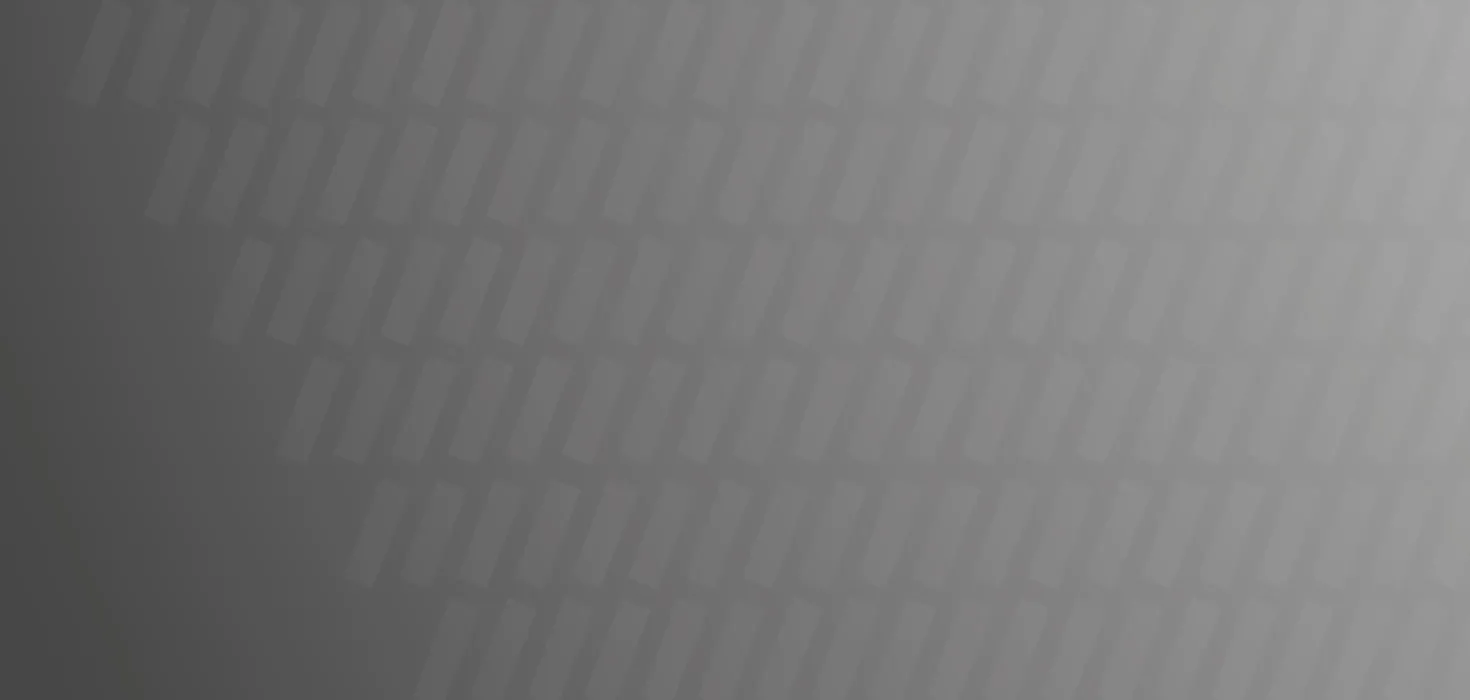
Spieglein, Spieglein an der Wand
Optimierung des Fertigungsprozesses von bedruckten Verpackungen
Die Gaster Wellpappe GmbH & Co. KG fertigt und verarbeitet Wellpappe in verschiedenen Ausführungen. Bei der Produktion kam es aus verschiedenen Gründen zu einem hohen Ausschuss, der durch dieses Projekt verringert werden sollte. Durch das Projekt konnte der Material- und Energieverbrauch reduziert werden, ohne die Effizienz des Prozesses und die Verfügbarkeit der Produktionslinie zu senken.
Die Gaster Wellpappe GmbH & Co. KG ist auf die Herstellung und Verarbeitung von Wellpappe spezialisiert. Im Heidelberger Werk Pfaffengrund fertigt das Unternehmen Verpackungen aus Wellpappe. Das Produktportfolio reicht dabei von der einfachen Zwischenlage für Sauerkonserven, über Stegsätze und Einlagen für Kombiverpackungen, bis hin zur fertigen Faltschachtel, die vom Kunden mit einem einzigen Handgriff aufgerichtet werden kann.
Die Verpackungen können individuell nach Kundenwünschen gestaltet werden. Eigene Deckenpapiere oder kaschierte Motive, sowie Druckbilder in mannigfaltigen Designs und Farben zählen zu den Gestaltungsmöglichkeiten.
Zusätzlich zum einkalkulierten und durch die Form der Verpackung bedingten Abfall, kann es durch die Eigenschaften des Rohmaterials Wellpappe bei komplexen Druckbildern zu einem erhöhten Ausschuss kommen.
Ziel des Projekts war es, Ansatzpunkte zu finden, diesen Ausschuss möglichst gering zu halten. Dadurch sollten die Material- und Energieressourcen geschont werden, ohne die Effizienz des Prozesses und die Verfügbarkeit der Produktionslinie zu senken.
