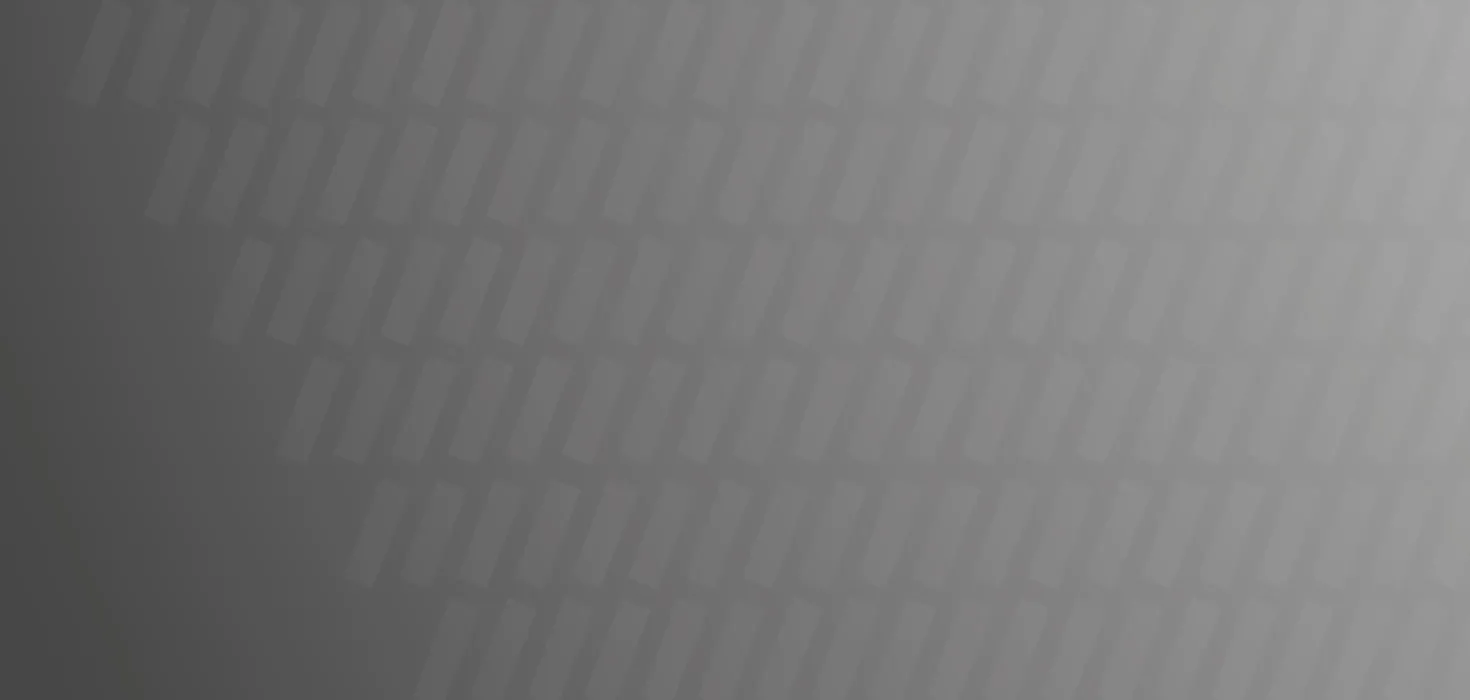
Digitaler Zwilling ermöglicht virtuelle Inbetriebnahme
Einsatz einer Software zur Vorab-Testung von Lagersystemen und frühzeitiger Fehlererkennung
Stromeinsparung
CO2e-Einsparung
Dieseleinsparung
CO2e-Einsparung
Die KASTO Maschinenbau GmbH & Co. KG hat den Prozess der Inbetriebnahme seiner vollautomatischen Lagersysteme digitalisiert. Dadurch wird der zeitliche und energetische Aufwand bei der Inbetriebnahme reduziert. Unnötige Probeläufe und Nacharbeit werden dabei vermieden, was den Energie- und Ressourceneinsatz wesentlich verringert.
Mit seinen Metallsägemaschinen, halbautomatischen und automatischen Lagersystemen, automatischen Handlingseinrichtungen für Metallstäbe, Bleche und Zuschnitte, sowie der dazugehörigen Software ist KASTO mit Sitz im badischen Achern weltweit führend.
