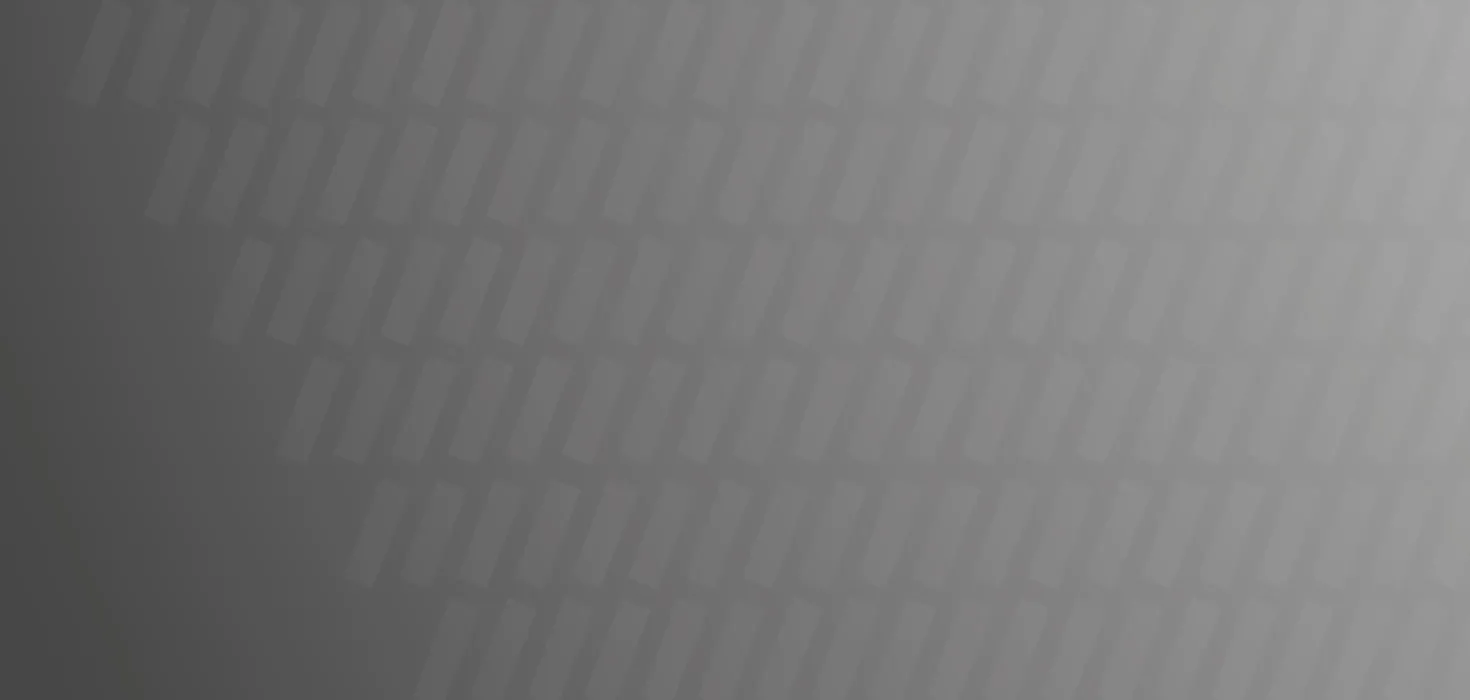
Hybride Bauteilfertigung – Schmieden und Metall 3D-Druck in Kombination
Hybride Kombination aus Freiformschmiedeprozess und selektivem Laserschmelzen (Metall 3D-Druck)
Das mittelständische Unternehmen Rosswag ist die größte Freiformschmiede Süddeutschlands. Da die Herstellung einiger Bauteile bisher mit hohen Materialverlusten verbunden war, hat das Unternehmen sich zum Ziel gesetzt, die Herstellungsverfahren zu optimieren. So wurde die Effizienz bei der Herstellung dieser Bauteile mittels eines hybriden Verfahrens gesteigert und die Kosten reduziert.
