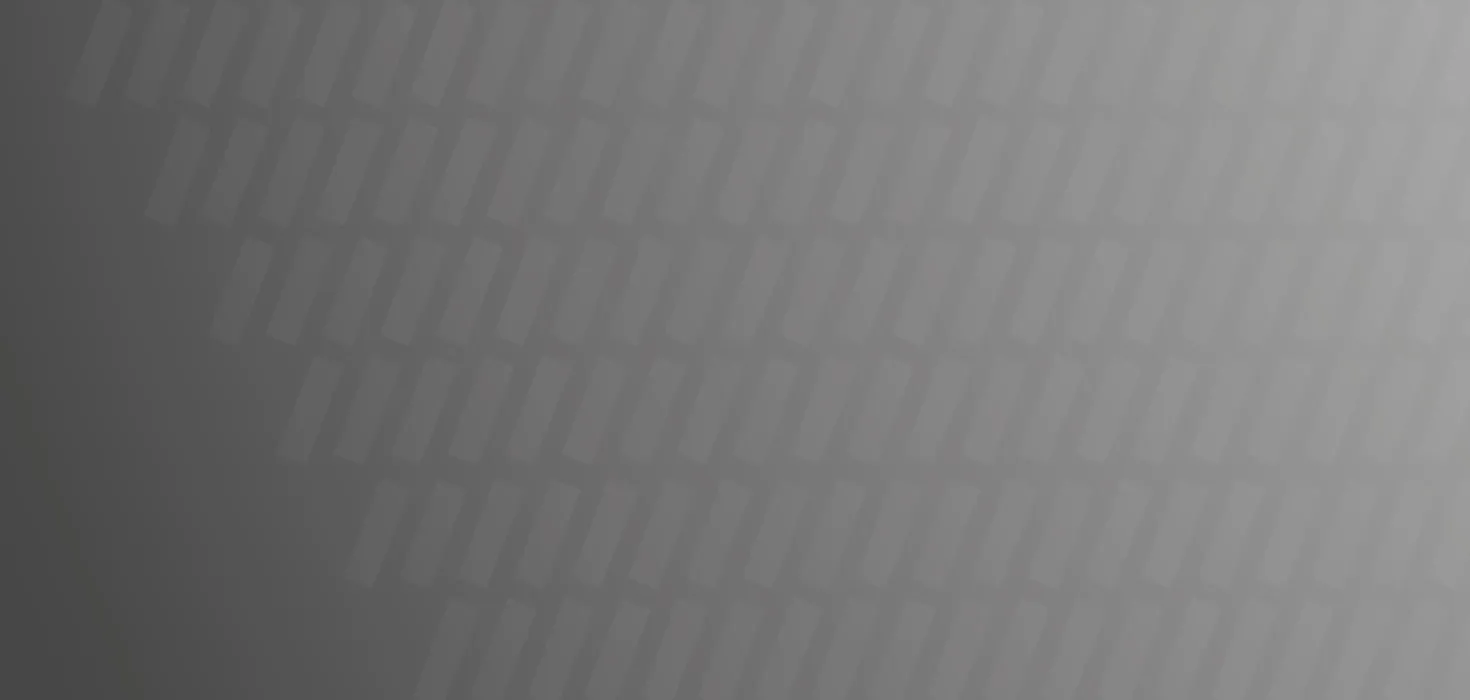
Smartes Re-Design von Anschlussschläuchen
Redesign eines Anschlussschlauchs unter ökologischen Gesichtspunkten
Materialeinsparung
CO2-Einsparung
Die NEOPERL GmbH hat in einem mehrjährigen Entwicklungsprozess sanitäre Anschlussschläuche nach Ecodesign Prinzipien weiterentwickelt und den Materialeinsatz kontinuierlich optimiert und reduziert. Durch die Nutzung von alternativen Materialien konnten enorme Mengen an Material eingespart werden, was sowohl die Klimawirkung als auch den Wasserverbrauch für die Herstellung reduziert.
Kostenvorteile
10 Millionen Euro Kostenvorteil
Die Produkte der Neoperl GmbH sind häufig dort zu finden, wo Wasser fließt. Sie formen den Strahl des Wassers, regeln den Durchfluss, schützen oder verteilen es. Der größte der insgesamt zwölf Produktionsstandorte befindet sich im baden-württembergischen Müllheim, wo Strahlregler, Rückflussverhinderer, Wassermengenregler, Duschschläuche und Anschlussschläuche für Armaturen gefertigt werden. Seit jeher steht der verantwortungsvolle Umgang mit der Ressource Trinkwasser im Fokus der Geschäftstätigkeiten von Neoperl.
