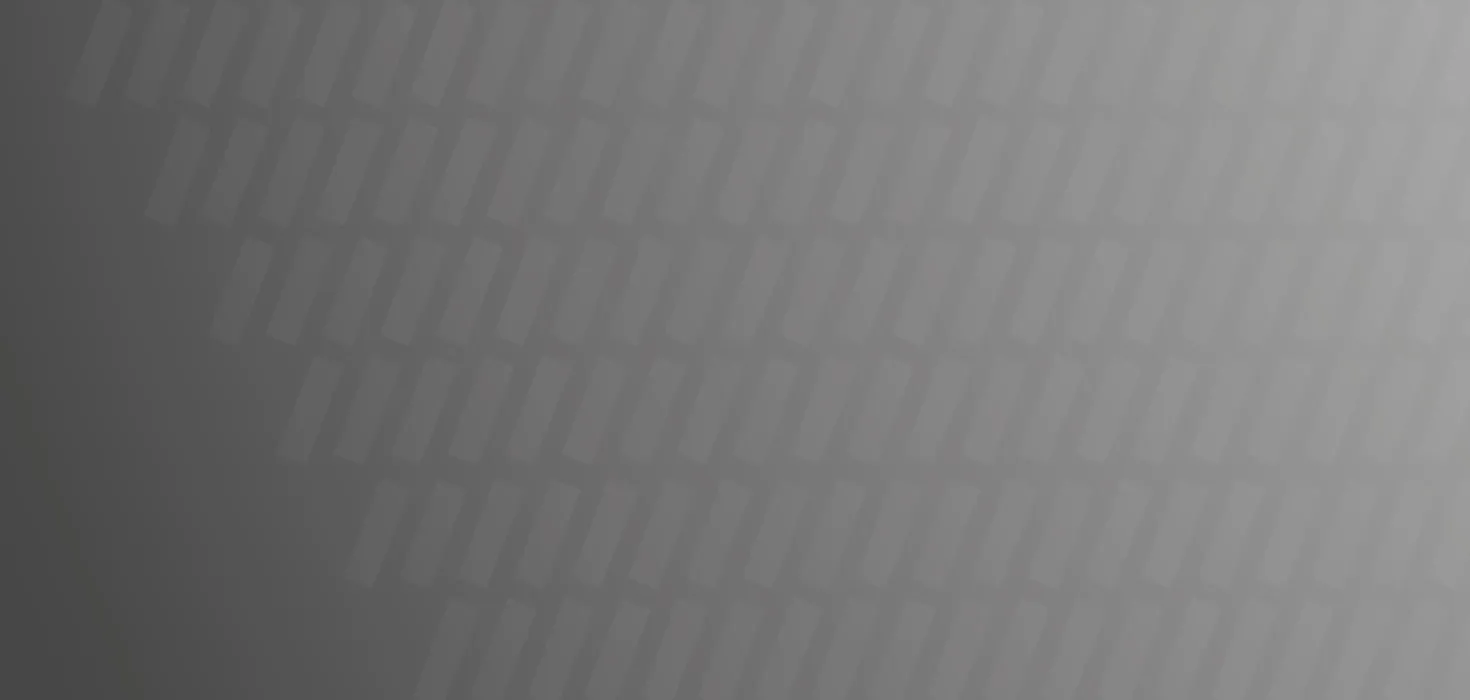
Umweltfreundliche Beschichtung durch Lackfolientechnik
Entwicklung einer neuartigen und umweltfreundlichen Lackbeschichtungstechnik
Stromeinsparung
CO2-Einsparung
Die Firma Wörwag entwickelt und produziert hochwertige Lacke für unterschiedliche industrielle Anwendungen. Das Ziel dieses Projektes war die Entwicklung eines Beschichtungsverfahrens, das deutlich umweltfreundlicher und ressourcenschonender ist als die herkömmlichen Verfahren. Dieses Verfahren erlaubt nun signifikante Einsparungen sowohl beim Energieverbrauch als auch beim eingesetzten Material.
Die Firma Wörwag entwickelt und produziert seit ihrer Gründung vor fast 100 Jahren hochwertige Lacke für industrielle Anwendungen. Das Unternehmen hat eine langjährige Expertise in der Beschichtung von Oberflächen und beschäftigt sich intensiv mit den Umweltaspekten beim Lackieren. Die Beschichtung von industriellen Produkten gilt als ein vergleichsweise ineffizienter Prozess. Bis heute ist in der Automobilindustrie der enorme Energieverbrauch für die Lackierprozesse ein bedeutender Faktor in der Produktion.
Zudem ist der Materialaufwand beim Beschichten von Fahrzeugkomponenten sehr hoch und mit hohen Materialverlusten verbunden. Außerdem treiben Fehlbeschichtungen den Materialaufwand in die Höhe. Bei bestimmten Bauteilen, wie etwa bei der Beschichtung von kritischen Oberflächen mit schwarzem Hochglanzlack, erreicht die Fehlbeschichtungsquote bis zu 40 %. Das Ziel des Projektes war die Entwicklung eines Beschichtungsverfahrens für industrielle Anwendungen, das deutlich umweltfreundlicher und ressourcenschonender ist als die herkömmlichen Verfahren. Der Energieaufwand sollte gesenkt werden und der eingesetzte Lack möglichst ohne Verluste genutzt werden. Prozessabfälle und Sondermüll sollten vermieden werden.
