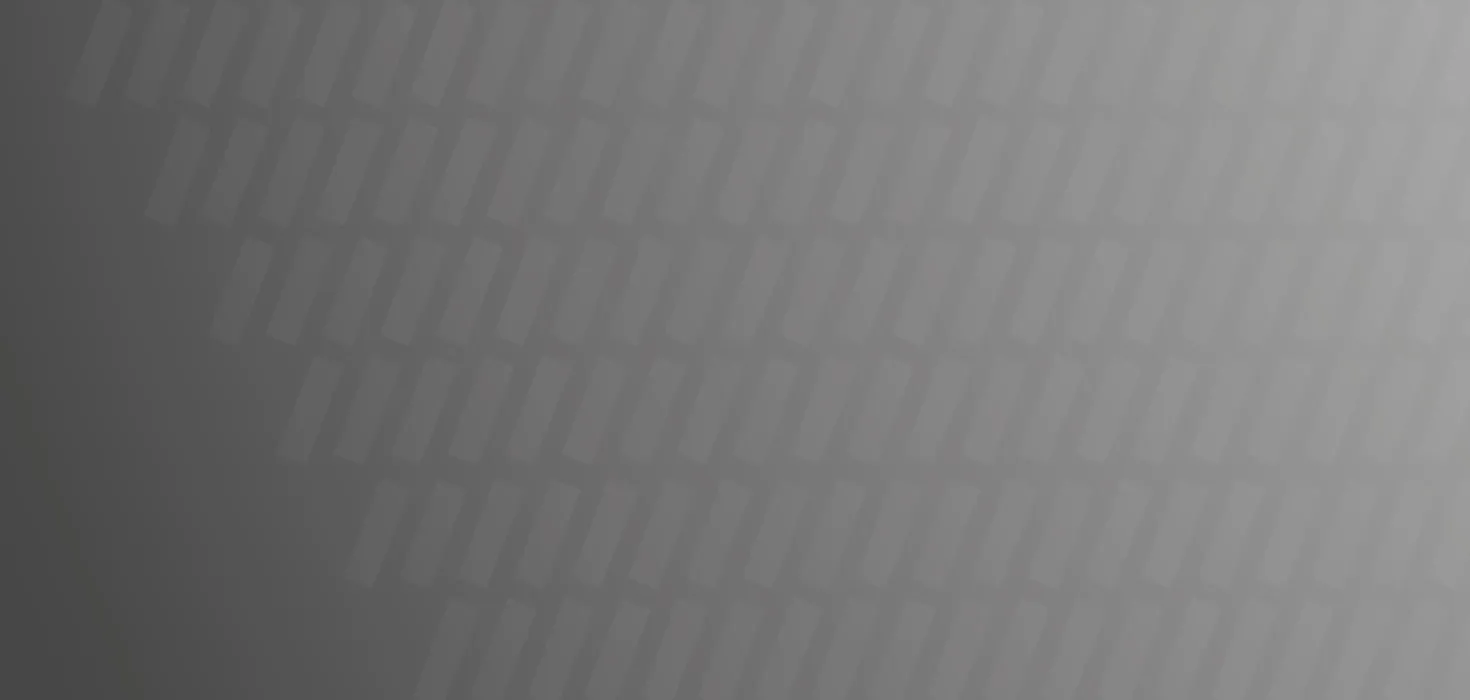
Weniger ist mehr – Optimierung mit der Finite Elemente Methode
Minimierung des eingesetzten Materials und Reduktion der Prozesszeiten
Neumaterialeinsparung
Das Unternehmen Interstuhl gilt mit seinem Angebot an Büromöbeln als Spezialist für professionelles Sitzen. Das Ziel war es, bei der Produktion von Fußkreuzen sowohl Material als auch Prozesszeit einzusparen. Dadurch konnten auch die Herstellkosten reduziert werden und gleichzeitig die Produktivität erhöht werden. Durch ein neues Design konnte das Unternehmen dieses Ziel umsetzen.
Das Unternehmen Interstuhl agiert mit zwei starken Marken. Die Marke Interstuhl umfasst alle Arten des Sitzens im Büro und Objektbereich, die Marke Bimos ist die führende Marke für beste Industrie-und Laborstühle in Europa. Tagtäglich werden rund 3.500 Stühle am Standort Meßstetten produziert und in die ganze Welt ausgeliefert. Mit ihren qualitativ wie gestalterisch erstklassigen Bürositz- und Konferenzmöbeln, Kommunikationseinrichtungen, Chefzimmereinrichtungen, Regenerationsmöbeln, sowie Produktions-, Labor- und Reinraumstühlen erzielt das Unternehmen Interstuhl derzeit einen jährlichen Werksumsatz von 130 Mio. Euro.
