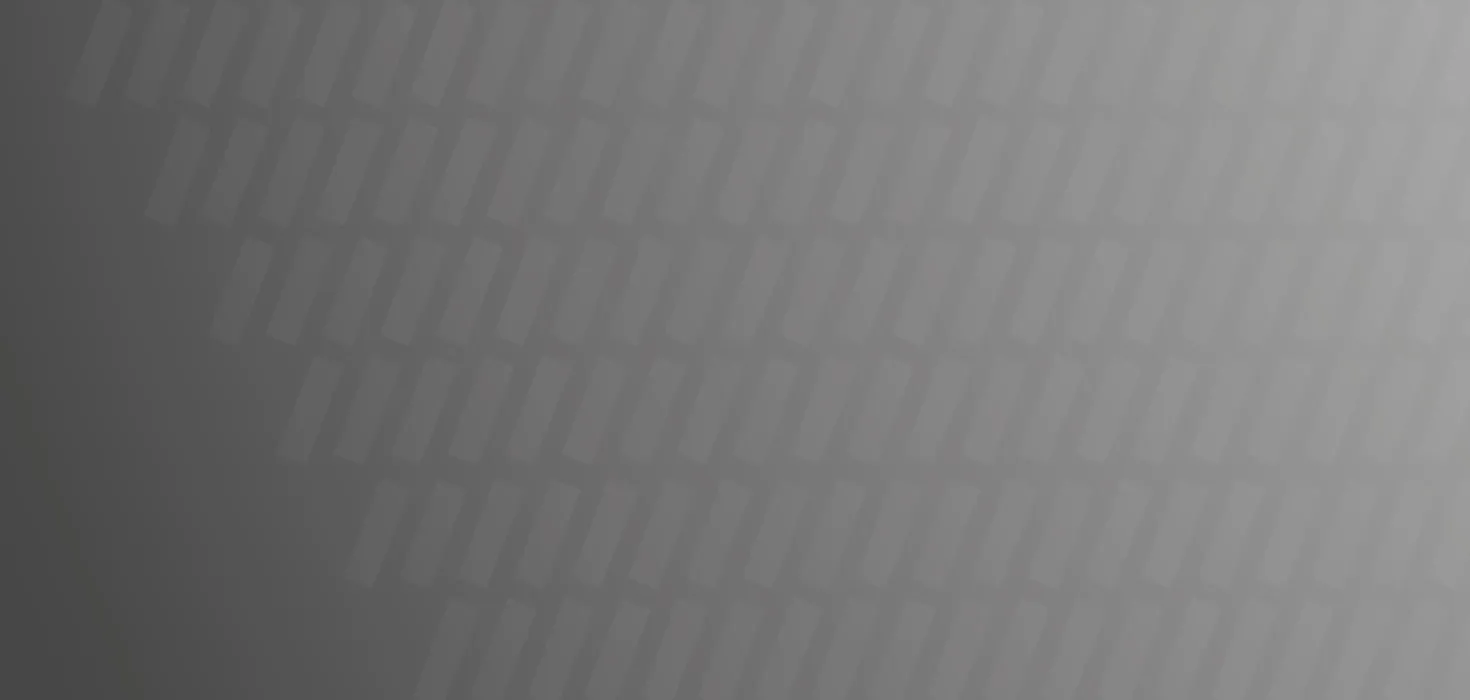
NOA! Noch Optimalere Abläufe!
Organisatorische Prozessoptimierung für Effizienzsteigerungen
Silikon-Komponenteneinsparung
Polyurethan-Schaum-Komponenteneinsparung
NOCH ist der Spezialist für den Modell-Landschaftsbau, vor allem im Bereich Modelleisenbahn. Da die Produkte sich oft sehr unterscheiden und individuelle Anforderungen haben, ist es besonders wichtig, auf die Material- und Informationsflüsse zu achten. Diese werden ständig durch das Projektteam NOA! analysiert und optimiert, wodurch einige Einspar- und Optimierungspotenziale aufgedeckt wurden.