Die Nutzung von getrocknetem Lack in Form von aufgerollter Bahnware war die Lösung. Der Lack wird zunächst in einer Beschichtungsanlage als Lackfolie hergestellt. Er wird auf Bahnen angeliefert und während der Bauteileproduktion auf das Bauteil kaschiert. Um den Energieaufwand bei der Herstellung der Lackfolie möglichst gering zu halten, wird die Lackfolie in einer idealen Beschichtungsanlage produziert. Sie stellt sicher, dass das Trocknungsvolumen so klein wie möglich ist. Außerdem wurde der Lack auf das Trocknungsverfahren hin optimiert, damit Verdünner und Lösemittel schnell entweichen können. Der Einsatz eines Gießverfahrens beim Lackauftrag erlaubt eine 100-prozentige Materialausnutzung bei der Herstellung der Lackfolien.
Der Einsatz von Lackfolien für die Beschichtung bedeutet für den Bauteilhersteller, dass ein Auftragen und Trocknen von Flüssiglack auf den Bauteilen entfällt. Die Lackfolie selbst verfügt über eine Haftschicht, die sich über Wärme mit dem Bauteil verbindet. Idealerweise werden die Folien bei der Extrusion von Bauteilen in der Kunststoffschmelze aufgebracht. Nach dem Abkühlen der Bauteile haftet die Lackfolie darauf. Da die Lackfolie sämtliche Oberflächeneigenschaften eines Industrielacks besitzt und das Aufbringen der Folie keinen Einfluss auf die optischen und technischen Eigenschaften des Bauteils hat, verringern sich die fehlerhaften Beschichtungen. Selbst bei kritischen Oberflächen sinkt die Fehlbeschichtungsquote unter 5 %.
Im Rahmen des Forschungsprojekts „Umweltfreundliche Beschichtung durch die Lackfolientechnik“ wurde die erste Stufe des Projekts ausgearbeitet. Dabei setzte die Projektgruppe konventionelle Lackapplikationen zur Beschichtung von Kunststoffen ein. Auf Basis dieser Vorarbeiten entwickelte Wörwag ein Projekt mit einem deutlich höheren Energiesparpotenzial, das von der Deutschen Bundesstiftung Umwelt gefördert wurde.
Ein siebenköpfiges Team von Wörwag arbeitete 36 Monate an diesem Projekt - gemeinsam mit Lieferanten und Kunden des Unternehmens. Zunächst suchte das Projektteam nach einem idealen Trocknungsverfahren. Nach umfangreichen Versuchen kristallisierte sich eine in der Textilindustrie eingesetzte Trocknungstechnik als geeignetes Verfahren heraus. Es stellt jedoch extreme Anforderungen an die Trocknungseigenschaften des Lackes. In einem zweiten Schritt entwickelte die Projektgruppe einen Lack, der diese extremen Bedingungen erfüllte.
Zusammen mit einem Automobilhersteller sollte das Projekt in die Serienproduktion überführt werden. Die Aufgabe war es, Dachzierstäbe, auch Wasserabweiser genannt, mit der Lackfolie zu beschichten. Dabei sollte die Lackfolie bei der Extrusion der Kunststoffbauteile ohne zusätzliche Energie aufgetragen werden. Nach der erfolgsversprechenden Vorserienentwicklung wurde zusammen mit einem Anlagenhersteller eine Prototypenanlage zur Herstellung von Lackfolien, die als Transferlack bezeichnet werden, entwickelt. Innerhalb eines Jahres wurde die Entwicklung des Lackaufbaus abgeschlossen und der Beschichtungsprozess optimiert.
Anschließend entwickelte die Arbeitsgruppe zusammen mit dem Kunden einen Prozess zur Herstellung von Bauteilen mit integriertem Lackauftrag bis zur Serienreife. Bereits drei Jahren nach Projektbeginn wurde eine Produktionsanlage zur Großserienherstellung von Transferlack errichtet. Heute produziert diese Anlage täglich Transferlack zur Beschichtung von 7.000 bis 8.000 Teilen. Diese werden vor allem von der Daimler AG in den Mercedes-Benz-Fahrzeugreihen eingesetzt. Die Zusammenarbeit mit Daimler war maßgeblich für die Entwicklung des Projekts. Weiterhin waren auch die Bauteilehersteller Silvatrim S.A.M sowie SMIA (Samvardhana Motherson Innovative Autosystems) beteiligt
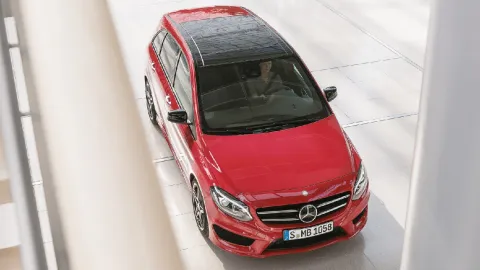
Das neue Beschichtungsverfahren erlaubt signifikante Einsparungen sowohl beim Energieverbrauch als auch beim eingesetzten Material. Es verringert überdies die Umweltbelastung erheblich. Die Energieeinsparungen sind enorm: Der gemessene Energieverbrauch liegt beim Einsatz von Transferlack bei 0,95 kWh pro Quadratmeter beschichteter Fläche. Das sind rund 15 % des Energieaufwands in Höhe von 6,5 kWh pro Quadratmeter, der bei herkömmlichen Beschichtungsverfahren benötigt wird.