Anschlussschläuche werden beispielsweise unter dem Waschbecken oder der Spüle verbaut. Aufgrund ihrer Verbindung zum Eckventil sind sie dabei einer permanenten Druckbelastung ausgesetzt und müssen über Jahre hinweg einwandfrei funktionieren. Funktionsausfälle wie etwa eine Leckage am Anschluss oder ein Platzen des Schlauchs können gravierende Schäden an Gebäuden zur Folge haben. Daher handelt es sich bei Anschlussschläuchen um Hochrisikoprodukte, die strenge internationale Zulassungskriterien erfüllen müssen.
Ursprünglich wurde ein individuell geformtes Kupferrohr anstelle eines flexiblen Anschlussschlauchs verwendet. Erst in den 1960er-Jahren erfolgte aus Gründen der Handhabung der Wechsel zum Anschlussschlauch. Die internationalen Zulassungskriterien für Anschlussschläuche orientieren sich bezüglich der Stabilität und Langlebigkeit als Vergleichsgröße an festen Kunststoffrohren. Das hat zur Folge, dass Anschlussschläuche bis heute meist überdimensioniert sind, um Anforderungen garantiert erfüllen zu können.
Aus Untersuchungen wusste man bei Neoperl bereits, dass der größte Teil der verursachten CO2-Emissionen auf die Vorketten der eingesetzten Materialien zurückzuführen ist. Aufgrund der Tatsache, dass mit der andauernden Überdimensionierung ein unnötiger Materialeinsatz verbunden ist, setzte man sich bei
Neoperl das Ziel, das bestehende Design der Anschlussschläuche zu überarbeiten, um Kosten und Materialverbrauch zu reduzieren.
Im Rahmen einer intensiven und kontinuierlichen Forschungs- und Entwicklungsarbeit sollte jede Einzelkomponente des Anschlussschlauchs auf den Prüfstand gestellt und optimiert oder ersetzt werden. Dabei war die Zielsetzung für jede Komponente die Realisierung eines ressourcensparenden Designs. Alles, was nicht erwiesenermaßen notwendig ist, sollte zukünftig weggelassen werden. Neoperl wollte so eine Vorreiterrolle übernehmen und neue Marktstandards setzen.
Im Zuge der Forschungs- und Entwicklungsarbeiten rund um den Schlauch wurden verschiedene Optimierungen durchgeführt. Kern der innovativen Schläuche und Basis für alle weiteren Optimierungen ist seit dem Jahr 2014 eine neuartige und patentierte Krimpausformung (Boostkerbe) im Bereich der Hülse. Diese Technologie ermöglicht eine Reduzierung von Tot-Zonen, Verwirbelungen und somit Druckverlusten im Schlauchinneren, was einen gleichen Durchfluss bei kleineren Schlauchquerschnitten ermöglicht. Im Rahmen dieser einzigartigen, strömungsoptimierten Lösung konnten alle weiteren Details des Schlauchs neu gedacht werden.
Zusätzlich konnte durch die intensive Forschungs- und Entwicklungsarbeit nachgewiesen werden, dass die herkömmliche Ummantelung von Anschlussschläuchen aus Edelstahl durch Polyamid ersetzt werden kann. Dies war insbesondere auf dem europäischen Markt lange undenkbar, da Kunststoff im Vergleich zu Edelstahl als minderwertig galt. Heute ist bewiesen, dass die Leistung des Schlauchs in Bezug auf die Langlebigkeit und die Fähigkeit höheren Temperaturen und Drücken standhalten zu können, sogar noch gesteigert werden konnte.
Im Jahr 2020 konnte im bisher letzten Entwicklungsschritt der Schlauch innerhalb der Ummantelung, der Inliner, welcher gewöhnlich aus Ethylen-Propylen-Dien-(Monomer)-Kautschuk (EPDM) oder vernetztem Polyethylen (PE-X) besteht, durch aufwendige Forschung durch ein unvernetztes Polyolefin ersetzt werden. Zur Herstellung dieser unvernetzten Inliner wird deutlich weniger Energie benötigt. Zudem können sie von mehr Zulieferern bezogen werden, wodurch für die weltweiten Produktionsstätten zusätzlich erhebliche Transportaufwände entfallen.
Für die Kunden ermöglicht das neue Schlauchdesign mit den verkleinerten Anschlüssen neue, generell kleinere Armaturendesigns und somit potenziell wieder erhebliche Ressourceneinsparungen.
Durch die vielen Anpassungen konnten aber nicht nur Materialien eingespart werden. Es konnte auch die Robustheit gegenüber höheren Temperaturen und Chemikalien sowie die mechanische Belastbarkeit und die Lebensdauer kontinuierlich gesteigert werden. Dies wurde in umfangreichen Tests, die beispielsweise an die DIN EN 13618 angelehnt sind, deutlich. Die neueste Schlauchgeneration hat alle notwendigen Zertifikate für eine weltweite Zulassung erhalten.