Kostenvorteile
- 28.000 Euro/Jahr Materialkosten
- 12.000 Euro/Jahr an Materialverlusten bei Fertigwaren
- 4.000 Euro/Jahr an Materialverlusten durch die systematische Lagerung und Kennzeichnung
- 12.000 Euro an Materialverlusten durch die Prozessoptimierung der Polyurethan-Schäumerei
- 24.000 Euro an verlorenen gegangener Wertschöpfung durch das Standzeitmanagement
- 8.000 Euro durch die systematische Lagerung und Kennzeichnung
Das Wangener Unternehmen NOCH ist seit über 100 Jahren der Spezialist für den Modell-Landschaftsbau, vorzugsweise im Bereich Modelleisenbahn. Gleichermaßen ist NOCH mittlerweile auch mit seinen speziellen Herstellungsverfahren im Sektor Werbe-Displays beheimatet.
Die Produkte mit sehr vielfältigen Anforderungen werden in der eigenen manufakturähnlichen Fertigung hergestellt. Die Herstellungsverfahren sind dabei oft durch eine hohe individuelle Verfahrensweise und einen relativ großen Anteil an Handarbeit bei gleichzeitig geringen Losgrößen geprägt.
In den maschinellen Herstellungsverfahren werden im Wesentlichen Polyurethan-Schäumtechnik, Tiefziehtechnik, Beflockungstechnik und Lasertechnik eingesetzt. Dabei steht jeweils eine hohe individuelle Qualität der hergestellten Produkte im Fokus, da die Artikel auch Gefühle in Form der kleinen heilen Welt transportieren sollen.
Aufgrund der sehr individuellen Herstellungsabläufe kommt es entscheidend auf eine starke und positive Kooperation und Kommunikation der Mitarbeiterinnen und Mitarbeiter untereinander an. Eine wesentliche Rolle spielt hier ein optimaler Material- und Informationsfluss. Beide Flüsse sind permanent durch Analysen der aktuellen Abläufe zu optimieren, anzupassen und auf eine entwicklungsstarke Zukunft des Unternehmens auszurichten. Einer der wichtigsten Aspekte ist dabei die Erreichung einer optimalen Ressourceneinsparung, insbesondere durch eine bedarfsgerechte Produktion.
Das abteilungsübergreifende Projektteam NOA! (Noch Optimalere Abläufe!) erhielt den Auftrag, die gesamten Material- und Informationsflüsse im Unternehmen zu erfassen, zu visualisieren und daraus resultierend die Effizienzpotenziale zu quantifizieren. Ein Fokus wurde dabei auf die Polyurethan-Schäumerei gelegt, da hier dauerhaft an der Kapazitätsgrenze gearbeitet wird und Effizienzverbesserungen eine sofortige Wirkung zeigen sollten. Gleichzeitig sollte diese Teamarbeit eine Keimzelle für neue Zusammenarbeit und Kooperationskultur über die Abteilungsgrenzen hinweg sein.
Durch die Material- und Informationsflussanalyse wurden jährliche Materialverluste von ca. 5,2 % des eingekauften Materials in Höhe von 57.000 Euro sowie die bedeutendsten Materialverlustursachen erfasst. Als wesentliche Ansatzpunkte wurden das Standzeitmanagement der Werkzeuge, die Vorratsproduktion und das Auslaufmanagement bei Neuprodukten identifiziert.
Die unterschiedlichen Standzeiten der qualitätssensiblen Silikon-Werkzeuge zur Herstellung von Hartschaumartikeln führten am Ende der jeweiligen Standzeit zu schwer erkennbaren Qualitätseinbußen am Produkt. Hierdurch mussten insbesondere im Mehrschichtbetrieb wiederkehrend bis zur offensichtlichen Erkennung der Werkzeugbeschädigung Hartschaumartikel entsorgt werden. Durch die Erfassung der artikelbezogenen Standzeiten kann die durchschnittliche Reichweite jedes Werkzeugs abgeleitet werden. Darauf aufbauend wird die Qualitätskontrolle gegen Ende der durchschnittlichen Standzeit signifikant erhöht, so dass die Gefahr von Materialverlusten deutlich reduziert wird. Hierfür wird für jedes komplexere Teil ein Prüfplan erstellt, der ein schnelles Erkennen von Qualitätsproblemen an den kritischen Stellen eines Artikels ermöglicht und so das Ende der Werkzeugstandzeit bestimmt.