Kostenvorteile
ca. 95 %ige Einsparung der Fertigungskosten (bei dem Beispiel des SchmiedeSLM-Hybrid)
Bislang werden mechanisch hochbelastete Bauteile geschmiedet, wärmebehandelt und anschließend mechanisch bearbeitet. Allerdings ist dies bei komplex konstruierten Bauteilen mit einem sehr hohen mechanischen Zerspanungsaufwand und damit hohen Kosten verbunden. Ein anschauliches Beispiel für diese Nachteile ist die Herstellung eines Verdichterrades, so wie es in einer üblichen thermischen Strömungsmaschine zur Stromerzeugung verbaut ist. Hier werden bislang die Strömungsschaufeln aufwendig aus dem massiven Vollmaterial gefräst. Wegen dem hohen Zerspanvolumen und der damit einhergehenden, kostspieligen mechanischen Bearbeitung wird die Herstellung eines Verdichterrades sehr teuer und sehr ressourcenaufwendig. Die Rosswag GmbH hat sich daher zum Ziel gesetzt, die Prozesskette der Herstellungsverfahren zu optimieren und damit die Effizienz bei der Herstellung bestimmter Bauteile zu steigern.
Zukünftig ist es das Ziel der Rosswag GmbH, den massiven Grundkörper für das zu fertigende Bauteil konturnah zu schmieden und mechanisch zu zerspanen. Hierbei muss insbesondere die Fügefläche für den späteren Aufbau vorbereitet werden. Auf diese wird die endkonturnahe, komplexe Geometrie additiv aufgebaut. Dabei ergeben sich durch die neuen Konstruktionsfreiheiten der generativen Fertigung vielfältige geometrische Optimierungsmöglichkeiten. Im Nachgang wird anschließend das Bauteil nochmals an den Funktionsflächen zerspant, um die notwendigen Pass- und Toleranzmaße einzustellen.
Daraus resultiert der zukünftige Fertigungsprozess von speziellen Verdichterradbauteilen, bei welchen der massive Grundkörper geschmiedet und im CNC-Bearbeitungszentrum zerspant wird. Anschließend können die Strömungsschaufeln endkonturnah ergänzt werden. Ihre charakteristische Profilform und die strömungsoptimierte Oberflächenqualität erhält die Schaufel durch eine verhältnismäßig kurze Zerspanung auf dem CNC-Bearbeitungszentrum im Anschluss an den generativen Fertigungsprozess.
Zusätzlich ermöglicht die neu entwickelte und optimierte Prozesskette konstruktive Freiheiten hinsichtlich innenliegender Strukturen. So ist es zum Beispiel möglich, Strömungskanäle zur Grenzschichtbeeinflussung und damit einhergehender Wirkungsgradsteigerung zu fertigen. Diese lassen sich mit konventionellen Fertigungsverfahren grundsätzlich nicht herstellen.
Rosswag hat die bestehenden Restriktionen der beiden Fertigungsverfahren Freiformschmieden und Selektives Laserschmelzen detailliert analysiert und verfolgt nun das Ziel, durch eine optimierte Prozesskette die Effizienz bei der Herstellung bestimmter Bauteile zu steigern. Dies geschieht, indem die Fertigungsverfahren in den jeweiligen Geometrieelementen miteinander kombiniert werden. Bei dieser Kombination werden die Vorteile der Umformtechnik mit der generativen Fertigungstechnik komplementär verbunden. Damit wird eine ressourcen- und kosteneffiziente Herstellung von massiven Bauteilen mit komplexen und auch innenliegenden Strukturen realisiert.
Die erste Umsetzung erfolgte in einer Fallstudie zusammen mit dem Anlagenhersteller SLM Solutions. Hierbei sollten die vielfältigen Möglichkeiten der SLM®-Fertigungsanlagen aufgezeigt werden. Darauf basierend wird in internen Entwicklungsprojekten der Ansatz der hybriden Bauteilfertigung weiter ausgeweitet und auf andere Produkte und Bauteile übertragen.
Die hybride Kombination aus Freiformschmiedeprozess und Selektivem Laserschmelzen ermöglicht eine erhebliche Effizienzsteigerung bei der Herstellung von komplexen Metallbauteilen. Bisher wurden die einzelnen Fertigungsprozesse unabhängig voneinander mit den jeweiligen Nachteilen eingesetzt. Beim Schmiedeprozess und der konventionellen Zerspanung lassen sich vor allem innenliegende Strukturen mit Hinterschneidungen gar nicht oder nur unter größtem Aufwand einbringen. Der generative Fertigungsprozess scheitert hingegen oftmals an der Wirtschaftlichkeit beim Aufbau geometrisch einfacher, massiver Strukturen. Für das Beispiel des Schmiede-SLM-Hybrids bedeutet dies eine Einsparung von ca. 95 % der Fertigungskosten, welche bei der additiven Fertigung des gesamten Bauteils angefallen wären. Durch die erhöhte Ressourceneffizienz des Ausgangsmaterials des generativen Fertigungsprozesses (i. d. R. Metallpulver) und der endkonturnahen Rohteilfertigung kann die Hauptnutzungszeit des CNC-Bearbeitungszentrums, je nach Anforderung, um bis zu 90 % reduziert werden. Dadurch werden auf effiziente Weise Materialabfälle vermieden und Umweltbelastungen werden durch den Einsatz von Kühlschmierstoffen reduziert. Weiterhin können vielfältige Zeit- und Kosteneinsparungen über die gesamte Prozesskette erreicht werden.
