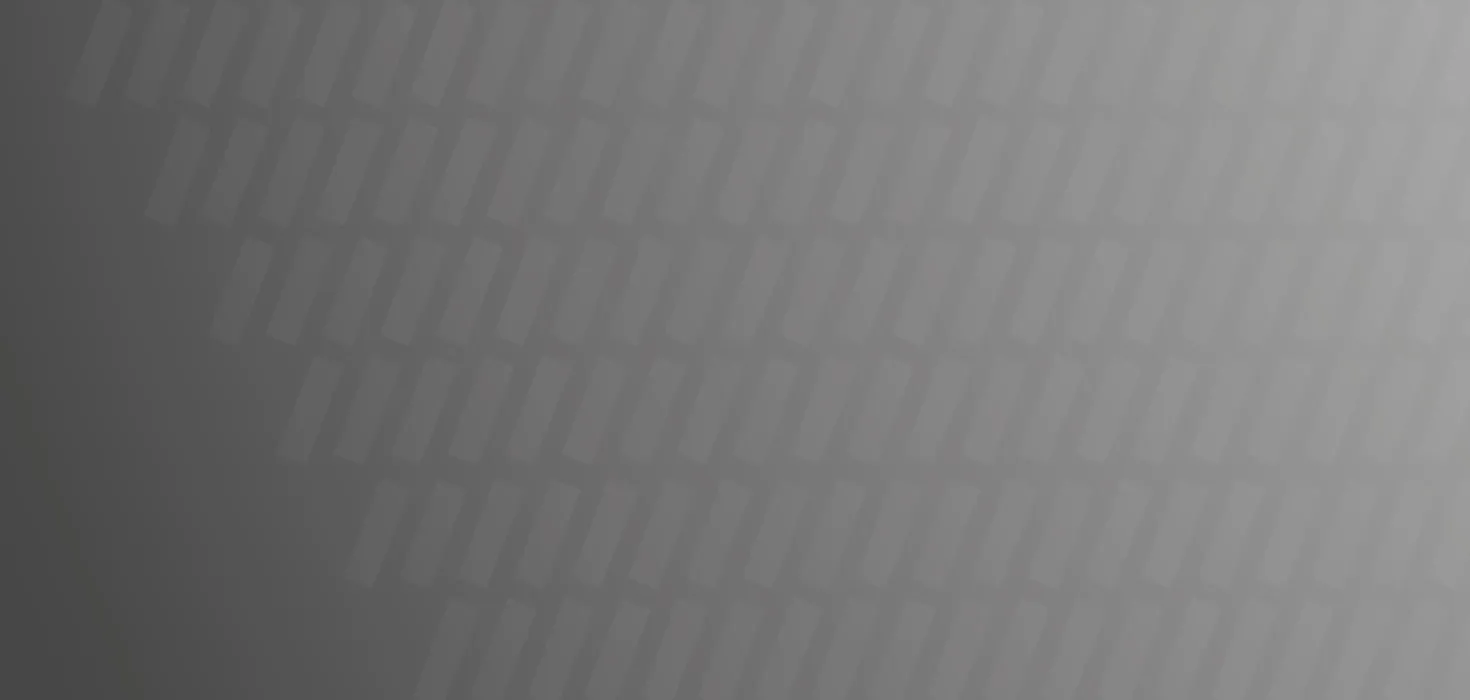
Auf die inneren Werte kommt es an – Einsatz von recyceltem Kunststoff im Drei-Komponenten-Spritzguss
Ersatz von Primärkunststoff durch Regranulat
CO2-Einsparung
Einsparung Polypropylen Copolymer
Einsparung TPE
Die WIHA Werkzeuge GmbH ersetzt bei der Fertigung von Werkzeugen wie Schraubendrehern konsequent den Einsatz von neuem Kunststoff durch Recyklat. In einem Zweikomponentenprozess werden nur die Sichtflächen mit Neumaterial gefertigt, was dessen Einsatz um 70% reduziert und somit Rohöl und CO2 einspart. Insgesamt hat das Unternehmen damit einige Herausforderungen gemeistert.
Die Wiha Werkzeuge GmbH ist einer der weltweit führenden Hersteller von Handwerkzeugen für den professionellen Einsatz in Industrie und Handwerk. Die Produktpalette umfasst u. a. Schraubendreher, Hammer, Zangen und Messwerkzeuge.