Durch die kontinuierliche Entwicklung und das neue Schlauchdesign konnten erhebliche Materialeinsparungen realisiert werden. So konnte das Schlauchgewicht über die Jahre von 68 auf 37 g reduziert werden und hat sich damit mehr als halbiert. Als Folge verringerten sich der Wasser- und CO2-Fußabdruck des Schlauchs um 80 bzw. 60 %. Jährlich werden etwa 100 Millionen Anschlussschläuche verschiedener Generationen verkauft. Im Vergleich zur ersten Schlauchgeneration, die nach wie vor auch auf dem Markt ist, werden durch die neuen Generationen etwa 1.000 t Messing, 1.300 t Edelstahl und 2.200 t EPDM pro Jahr eingespart. Andererseits werden für die neuen Schläuche jährlich 200 t Polyamid, 900 t PEX und 50 t Polyethylen zusätzlich eingesetzt. Insgesamt ergibt sich daraus eine Materialeinsparung von etwa 3.350 t. Unter Berücksichtigung der Emissionen der eingesparten und der neu eingesetzten Materialien werden jährlich etwa 8.000 t CO2e vermieden. Monetär betragen die jährlichen Einsparungen knapp 10 Mio. Euro.
Dadurch, dass das Re-Design in mehreren Entwicklungsschritten erfolgt ist, werden auch heute noch Anschlussschläuche der vorherigen Generation verkauft. Weiteres Einsparpotenzial würde sich durch die Umstellung aller Schläuche der Produktpalette auf die neueste Generation ergeben. Damit wäre es möglich, weitere 350 t Messing, 1.100 t Edelstahl, 400 t EPDM sowie die gesamten 900 t PEX einzusparen, gleichzeitig wären weitere 200 t Polyamid, und 1.000 t Polyethylen notwendig. In Summe könnten nochmals 1.600 t Material sowie 4.650 t CO2e vermieden werden und etwa 8 Mio. Euro eingespart werden.
Die Maßnahme zeigt, dass es sich lohnt, seit Jahren bestehende Designs zu hinterfragen und auf Verbesserungspotenziale hin zu untersuchen. Vorhandene Überdimensionierungen an Produkten können dabei als Ansatzpunkte für eine Verbesserung der Ressourceneffizienz dienen. Der verringerte Materialeinsatz macht sich auch für die Kunden in Form von geringeren Preisen und einer verbesserten Umweltbilanz bemerkbar und kann allgemeinen Kostensteigerungen in anderen Bereichen wie Energie und Transport entgegenwirken. Zudem konnte Neoperl seine Abhängigkeit von Zulieferern und die Anfälligkeit für schwankende Preise auf den Märkten durch die veränderte Materialauswahl reduzieren.
Die Neoperl Group ist führender Anbieter innovativer Lösungen rund ums Trinkwasser. Das inhabergeführte deutsch-schweizerische Unternehmen wurde 1959 gegründet und hat seinen Hauptsitz in Reinach-Basel (CH), der Hauptproduktionsstandort sowie das Zentrum für Forschung und Entwicklung sind in Müllheim (DE). Weltweit beschäftigt Neoperl rund 1.900 Mitarbeiterinnen und Mitarbeiter in 17 Ländern. Neoperl entwickelt und produziert Produkte, die den Wasserstrahl formen und die Durchflussmenge regeln. Diese leisten weltweit einen wertvollen Beitrag zum nachhaltigen Umgang mit der Ressource Trinkwasser.
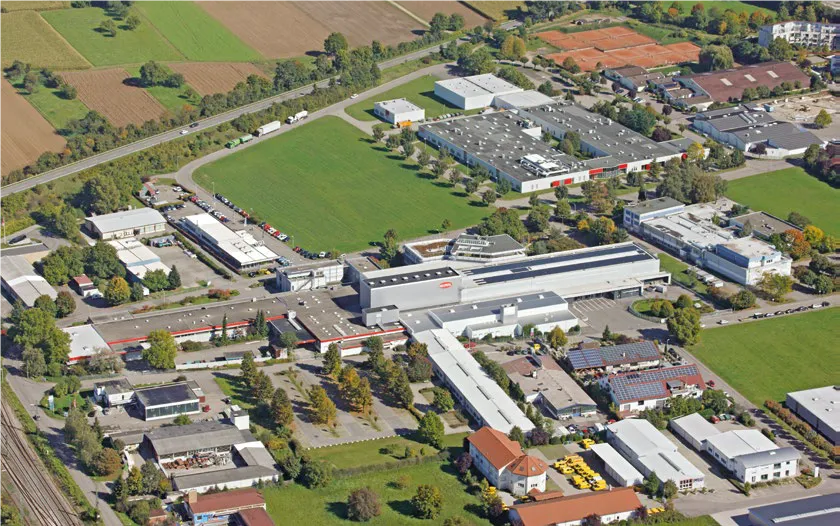
- Großserienfertigung
- Verarbeitungsprozess
- Energiekonzept
- Energie ,
- Material