Bisher wurden durch das Ziehen einer Probe alle 500 Stanzhübe, der Schnitt der Messer und der Versatz des Drucks kontrolliert. Dadurch konnten im Extremfall bis zu 500 Hub Ausschuss entstehen. Zur Verringerung dieses Ausschusses entstand die Idee einer häufigeren Kontrolle des IST-Zustands, um Prozessabweichungen früher zu erkennen und schneller beheben zu können. Gleichzeitig sollte gewährleistet sein, dass die Verfügbarkeit der Maschinen nicht beeinträchtigt wird. Es sollten Kontrollen im Produktionsfluss implementiert werden, ohne diesen wesentlich zu ändern.
Bei der Beobachtung des Produktionsablaufs wurde festgestellt, dass die gestanzten Bogenpakete bei der Abnahme der Ware um 90 ° aufgerichtet werden, um sie vor dem Palettieren besser ausrichten zu können. Dieser einzige Moment im Gesamtfertigungsprozess eignet sich, um das Druckbild zu überprüfen, ohne gleichzeitig in den Produktionsprozess eingreifen zu müssen.
Die qualitative Kontrolle des Druckstands ließ sich durch die Montage von mehreren Spiegelkacheln ohne Einsatz eines zusätzlichen Mitarbeiters erzielen. Mit der Installation einer Spiegelplatte am Querbalken des Nutzentrenners wird dem Abnehmer ein Kontrollblick auf den Druckstand ermöglicht. Eine schnelle Korrektur kann unmittelbar durch den Maschinenführer erfolgen. Zusätzlich werden die Produktionsmitarbeiter der Linie kontinuierlich geschult, um ihre Aufmerksamkeit weiter zu sensibilisieren.
Durch die Kontrollmöglichkeit pro Paket, alle 25 bis 40 Hub während des Produktionsprozesses, konnte der Ausschuss je nach Auftrag bis auf ein Zwanzigstel des bisherigen Maßes gesenkt werden. Die Gefahr einer unerkannten Weiterverarbeitung unzureichender Halbzeuge auf der Klebemaschine ist um bis zu 96 % gesunken. Neben der Einsparung von Wellpappe, Druckfarbe und Klebstoff konnte die Verfügbarkeit der Linien erhöht und der Energieverbrauch gesenkt werden.
Auch bei der Produktion der Wellpappe ist der, durch den gesunkenen Ausschuss, niedrigere Bedarf an Rohmaterial und Energie bemerkbar. Pro eingesparter Tonne Wellpappe werden CO2-Emissionen in Höhe von 887 kg vermieden. Die insgesamt erzielten Einsparungen werden jedoch erst im Folgejahr quantifizierbar sein, wenn sich die neuen Abläufe innerhalb des Produktionsprozesses vollständig etabliert haben.
Durch das weitgefächerte Produktportfolio von Gaster Wellpappe und die daraus resultierenden unterschiedlichen Produktionsprozesse können klassische Analyseverfahren zur Material- und Kostensenkung oft nicht greifen. Deshalb ist es unabdingbar, die Schnittstellen der einzelnen Teilprozesse genau zu betrachten, um diese zu egalisieren und einen möglichst glatten Produktionsfluss zu formen.
Der ganzheitliche Ansatz unter Berücksichtigung der Faktoren Mensch, Maschine und Produkt, kann auch bei weiteren Prozessen Verbesserungen bringen. Dazu ist es wichtig, die an den Fertigungsprozessen beteiligten Mitarbeiter einzubeziehen, um die richtige Balance zwischen Produkt- und Prozessanforderung zu finden.
Die familiengeführte Gaster Wellpappe GmbH & Co. KG wurde 1897 in Chemnitz gegründet und siedelte 50 Jahre später nach Heidelberg um. Im Jahr 1978 wurde das Werk Augsburg in Betrieb genommen und 1993 erfolgte die Gründung des Standorts Wieblingen. Ein weiterer Meilenstein war die Erweiterung des Hauptwerks in Heidelberg im Jahr 2010.
Nachhaltigkeit, Ressourcen- und Energieeffizienz sind wichtige Bestandteile des Unternehmensleitbilds.
Neben der Fertigung und Verarbeitung von Wellpappe betreut und berät das Unternehmen seine Kunden in allen Verpackungsfragen. Kundenorientierte Verpackungslösungen – von der individuellen Einzelverpackung bis hin zur Serienfertigung – zählen zu den Stärken des Familienunternehmens.
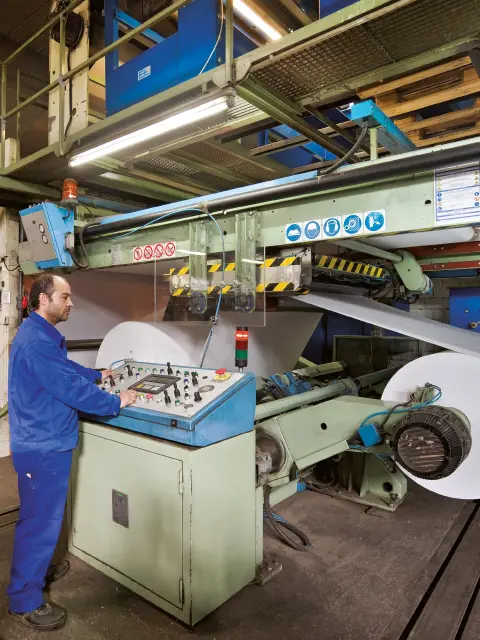
- Prozessindustrie
- Reparatur / Wartung
- Prozessinnovation
- Material ,
- Holz, Karton und Papier
- operativ (kleiner 1 Jahr)