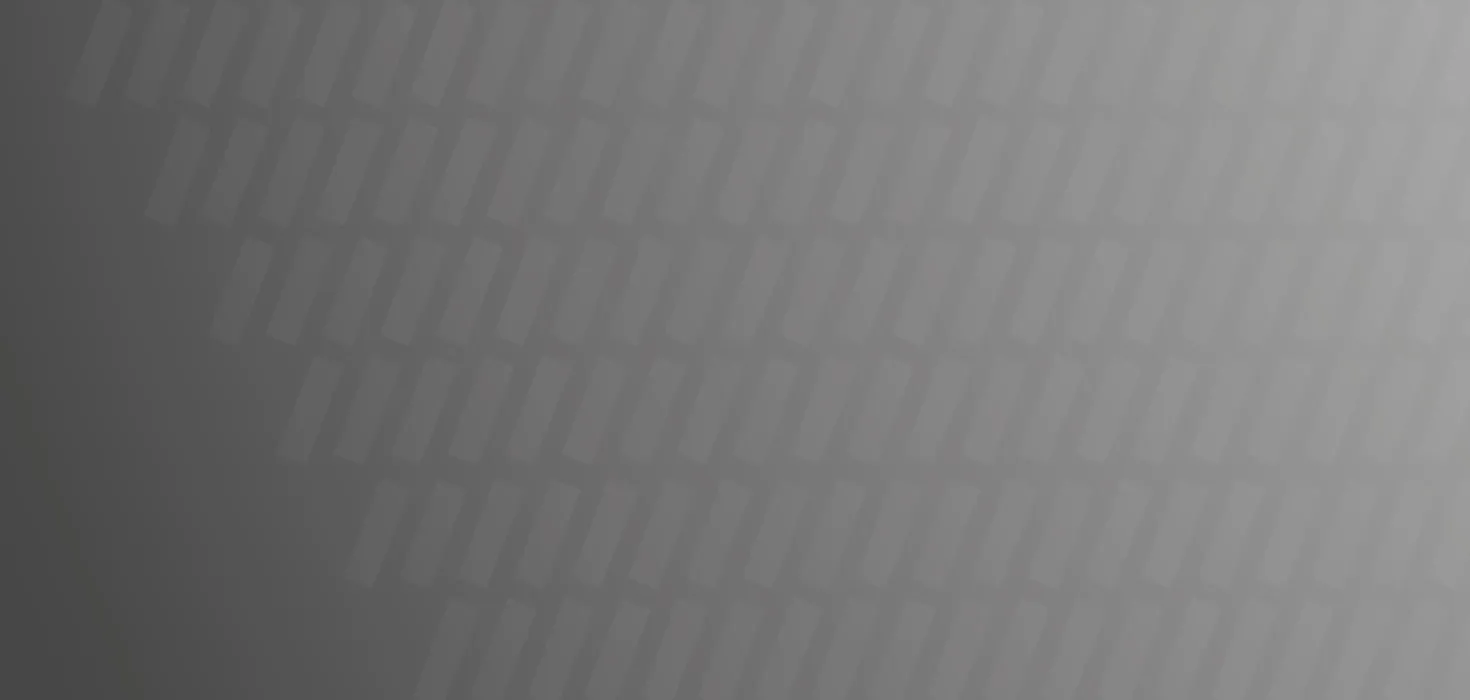
Ressourceneffizienz durch Hinzufügung – additiver Leichtbau für die Industrie 4.0
Kosten- und Gewichtsvorteile durch passgenaue Fertigung
Jomatik liefert passgenaue, ingenieurtechnisch entwickelte Prototypen und Produktionswerkzeuge. Für einen Kunden hat das Unternehmen einen neuen Greifer entwickelt, der deutlich weniger Gewicht hat und trotzdem weiterhin die technischen Anforderungen erfüllt. So konnte das Unternehmen Material und Kosten einsparen und der Kunde spart durch das geringere Gewicht des Greifers Energie im Betrieb.
Jomatik liefert passgenaue, ingenieurtechnisch entwickelte Prototypen und Produktionswerkzeuge. Vom Automobilbau über die industrielle Fertigung bis hin zur Medizintechnik bieten die Jomatiklösungen die Vorteile schnell, leicht und kostengünstig zu sein. Das additive Lasersintern, umgangssprachlich als 3D-Druck bezeichnet, bietet viele Vorteile wie u. a. schnelle Entwicklungszeiten für individuelle Anforderungen, Stückzahlen zwischen 1 und 1.000, verschiedene Sintermaterialien und eine hohe Präzision in Fertigung und Nachbearbeitung.