Interstuhl hat sich zur kontinuierlichen und nachhaltigen Verbesserung des betrieblichen und allgemeinen Umweltschutzes verpflichtet. In diesem Sinne steht auch die Ressourceneffizienz der Produkte immer wieder auf dem Prüfstand. Hierbei haben sich vor allem beim Fußkreuz unter dem Aspekt des Designs for Environment erhebliche Optimierungspotenziale gezeigt. Anlass für das Redesign des besagten Fußkreuzes war die geplante Ersatz- bzw. Neubeschaffung eines Spritzgusswerkzeugs. Gleichzeitig sollte der Durchmesser des Fußkreuzes vergrößert werden, um den Anforderungen hinsichtlich Kippsicherheit gerecht zu werden.
Das Ziel war es, den Materialeinsatz zu minimieren. Dies wurde bspw. durch die Reduktion der Wandstärken angestrebt, welche wiederum schnellere Prozesszeiten gewährleisten sollten. Durch die Verringerung des Materialeinsatzes und durch die Verringerung der Prozesszeit sollten folglich auch die Herstellkosten gesenkt und die Produktivität gesteigert werden.
In einem Design for Environment-Prozess sollte durch eine Ermittlung des minimalen Materialeinsatzes bei gleichbleibenden Festigkeitsanforderungen das Fußkreuz neu gestaltet werden. Zur Anwendung kam hierbei die Finite-Elemente-Methode (FEM). Mit Hilfe dieser Methode können Bauteile am Computer virtuell berechnet werden. Außerdem kann eine Simulierung von unter Krafteinfluss auftretenden Verformungen und Spannungen vorgenommen werden. Der Vorteil hierbei ist, dass die Geometrie der Bauteile direkt aus CAD-Programmen eingelesen und weiterverarbeitet werden kann. Dabei ist es auch irrelevant, aus welcher Branche die Bauteile stammen. Mit Hilfe der mit dem Programm erstellten Prototypen können bereits deutlich vor dem Fertigungsprozess Entwicklungszeit und Kosten eingespart werden, denn mögliche Fehler konstruktiver Art werden bereits vorher erkannt und vermieden, zumal teure und zeitintensive Prototypen in dieser frühen Phase erst gar nicht gebaut werden müssen.
Bei der Anwendung der Finite-Elemente-Methode mussten einige Dinge beachtet werden. So müssen die physikalischen Randbedingungen einer Konstruktion hinsichtlich Geometrie, Material, sowie die Lasten bekannt sein. Erst dann kann das Verhalten eines kompletten Bauteils vorhergesagt werden. Dazu wurde das zu untersuchende Bauteil in eine endliche (finite) Anzahl von Subbereichen (Elementen) unterteilt. In den Subbereichen können durch diese Aufteilung die mechanischen Zusammenwirkungen und Wechselwirkungen leichter beschrieben werden. Durch im Computerprogramm entsprechend hinterlegte Algorithmen konnte eine effiziente Berechnung des Gesamtverhaltens des Bauteils und dessen Struktur durchgeführt werden.
Die Erstellung eines realistischen Modells setzte aber noch zwei weitere Aspekte voraus. Das Verfahren konnte erst dann sinnvoll eingesetzt werden, als der Berechnungsingenieur eine gute Vorstellung von den auf das Bauteil wirkenden Belastungen und den eventuell auftretenden Effekten hatte. Außerdem musste zur Anwendung der Finite-Elemente-Methode bekannt sein, über welche Eigenschaften und Fähigkeiten die unterschiedlichen Elemente verfügen, bspw. hinsichtlich der möglichen Nichtlinearitäten. Erst als diese Voraussetzungen gegeben und die notwendigen Kenntnisse vorhanden waren, konnte die Erstellung eines gültigen und effizienten Berechnungsmodells vorgenommen werden.