Im Rahmen der Neuentwicklung dieser unternehmensweiten, ganzheitlichen Prozesskette für die hybride Bauteilfertigung wurden vielfältige Entwicklungstätigkeiten innerhalb der Rosswag GmbH gebündelt. Dass die Mitarbeiter der traditionell geprägten Schmiedeabteilung mit den Ingenieuren aus der Engineering-Abteilung an einem gemeinsamen Projekt bezüglich additiver Fertigung zusammenarbeiten ist im normalen Tagesgeschäft sonst nicht üblich. Dies wird allen Mitarbeitern positiv in Erinnerung bleiben und stärkt den Zusammenhalt im Unternehmen.
Der Ansatz der hybriden Fertigung wird weiterverfolgt und ist bei zahlreichen, bestehenden Stammkunden aus dem Schmiedebereich auf großes Interesse gestoßen. Hieraus ergeben sich möglicherweise Projekte, welche die hybride Bauteilfertigung innerhalb der Rosswag GmbH weiter vorantreiben und zukünftig Unternehmenswachstum generieren
Darüber hinaus plant Rosswag die Herstellung von individuellen, prozessoptimierten Metallpulvern aus Schmiedeabfällen sowie aus dem 6.000 t umfassenden Materiallager mit über 400 verschiedenen Werkstoffen. Das Unternehmen bietet damit eine einzigartige Prozesskette, welche sich von der Produktion des qualitativ hochwertigen Metallpulvers, über die generative Fertigung, spezifische Wärmebehandlung, CNC-Nacharbeit, Erprobung der mechanisch-technologischen Eigenschaften im hauseigenen Werkstofflabor, bis hin zur umfassenden Qualitätssicherung erstreckt.
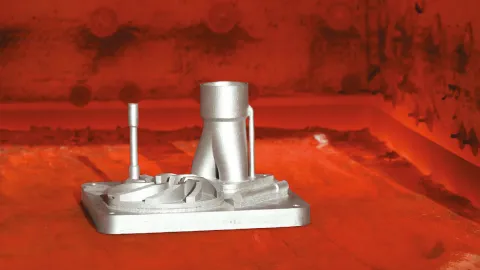
Das mittelständische Familienunternehmen Rosswag GmbH ist mit über 200 Mitarbeitern die größte Freiformschmiede Süddeutschlands und wird aus den Divisionen Edelstahl Rosswag und Rosswag Engineering gebildet. Seit mehr als 100 Jahren werden bei Edelstahl Rosswag hochbelastbare Freiformschmiedeprodukte, unter anderem für den Energiemaschinenbau, die Luft- und Raumfahrtindustrie, die Kraftwerkstechnik, den Pumpenbau und die optoelektronische Industrie hergestellt. Die Division Rosswag Engineering baut auf den Erfahrungen von Edelstahl Rosswag auf und erweitert das Produktportfolio um Ingenieurdienstleistungen und innovative Fertigungsverfahren.
Die Eingliederung des generativen Fertigungsverfahrens Selektives Laserschmelzen ermöglicht die Herstellung endkonturnah gefertigter, metallischer Bauteile ergänzend zum Schmiedebetrieb. Mit diesem Schritt wird einerseits das angebotene Produktportfolio erweitert und andererseits langfristig die Auswirkung der Substitution von Schmiedebauteilen reduziert.
Das über Jahrzehnte aufgebaute Know-how im Bereich der Materialwissenschaft und Werkstofftechnik dient als Grundlage, um den Zukunftsbereich der generativen Fertigung auf- und auszubauen.
- Einzelteilherstellung ,
- Kleinserienfertigung
- Entwicklung / Konstruktion ,
- Verarbeitungsprozess
- Prozessinnovation ,
- Industrie 4.0 / Digitalisierung
- Material ,
- Metalle
- taktisch (1 bis 5 Jahre)