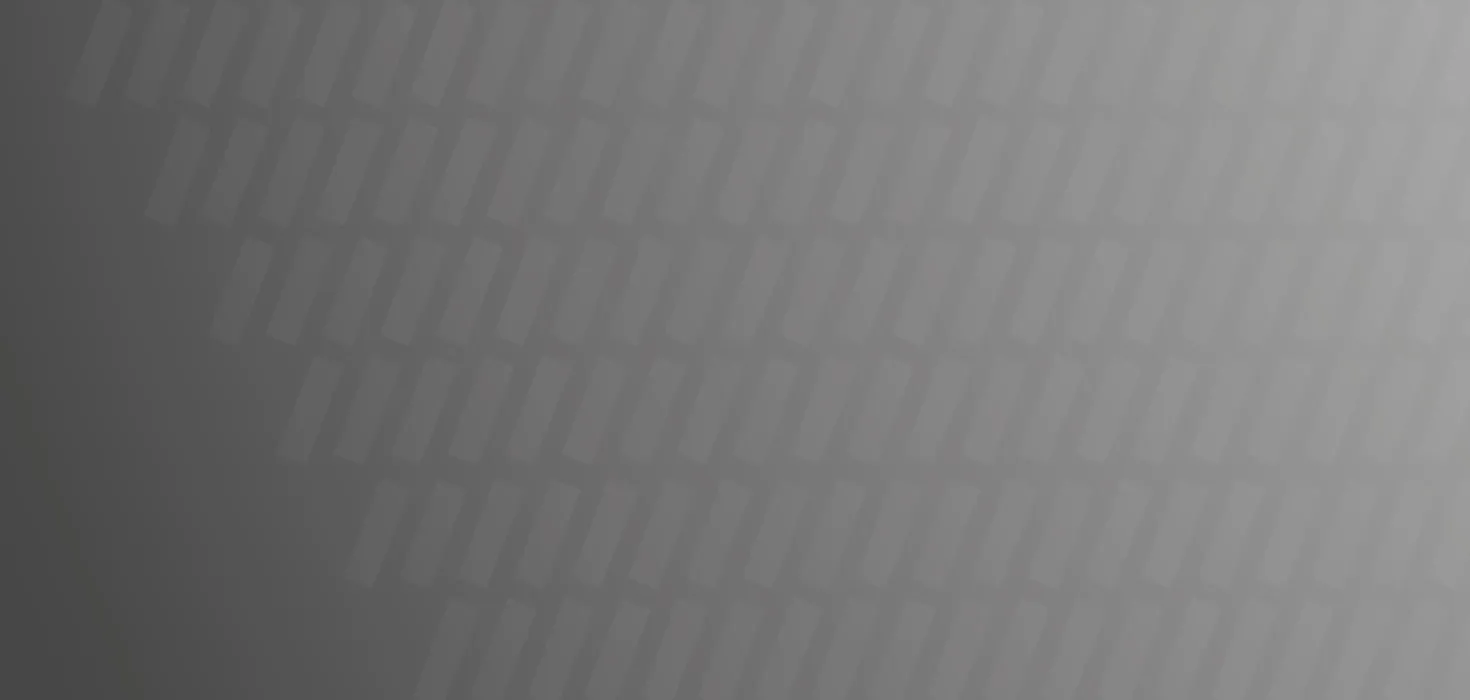
Rohstoffeinsparung bei Premium Design dank neuem innovativem Werkstoff
Entwicklung des neuen, innovativen Werkstoffs DuraCeram®
Rohstoffbedarfreduktion
Rohstoffeinsparung
Energieeinsparung
CO2-Einsparung
Die Duravit AG beschäftigt sich mit der Herstellung von Sanitärmobiliar. Im Rahmen eines Entwicklungsprojekts kam das Bedürfnis nach einem filigraneren Design für die Produkte auf, welches nur durch den Einsatz eines anderen Werkstoffes möglich wäre. Dafür wurde der neue Werkstoff DuraCeram® entwickelt, der die gewünschte Robustheit gewährleistet und dabei Rohstoffe und Energie einspart.