Bislang war die Inbetriebnahme von vollautomatischen Lagersystemen enorm zeit- und energieintensiv. Die einzelnen Anlagenkomponenten müssen beim Kunden vor Ort verbunden und Schnittstellen gekoppelt werden. Dafür sind die KASTO-Techniker täglich vor Ort, was mit hohen Kosten und großer Arbeitsbelastung einhergeht. Zusätzlich ist die Inbetriebnahme mit hohen Umweltbelastungen aufgrund von Energieverbrauch verbunden. Hinzu kommen nachträgliche Anpassungen und Nacharbeiten, die wiederum beim Kunden vor Ort durchgeführt werden müssen.
KASTO vernetzt schon heute seine Produkte und setzte sich daher das Ziel, Industrie-4.0- Lösungen auch bei der Inbetriebnahme von Lagersystemen einzusetzen, um Ressourcen einzusparen und noch wettbewerbsfähiger zu werden. Hierfür sollte eine entsprechende Lösung für die virtuelle Inbetriebnahme entwickelt werden.
Bevor ein Lager in Betrieb genommen wird, digitalisiert eine Software die gesamten Prozesse. Mit dem so entstandenen digitalen Zwilling werden reale vollautomatische Lagersysteme vorab digital entwickelt und getestet. Probleme, die bisher erst vor Ort aufgefallen sind, können so frühzeitig erkannt und behoben werden – Nacharbeiten beim Kunden werden sich reduzieren oder ganz entfallen.
Zusammen mit Siemens und dem Systemhaus BCT verwirklichte KASTO die virtuelle Inbetriebnahme. Während Siemens die Software für die Virtualisierung der Hardware lieferte, unterstützte BCT bei den Themen CAD und digitaler Zwilling. Gemeinsam mit seinen Projektpartnern entwickelte KASTO folgenden Prozess für die virtuelle Inbetriebnahme.
KASTO erstellt mithilfe der entsprechenden CAD-Dateien den digitalen Zwilling der fertig geplanten Anlage. Es wird eine Software verwendet, die Kinematik auf CAD-Modelle anwendet und so ein dynamisches, mechatronisches 3D-Modell der gesamten Anlage entstehen lässt. Sobald das SPS-Programm und das Lagerverwaltungsprogramm entwickelt wurden, können diese drei Teile über definierte Schnittstellen verbunden und getestet werden. Während der virtuellen Inbetriebnahme wird die komplette Hardware in Form von Steuerungen und deren Peripherie, wie bspw. Sensoren und Aktoren, virtualisiert und mit dem digitalen Zwilling verschaltet. Eine virtuelle Steuerung kontrolliert alle Abläufe des Modells. Über das digital angebundene Lagerverwaltungsprogramm werden verschiedene Aufträge gestartet und die komplette Anlage inklusive der Mechanik, Elektrik und Software in Form des digitalen Zwillings auf die volle Funktionstüchtigkeit geprüft. Auftretende Fehler können so frühzeitig erkannt und direkt behoben werden.
Mithilfe der virtuellen Inbetriebnahme verbessert KASTO, noch bevor die Anlage das Haus verlässt, die Softwarequalität und testet vorab ganze Use-Cases. Dies reduziert die notwendige Präsenzzeit beim Anwender. Durch entfallene Hotel- und Fahrtkosten entstehen weitere finanzielle Vorteile. Durch die geringere Anzahl an Fahrten lässt sich CO2 einsparen und damit die Umwelt entlasten. Die Mitarbeiter profitieren von geringeren und kürzeren Außeneinsätzen.
Auch der Kunde hat durch die virtuelle Inbetriebnahme Vorteile. Die Dauer der Inbetriebnahme verkürzt sich durch die Vorabtests deutlich, dadurch sinken die Kosten und die Anlage ist schneller verfügbar. Darüber hinaus bleibt der vorab erstellte digitale Zwilling für die gesamte Lebensdauer der Anlage erhalten. KASTO könnte damit den Anwender auch im laufenden Betrieb optimal bei der Wartung, Instandhaltung oder Fehlerdiagnose direkt unterstützen.