Ein wesentlicher Prozessschritt während der Schraubendreher-Produktion ist der Spritzguss der Kunststoffgriffe. Bereits seit Ende der 1990er-Jahre werden die im Spritzvorgang entstehenden Angüsse bei Wiha direkt in der Produktion in Angussmühlen gemahlen und wiederum dem Produktionsprozess zugeführt. Beim Angussmaterial handelt es sich entweder um Polypropylen (PP) oder Thermoplastische Elastomere (TPE). Durch die Wiederverwendung der Angüsse konnte der Bedarf an Neumaterial bereits um etwa 40 t pro Jahr reduziert werden. In Europa betreibt Wiha an seinen zwei Produktionsstandorten in Deutschland und dem Standort in Polen an allen Produktionsmaschinen Zerkleinerungsanlagen und entsprechende Vorrichtungen an den Maschinen für die Zuführung des Mahlguts.
Bei Wiha wollte man es jedoch nicht darauf bewenden lassen, Angüsse wiederzuverwenden. Vielmehr sollte der Bedarf an Kunststoff-Neumaterial weiter reduziert werden, weshalb man nach entsprechenden Möglichkeiten suchte. Um die Themen Nachhaltigkeit und Ressourceneffizienz im Unternehmen weiter voranzutreiben, wurden weitere Vorgänge in der Produktion untersucht. Schließlich definierte man das Ziel, den Anteil an recyceltem Kunststoff weiter zu erhöhen. Da das Regranulat aus der eigenen Produktion bereits vollständig wieder in den Produktionskreislauf beigefügt wurde, suchte Wiha nach einer externen Lösung um den Anteil an recyceltem Material in den Werkzeugen zu erhöhen.
Die Griffe der Schraubendreher werden im Drei-Komponenten-Spritzguss gefertigt. Dies bietet die Möglichkeit für die innere Spritzung buntes Regranulat aus dem eigenen Prozess und das meist dunkelbraune bis schwarze Rezyklat zu nutzen. Dadurch ist die Kern-Farbe des Kunststoffgriffes nicht relevant. Da die äußere Spritzung die innere Spritzung vollständig umschließt, ist der farblich bunte Kern nach der äußeren Spritzung nicht mehr sichtbar. Für die äußere Spritzung der sichtbaren Oberfläche wird folglich weiterhin Neuware verwendet, um die gewünschten Wiha Farben und die gewohnte Optik zu erzielen.
Insgesamt dauerte die Umsetzung von den ersten Versuchen bis zur Umstellung ein Jahr. Von Beginn stand jedoch die ausführliche Untersuchung der Prozesse an, wobei der Drei-Komponenten-Spritzguss als verbesserungswürdig im Hinblick auf Ressourceneffizienz und Nachhaltigkeit eingestuft wurde. Im Anschluss folgte die recht aufwendige Suche nach einem geeigneten Lieferanten. Nach mehrmaligen Messebesuchen im Bereich Kunststoffe und Recycling und ausführlicher Materialbemusterung, wurde ein Lieferant ausgesucht. Nach den ersten Tests stellte sich jedoch heraus, dass die Materialeigenschaften nicht den Anforderungen entsprachen. Erst der dritte Lieferant konnte alle Anforderungen an Qualität, Stoffreinheit und Materialeigenschaften erfüllen. Die ausführliche Bemusterung des Materials bestand ebenfalls aus mehreren Rezyklat-Spritzgüssen verschiedener Chargen. So konnten Materialeigenschaften, wie z. B. der MFI (Mold Flow Index) eingehend getestet werden. Bei den Spritzgüssen wurde sowohl auf die Materialeigenschaften, die Farbe als auch eine gleichmäßige, konsistente und nicht poröse Spritzung ohne unerwünschte Hohlräume (Lunker) geachtet. Da die innere Spritzung maßgeblich beeinflusst, wie gut die Klinge im Griff sitzt, musste sichergestellt werden, dass beim Spitzguss mit dem Rezyklat keine Lunker entstehen. Der Vorgang musste für alle Griffgrößen und alle Farbkombinationen wiederholt werden. Die fertigen Muster wurden im Anschluss strengen Qualitätskontrollen unterzogen, bis es schließlich zur Freigabe durch die Qualitätssicherungsabteilung kam. Das gesamte Projekt wurde von einem Projektteam aus den Fachbereichen Engineering, Produktion, Qualität und Einkauf begleitet. In der Schraubendreherproduktion wird für die innere Spritzung, die etwa zwei Drittel des Gesamtbedarfs ausmacht, nun eine Mischung aus zugekauftem Rezyklat und den eigenen gemahlenen Angüssen genutzt. Für die äußere Spritzung, auf die ein Drittel des Gesamtbedarfs entfällt, wird weiterhin Neuware benötigt.