Da in der Automobilproduktion heute eine Fläche von rund 280.000 m² mit diesem innovativen Verfahren beschichtet wird, ermöglicht der Einsatz der Lackfolientechnik eine Einsparung beim Stromverbrauch von 1.554.000 kWh pro Jahr und ist mit einer Reduktion von CO2-Emissionen in Höhe von 895,1 t verbunden. Hinzu kommen Materialeinsparungen beim Lack und der Bauteilefertigung durch effizientere Materialnutzung. Der Einsatz der Lackfolien verringert den Prozessabfall beim Beschichten. Während beim herkömmlichen Lackauftrag lediglich 50 bis 70 % des eingesetzten Lacks für das Beschichten der Bauteile verwendet werden, liegt die Quote beim Einsatz der Folien bei 85 %.
Außerdem wird durch den Einsatz der Lackfolie der Ausschuss an Fertigbauteilen signifikant gesenkt. Beim sogenannten Firstrun wird eine Beschichtungsquote von 94 bis 95 % erreicht – inklusive Fehler und Ausfallteile durch das Starten und Stoppen der Extrusion. Allein bei der Beschichtung ist bei herkömmlichen Lackierverfahren mit einer Ausfallrate von mindestens 30 % zu rechnen.
Um ein visionäres Forschungsprojekt wie die umweltfreundliche Beschichtung durch Lackfolientechnik realisieren zu können, sind einige Voraussetzungen nötig. Grundbaustein ist ein freigestelltes Team mit einem Projektleiter, die gemeinsam fokussiert an dem Thema arbeiten. Außerdem wird ein Auftraggeber benötigt, der wie Wörwag voll und ganz hinter dem Projekt steht. Ein starker Partner ist ebenfalls notwendig, der wie die Daimler AG, ein großes Interesse an der Entwicklung und Umsetzung des Themas hat. Viele gute Ideen, jede Menge Durchhaltevermögen und in manchen Phasen auch eine Portion Glück gehören dazu, um ein innovatives Projekt bis zur Serienreife zu führen.
Zu den überraschenden Erkenntnissen bei diesem Projekt gehörte das sehr hohe Einsparpotenzial beim Energieverbrauch. Niemand hatte dies für möglich gehalten. Dabei wurde das Einsparpotenzial bislang noch nicht vollständig ausgeschöpft. Eine weitere Überraschung war die Dynamik, mit der sich das Projekt entwickelte. Bereits im zweiten Jahr der Fertigung reichte die Kapazität der Prototypenanlage nicht mehr aus. Eine leistungsfähigere Serienanlage musste aufgebaut werden. Inzwischen ist die Lackfolientechnik ein fester Bestandteil der Wachstumsstrategie von Wörwag. Die bestehende Beschichtungsanlage wird in den nächsten Jahren weiter ausgebaut. Außerdem soll das Angebot auf weitere Bauteile für die Autoindustrie und auf die Beschichtung von Fenstern erweitert werden. Der geplante Ausbau zielt auf die Erhöhung der Produktionsmenge und auf die Vergrößerung der produzierten Folienbreite. Die Prototypenanlage konnte Lackfolien mit einer Breite von maximal 60 cm beschichten. Die heutige Serienanlage erlaubt die Beschichtung von 100 cm breiten Folien. In Zukunft sollen Folien mit einer Breite von bis zu 142 cm beschichtet werden. Mit diesem Format lassen sich alle Plattenbeschichtungsprozesse in der Industrie abdecken. Fassaden, Türen und Möbel können dann mit Hilfe von Lackfolien umweltfreundlich beschichtet werden.
Die Karl Wörwag Lack- und Farbenfabrik GmbH & Co KG entwickelt und produziert seit ihrer Gründung 1918 hochwertige Lacke für unterschiedliche industrielle Anwendungen. Das Familienunternehmen betreibt heute Werke in Deutschland, Polen, Schweiz, Spanien, China, Südafrika und den USA und beschäftigt rund 1.000 Mitarbeiter. Wörwag stellt in umweltschonenden Verfahren nach Vorgaben professioneller Anwender hochwertige Beschichtungsmittel her und liefert sie in die ganze Welt. Zudem berät Wörwag seine Kunden bei der Optimierung von Lackierprozessen.
- Großserienfertigung
- Entwicklung / Konstruktion ,
- Verarbeitungsprozess
- Produktinnovation
- Energie ,
- Material ,
- Chemieprodukte ,
- Abgas
- strategisch (größer 5 Jahre)