Bei Interstuhl konnten diese Voraussetzungen bestens erfüllt werden. Interstuhl verfügt nicht nur über ein im Jahr 2009 neu erbautes Zentrum für Forschung, Entwicklung & Konstruktion, welches technologisch auf dem neuesten Stand ist, sondern hat auch die Kompetenz, die Methode entsprechend verlässlich und effizient anwenden zu können. Dabei spielen unter anderem die bei Interstuhl im Bereich der Finite-Elemente-Methode tätigen Mitarbeiter eine bedeutende Rolle. Mit ihrer Erfahrung und Kompetenz, welche sie in den letzten Jahren bzw. Jahrzehnten erworben haben, konnten sehr präzise und verlässliche Aussagen über die Eigenschaften und Fähigkeiten der Sub-Elemente gemacht werden.
Mit diesem großen Know-how war es möglich, die minimale Geometrie zur Erfüllung der Anforderungen als Grundlage der Neuentwicklung bestimmen zu können. An diesem Prozess waren nicht nur Mitarbeiter von Interstuhl beteiligt, sondern auch ein externes Büro für Festigkeitsberechnungen, um die bestmögliche Anwendung der Finite-Elemente-Methode zu gewährleisten.
Das Design for Environment mit der Finite-Elemente-Methode führte zu einer Reduzierung des Bauteilgewichts von 1.850 g auf 1.580 g, also um 270 g pro Einheit. Dies entspricht bei 250.000 produzierten Einheiten einer Reduzierung von 67,5 t Polyamid mit einem Wert von über 100.000 Euro pro Jahr. Wird der Recyclatanteil von 15 % pro Einheit, also 237 g, mit eingerechnet, führt dies bei 250.000 Einheiten zu einer nochmaligen Einsparung von 59,25 t Recyclat im Jahr. Dies entspricht einer jährlichen Gesamteinsparung an Neumaterial von 126,75 t.
Das Unternehmen hat im Vorfeld des Projekts nicht damit gerechnet, dass derart große, kumulierte Einsparungen durch die Anwendung der Finite-Elemente realisierbar sind. Die vorhandenen Einsparpotenziale haben Interstuhl darin bestätigt, die Finite-Elemente-Methode weiterhin verstärkt im Entwicklungszyklus einzusetzen, um Festigkeitsanforderungen möglichst gewichtsoptimiert erreichen zu können und um somit kein Material zu verschwenden und Überdimensionierungen zu vermeiden. Folglich ist im nächsten Schritt die Umsetzung des Design for Environment-Ansatzes bei Fußkreuzen weiterer Stuhlmodelle geplant.
Mit viel Leidenschaft und noch mehr Sachverstand bauten im Jahre 1961 Vater Wilhelm und Sohn Werner Link in der Dorfschmiede im schwäbischen Meßstetten-Tieringen ihren ersten Stuhl und veränderten damit die Arbeitswelt. Mit der bi-regulette wurde zu diesem Zeitpunkt erstmals ein leistungsstarkes Arbeitsstuhlmodell zur Entlastung des Menschen für gesündere Arbeitsbedingungen angeboten und der Grundstein für eine erfolgreiche Unternehmensentwicklung gelegt. Bis heute ist das Familienunternehmen Interstuhl seinem Traditionsstandort auf der schwäbischen Alb treu geblieben – und dem Ziel, erfolgreiche Stuhl-Konzepte für die Zukunft zu entwickeln. Nicht umsonst gilt Interstuhl heute als der Spezialist für professionelles Sitzen.
Interstuhl wurde im Jahr 1993 als erstes Unternehmen der Branche nach DIN EN ISO 9001 zertifiziert und vom Umweltministerium des Landes Baden-Württemberg schon im Jahr 1994 für „herausragende Leistungen bei der Förderung des betrieblichen Umweltschutzes und der umweltorientierten Unternehmensführung“ ausgezeichnet. Außerdem erhielt Interstuhl als einer der Ersten der Branche die EMAS-Zertifizierung und ihre Produkte wurden als erste mit dem Blauen Engel ausgezeichnet.
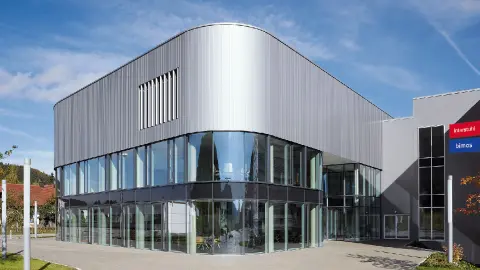
- Großserienfertigung
- Entwicklung / Konstruktion
- Produktinnovation ,
- Industrie 4.0 / Digitalisierung
- Material ,
- Kunststoffe
- operativ (kleiner 1 Jahr)