Das Lasersintern funktioniert dabei folgendermaßen: In den Hochpräzisionsmaschinen werden 0,1 mm dicke Schichten aus hochfestem Kunststoff- oder Aluminiumkomposit über den Brennraum gezogen. Der Laserstrahl fährt dann die gewünschten Konturen ab und härtet das Pulver an den bestrahlten Stellen aus. Danach wird erneut eine Schicht aufgetragen und ausgesintert. So werden pro Bauteil bis zu 5.000 Schichten nacheinander gesintert. Das Lasersintern ermöglicht eine große Freiheit in Konstruktion und Gestaltung. Druckund Saugluftkanäle können genauso mit aufgebaut werden wie Scharniere, Membranen oder Freiräume für Sensoren.
Für einen Kunden sollte ein neuer leichter Greifer entwickelt werden, der gleichzeitig bis zu 36 Kleinverpackungen eines Medizinproduktes greifen und ablegen kann. Der Nachteil des bisherigen Greifers war sein hohes Gewicht, das je nach Ausführung 12 bis 14 kg betrug. Daher benötigte er beim Verfahren mehr Energie und erforderte beim Rüsten der Maschinen einen hohen Krafteinsatz der Bediener. Oberstes Ziel des Kunden war die Gewichtsreduzierung: ein Gewicht über 14 kg hätte bedeutet, einen neuen Roboter mit hohen Kosten anzuschaffen.
Um die komplizierte Gelenkkonstruktion fertigen zu können, sollten mehrere Einzelteile zum Gesamtbauteil zusammengesetzt werden. Gemeinsam mit dem Kunden wurden die Anforderungen an die Bestandteile des neuen Greifers erarbeitet. Der neue Greifer sollte leicht sein, schnell reagieren, präzise greifen und eine Druckabfederung haben. Er sollte zudem die Integration von noch erforderlichen Metallkomponenten zulassen. Gleichzeitig war gefordert, dass der Greifer nur einen minimalen Pressdruck auf die empfindlichen Medizinverpackungen ausüben sollte.
Zusätzlich konnte durch eine bionische Simulation weiteres Gewicht eingespart werden. Bionik bedeutet die Übertragung von Konstruktionsmerkmalen natürlicher Materialien – etwa menschliche Knochen, die durch eine innere Schaumstruktur leicht und stabil zugleich sind – auf die Produktion von technischen Bauteilen.
In die Umsetzung war der Kunde mit seiner Produktionsabteilung von Anfang an eng eingebunden. In der Engineeringabteilung von Jomatik wurden zunächst die einzelnen Teile für die Lasersinterung konstruiert und gezeichnet. Nach einer internen Vorprüfung wurden die 3D-CAD-Entwürfe mit dem Kunden im Detail geprüft und abgestimmt. Anschließend ging das Bauteil in die Produktion, die meist über Nacht den Lasersinterungsprozess durchläuft. Gemeinsam mit dem Engineering und der Produktion bei Jomatik wurde die Neuentwicklung bereits beim ersten angefertigten Stück für den Echteinsatz in der Produktion hergestellt. Durch die hochpräzise Lasersinterung konnten zur Freude des Kunden im Endergebnis sogar Abweichungen von unter einem anstatt der angestrebten zwei Millimeter erreicht werden.
Der neu konstruierte Greifer von Jomatik hat im Gegensatz zum bisherigen Greifer nur noch ein Gewicht von weniger als vier Kilogramm und führt damit zu einer signifikanten Material- und Gewichtseinsparung. Bei der Lasersinterung werden für den Bauraum, das Standardmaß für die Lasersinterung, 6 kg Pulver benutzt. Davon können anschließend etwa 50 % wieder aufbereitet und neu verwendet werden. In einem Bauraum können gleichzeitig sehr viele unterschiedliche Teile produziert werden. Um dieselben Bauteile aus Aluminium herzustellen, werden rund 40 kg Aluminium benötigt. Pro Jahr werden bei Jomatik 2 t Pulver umgesetzt, mit einer spanabhebenden Fertigung aus Aluminium wären für das gleiche Ergebnis mindestens 13,3 t Aluminium erforderlich.