Die fehlende Verfügbarkeit von Ersatzwerkzeugen führte auch dazu, dass Mitarbeiter aufgrund von Liefertermindruck mit fehlerhaften Werkzeugen weiterproduzierten. Durch die parallele Einführung eines Werkzeug-Kanban-Systems mit Schwesterwerkzeugen für alle komplexeren Produkte, die das Hauptwerkzeug bei Verschleiß oder Bruch ersetzen, ist am Ende der Standzeit eines Werkzeugs die sofortige Weiterproduktion von Gutteilen möglich. Dies führt gleichzeitig zu einer Entzerrung der Kapazitätsspitzen in der eigenen Werkzeugproduktion.
Im Rahmen des Projekts erfolgte die Erfassung und Quantifizierung aller Ausschussteile bei Hartschaumartikeln. Auf der Basis der Wertberechnung der Ausschüsse erfolgt nun eine laufende Sensibilisierung der Mitarbeiterinnen und Mitarbeiter zu deren Erfolgen bei der Einsparung von Materialverlusten durch das funktionierende Standzeitmanagement. Das bisherige Vorgehen der Vorratsproduktion für die Fertigware führte wiederkehrend bei Fehlprognosen des Jahresproduktionsplans zu Ladenhütern und zu unerwünschter Lagervernichtung bei Überproduktionen. Deshalb erfolgte hier eine Umstellung auf eine Kanban-Steuerung der Produktion der unterschiedlichen Produktfamilien entsprechend der Abgänge aus dem Fertigwarenbestand. Gleichzeitig entstand hierdurch die Möglichkeit, Zwischenprodukte erst bei Abruf durch die Kunden sehr zeitnah bedarfsspezifisch zu veredeln.
In der Nachfolge des NOA!-Projektteams hat sich das Produktionsteam mit Mitgliedern aus Produktion und Vertrieb gegründet. Durch diese bessere Abstimmung können sogenannte Ladenhüter durch die jährlichen Artikelwechsel aufgrund von Neuheiten vermieden werden. Bestehende Restmengen von Fertigwaren werden zukünftig im Rahmen von Werbeaktionen vergünstigt an den Kunden weitergegeben.
Das mit den aufgedeckten Effizienzpotenzialen verbundene Einsparpotenzial leistet einen wesentlichen Beitrag zur Unternehmenssicherung. So konnten durch die Maßnahmen konkrete Einsparungen an reinen Materialkosten in Höhe von jährlich 28.000 Euro erzielt werden. Diese verteilen sich folgendermaßen auf die einzelnen Ansatzpunkte.
Durch die bedarfsbezogene Vorratsproduktion mit Kanban sowie das systematische Auslaufmanagement aufgrund von Neuprodukten und sich ändernder Kundennachfrage werden jährlich 12.000 Euro an Materialverlusten bei Fertigwaren eingespart. Eine jährliche Einsparung von 4.000 Euro an Materialverlusten wird durch die systematische Lagerung und Kennzeichnung erreicht.
Die Prozessoptimierung der Polyurethan-Schäumerei bringt eine jährliche Einsparung an Materialverlusten von 12.000 Euro. Hierdurch werden ca. 400 kg Silikon-Komponenten in der Werkzeugproduktion und 1.650 kg Polyurethan-Schaum-Komponenten bei der Herstellung der Hartschaumartikel eingespart.
Wird zusätzlich zu den Materialkosten die bis zur Entsorgung angefallene Wertschöpfung mit hinzugerechnet, dann erhöht sich die Kostenersparnis um weitere 32.000 Euro. Dabei entfallen Einsparungen von 24.000 Euro an verlorenen gegangener Wertschöpfung auf das Standzeitmanagement und 8.000 Euro auf die systematische Lagerung und Kennzeichnung.