Kostenvorteile
ca. 13.000 Euro durch Rohstoffeinsparungen
Aus der Zusammenarbeit mit dem internationalen Designstar und Architekten Philippe Starck resultierte der Wunsch nach besonders filigranen und exakt gearbeiteten Formen für die neuen Waschschalenmodelle der Badserie Cape Cod. Diese sind in den drei formalen Ausprägungen kreisrund, quadratisch und trioval erhältlich. Bei der runden und quadratischen Variante sitzt die Armatur auf einer ins Becken integrierten Keramikinsel, die sehr exakt gearbeitet sein muss, um die Passfähigkeit der Armatur zu gewährleisten.
Philippe Starck legt generell bei allen Neuentwicklungen größten Wert auf Nachhaltigkeit, sowohl was die zeitlos modernen, langlebigen Formen angeht als auch im Hinblick auf die verwendeten Materialien. Die neuen Waschschalen sollten wie hochwertiges, formschönes Porzellan feine, extrem dünne Ränder von nur 7 mm Stärke besitzen. Bei dieser Wandstärke ist es jedoch sehr schwierig bis nahezu unmöglich, die notwendige Festigkeit des Produktes zu gewährleisten. Das Ziel von Duravit war es daher, die Wandstärke der Keramik unter Erhaltung einer hohen Festigkeit zu reduzieren, ohne jegliche Einbußen hinsichtlich Qualität, Robustheit und Pflegeleichtigkeit.
Da mit den bisher verwendeten Gießmassen ohne Gefährdung der Festigkeit keine Reduktion der Wandstärke möglich war, konnte diese nur durch die Optimierung des Werkstoffs erreicht werden. Daher sollte ein neuer, innovativer Werkstoff entwickelt werden, der dünne Wandstärken zulässt und dennoch keine Minderung der Festigkeit zur Folge hat. Auf diese Weise können bislang nicht für möglich gehaltene Formen umgesetzt werden und es wird damit eine neue Dimension gestalterischer Vielfalt erreicht.
Die Reduzierung der auftretenden Glasphase wird notwendig, um die Deformation entsprechend zu verringern. Im Brennprozess werden aus den eingesetzten Rohstoffen unterschiedliche neue Mineralphasen gebildet. Eine wichtige Phase ist der Mullit, der aus Anteilen des Kaolin-Tongemisches in Verbindung mit Quarzen entsteht. Die Reaktionen treten üblicherweise bei Temperaturen oberhalb 1.100 °C auf. In Zusammenarbeit zwischen der Forschungs- und Entwicklungsabteilung und der Abteilung für Rohstoffaufbereitung wurden unterschiedliche Zusammensetzungen für Gießmassen aufbereitet, um das Deformationsverhalten aufgrund des Glasphasenanteils zu untersuchen. Hierzu wurden entsprechende Versuche mit unterschiedlichen Mahlgraden der Einzelrohstoffe durchgeführt.
Es zeigte sich, dass die Feinheit der eingesetzten Rohstoffe die Reaktionsgeschwindigkeit der Mineralphasenneubildung erhöht. Hierdurch kann auch die Bildung des Mullits beschleunigt werden. Eine beschleunigte Mullitbildung führt zu einem deutlich deformationsärmeren Verhalten des Produktes während des Brennprozesses. Am Ende der Zusammenarbeit der Abteilungen entstand ein hinsichtlich der Zusammensetzung der Einzelrohstoffe optimierter Werkstoff, das DuraCeram®.
