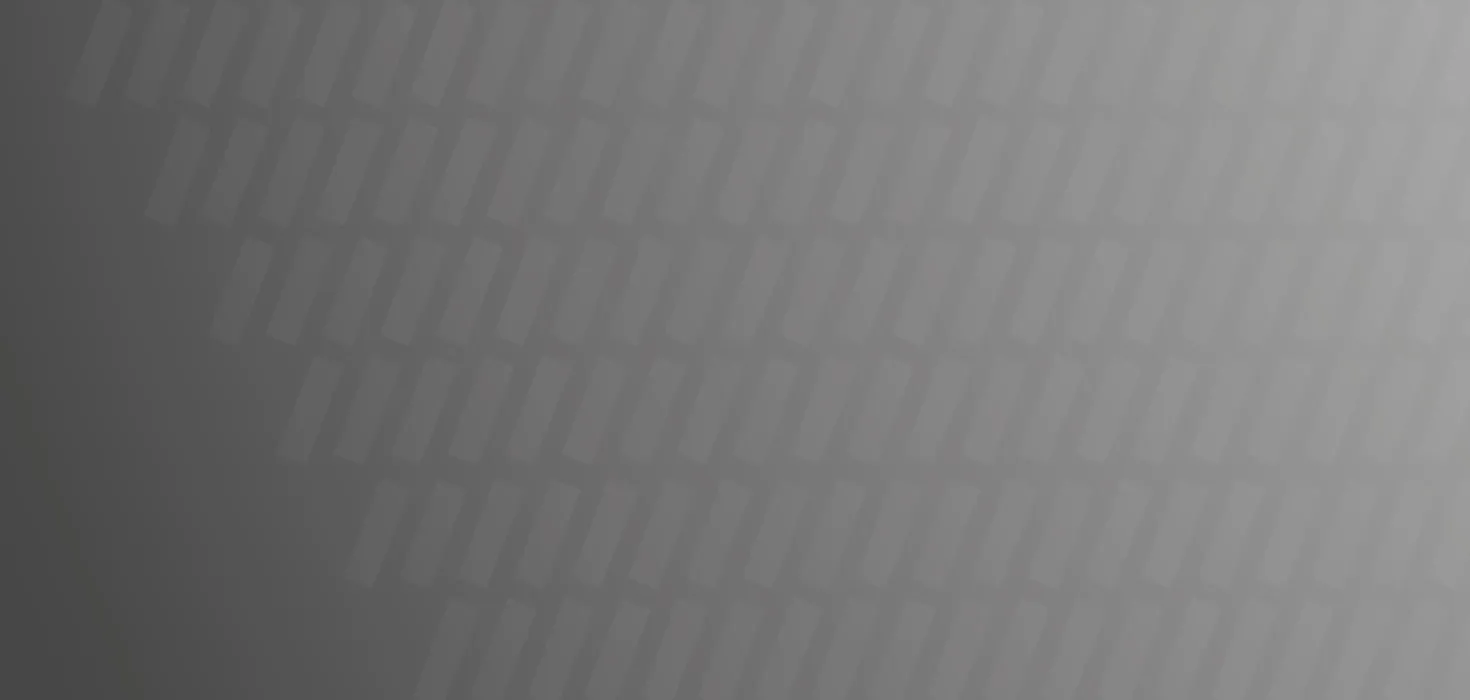
Weniger ist mehr – Fahrweisenoptimierung in der Lackiererei
Optimierte Prozesssteuerung in der Lack-Vorbehandlung
Abwasserreduktion
Energieeinsparung
CO2-Einsparung
Die Porsche AG mit Sitz in Stuttgart-Zuffenhausen steht als einer der profitabelsten Automobilhersteller für wertschaffendes Wachstum. Bis zum Jahr 2025 will das Unternehmen seine Umweltauswirkungen der Produktion signifikant reduzieren. Aus diesem Grund wurde die Prozesssteuerung für die Lack-Vorbehandlung so optimiert, dass eine große Menge an Chemikalien und Frischwasser eingespart werden.