Über den Produktionsprozess hinaus, erzielt auch der Kunde weitere Einsparungen. Die Produktionswerkzeuge sitzen in der Regel am Ende eines Roboterarms. Durch die Gewichtseinsparung von 85 % brauchen die Roboter weniger Energie beim Anfahren, Verfahren und Abbremsen. Durch die Produktion von Ersatzteilen für ältere Maschinen, können diese Maschinen länger im Prozess verbleiben. Eine Ersatzbeschaffung wird dadurch erst später erforderlich.

Für alle industriellen Kunden gelten ähnliche Rahmenparameter. Eine Neuentwicklung muss schnell, kostengünstig und in hoher Qualität gefertigt werden. Eine komplette Neuentwicklung ist jedoch ein Prozess, der sowohl Aufwand, d. h. Geld, als auch Denk- und Konstruktionsarbeit, d. h. Zeit, erfordert. Durch die enge Verzahnung zwischen der Entwicklungsabteilung und der Produktion des Kunden mit dem Engineering, der Sinterung und dem Produktionsbereich von Jomatik konnten die Anforderung schnell und kostengerecht erfüllt werden. Allerdings muss hierbei großer Wert auf eine schnelle und präzise Kommunikation gelegt werden. Nur diese gewährleistet die Erreichung der angestrebten Ziele mit einem akzeptablen Aufwand für alle Beteiligten.
Die Entwicklungen haben sich nicht nur in dem hier dargestellten Beispiel rentiert. Durch die schnelle Entwicklung, auch für singuläre Prototypen, können deutliche Kosten- und Zeitvorteile erzielt werden. So sind die Prototypenfertigung und Greifer für den Echteinsatz bereits ab Stückzahl eins wirtschaftlich darstellbar. Insbesondere der Einsatz bionischer Prinzipien trägt sowohl zur Gewichtsreduzierung als auch zu hohen Festigkeiten der gesinterten Werkstücke bei. Das wird zukünftig mit dem Einsatz einer bionischen Simulationssoftware noch stärker werden.
Ein Aha-Effekt konnte mit der Übertragung der lasergesinterten Werkzeuge auf den medizintechnischen Bereich erreicht werden. So wurden für die Universität Tübingen Tierträger für MRT-(Magnetresonanztomographie)- Untersuchungen hergestellt. In die Träger für die Kleinkörper wurden Zuführungen für Narkosegas und andere erforderliche Flüssigkeiten sowie Frischluftzufuhr integriert. Auf diese Weise konnten nicht mehr erhältliche Ersatzteile für funktionierende Maschinen bereitgestellt werden, die die Nutzungsdauer der teuren Spezialapparate deutlich verlängern. Die Präsentation dieser Tierträger bei einem medizinischen Fachkongress erzielte große Aufmerksamkeit, so dass einige nationale sowie internationale Kliniken und Forschungsinstitute solche Entwicklungen für ihre Zwecke konkret anfragen. Damit konnte ein vielversprechendes neues Einsatzfeld für die Lasersinterung eröffnet werden.
Jomatik entwickelt Produktionswerkzeuge und stellt diese durch additive Fertigung im 3D-Verfahren durch Lasersinterung auch selbst her. Damit werden hauptsächlich Wechselsysteme für Roboter und Werkzeugmaschinen hergestellt, die zu signifikanten Material- und Ressourceneinsparung führen. Mit dem 3D-Druck können hier sowohl die Entwicklungszeiten als auch die time to market Zeiten dramatisch verkürzt werden. Die Jomatik GmbH wurde erst in 2014 von Johannes Matheis gegründet. Seit 2016 beschäftigt die Jomatik GmbH acht fest angestellte Mitarbeiter. Johannes Matheis freut sich über ein dynamisches und exponentielles Wachstum durch sehr schnell wachsende Kundenzahlen.
- Einzelteilherstellung ,
- Kleinserienfertigung
- Entwicklung / Konstruktion
- Prozessinnovation ,
- Industrie 4.0 / Digitalisierung
- Energie ,
- Material ,
- Metalle ,
- Abgas
- operativ (kleiner 1 Jahr)