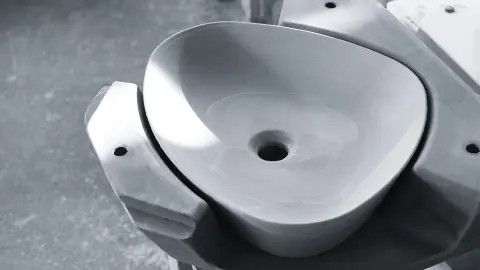
Mit dem neuentwickelten Werkstoff DuraCeram® können die neuen Cape Cod Waschschalenmodelle mit einer Wandstärke von 7 mm und einem Gewicht von 7,4 kg gefertigt werden. Unter Verwendung der konventionellen Werkstoffe würde die Wandstärke 11 mm betragen und das Gewicht bei 10,3 kg liegen. So reduziert sich der Rohstoffbedarf aufgrund der Gewichtsreduzierung des Sanitärartikels um 28 %. Hierdurch können jährlich Rohstoffe in der Größenordnung von 22 t eingespart werden. An die Rohstoffreduzierung ist auch eine Reduzierung der benötigten Energie gekoppelt. Der durchschnittliche Energiebedarf zur Herstellung einer Sanitärkeramik beträgt 6,5 MWh/t. Die voraussichtliche jährliche Energieeinsparung beträgt somit ca. 143 MWh. Umweltseitig werden die CO2–Emissionen dadurch um ca. 71,5 t reduziert. Monetär ergibt sich aus der Rohstoffeinsparung eine jährliche Ersparnis von ca. 13.000 Euro.
Die Maßnahmen zur Wandstärkenreduktion und die daraus resultierende Anpassung des Deformationsverhaltens durch die Werkstoffoptimierung führten zu einer intensiveren Betrachtung der möglichen Rohstoffauswahl. Es stellte sich heraus, dass das Deformationsverhalten der konventionellen Rohstoffmischung verändert werden kann und sich dadurch die Schwierigkeiten der Eigendeformation reduzieren lassen. Resultierend aus dieser Idee ist auch eine Anpassung des Formenbaus möglich. Denn durch die Reduktion der Deformation können die Formen endkonturnäher hergestellt werden.
Eine weitere Optimierung der Maßnahme ist zudem in Bearbeitung. So soll eine Änderung des Formgebungsverfahrens vom Gipsgussverfahren hin zum Druckgussverfahren erfolgen. Dadurch würde sich die benötigte Menge an Gipsformrohstoffen reduzieren. Die Anzahl der Abgüsse im Gipsgussverfahren liegt bei ca. 80 Zyklen pro Form. Die Umstellung auf das Druckgussverfahren, bei dem bis zu 100.000 Zyklen pro Form erreicht werden können, würde den Bedarf an Gips um 96 t reduzieren. Die Einsparungen an Gips würden zu einer Reduktion der CO2–Emissionen um weitere 8,8 t führen. So können zusätzliche Ressourcen eingespart werden.
„Leben im Bad“ zeichnet die Firmenphilosophie der Duravit AG aus. Dies spiegelt sich in der Zusammenarbeit mit bedeutenden Designern wie z. B. Philippe Starck, Phoenix Design, EOOS, sieger design, und Matteo Thun wider. Das Resultat sind innovative Neuentwicklungen, mit denen Duravit stets Maßstäbe setzt - für unterschiedliche Budgets und Lifestyles. Dabei legt das Unternehmen den Fokus auf gutes Design, intelligent eingesetzte Technik und höchsten Qualitätsanspruch. So entstehen sinnvoll gestaltete Bäder, die die Lebensqualität der Benutzer nachhaltig steigern.
Das Produktportfolio von Duravit umfasst Sanitärkeramik, Badmöbel, Dusch- und Badewannen, Wellnesssysteme sowie DuschWCs und Accessoires.
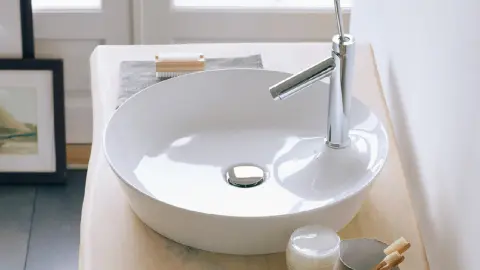
- Großserienfertigung
- Entwicklung / Konstruktion ,
- Verarbeitungsprozess
- Produktinnovation
- Energie ,
- Material ,
- Baustoffe ,
- Abgas
- taktisch (1 bis 5 Jahre)