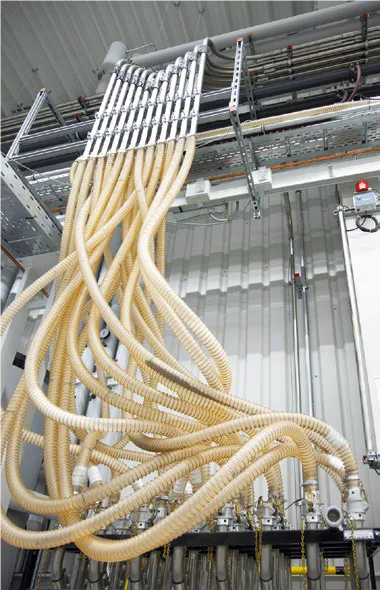
Durch die Nutzung der anfallenden Angüsse und des angekauften Regranulats reduziert sich der Bedarf an Neuware bei Wiha jährlich um 75 t Polypropylen Copolymer und 7,5 t TPE. Die 7,5 t TPE stammen vollständig aus der Wiederverwendung der Angüsse. Beim Polypropylen Copolymer werden 31,25 t durch die Wiederverwendung der Angüsse und die restlichen 43,75 t durch Regranulat gedeckt. Die Herstellung des ersetzten Neumaterials ist mit ca. 212 t CO2e verbunden. Für die Herstellung des Regranulats und das Aufbereiten der Angüsse fallen etwa 10 t CO2e an, sodass rund 202 t CO2e pro Jahr durch die Maßnahme vermieden werden.
Die umgesetzte Maßnahme zeigt, welches Potenzial mit der Nutzung von Regranulat bzw. Rezyklat in nicht sichtbaren Produktkomponenten verbunden ist. Grundsätzlich ist denkbar, die Maßnahmen an weiteren Produktionsstandorten umzusetzen, auf weitere Produktgruppen auszuweiten und nach Möglichkeit den Anteil an Regranulat und Rezyklat weiter zu erhöhen. Abgesehen davon wurden weitere Maßnahmen zur Einsparung von Kunststoff umgesetzt. So werden z. B. die Produkte des Unternehmens seit 2019 in FSC-zertifizierten Kartonagen anstelle von Kunststoffblistern verkauft. Dadurch werden jährlich etwa 20 t Kunststoff eingespart.
Das größte Learning aus dem Projekt ist, die eigenen Prozesse genauer unter die Lupe zu nehmen und immer wieder zu hinterfragen, ob es nicht umweltfreundlichere und ressourcenschonendere Alternativen gibt. Auch wenn man denkt, dass alle Prozesse schon optimiert sind, schlummert immer irgendwo noch mehr Potenzial. In Fällen von Kunststoffteilen, bei denen Optik und Farbe nicht relevant sind, kann man es auf die „inneren Werte ankommen lassen“ und nach neuen Alternativen suchen. Man muss nicht sofort die ganze Produktion umstellen - aber solange man kleine Schritte geht, macht man Fortschritte in Richtung größerer Ressourceneffizienz und mehr Nachhaltigkeit.
Im Jahr 1939 als kleiner Familienbetrieb gegründet, steht Wiha dem Anwender heute mit rund 10.000 gelisteten Präzisionswerkzeugen weltweit zur Seite und hat sich als Innovationsmotor im Markt positioniert. Dabei profitiert Wiha von der engen Zusammenarbeit mit den eigenen Produktions- und Vertriebsgesellschaften und Partnern in den wichtigen Wirtschaftszonen Europa, USA und Asien. Seit jeher verfolgt Wiha eine leistungsstarke und nachhaltige Wachstumsdevise: Die Konzentration der Ressourcen auf jene Produkt- und Marktsegmente, die ausreichendes Potenzial für beständiges Wachstum bieten. Dieser Gedanke, gepaart mit der Schwarzwälder Leidenschaft für Ideen, Tüftelei und Präzision, stellt den Treiber für vergangene und zukünftige Wachstumsschritte dar.
- Großserienfertigung
- Verarbeitungsprozess
- Stoffkreislauf / Recycling
- Energie ,
- Material ,
- Kunststoffe ,
- Sonstige Materialien ,
- Abgas