Die bisher als Filtermedium verwendete Glaswolle ist aufgrund ihrer mechanischen Eigenschaften nicht für das Plissieren geeignet. Die Verarbeitung von neu entwickelten, plissierbaren Filtermedien aus Mikroglasvlies war jedoch auf der bestehenden, in die Jahre gekommenen Plissiermaschine nicht möglich.
Die Neuinvestition in eine moderne Plissiermaschine soll die prozesssichere Verarbeitung des empfindlichen Mikroglasvlieses und die Hebung des damit verbundenen Effizienzpotenzials der Filterpatronen ermöglichen.
Infolge einer Marktanalyse und der Spezifikation der Plissiermaschine, wurde der Auftrag an den Schweizer Maschinenbauer JCEM GmbH vergeben. Nach der Fertigstellung der Plissiermaschine und der Umbaumaßnahmen am Einsatzort wurde die Plissiermaschine vertragsgemäß geliefert und aufgebaut. Im Anschluss an die Inbetriebnahmeprüfung wurden mehrere Testpatronen produziert und in einem Ölnebelprüfstand untersucht.
Durch das neue Filtermedium und den neuen Aufbau der Ölnebelpatrone kann der Druckverlust auch bei doppeltem Luftdurchsatz auf weniger als 50 Prozent des Werts der bisherigen Patrone gesenkt werden. Somit ergibt sich eine Reduktion des spezifischen Energiebedarfs auf etwa 25 Prozent und eine Reduzierung der benötigten Patronen auf die Hälfte. Unter Berücksichtigung der benötigten Patronenanzahl wird für die gleiche Filtrationsleistung nur rund ein Viertel des bisher verwendeten Glasfasermaterials eingesetzt. Derzeit wird von einer jährlichen Einsparung von etwa 6,5 Tonnen Glasfasermaterialien, rund 2,5 Tonnen Kunststoff sowie circa 4,4 Tonnen Stahlblech ausgegangen, was einer CO2-Einsparung von fast 17 Tonnen entspricht. Die höchste Energie und CO2-Einsparung werden jedoch in der Nutzungsphase der Patronen erzielt werden. Bei 1.000 Patronen Jahresabsatz werden über eine Lebensdauer von etwa drei Jahren bis zu bis zu 34,7 Gigawattstunden Strom und 17.300 Tonnen CO2 eingespart.
Aufgrund der Anforderung, als Automobilzulieferer die Gefahr von lackbenetzungsstörenden Substanzen (LABS) zu vermeiden, war eine ungeplante Sanierung der Halle notwendig. Eine große Herausforderung war auch das enge Zeitfenster zwischen Bewilligung des Projekts und dem festgesetzten Projektende.
Im Jahr 1956 gründete Adolf Junker in Obergimpern, heute Ortsteil von Bad Rappenau, in einem Raum von 20 Quadratmeter die Einzelfirma Junker-Filter. Im Jahr 1971 siedelte das Unternehmen in eine errichtete Fertigungsstätte nach Sinsheim um. 1989 verstirbt unerwartet der Firmengründer Adolf Junker und sein Sohn Jürgen Junker übernimmt die komplette Verantwortung für das Unternehmen. 2019 hat das seit 1978 als GmbH firmierende Unternehmen der Umwelttechnikbranche eine Mitarbeiterzahl von 110 erreicht, davon über zehn Auszubildende und Werksstudierenden. Der Umsatz betrug in 2018 über 16 Millionen Euro. Junker-Filter entwickelt innovative Konzepte nach Maß für den Einsatz von technischen Textilien für modernste Entstaubungssysteme und Anlagen in der Fest-Flüssig-Trennung.
- Großserienfertigung
- Entwicklung / Konstruktion ,
- Verarbeitungsprozess
- GreenTech BW ,
- Produktinnovation ,
- Prozessoptimierung
- Energie ,
- Prozessenergie ,
- Material ,
- Metalle ,
- Kunststoffe ,
- Textilprodukte
- strategisch (größer 5 Jahre)