Porsche hat sich für den Bereich Umwelt und Energie das strategische Ziel gesetzt, die Umweltauswirkungen der Produktion bis zum Jahr 2025 um 45 % gegenüber dem Jahr 2014 zu reduzieren. Die Reduzierung basiert auf den Umweltindikatoren Abfall, CO2, Energie, VOC (Volatile Organic Compounds) und Wasser. Um langfristig und nachhaltig Ressourcen einzusparen, setzt Porsche an den Produktionsstandorten seit dem Jahr 2014 eine interne Ressourceneffizienzstrategie um. Mit der verbindlichen Integration dieser Strategie entwickeln die Mitarbeiterinnen und Mitarbeiter von Porsche kontinuierlich eigene Lösungen zur Etablierung von Ressourceneinsparungen in der Produktion. Des Weiteren dienen die Effizienzprogramme als Qualitätssicherungsmaßnahmen, da durch die konsequente Suche nach Optimierungen die einzelnen Prozesse und Abläufe in der Produktion nachhaltig verbessert werden können.
Ein solches Ressourceneffizienzpotenzial wurde auch in der Lackiererei in Zuffenhausen identifiziert. Dort durchlaufen die einzelnen Fahrzeugkarosserien zur Vorbereitung auf den Lackierprozess in der kathodischen Tauchlackierung (KTL) insgesamt zehn Vorbehandlungsbecken, sogenannte Zonen. Die Becken sind durch Überlaufzonen kaskadenartig miteinander verbunden. Über ein Shuttlesystem werden die Karosserien von Becken zu Becken transportiert und rotieren in den jeweiligen Zonen, um Lufteinschlüsse zu vermeiden.
Die Vorbehandlungsprozesse lassen sich wie folgt beschreiben: In den Zonen 1 bis 3, der Tauchentfettung, werden bei 65 °C grober Schmutz und Fettreste mit Hilfe von Reinigungsmitteln und Tensiden entfernt. In Zone 4 erfolgt eine Spülung in vollentsalztem Wasser, um die Verschleppung von Reinigungsmitteln zu verhindern. Die Tauchaktivierung in Zone 5 gewährleistet die Bildung einer gleichmäßigen Grundierungsschicht. Die Spritzphosphatierung erfolgt in Zone 6, um mit Hilfe einer Phosphatlösung die Stahl-Alu-Karosserie zu beschichten. In den Zonen 7 und 8 findet ein Spülen mit vollentsalztem Wasser statt, um freigewordenes Aluminium von der Karosserieoberfläche zu entfernen. In Zone 9 wird eine Tauchpassivierung mit Hilfe von Titanoxid vollzogen, welches eventuelle Fehlstellen besetzt und so für eine schützende Passivschicht sorgt. Abschließend kommt es in Zone 10 nochmals zu einer Spülung mit vollentsalztem Wasser, um alle Reaktionen abzubrechen und alle überschüssigen Substanzen von der Fahrzeugoberfläche zu entfernen.
Wiederholte Analysen und Überprüfungen der chemischen Zusammensetzungen in den Zonen 1 bis 4 haben gezeigt, dass die Fahrweise und Prozessführung der Tauchentfettung in Zone 2 optimiert werden kann. Die Fahrweise der Wasserkreisläufe und der chemischen Zusammensetzung der Entfettungskaskade erfordern dazu eine bedarfsgerechte Prozesssteuerung. Im bisherigen Zustand der Fahrweise konnten die Füllstandsonden in den Vorbehandlungsbecken den Anforderungen an eine feinere Steuerung jedoch nicht gerecht werden. Das Becken konnte nicht ausreichend nachgefüllt werden, um den Überlauf der ölhaltigen Bestandteile an der Oberfläche des Bades optimal abzuschwemmen. Reiniger- und Tensidverluste waren die Folge, wodurch die Chemikaliennachspeisung insgesamt zu hoch war.
Ziel des internen Effizienzprojekts war es, die chemische Taktdosierung sowie die Wasserkreisläufe effizienter zu regeln und so den Bedarf an Chemikalien und Wasser zu reduzieren.
Die notwendige Feindosierung sollte über Nachspeiseventile erfolgen, die sich sekundengenau und für jede Zone getrennt voneinander steuern lassen. Die ungenauen Füllstandsonden sollten als Sicherungslinien beibehalten werden.