Noch steht der erste Praxiseinsatz der virtuellen Inbetriebnahme aus. Auf Basis von Nacharbeitslisten vergangener Projekte kann die Höhe möglicher Einsparungen jedoch abgeschätzt werden. Nach der Auswertung zweier Projekte prognostiziert KASTO ein Einsparpotenzial von mindestens 20 % aller Energieaufwände. So ließe sich mit der virtuellen Inbetriebnahme im Jahr durch die Reduzierung der Arbeitstage auf der Baustelle der Strombedarf um rund 336 MWh verringern und es könnten etwa 4.100 l an Diesel für die Fahrten zur und von der Baustelle entfallen. Das würde jährlich ca. 13 t CO2e durch die Reduzierung von Diesel und weitere 194 t CO2e durch die Reduzierung des Strombedarfs einsparen. Der Blick auf die Nacharbeitslisten lässt sogar eine potenziell höhere Einsparung erwarten.
Prozesse können mit Hilfe der Digitalisierung ressourceneffizienter gestaltet werden. Das Projekt verknüpft zwei wichtige zukunftsfähige Elemente – Digitalisierung und Ressourceneffizienz, die so einen gemeinsamen Beitrag zum Klimaschutz leisten. Durch Vorabtests der Schnittstellen werden die Techniker viele Fehler im Voraus finden und inhouse beheben können. Die virtuelle Inbetriebnahme kommt Ende des Jahres beim ersten Projekt zur Anwendung und soll zukünftig auch auf die Sägetechnik und Handling-Einrichtungen (Roboter) angewendet werden, um gesamteinheitlich an Effizienz zu gewinnen.
KASTO blickt auf mehr als 175 Jahre Tradition zurück. Die Geschichte von KASTO begann im Jahr 1844 als der Zimmermann Karl Stolzer im baden-württembergischen Achern eine Werkstatt eröffnete. Inzwischen wird KASTO von seinem Urenkel Armin Stolzer geleitet und zählt zu den ältesten Familienbetrieben in ganz Europa. KASTO beschäftigt weltweit über 700 Mitarbeiter und Mitarbeiterinnen und erwirtschaftete in den vergangenen Jahren regelmäßig einen Umsatz im dreistelligen Millionenbereich.
Ein entscheidender Faktor für den anhaltenden Erfolg von KASTO ist der hohe Innovationsgrad der Säge- und Lager-Lösungen. Mehr als 170 Patente und zahlreiche Preise wie der Red Dot Design Award oder die Auszeichnung „100 Orte für Industrie 4.0“ belegen die herausragenden Leistungen in der Produktentwicklung. Neue Trends wie Digitalisierung und Vernetzung, Automatisierung und Robotik, Additive Fertigung oder Augmented Reality werden frühzeitig aufgegriffen und zu Produkten entwickelt, die dem Anwender in der Praxis einen spürbaren Mehrwert verschaffen.
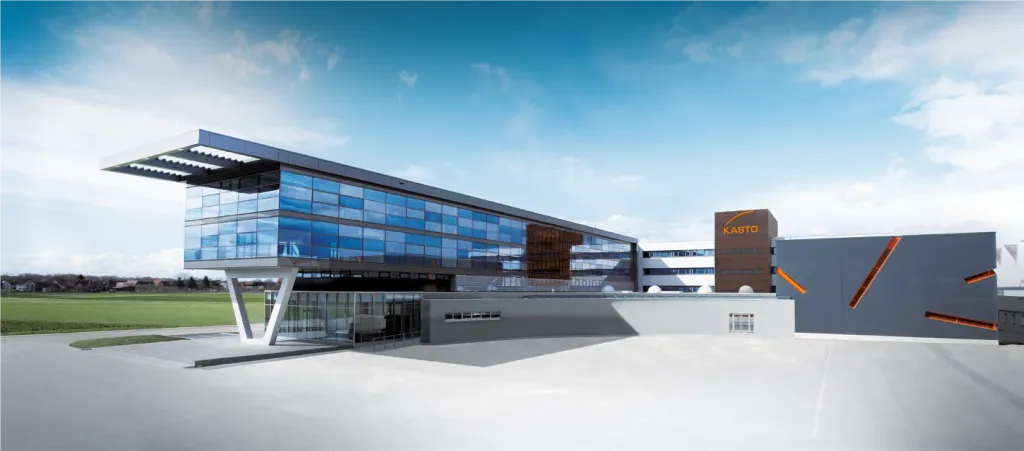
- Einzelteilherstellung
- Entwicklung / Konstruktion ,
- Montage
- Prozessinnovation ,
- Industrie 4.0 / Digitalisierung
- Energie