Die nutzbringenden Veränderungen wurden alle durch das abteilungsübergreifende NOA!- Team erarbeitet. Durch das gewachsene Verständnis der Mitarbeiterinnen und Mitarbeiter untereinander sind eine abteilungsübergreifende Verständigung sowie das Entdecken und Abstellen von Fehlerquellen wesentlich leichter geworden. Teamarbeit ist bei NOCH für das Erreichen strategischer Ziele inzwischen zum Standard geworden. Die durch das Projekt angestoßenen Kommunikationstreffen PTT (Produktions-Team-Treffen mit Vertretern von Produktion und Vertrieb) führten dazu, dass die gesamte Gebäudestruktur sowie die Logistik innerbetrieblich und hin zum Endkunden komplett revolutioniert wurden.
Durch eine Visualisierung und Quantifizierung von Materialflüssen können Zusammenhänge aus dem betrieblichen Alltag bewusst gemacht, Verbesserungspotenziale entdeckt und aufgrund der gemeinsamen Erarbeitung auch wirklich von den beteiligten Personen umgesetzt werden. Damit wurde der Wirkungsgrad der Umsetzung von Verbesserungspotenzialen bei NOCH deutlich erhöht.
Die Firma NOCH wurde 1911 von Oswald Noch, Urgroßvater des heutigen Geschäftsführers, in Glauchau in Sachsen gegründet. Das über die Generationen hinweg inhabergeführte Familienunternehmen entwickelte sich zum Spezialist für den Modell-Landschaftsbau.
Jahr für Jahr versucht das NOCH-Team, die Anwendungen zu verbessern und neue, innovative Produkte für das schönste Hobby der Welt zu entwickeln. Die Leidenschaft für das Detail ist für NOCH der zentrale Baustein. Das „...wie im Original“ im Logo verpflichtet dabei.
Über 2.000 Produkte zu den Themen Gelände- und Gleisbau, Brücken und Viadukte, Portale, Mauern und Arkaden, Landschaftsgestaltung mit Bäumen und Büschen, Gebäude und Figuren, Fahrzeuge und Deko, Modellbahnen u. v. m. stehen für den Hobbyisten zur Verfügung. Abgerundet wird das Angebot durch die Highlights aus den Sortimenten der Partner ROKUHAN, KATO und Athearn.
Die Firma NOCH in Wangen beschäftigt rund 80 Mitarbeiterinnen und Mitarbeiter am Stammsitz, von denen etwa 50 in der Produktion tätig sind. Unterstützt werden sie durch 30 weitere Heimarbeiterinnen und Heimarbeiter.
Ergänzt wird das Leistungsspektrum in Wangen durch die Tochter NOCH Asia in Vietnam. Dort werden die Fäden von Wangen aus selbst in der Hand gehalten. Ein gutes und gesundes Arbeitsumfeld sorgt dafür, dass auch hier die über 100 Kolleginnen und Kollegen sehr gerne zur Arbeit kommen.
Teamgeist und ein inhabergeführtes Familienunternehmen, in dem auch der Chef die Ärmel hochkrempelt, stehen für eine flache Hierarchie, kurze Entscheidungswege und sorgen für einen hohen Identifikationsgrad des Einzelnen – in allem was zu tun ist.
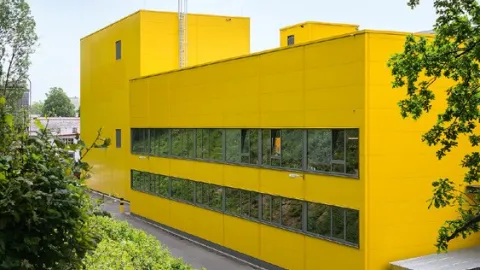
- Kleinserienfertigung
- Produktionsplanung / -steuerung ,
- Produktionslogistik ,
- Verarbeitungsprozess
- Prozessoptimierung ,
- Green Supply Chain Management ,
- Lean Management
- Material ,
- Kunststoffe
- operativ (kleiner 1 Jahr)