Die Wasserkreisläufe wurden so eingestellt, dass die chemische Zusammensetzung aller Zonen nur durch die Chemikaliendosierung in Zone 3 gewährleistet wird. In Zone 2 werden nun keinerlei Reiniger und Tensid zugeführt. Die umfangreichen Änderungen an der Kaskadenfahrweise wurden in einen neuen Prozessstandard zur Steuerung der Überläufe überführt und im Handbuch für ressourceneffiziente Produktion dokumentiert. Dieser beinhaltet die Programmierung einer Plausibilitätsbegrenzung bei den Hand- und Taktdosierungen, individuell für jede Dosierstation. Dazu wurden die Beckenstandzeiten und die chemischen Eingriffsgrenzen optimiert sowie ein Standard zur täglichen Kontrolle der Kaskadenparameter eingeführt.
Neben der Anpassung der Reinigungszyklen erfolgt auch eine Qualitätserfassung, die siebenmal am Tag durchgeführt wird. Die Umsetzung der Ressourceneffizienzmaßnahme erfolgte innerhalb von drei Monaten. Die neue Fahrweise im Vorbehandlungsprozess ist seit zwei Jahren am Standort Zuffenhausen erfolgreich im Einsatz und wird fortlaufend optimiert.
Die Optimierungen der Prozesssteuerung haben den Verbrauch von vollentsalztem Wasser und Chemikalien nachhaltig reduziert. Weiterhin sind mit der bedarfsgerechten Prozesssteuerung auch Einsparungen von Betriebskosten verbunden. Zudem war die Lagerkapazität für Reiniger und Tenside beschränkt.
Insgesamt beträgt die jährliche Einsparung an Chemikalien, d. h. an Reinigern, Tensiden und pH-Regulatoren, rund 60 t und die aufbereitete Frischwasserzugabe reduziert sich um 5.500 m³. Durch die Reduzierung des Überlaufs aus den Zonen verringert sich die jährlich anfallende Abwassermenge um ca. 4.600 m³. Die Einsparung an elektrischer Energie für die Aufbereitung des Frischwassers in vollentsalztes Wasser beträgt 7,42 MWh jährlich, das entspricht 3,14 t CO2.
Das unternehmensinterne Ressourceneffizienzprogramm hat kontinuierliche Verbesserungen fest im Produktionsalltag bei Porsche verankert. Dies hilft nicht nur dabei, das strategische Umweltentlastungziel zu erreichen, sondern führt auch zu jährlichen Einsparungen in Höhe von rund einer Million Euro an den Produktionsstandorten Zuffenhausen, Sachsenheim und Leipzig.
Die einzelnen Ressourceneffizienzmaßnahmen werden in einer Datenbank dokumentiert und können so für den internen Austausch und für weitere Projekte verwendet werden. Als weitere Effizienzpotenziale im Lackierprozess wurden aus den Erfahrungen des Projekts die Umstellung von Spritz- auf Tauchphosphatierung sowie das übergelaufene Filtrat aus den Zonen 2 und 3 erkannt. Dieses kann zusätzlich intern aufbereitet und dann wiederverwendet werden, um noch mehr Chemikalien und Wasser einzusparen. In weiterer Folge führt dies zu einer noch stärkeren Abwasservermeidung. Diese Prozessoptimierungen werden für die neue Lackiererei des Mission E eingesetzt.
Die Dr. Ing. h.c. F. Porsche AG mit Sitz in Stuttgart-Zuffenhausen steht als einer der profitabelsten Automobilhersteller für wertschaffendes Wachstum. Im Jahr 2016 hat Porsche die weltweiten Auslieferungen auf 237.778 Fahrzeuge gesteigert und damit die Bestmarke aus dem Vorjahr um 6 % übertroffen. Auch die Belegschaft ist in diesem Zeitraum um 13 % auf 27.612 Beschäftigten angewachsen.
Porsche produziert an den Standorten Zuffenhausen sowie Leipzig und betreibt ein Entwicklungszentrum in Weissach. Porsche war der erste Automobilhersteller im Premiumsegment, der mit dem Cayenne, dem Panamera S E-Hybrid und dem 918 Spyder drei Plug-in-Hybridmodelle anbot. Ende dieses Jahrzehnts bringt Porsche mit dem Mission E den ersten rein elektrisch betriebenen Sportwagen auf die Straße.

- Großserienfertigung
- Produktionsplanung / -steuerung
- Prozessoptimierung
- Energie ,
- Material ,
- Trinkwasser ,
- Chemieprodukte ,
- Abwasser ,
- Abgas
- operativ (kleiner 1 Jahr)